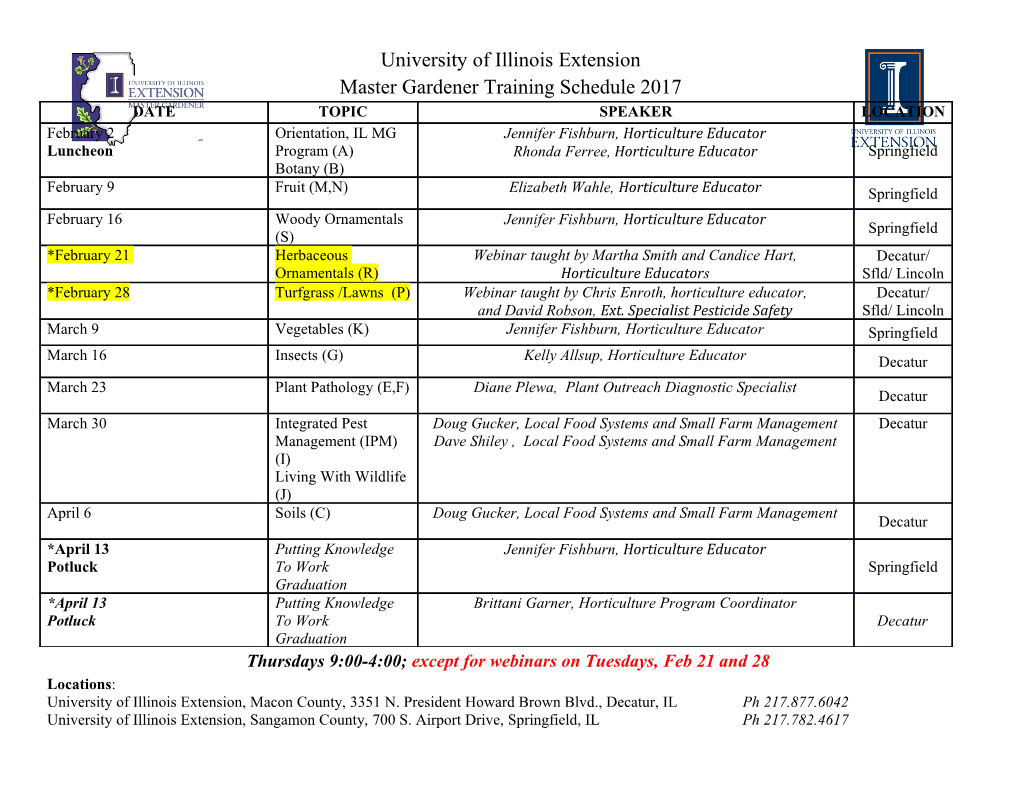
United States Department of Agriculture Drying Hardwood Forest Service Forest Lumber Products Laboratory General Technical Joseph Denig Report Eugene M. Wengert − − FPL GTR 118 William T. Simpson Abstract Units of Measurement Drying Hardwood Lumber focuses on common methods for In this manual, measurements are expressed in both English drying lumber of different thickness, with minimal drying (inch–pound) and SI units. The following provides SI defects, for high quality applications. This manual also equivalents for lumber thickness sizes, dimension lumber, includes predrying treatments that, when part of an overall board foot volume, and other units. quality-oriented drying system, reduce defects and improve drying quality, especially of oak lumber. Special attention is given to drying white wood, such as hard maple and ash, without sticker shadow or other discoloration. Several special SI equivalents for lumber thickness sizes drying methods, such as solar drying, are described, and 3/4 19 mm proper techniques for storing dried lumber are discussed. 4/4 25 mm Suggestions are provided for ways to economize on drying costs by reducing drying time and energy demands when 5/4 32 mm feasible. Each chapter is accompanied by a list of references. 6/4 38 mm Some references are cited in the chapter; others are listed as 8/4 51 mm additional sources of information. 10/4 64 mm 12/4 76 mm Keywords: drying, hardwood, lumber, warp, kiln 14/4 89 mm 16/4 102 mm SI equivalents for dimension lumber Nominal (in.) Standard (mm) 2 by 4 38 by 89 2 by 6 38 by 102 2 by 10 38 by 165 September 2000 Denig, Joseph; Wengert, Eugene M.; Simpson, William T. 2000. Drying hardwood lumber. Gen. Tech. Rep. FPL–GTR–118. Madison, WI: SI equivalents for other units U.S. Department of Agriculture, Forest Service, Forest Products Laboratory. 138 p. a −3 3 board foot 2.36 × 10 m A limited number of free copies of this publication are available to the ft3 0.0283 m3 public from the Forest Products Laboratory, One Gifford Pinchot Drive, Madison, WI 53705–2398. Laboratory publications are sent to hundreds ft/s 0.305 m/s of libraries in the United States and elsewhere. ft/min 0.005 m/s The Forest Products Laboratory is maintained in cooperation with the lb 0.454 kg University of Wisconsin. lb/in2 6.895 kPa The use of trade or firm names is for information only and does not imply endorsement by the U.S. Department of Agriculture of any product or lb/ft3 16.0 kg/m3 service. °F 0.56°C The United States Department of Agriculture (USDA) prohibits discrimina- temperature T = [T − 32]/1.8 tion in all its programs and activities on the basis of race, color, national C F origin, sex, religion, age, disability, political beliefs, sexual orientation, or aThe conversion factor for board foot is used marital or familial status. (Not all prohibited bases apply to all programs.) to convert gross volumes of lumber. It does Persons with disabilities who require alternative means for communication not take into account any variation between of program information (Braille, large print, audiotape, etc.) should contact actual and nominal sizes but rather is based the USDA’s TARGET Center at (202) 720–2600 (voice and TDD). To file a on the volumetric ratio between 1 cubic complaint of discrimination, write USDA, Director, Office of Civil Rights, meter (1 m × 1 m × 1 m) and 1 board foot Room 326-W, Whitten Building, 1400 Independence Avenue, SW, Wash- × × ington, DC 20250–9410, or call (202) 720–5964 (voice and TDD). USDA (1 in. 12 in. 1 ft). is an equal opportunity provider and employer. Drying Hardwood Lumber Joseph Denig Associate Professor North Carolina State University, Raleigh, North Carolina Eugene M. Wengert Professor Emeritus University of Wisconsin, Madison, Wisconsin William T. Simpson Research Forest Products Technologist Forest Products Laboratory, Madison, Wisconsin Preface For hardwood lumber producers, drying is an opportunity to add value to products and to enter new, previously inaccessible markets. For most hardwood users, such as furniture manufacturers, lumber drying is an essential procedure in the manufacturing process. As with any part of the manufacturing process, costs must be controlled. Costs can be magnified by improper drying techniques that cause degrade, resulting in quality losses; mistakes can be made that cause problems in subsequent manufacturing processes; and considerable amounts of energy can be wasted. As hardwood lumber prices escalate, ensuring that the highest yield is obtained from the hardwood resource becomes critical in controlling overall costs. Fortunately, drying techniques and systems are available that can produce a quality hardwood lumber product at minimum cost. Drying Hardwood Lumber is an update of a previous Forest Service publication, Drying Eastern Hardwood Lumber by John M. McMillen and Eugene M. Wengert. Both publications contain information published by many public laboratories, universities, and associations, as well as that developed at the Forest Products Laboratory and other Forest Service units. The updated version includes much basic information from the original publication and new information relevant to new technology and the changing wood resource. iii Contents Page Page Chapter 1 Overview......................................................... 1 Tropical Hardwoods.......................................................78 Quality Requirements and Cost of Degrade .....................1 Kiln Start-Up Procedures ...............................................79 Basic Drying Concepts.....................................................1 Equalizing and Conditioning..........................................86 Drying Methods................................................................3 Sterilization ....................................................................88 Moisture Content..............................................................5 Drying Time ...................................................................88 References....................................................................... 6 Operational Considerations ............................................90 References......................................................................91 Chapter 2 Drying Mechanisms of Wood........................ 7 Wood Characteristics That Affect Drying........................7 Chapter 8 Advanced Kiln Drying Procedures............. 93 Environmental Factors....................................................12 Modifications to General Hardwood Schedules.............93 Rate of Drying................................................................18 Special Hardwood Schedules .........................................94 Stages of Drying.............................................................21 Adjustment of Moisture Content of Kiln-Dried Wood...95 References .....................................................................24 Alternative Schedules for Some Species ........................96 Kiln Operational Techniques..........................................97 Chapter 3 Stock Preparation and Stacking................. 25 References....................................................................102 Protection of Logs ..........................................................25 Sawing Procedures .........................................................25 Chapter 9 Drying Defects............................................ 103 Protection of Green Lumber...........................................26 Checking.......................................................................103 Prevention of Surface Checks.........................................27 Shake............................................................................105 Prevention of End Checks ..............................................27 Collapse........................................................................106 Color Enhancement Through Steaming..........................28 Warp.............................................................................106 Other Lumber Pretreatments ..........................................28 Discoloration................................................................107 Sorting............................................................................29 Problems Caused by Incorrect Lumber Stacking..........................................................................30 Moisture Content..........................................................109 Additional Ways to Control Warp..................................33 Residual Tension set (Casehardening)..........................110 References......................................................................33 Machining and Gluing Problems..................................110 Insect Damage ..............................................................111 Chapter 4 Air Drying .................................................... 35 Statistical Process Control............................................112 Advantages and Limitations ...........................................36 References....................................................................114 Utilization of Air Movement ..........................................36 Other Factors That Affect Drying Rate and Degrade .....37 Chapter 10 Special Drying Methods .......................... 115 Drying Time and Final Moisture Content.......................40 Heated-Room Drying ...................................................115 Air Drying and Shed Drying Operating Costs................43
Details
-
File Typepdf
-
Upload Time-
-
Content LanguagesEnglish
-
Upload UserAnonymous/Not logged-in
-
File Pages144 Page
-
File Size-