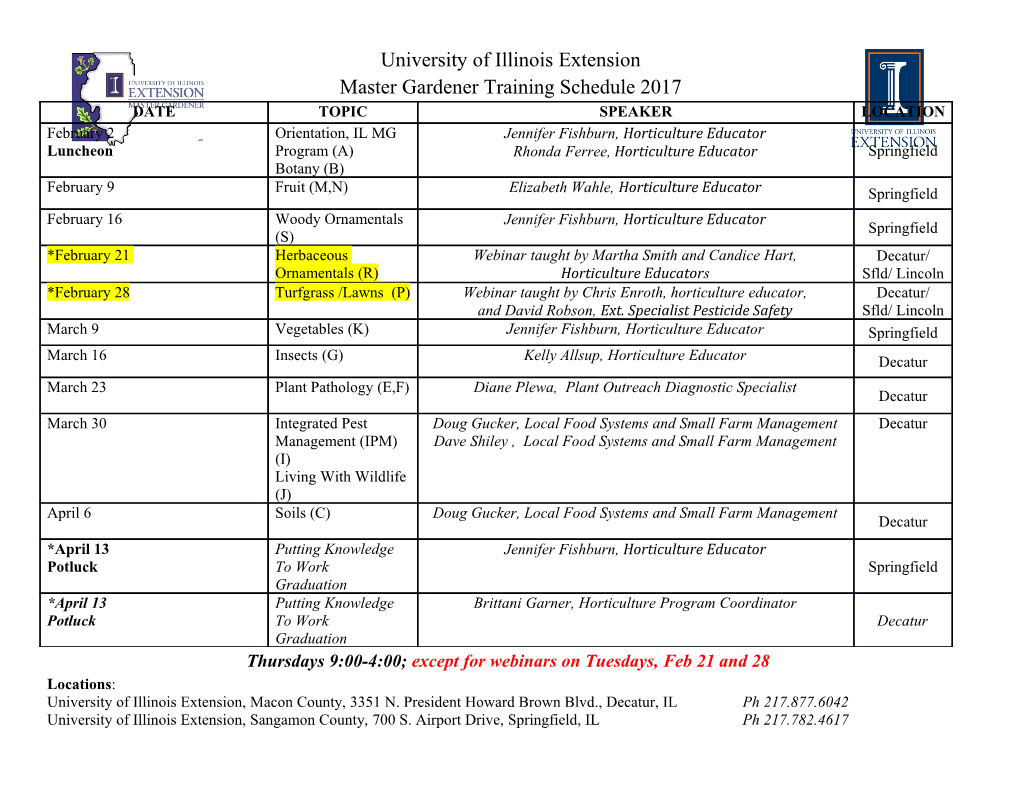
MT-SRC-004-012 EFFECTS OF HEATING RATE AND PRIOR MICROSTRUCTURE ON SAE 1541 FORGING STEEL Submitted to: Forging Industry Eductional and Research Foundation 25 W. Prospect Avenue, Suite 300 Cleveland, OH 44115-1000 Submitted by: A.Shutts Advanced Steel Processing and Products Research Center Colorado School of Mines Golden, Colorado 80401 April 2004 TABLE OF CONTENTS Page INTRODUCTION 3 INDUSTRIAL RELEVANCE 3 PREVIOUS RESEARCH 3 MATERIAL 4 EXPERIMENTAL DESIGN 4 RESULTS 8 DISCUSSION 15 POSSIBLE FUTURE WORK 15 CONCLUSIONS 15 ACKNOWLEDGEMENTS 16 REFERENCES 16 2 EFFECTS OF HEATING RATE AND PRIOR MICROSTRUCTURE ON SAE 1541 FORGING STEEL: by Adam Shutts Introduction This project was initiated in May 2003 as summer research for Adam Shutts, an undergraduate student in Metallurgical and Materials Engineering. The purpose of this project was to investigate the effects of heating rate on 1541 steel as pertinent to forging related processes. Heating rates, varying over several orders of magnitude, were applied to two vastly different prior microstructures: as quenched martensite and coarse pearlite. These heating rates were applied and measured using a Gleeble 1500 thermo-mechanical testing machine. Each specimen provides data consisting of prior austenite grain size, presence of undissolved carbides and retained ferrite, and hardness. This project is linked to Jason Coryell’s project on induction heating which makes use of the same material in applications of induction heating. Industrial Relevance This project was identified in response to research objectives set forth by the FIA Technical Committee in the October 30, 2001 document entitled “Forging Industry Educational and Research Foundation Magnet School Student Project Ideas.” The two titles selected were “Develop a matrix of where phase change occurs at different heating rates for a given alloy” and “Quick normalizing techniques.” These projects both involve issues related to microstructural evolution during heating. Industrial use of rapid austenitization processes is becoming more prevalent due to economic benefits versus conventional furnaces. Quantitative knowledge is needed to refine the processes. For some induction heated forgings, practices should avoid undissolved carbides and soft microstructures in the final product. The austenite grain size is also of importance to the final structure/properties of the forging (4). The two prior microstructures selected, coarse pearlite and as quenched martensite, were chosen to represent two extremes in the microstructural spectrum, particularly related to expected carbide dissolution and austenite grain growth kinetics. Comparison of these two microstructures should demonstrate the range of effects of prior microstructure in rapid heating. Previous Research K.C. Smith has used similar laboratory practices at CSM in past programs. Smith examined the heating response of a 1070 steel using similar procedures as planned for the present research. Dilatometry provided a temperature associated with the phase changes. An inverse relationship between heating rate and prior austenite grain size was reported. Limits on heating rate were defined for lamellar cementite dissolution in both microstructures used by Smith (2). Other pertinent work has also been done at CSM. T.J. Favenyesi performed induction case hardening of 1541 steel as applied to fatigue response. The heating rate used by Favenyesi corresponds with the higher heating rates being planned for this project (3). 3 Similar studies were reported by Feuerstein and Smith in 1953. Heating rate, prior microstructure, and alloy were examined. Feuerstein and Smith used different degrees of tempering on their quenched steels and measured the increase of the Ac1 and Ac3. The data show that the critical temperatures increase with heating rate, in some cases as much at 120° C. Coarser microstructures exacerbate this effect. Annealed 4130 showed an increase of 120° C while 4130 tempered at 400° F showed an increase of only 65°C (5). Another researcher, Chen, studied the effect of heating rate on the Ac1 as applied to laser surface hardening. With heating rates approaching 1000°/sec Chen reported an increase of 47°C (6). Extensive work has also been done at the Heinz-Joachim Spies Freiberg University of Mining and Technology in the Institute of Materials Engineering at Freiberg, Germany by Johannes Rodel. This work focused on austenite formation in spherodized microstructures, which were surface hardened through the use of laser or electron beams. Extensive mathematical modeling was used to predict the austenite formation kinetics. Rodel indicates that rapid heating raises the austenite finish temperature. He also makes the assertion that diffusion controls the rate at which the austenite may form. Alloy elements, mainly carbon, must be given adequate time to diffuse into the austenite in order for it to form completely. Rodel’s heating rate of 1000 K/s matches the highest heating rate applied in the present study. One difference between Rodel’s work and the work done here at CSM is the material evaluated. Rodel’s work and much of the other work found on laser hardening was performed on a variety of steels from plain carbon to high alloy compositions with chromium and molybdenum (7). Material The steel being used is SAE 1541 and was received from North Star Steel in 1.259-inch diameter 4-foot long bars. The steel was hot rolled, consisting roughly of a 10% ferrite- 90% pearlite microstructure. The composition of the as-received steel is listed in Table 1 (4). TABLE 1 – Chemical Composition Of Selected Steel (4) Steel C Mn P S Si Cu Ni Cr Mo V Al Ti Nb 1541 0.39 1.444 0.01 0.024 0.27 0.119 0.05 0.09 0.01 0.005 0.024 0.003 0.001 Experimental Procedure Bandsaw Services reduced the 1.259-inch diameter bars into .25-inch square rods 12 inches in length as is illustrated in Figure 1a. The steel was then heat treated in the CSM physical metallurgy lab to attain quenched martensite and coarse pearlite microstructures. The pearlite samples were held at 900°C for 35 minutes and then were allowed to furnace cool to room temperature in approximately 12 hours (Fig. 2a). The martensite samples were held at 900°C for 35 minutes and then quenched in oil (Fig. 2b). The samples were ground to 3mm diameter cylinders and cut into 70mm lengths as is illustrated in Figure 1b. 4 A) B) Figure 1 Schematic cross-section of machining operations; (A) Bandsaw reduction of 1.259 in. samples to .25 in. square rods. (B) Final form for Gleeble test, after grinding; 3mmx70mm. 5 A) 10 µm B) 20 µm Figure 2 Light optical micrographs of 1541 steel with 2% nital etch, (A) Pearlitic microstructure taken at 1000x (B) Martensitic microstructure taken at 500x. 6 The samples were then heat treated in the Gleeble tester to simulate heating as applied in forging or final heat treatment. Copper jaws of the prescribed size were already available to hold and cool the ends of the sample from Smith’s previous work. Temperature monitoring and current delivery were executed with a type-K thermocouple welded to the center of the sample. An attempt was made to use dilatometry to measure expansion and contraction during heating in order to deduce the transformation temperature. This attempt was not successful due to small cross- sections and a dilatometer malfunction, which was discovered much later. Heating rates tested ranged from 1.0°C/second to 1000°C/second, incremented by orders of magnitude. Each of these five rates was carried out to 4 different maximum temperatures ranging between 900°C-1200°C. After heating, the samples were quenched by a direct spray of argon gas to the center of the sample. Cooling rates of approximately 200°C/sec were attained by this method and martensite was formed throughout the cross section, where austenitized. Sample Gleeble data can be seen in Figure 3. 1200 Target temperature profile Actual temperature profile ) 800 C e ( ur at er p m e 400 T 0 0 40 80 120 Time (sec) Figure 3 Sample heating and cooling curve for Gleeble sample heated at 10 C/s to 1000 C and argon gas quenched. After the samples were resistance heated and quenched, metallography was performed. The samples were cross-sectioned and mounted in Bakelite, ground with SiC paper to 600 grit, and polished with six and one micron diamond solution. The prior austenite grain size was evaluated using an etchant composed of 100ml picric acid, 2ml Teepol, and two drops of hydrochloric acid. This mixture was gently boiled using a hot plate and samples were 7 immersed for 35 seconds and then back polished with a cotton ball. These two steps were repeated until the austenite grain boundaries were easily visible. Statistical grain counting methods were then employed by placing circles of known circumference over a micrograph at 100 and 200x. Intersections with grain boundaries were counted for three cross-sections and the magnification was incorporated in the calculation of the average austenite grain size (4). Hardness profiles were taken from the center of the samples out to the edge with a Vickers Microhardness tester. Conversion to Rockwell C was presented in another display on the tester. The presence of undissolved carbides and retained ferrite was assessed by light microscopy after a 2% nital etch for 35 seconds. Results The results of this experiment are summarized in Tables 2 and 3 and Figures 5 through 11. The data show the presence of “retained ferrite” and undissolved lamellar carbides (i.e. “ghost pearlite”) at heating rates between 100°/s and 1000°/s for maximum temperatures under 1100°C with a coarse pearlite starting microstructure. These phenomena provide clear evidence of incomplete austenitization under these conditions. Examples of “retained ferrite” are shown in Figure 7. Hardness tests on these areas as well as “ghost pearlite” regions show a marked decrease in hardness as presented in Table 2, with values around 50 HRC compared to about 58 HRC in the fully austenitized regions.
Details
-
File Typepdf
-
Upload Time-
-
Content LanguagesEnglish
-
Upload UserAnonymous/Not logged-in
-
File Pages16 Page
-
File Size-