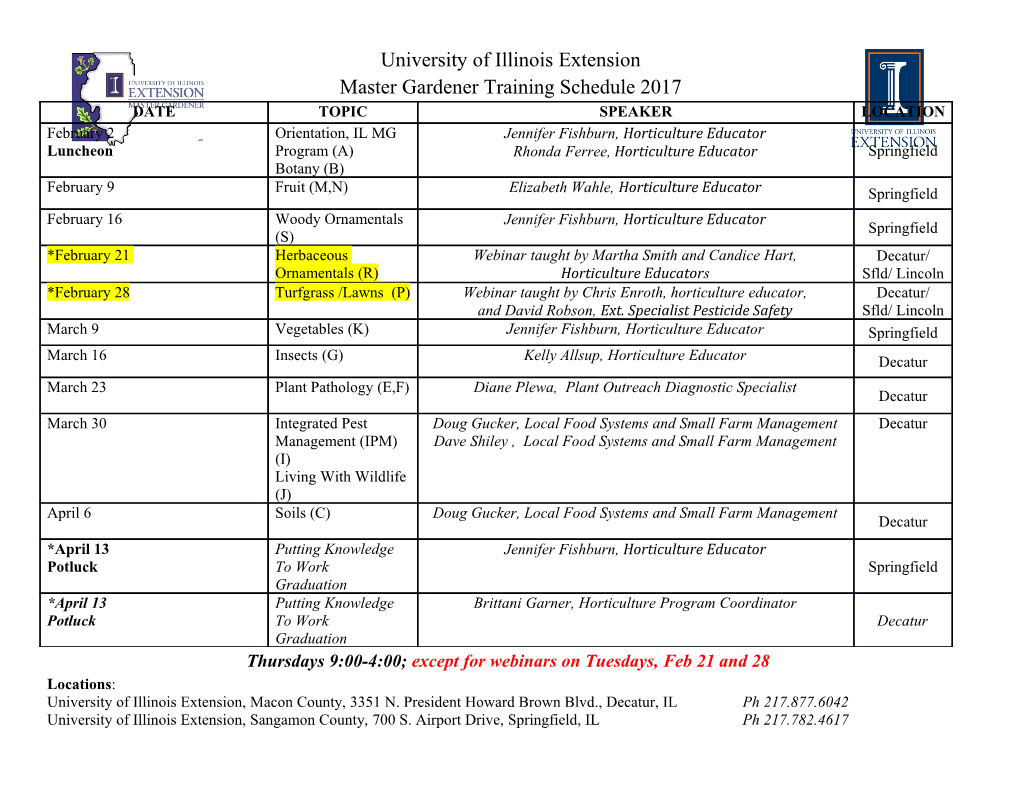
M2794.001800 M A T E R I A L A N D M A N U F A C T U R I N G P R O C E S S E S Chapter 5. Metal-Casting Processes and Equipment; Heat Treatment Prof. Ahn Sung-Hoon ( ) School of Mechanical and Aerospace Engineering Seoul National University 2 Historical casting parts Korean bronze dagger( ( )) Bronze bell( ) & molds( ) © Prof. Ahn, Sung-Hoon 3 Casting . Casting is a manufacturing process by which a molten material such as metal or plastic is introduced into a mold made of sand or metal, allowed to solidify within the mold, and then ejected or broken out to make a fabricated part. Advantages . Making parts of complex shape in a single piece. Producing large number of identical castings within specified tolerances. Good bearing qualities and jointless product. Disadvantages . Limitations of mechanical properties because of the polycrystalline grain structure. Poor dimensional accuracy due to shrinkage of metal during solidification. If the number of parts cast is relatively small, the cost per casting increases rapidly. Fundamental aspects in casting operations . Solidification of the metal from its molten state. Flow of the molten metal into the mold cavity. Heat transfer during solidification and cooling of the metal in the mold. Mold material and its influence on the casting process. © Prof. Ahn, Sung-Hoon 4 Solidification of Metals © Prof. Ahn, Sung-Hoon 5 Solid solution . Solute( ) . Solvent( ) . When the particular crystal structure of the solvent is maintained during alloying, the alloy is called solid solution. Substitutional solid solution( ) . Interstitial solid solution( ) . 5.2.2 Intermetallic compound( ) . Complex structures in which solute atoms are present among solvent atoms in certain specific proportions. 5.2.3 Two-phase system( ) . Phase: a homogeneous portion of a system that has uniform physical and chemical characteristics © Prof. Ahn, Sung-Hoon 6 Polycrystalline alpha brass © Prof. Ahn, Sung-Hoon 7 Phase diagram ( ) Graphically illustrates the relationships among temperature, composition, and the phase present in a particular alloy system. Lever Rule S C C O L S L CS CL L C C S O S L CS CL © Prof. Ahn, Sung-Hoon 8 Lever-Rule ( ) © Prof. Ahn, Sung-Hoon 9 Eutectic system, Pb-Sn © Prof. Ahn, Sung-Hoon 10 Types of 3-phase invariant reactions © Prof. Ahn, Sung-Hoon 11 Iron-carbon system (1) . Pure iron( ) : 0.008% C . Steels( ) : 2.11% C . Cast irons( ) : ~6.67% C . a-ferrite( ): BCC, soft and ductile . d-ferrite: BCC, stable only at very high temperatures . Austenite( ) : FCC, ductile . Cementite( ): Fe3C, C 6.67%, iron carbide( ), brittle © Prof. Ahn, Sung-Hoon 12 a-ferrite & austenite a-ferrite (x 90) Austenite (x325) © Prof. Ahn, Sung-Hoon 13 Iron-carbon system (2) © Prof. Ahn, Sung-Hoon 14 Eutectoid steel . a- ferrite: white . Fe3C: dark . Lamellar structure (pearlite) . (x 500) © Prof. Ahn, Sung-Hoon 15 1% carbon (hypereutectoid) pearlite steel . a- ferrite - white . eutectoid - cementite - blue . proeutectoid - cementite - violet . (x 500) © Prof. Ahn, Sung-Hoon 16 Classification of ferrous alloys © Prof. Ahn, Sung-Hoon 17 Composition and naming steels © Prof. Ahn, Sung-Hoon 18 Amount of phases in carbon steel Casting 1040 steel 10kg, calculate a phase and g phase at (a) 900 C, (b) 728 C and (c) 726 C (a) Austenite:100% g Cg Co 0.77 0.40 (b) a(%) 100 100 50%, that is 5kg, Cg Ca 0.77 0.022 C C 0.40 0.022 g (%) o a 100 100 50%, that is 5kg, Cg Ca 0.77 0.022 6.67 0.40 (c) a 100 94%, that is 9.4kg 6.67 0.022 © Prof. Ahn, Sung-Hoon 19 Cast irons . Fe, C 2.11~4.5%, Si ~3.5% . According to solidification morphology : Gray cast iron( ) . Flake graphite( ) . Gray fracture surface( ) . Damping( ) Ductile(nodular) iron( ) . Ductile White cast iron( ) . Large amount of Fe3C . Brittle . White fracture surface( ) Malleable cast iron( ) . Obtained by annealing white cast iron Compact graphite iron( ) © Prof. Ahn, Sung-Hoon 20 Cast irons © Prof. Ahn, Sung-Hoon 21 Cast irons © Prof. Ahn, Sung-Hoon 22 Ternary phase diagram . Fe-Cr-Ni © Prof. Ahn, Sung-Hoon 23 Cast structures . Pure metal vs. alloys © Prof. Ahn, Sung-Hoon 24 Dendrites ( ) © Prof. Ahn, Sung-Hoon 25 Dendrites © Prof. Ahn, Sung-Hoon 26 Fluid flow v c 2gh p v2 h constant g 2g p v 2 p v 2 h 1 1 h 2 2 f 1 g 2g 2 g 2g Q A1v1 A2v2 A h 1 2 A2 h1 vD Re © Prof. Ahn, Sung-Hoon 27 Solidification time & shrinkage . Chvonrinov’s rule Solidification time = C(volume/surface area)2 . Shrinkage occurs at . Molten metal . Phase change . Solid metal . Cast iron expands . Graphite has high volume/mass . Net expansion during precipitation . Similarly Bi-Sn alloys expand © Prof. Ahn, Sung-Hoon 28 Defects/DFM © Prof. Ahn, Sung-Hoon 29 Casting alloys © Prof. Ahn, Sung-Hoon 30 Applications © Prof. Ahn, Sung-Hoon 31 Properties © Prof. Ahn, Sung-Hoon 32 Casting processes . Expendable mold, permanent pattern . Sand casting . Shell-mold casting . Plaster mold casting . Ceramic mold casting . Vacuum casting © Prof. Ahn, Sung-Hoon 33 Casting processes (2) . Expendable mold, expendable pattern . Evaporative-pattern casting (lost foam) . Investment casting (lost wax) © Prof. Ahn, Sung-Hoon 34 Investment casting © Prof. Ahn, Sung-Hoon 35 Casting processes (3) . Permanent mold . In permanent-mold casting, a mold are . Slush casting made from materials such as steel, bronze, refractory metal alloys, or . Pressure casting graphite. Because metal molds are better . Die casting heat conductors than expendable molds, . Centrifugal casting the solidifying casting is subjected to a . Squeeze casting higher rate of cooling, which turn affects . Semisolid metal forming the microstructure and grain size within . Casting for single crystal the casting. Rapid solidification . Cooling methods : water, air-cooled fin . Used for aluminum, magnesium, and copper alloys due to their lower melting points . Pros : good surface finishing, close dimensional tolerances, and uniform and good mechanical properties . Cons : not economical for small production runs, not good for intricate shapes © Prof. Ahn, Sung-Hoon 36 Pressure casting/centrifugal casting © Prof. Ahn, Sung-Hoon 37 Die casting . Hot-chamber process . Cold-chamber process © Prof. Ahn, Sung-Hoon 38 Squeeze casting/single crystal © Prof. Ahn, Sung-Hoon 39 Casting for single crystal Crystal-pulling method floating-zone (Czochralski process) method © Prof. Ahn, Sung-Hoon 40 Heat treatment-ferrous alloys . Pearlite . Spheroidite . Bainite . Martensite . Quenching( ) . Body Centered Tetragonal(BCT) . Retained austenite . Tempered martensite © Prof. Ahn, Sung-Hoon 41 Transformation-ferrous alloys Austenite Slow cooling Quenching Moderate cooling Pearlite Martensite (a+Fe3C) (+proeutectic a) Bainite reheat (a+Fe3C) Tempered martensite © Prof. Ahn, Sung-Hoon 42 Ferrous alloys © Prof. Ahn, Sung-Hoon 43 Shape memory alloy (SMA) © Prof. Ahn, Sung-Hoon 44 Quenched AISI 9310 steel . The white strikes are excess proeutectoid cemetite . Cream color is retained austenite . Gray area is bainite . Blue/brown regions are martensite . (x 320) © Prof. Ahn, Sung-Hoon 45 Nonferrous alloys/stainless steel (1) Precipitation hardening Age hardening( ) ( ), Al-Cu alloy © Prof. Ahn, Sung-Hoon 46 Nonferrous alloys/stainless steel (2) . Solution treatment . Precipitation hardening . Aging . Maraging(martensite + aging) © Prof. Ahn, Sung-Hoon 47 Case hardening . Surface hardening . Carburizing ( ) . Carbonitriding ( ) . Cyaniding ( ) . Nitriding ( ) . Boronizing ( ) . Flame hardening ( ) . Induction hardening ( ) © Prof. Ahn, Sung-Hoon 48 Annealing ( )/ tempering ( ) . Normalizing( ) © Prof. Ahn, Sung-Hoon 49 Design consideration (1) © Prof. Ahn, Sung-Hoon 50 Design consideration (2) © Prof. Ahn, Sung-Hoon 51 Design consideration (3) © Prof. Ahn, Sung-Hoon 52 Economics of casting © Prof. Ahn, Sung-Hoon 53 Case study © Prof. Ahn, Sung-Hoon 54 Bridge design © Prof. Ahn, Sung-Hoon 55 Material of the bridge Another bridge © Prof. Ahn, Sung-Hoon.
Details
-
File Typepdf
-
Upload Time-
-
Content LanguagesEnglish
-
Upload UserAnonymous/Not logged-in
-
File Pages55 Page
-
File Size-