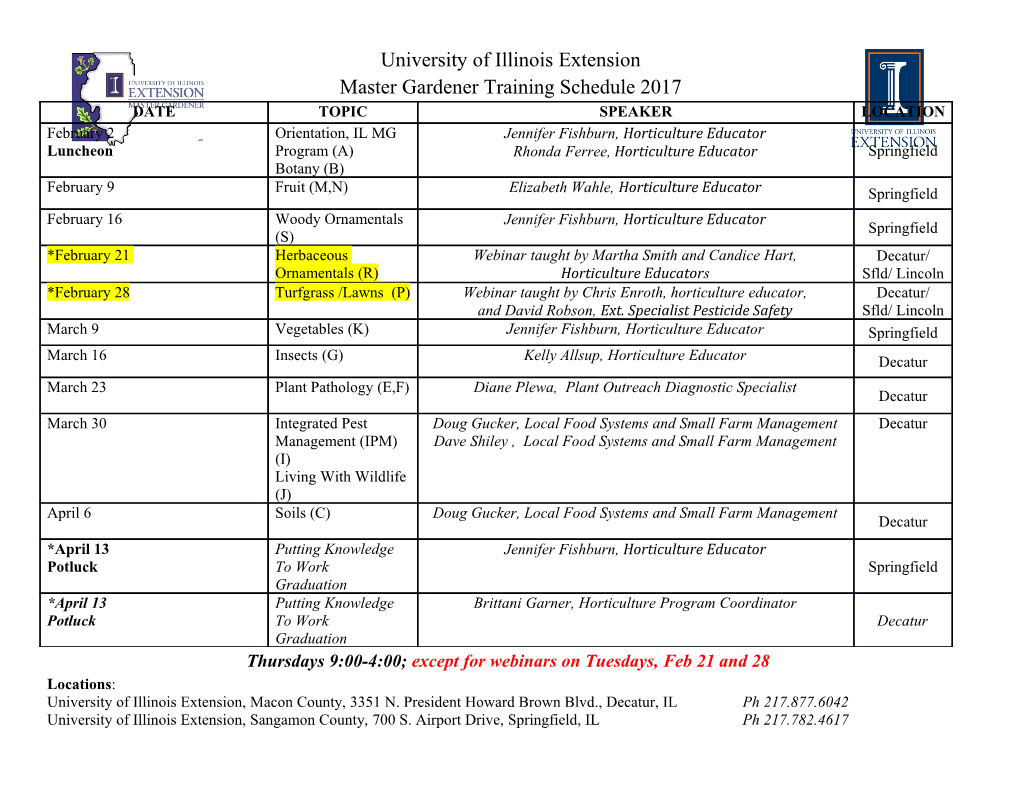
NuclearAMRC Q1 2014 news ISSUE 14 First light UK’s largest electron beam welding chamber fires up £13m research funding Hargreaves gets Fit For Nuclear Triple Bar Nuclear Manufacturing EUROPEAN UNION NNL collaboration Investing in Your Future European Regional Small modular reactors Development Fund 2007-13 ALSO IN THIS ISSUE Three AP1000s for Moorside 100mm weld promises Joined-up thinking: full-size deep benefits cross-section of a single e-beam weld Nuclear AMRC welding specialists have welds – between 20 and 80 runs for a 100mm with a horizontal beam, and successfully joined 100mm thick steel plates with thick section – with repeated non-destructive you still have to keep the metal a single weld. The landmark result means that evaluation (NDE) to ensure material quality. contained.” welding time for large pressure vessels could be With an electron beam, it takes just one weld and reduced from weeks to hours. one round of NDE. Electron beam welding also Initial tests show that the reduces the requirement for pre-weld machining, join has excellent material The team used electron beam welding, which as it requires a simple butt rather than a v-shaped properties, comparable to the is capable of joining much thicker components weld prep. plate material. The team has in a single run than other welding technologies also achieved 80mm single-pass while maintaining high material quality. The Baufeld’s team used the Nuclear AMRC’s joins in stainless steel and 85mm technique has become accepted in the aerospace Pro-Beam K25 to demonstrate the techology’s in nickel-base alloy. and automotive industries, but is not yet used in feasibility for nuclear applications. They achieved a WELDING FOCUS nuclear manufacturing. 100mm depth of weld using SA508 grade 3 steel, Baufeld and the team are commonly used in civil nuclear pressure vessels, continuing to develop the “Parts which would traditionally be welded in at a rate of 18cm per minute. technique to produce larger weeks could be welded in one day,” says Bernd demonstration parts, and apply Baufeld, power beam technology leader at the “100mm is at the border of what’s traditionally the lessons learned on the K25 Nuclear AMRC. “E-beam welding has a major done in the e-beam world,” Baufeld notes. to the Nuclear AMRC’s giant advantage in cutting costs for pressure vessels and new K2000 e-beam chamber other large nuclear components by reducing the One of the biggest challenges was dealing with (see below). time of production.” the several cubic centimetres of liquid metal produced by the electron beam. “You can’t weld • To find out more about the Nuclear AMRC’s Pressure vessel walls are currently joined by with a vertical beam because you’d lose metal electron beam welding capabilities, contact multiple tungsten inert gas or submerged arc through dripping,” says Baufeld. “You have to weld Bernd Baufeld: [email protected] This photo shows the first firing of the Nuclear AMRC’s Pro-Beam K2000 electron beam welding chamber. At over 80 times the volume of the established K25 facility, First firing for giant the K2000 is believed to be the largest e-beam chamber in the UK. The 208m3 chamber arrived at the Nuclear electron beam AMRC in three sections in May 2013. Thanks to the hard work of the Pro-Beam installation team, its gun was fired for the first time shortly before Christmas. The cell will be fully commissioned and available for collaborative research from the end of March. The Pro-Beam K2000 gives the capability to complete very intricate joins on large components using nine axes of movement – four for the component and five for the electron gun. It can be used to weld gas turbine parts up to three metres in diameter, with fully automatic joint following and variable thickness programming – capabilities found in only a handful of machines worldwide. The Nuclear AMRC power beam team is currently scoping initial collaborative projects with civil nuclear partners. The chamber’s capabilities can also be exploited by manufacturers serving other sectors such as offshore renewables and aerospace. Nuclear AMRC news Q1 2014 2 High speed cladding with high power laser Next generation of cladding: simulation of the Nuclear AMRC’s diode laser cell The Nuclear AMRC is adding diode laser cladding The Nuclear AMRC’s new facility features a Research will initially focus on proving the viability to its R&D capabilities, with a high power cell being 15kW Laserline fibre couple diode laser on a of diode laser cladding for civil nuclear pressure commissioned this spring. gantry-mounted robot arm, inside a cell measuring vessels. The cell will also be available for collaborative 10 metres square. The cell will be capable of research and development for other industries Diode laser cladding uses a powerful laser to rapidly depositing stainless steel, nickel alloys, wear-resistant requiring large-scale surface enhancement. coat large areas of metal with a high quality layer alloys and other specialist cladding material at rates of speciality alloy. Currently used in the aerospace, of up to 10kg an hour. The team will also use the facility to investigate automotive and offshore industries, it can potentially an innovative smoothing technique developed at revolutionise the production of pressure vessels “This is one of the most powerful diode lasers Rolls-Royce. An initial project used a diode laser for civil nuclear. Compared with current methods commercially available,” says Bernd Baufeld, power cell to produce a surface which is at least as smooth used to clad vessel interiors, such as conventional beam technology lead at the Nuclear AMRC. as a traditional machined surface, with an average wire or strip cladding, diode laser cladding can cut “As a research and development facility, we can roughness value (Ra) of 1.7μm. “This will allow us to production time from weeks to hours. work with large pieces and bridge the gap between clad a component and achieve a high quality surface small university-scale development and final large- finish in one set up, drastically reducing production scale production.” costs,” says Baufeld. 3 namrc.co.uk Growing potential for additive Proof of concept: SMD can create energy manufacturing sector parts from welded wire Large parts for the energy industry can be In these markets, large components are typically “SMD gives material properties which are at WELDING FOCUS made using an innovative weld-based additive made from welded fabrications of cast or least as good as conventional casting, with tighter manufacturing technique, a new study has shown. forged components. These can be weakened process monitoring and control for tailoring by impurities and defects from various stages of material properties,” says Woy. “We’re now Shaped metal deposition (SMD) produces the production process, which are often only investigating the problems encountered while near-net components by welding a continuous identified after fabrication is completed. Additive building the representative part, and exploring metal wire into the desired shape. This reduces manufacturing techniques such as SMD which other part geometries and features.” the material waste involved in machining parts feature in-process monitoring can radically reduce from a larger forging, and removes the need for these expensive defects, while cutting production The team is also looking at commissioning a larger the expensive tooling used in processes such time and material waste. SMD cell to create parts of up to two metres as casting. diameter. The basic technique can also be applied “Because SMD is basically a welding process to some of the other welding technologies at The technique was created at Rolls-Royce, which is widely accepted and used in industry, the Nuclear AMRC, including the new 200m3 and developed for aerospace applications in a it’s a relatively low-risk approach to nuclear electron beam chamber which includes a wire major collaborative project called Rapolac led industry manufacturing compared with other feed mechanism. by the University of Sheffield AMRC. Rapolac innovative technologies,” says Udi Woy, additive demonstrated the commercial viability of the manufacturing technology lead at the Nuclear “We’re very interested in exploring new technology, and developed an automated control AMRC. “However, there’s still a lot of work to get applications for SMD with companies,” says Woy. system while optimising the process to improve it to the stage where it can go into production.” “For the energy sector, it’s a very potent additive material properties. manufacturing technology.” To investigate the technique’s potential, the SMD The pilot SMD cell, now located in the Nuclear team produced a representative part, featuring • For more information on SMD and other AMRC research factory, features a robotically- two abutting cylinders, from 316L austenitic additive manufacturing techniques, contact controlled tungsten arc welding head within an stainless steel wire. The part was then analysed Udi Woy: [email protected] argon-atmosphere cell. It has seen interest from a to characterise its microstructure, mechanical number of sectors, including from manufacturers properties and chemical composition and – apart in the nuclear, oil and gas, and offshore from some material flaws thought to be caused by renewables supply chains. programming errors – met all requirements. £13 million for collaborative R&D Companies are invited to bid for £13 million of collaborative research funding to The programme includes up to £10 million for business-led collaborative help develop the UK’s civil nuclear supply chain. R&D projects. Qualifying projects will generally have a value of between £500,000 and £3 million, and last two to three years. Businesses can claim up The programme, backed by the Technology Strategy Board, Department of to half of their project costs, or 60% for SMEs.
Details
-
File Typepdf
-
Upload Time-
-
Content LanguagesEnglish
-
Upload UserAnonymous/Not logged-in
-
File Pages12 Page
-
File Size-