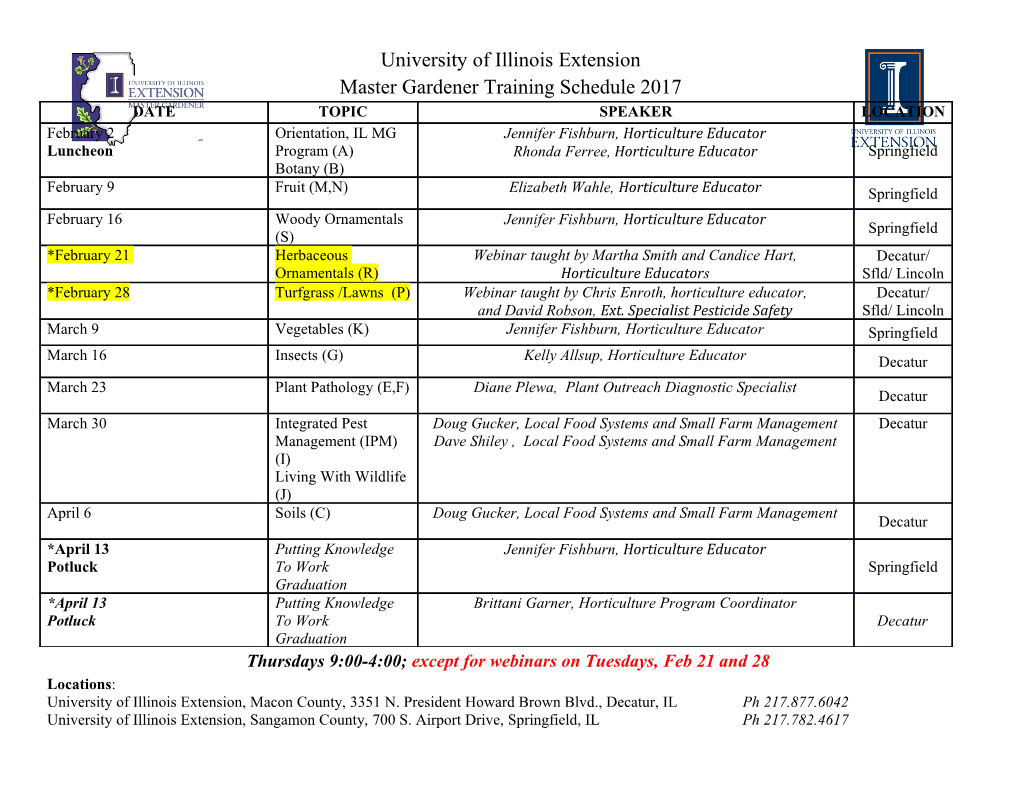
WHAT IS ? Disclaimer: This Guide to Liquidmetal® is subject to change and update at any time without notice and any errors are subject to correction without liability. Copyright: Liquidmetal Technologies, Inc. January 31, 2018 A GUIDE TO AMM TABLE OF CONTENTS 5 Chapter 1: INTRODUCTION TO AMORPHOUS METALS 6 Chapter 2: THE TECHNOLOGY & PROCESS TODAY • Company Introduction • The Beginning: From Crystal to BMGS 9 Chapter 3: HOW & WHY TO CHOOSE AMORPHOUS METALS 10 Chapter 4: DIMENSIONAL ACCURACY & REPEATABILITY • Recent Studies 12 Chapter 5: MATERIAL PROPERTIES 15 Chapter 6: CORROSION RESISTANCE & BIOCOMPATIBILITY • Salt Fog • Galvanic • Result Summary 18 Chapter 7: TECHNOLOGY COMPARISON 19 Chapter 8: NEXT STEPS 3 THE COMPANY Liquidmetal Technologies provides advanced molding solutions for complex and high-performance metal parts. The company began on the foundation of amorphous metal technology, and has now expanded process capabilities to metal injection molding (MIM). Matching every customer application with the best process available is a focus at Liquidmetal. Because of this, customers benefit from a solid technical and economic solution. INTRODUCTION 1 INTRODUCTION TO AMORPHOUS METALS THE BEGINNING: FROM CRYSTALS TO BMGS Centuries of technological advancement has led to hundreds of metal alloys, and until recently, each of them shared a common thread of a crystalline microstructure. Every crystalline alloy’s atoms arrange in naturally occurring patterns that represent the most stable form of the material. These materials exhibit broad trends that limit what can be done with them. For example, a metal’s melting temperature is usually proportional to its hardness, and a material’s strength is usually inversely proportional to its ductility. This means that alloys with low melting points (which can be cast readily) are often soft and low-strength while alloys with high melting points (which cannot be cast easily) are often hard, brittle, and high-strength. The fundamental innovations leading up to Liquidmetal’s amorphous metal technology date back to the early 1960s with the development of gold-silicon alloys that could be formed into a non-crystalline (also known as “amorphous”) microstructure at extremely high cooling rates. By designing alloy compositions around deep melting points (also called “eutectics”), the alloy could be cooled from the liquid state (where no crystal structure exists) to room temperature without forming a crystalline structure. By rapidly cooling, one could trap the Alloy in Molten State “liquid-like” microstructure into the non-crystalline (or “amorphous”) solid, creating a new class of metal alloys, which can be called amorphous. Ordinary Alloys Several decades of R&D proved Amorphous it difficult to form amorphous Atomic Naturally Crystallize metal parts thicker than a ribbon Structure < Chill Crystals < Equiaxed Grains without crystal grain boundaries < Columnar Grains (the “weak regions” in crystalline materials). In 1990, with support from NASA, Caltech formulated Vitreloy, the first bulk metallic < WEAK REGION glass (BMG) with a thickness greater than 1mm.ter than 1mm. AMORPHOUS CRYSTALLINE Figure 1. ATOMIC ATOMIC STRUCTURE STRUCTURE 5 2 THE TECHNOLOGY & PROCESS TODAY Amorphous alloys as a scientific breakthrough now impact hundreds of applications and components across a wide range of markets. To engineers, metallurgists, scientists, and business professionals alike, interest comes from material properties that are nearly impossible to form in crystalline metals, with CNC-like complex precision molding. Now, as a production-ready, high volume manufacturing solution, amorphous metals represent a host of powerful material and manufacturing capabilities. Two molding technologies exist for manufacturing amorphous alloy parts. The first is a cold-crucible process that produces very high purity alloys suitable for the medical and dental device, and implant markets. The second molding technology is a hot-crucible process that makes much larger parts with thinner walls in lower-cost alloys. The hot- crucible platform lends itself well to applications from a broad range of markets including automotive, consumer, electronics, industrial, and sporting equipment. COLD-CRUCIBLE HOT-CRUCIBLE Platform Modified plastic injection molding Modified die cast Heating Injection unit in to vacuum >1000ºC Crucible in vacuum to >1000ºC Automation Fully automated continuous production Fully automated continuous production Shot Size 100g shot size 300g shot size Max Part Weight 80g shot size 180g shot size Maximum dimension 100mm 200mm Wall thickness 0.6mm-4.0mm 0.3mm-3.0mm Table 1. A comparison of Liquidmetal's two AMM processing platforms. THE TECHNOLOGY & PROCESS TODAY The Liquidmetal molding process begins with crystalline material, which is automatically loaded into the machine for melting. Liquidmetal alloy ingots weighing up to 300 grams (depending on the process) are heated under vacuum to protect the alloys from unwanted contamination, such as exposure to oxygen. When the alloy is fully molten, the metal is injected under pressure into permanent steel molds similar to conventional plastic injection molds. Mold temperatures are controlled to cool and solidify the Liquidmetal alloy into final part geometries until the part is ready for ejection. By the time the part is ejected from the mold, it has achieved full material properties in this single-step molding process. Parts can be designed to include the same level of three-dimensional complexity as plastic injection molded parts. Figure 2. INGOT REMOVAL Amorphous alloys begin as a Parts removed from the mold crystalline ingot, and currently are in their final geometry, a maximum mass of 300 aside from gate and runner grams. The alloys are mainly removal. composed of titanium and zirconium. MELTING DEGATING Using an induction coil, melting Several cutting tools can be concludes when the material is used to remove the gate and molten at roughly 1000°C. runner, depending on the precision required. Most often CNC-machining or waterjetting is required. MOLDING RECYCLING Due to the nature of metal The Liquidmetal team takes molding, and the materials steps to recycle material that is minimal shrinkage, mold wear not used in material features, and durability is a primary mainly gate and runner focus. vestiages. 7 (Above) Liquidmetal headquarters in Lake Forest, CA. (Left) ENGEL e-motion cold-crucible molding machine for processing amorphous alloys. (Right) EONTEC hot-crucible machine for processing amorphous alloys. HOW & WHY TO CHOOSE AMORPHOUS METALS 3 HOW & WHY TO CHOOSE AMORPHOUS METALS When developing a new product design, designers of metal components must always consider the manufacturing methods available to them. At the same time, they must consider the geometric possibilities and material characteristic needs for the particular functional and performance requirements of the application for which they are designing. This is not always a simple task, as different manufacturing processes yield different results and costs. The Liquidmetal process is a combination of an unusual metal alloy with highly useful properties, and a shape forming process common to plastic components. This provides a new set of possibilities for metal parts fabrication and component designs not previously possible with other metal forming technologies. The key capabilities of the Liquidmetal process are listed below: • Exceptional dimensional control and repeatability • Excellent corrosion resistance • Brilliant surface finish • High strength • High elastic limit • High hardness, scratch & wear resistance • Non-magnetic • Complex shapes that can be molded If you need three or more of these characteristics, you likely have a Liquidmetal application. Table 2. MARKET APPLICATIONS Engine timing systems, fuel injection, fuel rail components, small precision gears, passenger safety devices, Automotive pumps, pressure sensors, ABS system components, decorative interior and exterior components, severe duty connectors, ignition systems, variable valve components Dental Tools, equipment, orthodontia brackets Medical Broad range of device applications for actuation components, clamping, cutting, piercing, sealing, stapling, Devices suturing Medical ISO 10993 Biocompatibility testing has been completed successfully, including long-term animal implant Implants studies. Pressure sensors, compressor components, power tools, hand tools, small precision gears, severe duty Industrial connectors, mechanical assemblies, poppets, valves, pumps Sporting Archery, bicycling, firearms, fishing reels, knives, recreational tools, scuba equipment Equipment 9 4 DIMENSIONAL ACCURACY & REPEATABILITY The Liquidmetal® amorphous metal process can achieve dimensional accuracy and repeatability results that are usually only common to production CNC (Computer Numerical Control) machining processes, but at a much lower cost. Today, designers can expect dimensional accuracy and repeatability of ±0.08% of a given part dimension. Liquidmetal alloy solidifies during the molding process nearly isotropically, so design sensitivities to the 0.4% solidification shrinkage of the material and dimensional tolerances of part features are insignificant. Freezing incompressible molten metal during the molding process without changes to the atomic structure of the material plays a significant role in the resulting dimensional accuracy and repeatability of the process. This highly unique aspect of dimensional control is not inherent to
Details
-
File Typepdf
-
Upload Time-
-
Content LanguagesEnglish
-
Upload UserAnonymous/Not logged-in
-
File Pages20 Page
-
File Size-