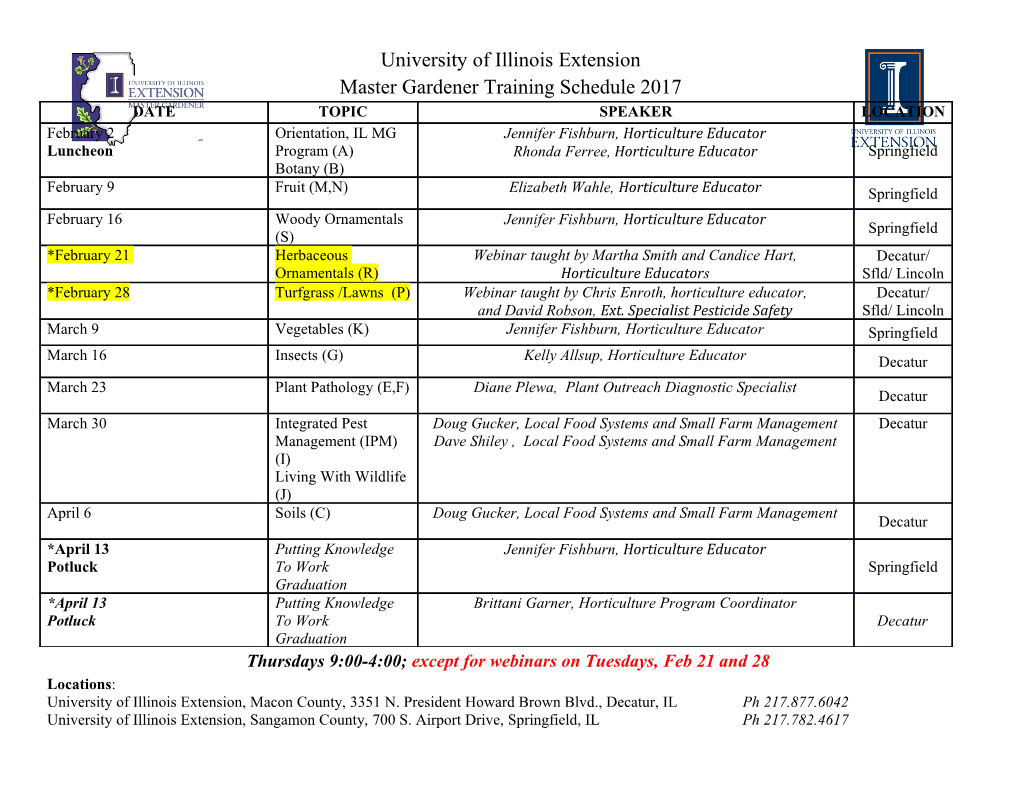
Electrocomponent Science and Technology Gordon and Breach Science Publishers Ltd. 1974, Vol. 1, pp. 17-25 Printed in Great Britain WIRE WRAPPED JOINTS REVIEW P. M. A. SOLLARS "[he Plessey Company Limited, Allen Clark Research Centre, Northants, U.K. (Received October 27, 1973; in final form December 6, 1973) The basic technique of wire wrapping is now well established as a simple and reliable method for joining conductor wires in a permanent, though easily replaceable, manner to more massive terminals. This paper describes the mechanical and the metallurgical basis of the joining technique and outlines the advantages. The scope of the technique as it has developed up to the present day is discussed in terms of the ranges of wrapping terminals and wrapping wires used and the types of wrapped joint that have been evolved. Finally the tools available for wire wrapping are briefly reviewed with particular emphasis on the wrapping bit. THE MECHANICAL BASIS OF THE WRAPPED at various temperatures. Extrapolation techniques can JOINT be used to predict the long term stress relaxation behaviour at room temperature using results obtained The mechanical basis of the wire wrapped joint was by accelerating the process at elevated temperature. investigated very extensively by workers at Bell The elastic stress level in the joint is of importance Telephone Laboratories 20 years ago. Their very full since it indicates the pressure with which the wrap- analysis of the joining system is still considered to be ping wire and terminal are being pressed together to essentially correct. The work included photoelastic maintain electrical contact. observations on a wrapped joint model to investigate strain patterns produced by wrapping, and the study of stress relaxation as a function of time and tem- 2 THE METALLURGICAL BASIS OF THE perature. WRAPPED JOINT The wire wrapped joint consists of a wire which is tightly wrapped around a sharp cornered terminal. Work at this laboratory 2 has suggested that the Sufficient deformation is engendered in the many concept of the wrapped joint as essentially a mechan- notches created by the terminal in the wrapping wire ical joint, with residual elastic stress keeping the to create metal to metal interfaces with a high level of relevant metal components in close contact, is not integrity. The wrapping wire, which is bent several sufficiently comprehensive. The stresses involved in times during wrapping before final positioning in the the notch zones are apparently sufficiently large to wrap, is under a high level of tensile stress during penetrate oxide and tarnish films and promote cold wrapping. The tensile strain which is caused remains welding. Evidence of such cold welding has been in the wire after wrapping because the stretched wire obtained by unwrapping joints and examining them is locked by the notches formed in it. The bulk of the using scanning electron microscope and electron wrapped wire will remain under a tensile stress with microprobe analysis techniques. The latter technique the wrapped terminal under a compressive stress: the was used to show the transfer of metal from one zones, in the wrapped wire, immediately adjacent to component to the surface of the other, indicative of the notches will also be under compressive stress. welding phenomena. Thus tin from a tinned copper Since the wrapped wire is a helix, rather than a series wire wrap has been found to be present on the of hoops the stresses in the wire have components in surface of a brass terminal after unwrapping. Other certain directions and produce a bending moment metal systems have provided similar evidence and the about the long terminal axis. The terminal will twist scanning electron microscope has shown examples of slightly until the relevant stress components in the cold welded metal debris. The original notch pro- wire are balanced by those in the terminal. The twist duced during wrapping is modified when the adjacent induced in the terminal is a useful indication of the notch is formed; the wire is effectively pulled towards level of elastic stress in the joint and it provides a the second notch so that while one side experiences monitor for following the process of stress relaxation an increased compressive stress the other experiences 17 18 P.M.A. SOLLARS a shear stress. The increased compression will tend to six wrapped turns and, except for the outer wraps, extrude any soft terminal coating and increase the there will be notches on four terminal corners for integrity of the metal to metal contact locally; such each turn. Therefore about twenty successful ter- an area will frequently be one in which pronounced minal/wire notches are normally produced, each with metal transfer can be observed. intimate metallic contact. The occurrence of pressure welding in the notches The wrapped joint need not be regarded as a of wrapped joints provides connections which are permanent connection. It can be removed relatively more resistant to corrosive attack; even when the easily when required, by unwinding the wire in the whole joint is visibly corroded electrical quality can opposite direction to that used during wrapping. still be high. The maintenance of satisfactory elec- Fresh wrapped joints can be produced on a terminal trical quality at low levels of residual elastic stress from which previous wrapped joints have been (for example after accelerated stress relaxation) indi- removed. This can be performed many times before cates the benefits of this high level of joint integrity. the terminal corners are sufficiently rounded to affect Because of the increased importance of the metallurg- joint integrity. The number of rewraps will depend on ical micromechanisms in the notch the coating chosen the terminal material but typically the number on the terminal attains greater importance. It is allowed is thirty, or in the case of brass, ten suggested that it is particularly important in the case Another advantage which wire wrapping holds of micro-wrapped joints, where the contact areas are over soldering is the absence of extraneous elements, very small and therefore required to be of high such as solder and flux, that are required to produce integrity if general electrical quality is to be good. the joint. The active tlux which is frequently neces- sary to ensure good joint integrity during soldering must be carefully removed when the joint procedure 3 THE ADVANTAGES OF WIRE WRAPPED is finished in order to minimise the possiblity of CONNECTIONS corrosion. Wire wrapping also avoids damage to adjacent insulation and heat sensitive components by Whenever component leads or wire connections are to the soldering bit, and damage caused by excess solder be jointed to a panel or base in an electrical assembly, splashes falling into the circuitry. An additional soldering is usually considered as the technique to be advantage claimed for wrapped joints is that they used. However against this prevalent acceptance of often show less tendency to fail under vibration than soldering can be laid several disadvantages. Primarily soldered joints; this is though to be due to the 'graded the hand soldered joint is not of reproducible quality; stiffness' of the joint. The change from the terminal the joint quality will depend very largely on operator to the wire dimensions is less sudden, especially as the experience and expertise. The wrapped joint quality wrap does not maintain close contact on the first two is much more consistent, the operator can be trained terminal corners, and there is thus a lower stress very quickly to produce consistent, good quality concentration effect. joints and with some experience these joints can be made at a very fast rate. Most soldered joints can be made to a suitable quality in many cases, with hand 4 THE RANGE OF TERMINALS USED IN WIRE soldering. If the joint does not wet immediately WRAPPED JOINTS prolonged attention will usually achieve the goal. Because the quality of the soldered joint is dependent An appreciation of the range of terminals which are on operator technique, however, a certain percentage used to produce wire wrapped joints can be gained by of joints will be of poor and unacceptable quality. a study of Figure 1. Many of the terminals on the right This percentage of faulty joints may be quite low, but hand side of the photograph are relatively massive, for assemblies which must give very high reliability, .072" x .048" cross section being typical, and they are especially where large numbers of joints are used, it used extensively in panels in telephone exchange can be unacceptable. The percentage of unacceptable racks. An example of an array of wrapped joints joints produced by correct wrapping techniques is made on such terminals is shown in Figure 2. This panel extremely low, in fact it is very difficult to find any contains 210 double-sided terminals and some of failures even when relatively severe accelerated test these can be seen to have two wrapped joints on the procedures are employed. This high level of con- one side. Many of the terminals on the left hand side sistency is essentially due to the inherent 'over-design' of Fig. are relay springs stamped out of suitable of the wrapped joint. The typical joint might involve hard grades of spring alloys; one end of the stamping WIRE WRAPPED JOINTS 19 FIGURE A representative selection of terminals on to which wire wrapped connections are made. FIGURE 2 A typical example of an array of wire wrapped connections taken from a telephone exchange rack. 20 P.M.A. SOLLARS acts as a wrapping terminal and the central portion is are folded together apex to apex) exist. These two located in a suitable plastic moulding. Normally the types do not find universal favour because it is mechanical requirements of the spring end are the considered that the pressure exerted by the wrapping most critical, and to obtain suitable rigidity in the wire can cause plastic distortion and reduction of the wrapping terminal, such that it will not simply distort wrapped terminal dimensions.
Details
-
File Typepdf
-
Upload Time-
-
Content LanguagesEnglish
-
Upload UserAnonymous/Not logged-in
-
File Pages10 Page
-
File Size-