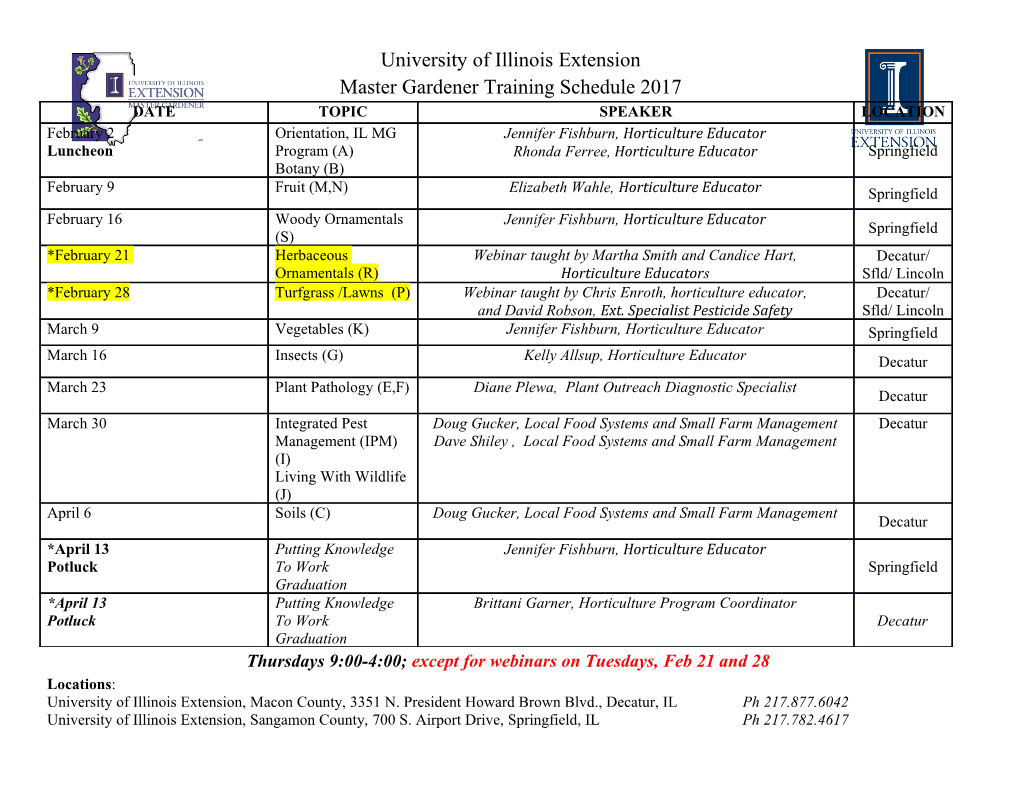
Catalysis – Innovative Applications in Petrochemistry and Refining DGMK Conference October 4-6, 2011, Dresden, Germany Catalytic Dehyration of Ethanol to Ethylene Ying Zhu, Zhaosheng Jin, Wei Shen SINOPEC Shanghai Research Institute of Petrochemical Technology, Shanghai 201208, People´s Republic of China Abstract The different routes of ethylene production were briefly introduced and the advantage of ethanol to ethylene (ETE) route was explained. Followed by that, the upgraded catalyst applied in this route developed by SINOPEC Shanghai Research Institute of Petrochemical Technology (SRIPT) was introduced together with the development of the ethanol to ethylene process. The core technologies involved in this process development were discussed, such as isothermal fixed-bed reactor, water scrubber and alkaline wash column, two columns of low-temperature separation as well as process heat integration. Furthermore, the performance of one of ethanol industrial plants licensed by SRIPT was reviewed. It is as follows, conversion of ethanol reaches 99% while selectivity of ethylene is over 96% at the reaction temperature of 350~450°C, the liquid hourly space velocity (LHSV)of 0.5~1.0 h-1 and atmosphere pressure. Meanwhile, the catalyst shows its life time of one year. This route is considered not only as an economical and practical process but also as an environment- friendly path to ethylene production. Introduction Ethylene is considered as one of the most important chemicals in petrochemical industry, such as ethylene, ethylene oxide, ethylene glycol, polyvinyl chloride, styrene, vinyl acetate etc. The production rate of ethylene nationwide is the indication of development level in the chemical industry. Therefore, ethylene production always draws the most attention. The different routes of ethylene production co-existed in industry in the different period of time. As a traditional ethylene production process, ethanol dehydration was widely used in Brazil, India, Pakistan, and Peru in 1980s. However, this route was phased out in the past two decades. Ethylene is mainly derived from hydrocarbon steam cracking of naphtha and natural gas feedstock due to its more competitive investment and operating cost at that time. With the depletion of crude oil and continuing increase in crude oil price, ethanol dehydration process is back to people’s sight due to its great advantage compared to hydrocarbon stream cracking of petroleum process. With the great breakthrough of biomass-to-ethanol technology, the raw material price of ethanol declined to a large extend, which makes the ethanol dehydration process is more feasible. Ethanol dehydration process has more flexible in terms of ethanol feedstock not only with different concentration but also various biomasses. Furthermore, this process operates at mild reaction conditions, normally 250~480°C and 0.01~1.8MPaG while the steam cracking of naphtha occurs at 800~850°C and 0.18MPaG. Compared to the number of equipments required by steam cracking process, ethanol dehydration process requires far less and around 80 equipments. Therefore, the construction cost of ethanol dehydration plant is much lower than that of steam cracking process due to the low standard construction material and less equipment required. In addition, ethanol dehydration process has high ethylene selectivity which leads to the more purified product and this directly reduces the separation cost. Therefore, ethanol dehydration process is DGMK-Tagungsbericht 2011-2, ISBN 978-3-941721-17-3 61 Catalysis – Innovative Applications in Petrochemistry and Refining much simpler and easier to be controlled than the steam cracking process. In literature, it is found that, for ethanol dehydration process, the energy consumed for each tonne of ethylene produced is much less than the energy consumption for a common steam cracking process. Again, the low capital investment, simple process, short construction period leads to the quick investment return and make the dehydration of ethanol to ethylene process even more attractive. Most importantly, the ethanol dehydration process has limited impact on the environment due to its high selectivity of ethylene. This process is considered as an environment-friendly one. The reactor types in the ETE process route are common: one is fixed-bed and the other is fluidised-bed. The process with fluidised-bed reactor was first brought up by ABB in late 1970s; however, no industry application is launched yet. Whereas the process with fixed-bed reactor is more common nowadays, either adiabatic or isothermal process. The ethanol dehydration reaction in the early stage takes place in the tubular fixed-bed reactor at atmosphere pressure where the heat for reaction is supplied directly or indirectly by heating medium. In this case, the reaction temperature and flow rate are key factors which affect the product composition. Too high temperature or too low flow rate of ethanol leads to the formation of by-products. On the other side, the conversion rate decreases with the increase of the ethanol flow rate. To solve this issue, isothermal process of ethanol dehydration is suggested that ethanol feed is heated to desired reaction temperature to ensure the reaction occurs. Based on this, three adiabatic fixed-bed reactors connected in series and the process with this reactor arrangement is industrialised in the 1980s with the capacity of 60 kilo-tonnes per year. The furnace is applied to heat up the feed mixture of ethanol and steam in each section of reactor and unconverted ethanol and by-products circulate. The steam prevents the reaction from coking. At mean time, it improves the catalyst activity enhance production rate. Halcon/SD developed its isothermal fixed-bed reactor technology and industrialised soon in the 1970s. Soon after, Halcon/SD developed the multi-sections of adiabatic fixed-bed reactor. Lummus also had its fixed-bed reactor process and industrialised in the 1960s. It applied the tubular isothermal reactor in the process and utilised hot-oil as the heating media to supply the reaction heat. By combining these characterise, SRIPT developed its own technology on the ethanol dehydration to ethylene process. To understand its process, the mechanism of ETE process is reviewed at first. The Mechanism of ETE Process Under certain reaction temperature and pressure, the ethanol is catalytically converted to ethylene and water. It is an endothermic and molecules increasing reaction. (a) Main Reaction The main reaction of ethanol to ethylene is illustrated as follows: Catalyst C2H5OH ⎯⎯→⎯ C2H 4 + H 2O +10.82kcal/mol Equation 1 (b) Side Reactions The primary side reactions in the ETE process are: The intermolecular dehydration of ethanol leads to ethers formation, the dehydrogenation of ethanol results in the formation of acetaldehyde and hydrogen, and the ethylene oligomerization and cracking produce methane, ethane, C3’s and C4’s, and so on. The main factors which affect the dehydration reaction are the reaction temperature, LHSV, and reaction pressure. Besides, the catalyst performance and impurities contained in the ethanol feed will also affect the reaction to some extent. DGMK-Tagungsbericht 2011-2 62 Catalysis – Innovative Applications in Petrochemistry and Refining SRIPT’S ETE Process In Figure 1, it can be seen that the ETE process developed by SRIPT includes three sections, reaction and water scrubbing, compressing and drying as well as ethylene purification. Figure 1 Schematic Draw of ETE Process The ethanol feed is vaporized and preheated with the reactor effluent before it is charged into the reactor. In the reactor the ethanol is catalytically converted to ethylene and water. After heat-exchanging with feed, the reactor effluent enters the bottom of water scrubber, and directly contacts the spraying water from the top part, and gets further cooling. The water and other high boiling point components in the reactor effluent are condensed and discharged as process waste. The gas-phase stream from the top of the water scrubber enters the bottom of alkaline washing column. This column is divided into two parts: the lower one is alkaline washing part, in which diluted alkaline solution is sprayed and recycled to remove the acidic gas such as carbon dioxide; and the upper one is water washing part, directly scrubbing with spraying water. The crude ethylene stream from the alkaline washing column is compressed, and cooled down, then enters ethylene dryer to remove the water contained. The stream from ethylene dryer enters the ethylene column to remove ethane, C3 and other heavier components. The stream from the top of ethylene column enters the stripper to remove light ends such as hydrogen, methane and carbon monoxide. The ethylene product from the bottom of the stripper is sent to storage tank. JT-II Catalyst Specification A number of catalysts are used in the ETE reaction; the results show that the activated alumina and silica-alumina are the most effective ones. The specification of the activated alumina catalyst JT-II developed by SRIPT is shown below. Table 1 JT-II catalyst specifications Items Specifications Appearance White (or reddish) cylinder Main component Alumina Physical size Ф3.5~4.0×10~20mm Bulk density 0.60~0.80 g/ml Crush strength ≥ 80 N/cm DGMK-Tagungsbericht 2011-2 63 Catalysis – Innovative Applications in Petrochemistry and Refining JT-II is a very stable catalyst with high yield in ethanol dehydration. The conversion rate of ethanol reaches 99% while selectivity of ethylene is over 96% at the reaction temperature of 350~450°C, LHSV of 0.5~1.0 h-1 and atmosphere pressure. Meanwhile, the catalyst shows its life time of one year. Commercial References SRIPT started its research on ethanol to ethylene process in 1982. Based on the JT-II catalyst, SRIPT has developed the process design package of ethanol dehydration to ethylene, and it was commercialized soon after. In 1988, this technique was first applied on the ethylene industrial plant in China. This process was upgraded based on actual plant data and improved catalyst for ethylene production.
Details
-
File Typepdf
-
Upload Time-
-
Content LanguagesEnglish
-
Upload UserAnonymous/Not logged-in
-
File Pages4 Page
-
File Size-