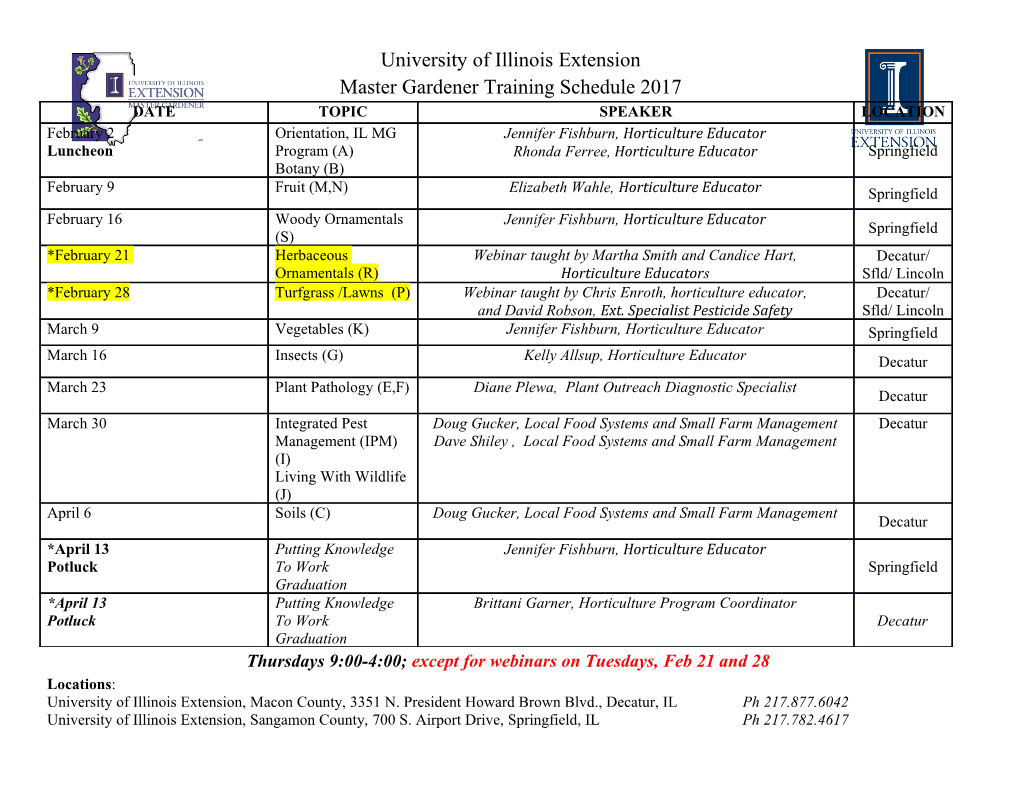
Control of Volatile Organic Compound Emissions from Batch Processes - Alternative Control Techniques Information Document Control of Volatile Organic Compound Emissions from Batch Processes Emislion Standard Division US. ENVIRONMENTAL PROTECTlON AGENCY Office of Air and Radiation Office of Air Quality Planning and Standards Research Triangle Park, North Carolina 2771 1 This report is issued by the Office of Air Quality Planning and Standards (OAQPS) to provide information to State and local air pollution control agencies. Mention of trade names or commercial products is not intended to constitute endorsement or recornendation for use. Copies of this report will be available - as supplies permit - from the Library Services Office (MD-35), U. S. Environmental Protection Agency, Research Triangle Park, North Carolina 27711. Springfield, Virginia 22161. TABLE OF CONTENTS 1.0 INTRODUCTION ..................... 1-1 2.0 BATCH PROCESS DESCRIPTIONS ............. 2.1 UNIT OPERATIONS IN BATCH PROCESSING .... 2.1 2.1.1 Reactors ................ 2-2 2.1.2 Solid/Liquid Separation ........ 2-12 2.1.3 Drying ................. 2-21 2.1.4 Distillation .............. 2-26 2.1.5 Extraction ............... 2-30 2.1.6 Crystallization ............ 2-31 2.1.7 Storage ................ 2-34 2.1.8 Transfer Operations .......... 2-35 2.1.9 Equipment Leaks ............ 2-36 2.1.10 Wastewater ............... 2-36 2.2 EXAMPLE INDUSTRY DESCRIPTIONS ......... 2.2.1 Synthetic Resin Manufacturing ..... 2.2.2 Pharmaceuticals Industry Description ............. 2.2.3 Pesticide Manufacturing ........ 2.2.4 Synthetic Organic Chemicals Manufacturing Industry (SOCMI) .... 3.0 EMISSION ESTIMATION METHODOLOGIES ......... PROCESS VENT EMISSIONS 3.1.1 Drying ................. 3.1.2 Tank and Reactor Purging ........ 3.1.3 Vapor Displacement Losses ....... 3.1.4 Vessel Heating ............. 3.1.5 Gas Evolution ............. 3.1.6 Sparging ................ 3.1.7 Batch Pressure Filtration ....... 3.1.8 Emissions from Vacuum Generating Equipment 3.2 EVAPORATIVE LOSSES FROM WASTEWATER ...... 3.3 STORAGETANKEMISSIONS ......... 3.4 EQUIPMENTLEAKS ................ iii TABLE OF CONTENTS ( continued) 4.0 CONTROL TECHNOLOGIES . .'. 4.1 CONDENSERS . 4.1.1 Design . 4.1.2 Specific Systems and Applications . 4.2 SCRUBBERS . 4.2.1 General Gas Absorbers . 4.2.2 Design. 4.2.3 Specific Systems and Applicability . CARBON ADSORPTION 4.3.1 Design. 4.3.2 Applicability . THERMAL DESTRUCTION 4.4.1 Flares . 4.4.2 Thermal and Catalytic Oxidizers . 4.5 SOURCE REDUCTION MEASURES . 4.5.1 Vapor Containment . 4.5.2 Limiting the-Use of Inert Gas . 4.5.3 Use of Closed Processing Equipment . 4.5.4 Material Substitution/Improved Separation Techniques . 4.5.5 Improved Process Design . 5.0 ENERGY AND ENVIRONMENTAL IMPACTS . 5.1 ENERGYIMPACTS . 5.2 AIRQUALITYIMPACTS. 5.3 WASTEWATER AND SOLID WASTE IMPACTS . TABLE OF CONTENTS (continued) 6.0 DESCRIPTION OF CONTROL OPTIONS ........... 6.1 BACKGROUND .................. 6.2 TECHNICAL BASIS FOR OPTIONS .......... 6.2.1 Approach ................ 6.2.2 Options Methodology .......... 6.3 PRESENTATION OF FLOWRATE REQUIREMENTS ..... 6.4 IMPACTS OF APPLYING OPTIONS .......... 6.4.1 Industries Covered ............ 6.4.2 Model Processes ............ 6.4.3 Baseline Asaumptions/Extrapolations . 7.0 IMPLEMENTATION.................... 7.1 DEFINITIONS AND APPLICABILITY ......... 7.1.1 Definitions .............. 7.1.2 Applicability ............. 7.2 FORMATOFSTANDARDS .............. 7.3 TESTING .................... 7.4 COMPLIANCE MONITORING REQUIREMENTS ...... 7.5 REPORTING/RECORDKEEPING REQUIREMENTS ..... APPENDIXA . PHYSICALDATA ............... APPENDIX B . CALCULATIONU ISSUES ........... APPENDIX C . SAMPLE CALCULATIONS ............ APPENDIX D . COST CALCULATIONS ............. APPENDIX 6 . MODEL EMISSION STREAM CALCULATIONS .... APPENDIX F . MASS EMISSIONS .............. APPENDIX G . BATCH PROCESSING EXAMPLE RULE ....... TABLE OF CONTENTS ( co CONTROL TECHNOLOGIES CONDENSERS ......... 4.1.1 Design ........ 4.1.2 Specific Systems and A SCRUBBERS ............ 4.2.1 General Gas Absorbers 4.2.2 Design. ....... 4.2.3 Specific Systems and A CARBON ADSORPTION ...... 4.3.1 Design. ....... 4.3.2 Applicability .... THERMAL DESTRUCTION 4.4.1 Flares ........ 4.4.2 Thermal and Catalytic SOURCE REDUCTION MEASURES . 4.5.1 Vapor Containment . -1 - . , a -* - - 5.1 ENERGY IMPACTS ....... 5.2 AIR QUACITY IMPACTS ..... 5.3 WASTEWATER AND SOLID WASTE IM LIST OF FIGURES (continued) Figure 6-6. Dependence of control devise cost on emission intermittency . Figure 6-7. Annual Mass Emission Total C/E Curve . Figure 7-1. Example Option Analysis . vii LIST OF FIGURES Figure 2-1. Basic Design of a kettle-type batch reactor . Figure 2-2. Plate-and-frame filter press . Figure 2-3. Agitated pressure Nutsche filter . Figure 2-4. Top-auspended centrifugal filter . Figure 2-5. Vacuum tray dryer . Figure 2-6a. Counter-current air-heated rotary dryer . Figure 2-6b. Cross-sectional view . Figure 2-7. Tumble (double-cone)dryer . Figure 2-8a. Batch fractionator . Figure 2-8b. Vacuum generating equipment . Figure 2-9. Vacuum crystallizer . .. Figure 2-10. Wet-strength resins production . Figure 2-11. Aspirin manufacturing . Figure 2-12. Process schematic for Heptachlor . Figure 2-13. Process schematic for Chlorendic Anhydride . .* . 2- 63 Figure 4-1. Filter cake drying curve . 4-9 @ Figure 4-2. Dryer emission stream aolvent content . 4- 9 Figure 4-3. Closed-loop drying system . 4-14 Figure 6-1. Model Batch Process . 6-4 *P Figure 6-2. Flowrateprofile . 6- 6 Figure 6-3. Concentration profile . 6-7 Figure6-4. Emissionsprofile ............. 6-8 rr Figure 6-5. Flowrate, concentration and emissions profiles 6-9 INTRODUCTION The purpose of this document is to provide information on alternative control techniques for volatile organic compound (VOC) emissions from batch operations. Although the control , techniques information applies to batch processing in all industries, the document focuses primarily on batch processes in the following six industries: plastic materials and resins (described by Standard Industrial Classification (SIC) Code 2821), pharmaceuticals (SIC 2833 and 2834), gum and wood chemicals (SIC 2861), cyclic crudes and intermediates (SIC 2865), industrial organic chemicals (SIC 28691, and agricultural chemicals (SIC 2879). This document contains information on emissions, controls, control options, and costs that States can use in developing rules based on reasonably available control technology. The document presents options only, and does not contain a recommendation on reasonably available control technology. 2.0 BATCH PROCESS DESCRIPTIONS This chapter identifies and describes the most conunon unit . operations found in batch processing and provides descriptions of industries that typically use batch processing. The unit operations section of this chapter provides descriptions of the equipment (i.e., reactors, filters, dryers, distillation columns, extractors, crystallizers, and storage/transfer devices) used to perform batch processing steps. In the industry description section, four industries were selected to illustrate how these unit operations are combined to produce polymers and resins, pharmaceutical products, pesticides, and synthetic organic chemicals. Whereas the unit operations section provides general information on equipment operation and sources of VOC emissions, the industry description section focuses in detail on equipment arrangements, process flows, operating conditions, and sources of emissions. Whenever possible, information is provided that can' be used, in conjunction with the procedures described in subsequent chapters, to estimate VOC emissions from the five example batch processes. Moreover, the readers may use these examples as a guide in evaluating emissions from other specific batch processes that use these same or similar unit operations. 2.1 UNIT OPERATIONS IN BATCH PROCESSING The unit operations discussed are commonly used to produce, separate, and prepare chemical products or intermediates on a batch basis. For each unit operation, a discussion is provided of the equipment used to accomplish that operation, key equipment design considerations, principles of equipment operation, and factors affecting emissions. d to provide a more general description of the operations :d in this stage of the process. ..I Reactor. The reaction cycle is normally. Xion ced by charging solvents, catalysts, and raw materials into )per actor. For the purpose of this description, "raw t. .alsnrefers to compounds that are combined with other mts to produce the desired product or intermediate. The on or nl charging step may be accomplished in many ways. If the :S are or is tied into -a vacuum system, the materials can be or to edm into the reactor by reducing the pressure in the reactor J atmospheric. Steam jet ejectors, as shown in Figure 2-1, 3cuum pumps may be used for this purpose. The hookup ection for material addition is then used to introduce rials into the reactor. Drums containing solvents, tep ~lysts,and raw materials can be hooked up to the reactor his lg flexible e lflex) hoses. A dip-leg is inserted into drum and connected to one end of the flex hose. The other of the flex hose is connected to the reactor hookup mection. When the valve located at the reactor (in the hookup le shown in Figure 2-11 is opened, material in the drum flows rough the flex hose and into the reactor due to the pressure fferential. 'ed Solvents, catalysts, and raw materials can also be pumped * to the reactor
Details
-
File Typepdf
-
Upload Time-
-
Content LanguagesEnglish
-
Upload UserAnonymous/Not logged-in
-
File Pages377 Page
-
File Size-