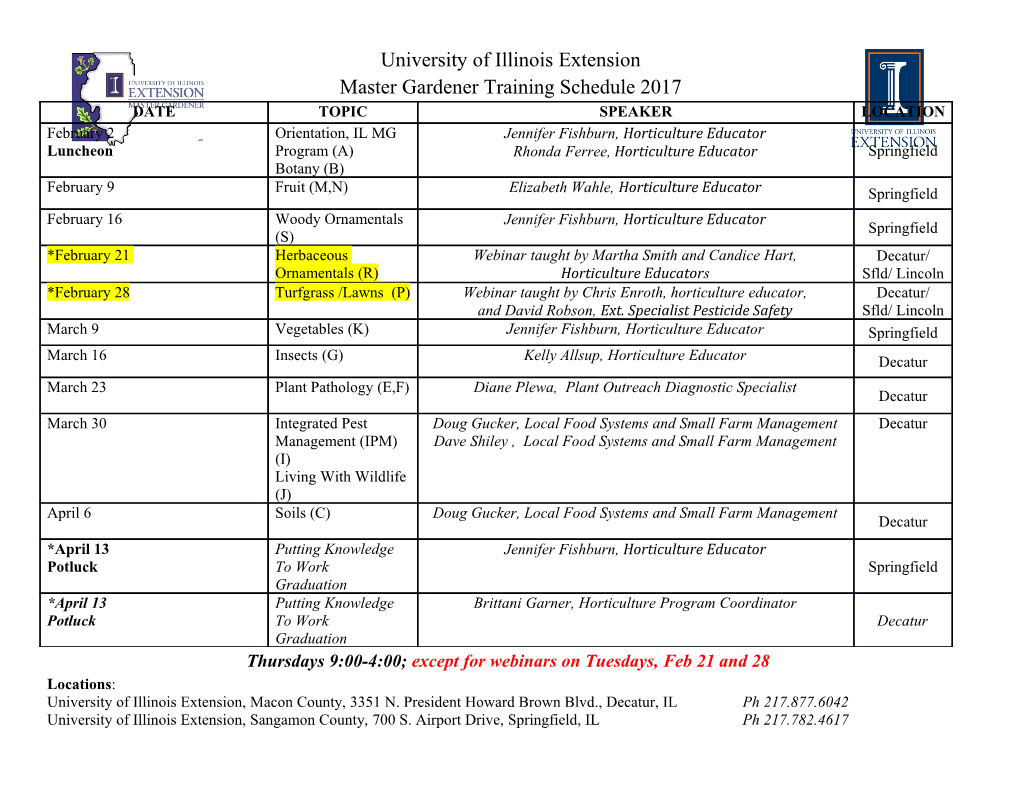
Waldemar Cierpucha, Applicability of Flax and Hemp as Raw Ryszard Kozłowski, Jerzy Mańkowski, Materials for Production of Cotton-like Józef Waśko, Tomasz Mańkowski Fibres and Blended Yarns in Poland Institute of Natural Fibres Abstract ul. Wojska Polskiego 71 b, 60-630 Poznań, Poland This paper contains a review of basic research and new concepts in flax and hemp fibre processing for flax and hemp cotton-like and wool-like yarns spun by different spinning systems. The review covers the trends and economical conditions since the beginning of the 20th century. We present the advantages and disadvantages of flax and hemp as raw materials for the production of cottonised fibres from the agricultural and economical point of view. Some significant morphological differences between flax and hemp are highlighted regarding the applicability of these fibres to the cottonisation process and spinning in blends with cotton by the pneumatic-mechanical spinning system. The content of mechanically obtained flax and hemp cottonised fibres in blends with cotton and the range of linear density of yarns is discussed. Examples of blended yarns with flax and hemp cottonised fibres applied in ready-made products are also presented. Key words: flax, hemp, cotton-like fibres, cottonised fibres, blended yarns, elementary fibres, production of blends, cotton, wool, polyester (PET), polyacrylonitril (PAN). tonised fibres; they produced it on their To increase the economics of flax and own initiative, and added it to cotton hemp utilisation, in the 1970s studies in blends. At that time, the state effectively applying these raw materials in non-flax n Introduction supported the domestic flax industry processing technologies were initiated. through tax reductions for enterprises Many experiments were carried out to Poland has a rich and long tradition of which used cottonised fibres. It should manufacture and apply cottonised fibres cultivating and processing flax and hemp. be emphasised that at that period, up in yarn blends produced by unconven- The flax and hemp multi-cell fibre was to 40,000 tonnes of cottage-worked tional spinning technologies. processed into yarn according to tradi- flax and hemp fibre was manufactured tional flax spinning technology [8, 9, 11, annually (cultivated on c. 100,000 ha) Efforts at utilising flax and hemp in dif- 12, 36, 37, 46]. The materials spun were [36]. Most of the fibre was effectively ferent spinning systems and raw mate- technical flax and hemp long and short exported abroad. Before 1939, attempts rial compositions are documented in (two-type) fibre. The spinning was carried at hemp cotton-like cottonised fibres numerous publications. These studies out by the wet (with possible boiling and production were initiated in Italy [47]. were characterised by different ranges of bleaching of fibre) and the dry method. The content of hemp cottonised fibres in flax and hemp content, and by scales of The flax spinning system, in comparison these blends was 12.5-50%. The linear research, from laboratory and semi-tech- to other spinning systems such as the density of the yarns obtained was about nical to full industrial. Over time, these cotton or woollen system, is more labour- 100 tex. However, the spinning process non-flax technologies were improved, consuming and costly. was more difficult when compared to the content of cotton- or wool-like fibre pure cotton yarns; this resulted in lower was increased, and the resulting yarns One possibility of more effective utilisa- efficiency of the spinning frames. The were thinner. tion of flax and hemp in non-flax technolo- yarn also had lower tenacity in com- gies is to adapt these fibres for spinning by parison to pure cotton yarn. Thus, the The studies were conducted by the In- modifying them by cottonisation, which technology was not implemented com- stitute of Natural Fibres (previously the yields cotton- or wool-like fibres. The first mercially. Institute of Domestic Natural Fibres) in scientist who suggested utilising flax and Poznań, the Textile Research Institute in hemp for cotton-like cottonised fibre in After the Second World War, the Łódź, the Technical University of Łódź, textiles was Prof. Bratkowski [5-7]. He processing potential of flax and hemp and the R&D Centre of Flax Industry in justified his special interest in hemp and increased considerably, due to the Żyrardów. flax by the fact that these fibres were a increase in their cultivation area up domestic raw material of strategic im- to 150,000 ha (60,000 tonnes of fibre Over the last 20 years, many technolo- portance for Poland, and they could (after yield) [12]. gies have been developed for spinning certain modification) partially replace and processing flax and hemp in blends imported cotton. This opinion was stated In traditional processing technology, with cotton, wool and chemical fibres. at the beginning of the twentieth century. flax was mainly used for thin yarns Unfortunately, due to the extremely unfa- At that time Prof. Bratkowski was the devoted to light fabrics (mainly shirts, vourable conditions of the textile industry initiator of innovative research conducted underwear, tablecloths, curtains and restructuring over this period, especially on manufacturing flax and hemp cotton- clothes). On the other hand, hemp was since 1990, many companies were closed ised fibres and spinning it in blends with mainly used for the production of thick or had to reduce their production, among cotton. After the First World War, cotton yarns and technical fabrics (tarpaulins, them companies processing flax and spinning mills were very interested in cot- twine, and farm string). hemp cottonised fibres in blends. FIBRES & TEXTILES in Eastern Europe July / October 2004, Vol. 12, No. 3 (47) 13 n Studies on Utilisation further technologies for manufactur- contamination level was achieved which of Flax and Hemp in Woollen ing blended yarns were included. The finally allowed spinning in blends with Spinning System composition was 20% hemp/80% PAN; chemical fibres by the cotton spinning the linear density ranged between 32 tex system [1-4]. This fibre was called ‘pa- Woollen combing system and 64 tex. kulen’. The ‘pakulen’ technology was The first studies in Poland into the implemented in the Włóknolen retting modification of flax for manufacturing Flax cottonised fibre was also used plant in Lębork. The ‘pakulen’ fibre was wool-like cottonised fibres were carried for spinning biological, enzyme-treated used for manufacturing blended yarn out in 1972-1974, when garments made noils by the woollen system, according with a linear density of 40 tex, containing of natural fibres were very popular in to a method developed at the Institute of 40% ‘pakulen’ and 60% PAN. domestic and international fashion. The Natural Fibres. The resulting yarn was fibre obtained was named Milen [38-40]. composed of 50% linen and 50% wool, Research was also conducted into apply- The tests were carried out with chemi- with a linear density of 32 tex [42,44]. ing mechanically obtained, cotton-like cally modified flax biological noils. The flax cottonised fibres in the ZPDz Sigma- modified (bleached) fibre in the form Woollen carding system tex cotton mill in Piotrków Trybunalski of slivers was processed in blends with The woollen carding system was used for [41]. The material for these tests was wool or chemical fibres by the combing the production of blended yarns with a Ns10 and Ns12 flax noils. The param- or carding woollen system. linear density of 84-134 tex [38-40]. For eters of the cottonised fibres obtained the investigation ‘Milen’ yarn was used; were as follows: length 25-35 mm, linear The weaving yarns obtained in the card- this is a cottonised wool-like flax, chemi- density 1.5-2.0 tex, impurities content ing system had a linear density of 32 cally processed. The spinning trials were 1.5%. It was found that in the Sigmatex tex and were available in the following conducted at the Bardowski company in conditions, it was possible to produce compositions: 60% PET/35% flax, or Łódź. three-component blended yarns contain- wool 65% wool/35% flax. The blend ing 20% linen, 50% cotton, and 30% linen 25% flax/25% PET/50% PAN was The first trials on spinning wool-like PET. The best spinning performance used for manufacture weaving and knit- cottonised fibres were conducted by was at linear densities of 25 and 30 tex. ting yarns with a linear density of 32-36 the woollen carding spinning system The company manufactured a cotton-like tex. The results were implemented in the [10, 17, 20]. The one-type hemp fibre yarn with a maximum linen content of Polish companies Vigoprim, Tomtex and and modified dew-retted hemp noils were 20%. Any higher flax content caused Norbelana, among others. used for the trials. The modification of technological problems in ring spinning. noils included variants of single and re- Broader research on the application peated processing by a tearing machine. Tests aimed at establishing the impact of of flax in spinning by woollen system The cottonised fibre was manufactured the physical and chemical modification was conducted using a wool-like fibre mechanically. The average length of the of flax fibre on the quality of cotton- obtained by mechanical processing of fibre obtained was 70-100 mm, at a very ised fibres were also conducted [11, 21, dew-retted noils [13-16,18]. The trials high linear density of 4.57-4.76 tex. 26-29, 31]. Yarns containing 20% and yielded a wool-like fibre with an average 50% of cottonised, cotton-like flax fibre fibre length of about 94 mm and a lin- The manufactured blend of 40% hemp, were manufactured on laboratory scale ear density of 2.3 tex, and were used for 30% wool and 30% PAN had a linear for comparison.
Details
-
File Typepdf
-
Upload Time-
-
Content LanguagesEnglish
-
Upload UserAnonymous/Not logged-in
-
File Pages6 Page
-
File Size-