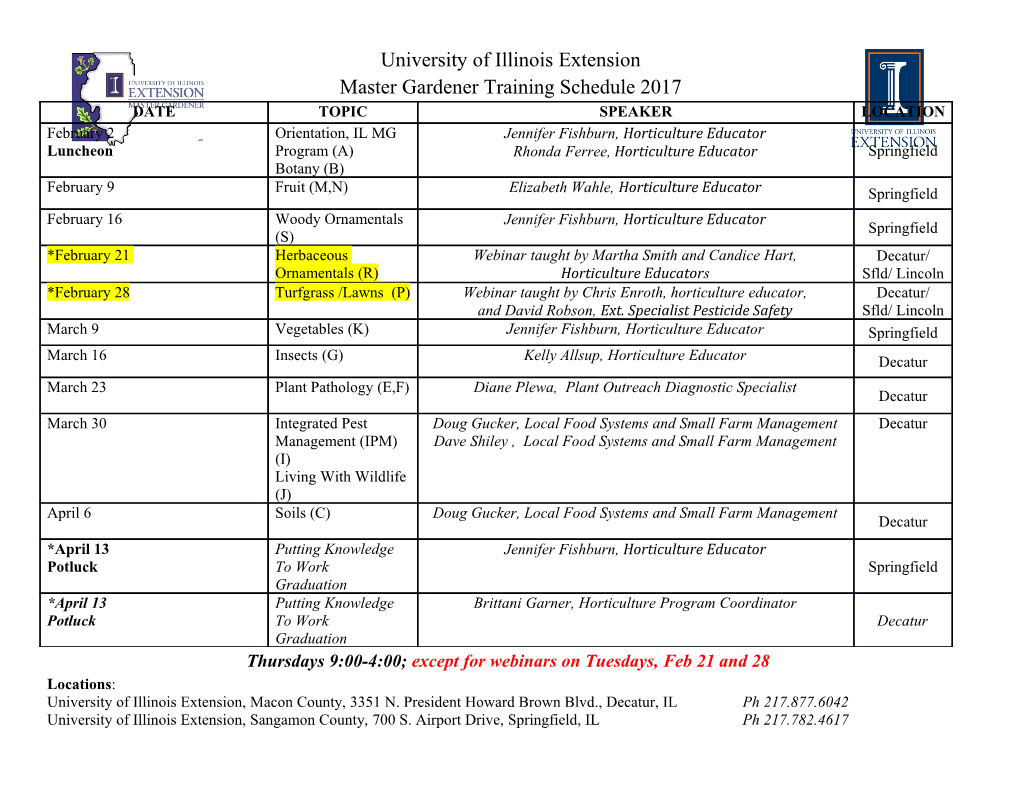
Sci Eng Compos Mater 2017; 24(4): 581–590 Xiaodan Yuan, Wenxian Wang*, Xiaoqing Cao, Tingting Zhang, Ruishan Xie and Ruifeng Liu Numerical study on the interfacial behavior of Mg/Al plate in explosive/impact welding DOI 10.1515/secm-2015-0316 Received March 13, 2015; accepted October 11, 2015; previously 1 Introduction published online December 18, 2015 Magnesium alloys, one of the lightest structural metals Abstract: In this study, the process of explosive welding with a density one-third lighter than that of aluminum of Mg/Al plate is represented, and the interfacial behavior alloys, have been researched extensively for industrial of two metals is researched. The objective of this work is applications during the past decades [1]. However, the to investigate the factors that affect the quality of explo- poor corrosion resistance of magnesium limits its appli- sive bonding and the distribution of physical parameters cation in industry. Aluminum alloys, which offer high on the collision. A finite difference engineering package strength-to-weight ratio, good formability, and good cor- with smoothed particle hydrodynamics method is used rosion resistance, are widely used in the aerospace and to model the oblique impact of a thin flyer plate (Al) on automobile industries [2]. Composite laminates of magne- a relatively thick base plate (Mg). Wavy interface and jet- sium alloys and aluminum alloys, which take advantage ting phenomenon, which existed in the experiment, are of their high specific strength and overcome disadvan- well reproduced in the simulation. The contours of pres- tages of magnesium alloys, would be promising structural sure, shear stress, velocity, and effective plastic strain of materials. Therefore, the technology for joining aluminum magnesium and aluminum are also distinctly described. alloys to magnesium alloys is required for manufacturing The bonding turns out to be a possible solid-state welding new structural materials. Recently, macroscopic compos- process. The effective plastic strain exceeds a minimum ites and/or multilayer laminates of aluminum and mag- value, and the shear stress is just the opposite sign in this nesium alloys have received much attention [3–9]. This simulation where available bonding occurred. Wave for- composite laminate may own a good combination of the mation appears to be the result of variation in the veloc- properties of aluminum and magnesium alloys. ity distribution on the interface and periodic disturbances By traditional techniques, brittle intermetallics are of magnesium and aluminum. A transition from straight easy to generate on the bonding interface of magnesium to wave occurs along the interface. High values of plastic alloys and aluminum alloys, which greatly reduce plastic- strain of two metals are predicted on the interface. ity [10–12]. The aim of this study is to produce a composite plate via cladding aluminum alloys plate to magnesium Keywords: impact/explosive welding; jetting; Mg/Al; sim- alloys plate by explosive welding. High energy rate ulation; wave. welding methods are capable of producing good-quality and large-area bonding bi-metal plates, including plates with grossly different mechanical properties [13]. As a main method, explosive welding has been developed and widely applied in industry production for decades. *Corresponding author: Wenxian Wang, College of Materials As one of the joining technologies, explosive welding has Science and Engineering, Taiyuan University of Technology, 79 West a number of benefits in comparison with other conven- Yingze Street, Taiyuan 030024, Shanxi Province, China, tional welding techniques. The primary advantage is its e-mail: [email protected]; and Key Laboratory of Interface Science and Engineering in Advanced Materials, Ministry of capability to fabricate layered target with a high-quality Education, 79 West Yingze Street, 030024 Taiyuan, Shanxi Province, metallurgical bonding between similar or dissimilar China metal plates [14–19], such as steel-steel plates [14, 15], Xiaodan Yuan, Xiaoqing Cao, Tingting Zhang, Ruishan Xie and titanium-stainless steel clad plates [16], titanium-alu- Ruifeng Liu: College of Materials Science and Engineering, Taiyuan minum clad plates [17], copper-stainless steel clad plates University of Technology, 79 West Yingze Street, 030024 Taiyuan, Shanxi Province, China; and Key Laboratory of Interface Science and [18], or other multi-layer materials. Another advantage is Engineering in Advanced Materials, Ministry of Education, 79 West higher bonding strength than the flyer plate or the base Yingze Street, 030024 Taiyuan, Shanxi Province, China plate. In addition, it allows the fabrication of large-scale 582 X.D. Yuan et al.: Study on the interfacial behavior of Mg/Al plate composite plates. In the process of welding, some com- process [24] have been investigated. With regard to the plicated physical phenomena, such as explosion, high- numerical simulation, FEM has been applied to simu- speed collision, plastic deformation of metal plates, late the explosive welding in recent works. EI-Sobky and interaction of different materials, moving interface or free Blazynski studied the explosive welding process using a surface, and high-temperature and high-pressure states, liquid analogue, which is based on the similarity between occur in very short duration due to detonation effect of hydrodynamic fluid behavior and material deformation the explosive [20]. Furthermore, the process is capable of in explosive welding. Lazari and Al-Hassani analyzed the joining with high surface areas due to its ability to dis- transient response of metal plates under explosive loading. tribute the high energy density through explosion [21]. A Oberg et al. simulated the process employing Lagrangian schematic illustration of explosive welding is shown in finite difference code method but only obtained jetting. In Figure 1. The flyer plate impacts on the base plate after Akihisa’s [24] paper, wavy interface was formed, but there explosion. The metal plates are made to collide obliquely was not any jetting reproduced. Akbari Mousavi et al. with each other at high velocity after the detonation of studied the process using Euler processor. The materials at the explosive charge with rate Vd. The flyer plate col- the collision point were considered to behave like a liquid. lides to the base plate with rate Vp under the impetus of The straight or wavy interface and jetting phenomena the detonation wave. During the high-speed impact of were modeled, and the velocity of jet was also predicted. metal plates, a high-speed jet is produced between the Euler computation can be applicable to plate impact, but metal plates. The appropriate impact angle β and impact historical process is difficult to be understood [25]. Akbari velocity Vp are required for well-bonding. Collision point Mousavi and Burley [26] also simulated the explosive S moves forward with rate Vcp governing the time avail- welding of titanium and steel plates using the model of able for bonding. The high pressure during the collision low detonation velocity explosives and analyzed two cri- process also leads to considerable local plastic deforma- teria that form the basis of a welding window including tion of the metals in the bonding zone. The process of the shear stress and plastic strain. However, their simulations explosive welding is finished in an instant, as the release did not model the whole adhesion process of two sur- of explosive energy and the interaction of metal system faces. Akbari Mousavi and Al-Hassani [27] used ABAQUS are completed in microseconds. with Arbitrary Eulerian Lagrangian formulation to model Therefore, explosively driven impact welding is a true the process of explosively driven plate. But only the last example of multidisciplinary research, as the phenomena contacting layers were shown in the ABAQUS figures. In associated with it fall under the various branches of engi- addition, the wave interface is not obvious. Tanaka [28] neering science. As a multidisciplinary research field, the simulated the explosion and gained well wave structure mechanism of explosive welding has been explored by and jetting using smoothed particle hydrodynamics (SPH) many investigators in the past several years. Some vari- method. SPH is a gridless Lagrangian hydrodynamics eties of research work about the welding interface [14], using particles. Unlike conventional Lagrangian tech- bond strength [22], welding window theory [19], joint niques, SPH avoids mesh tangling and is therefore much mechanism [23], and numerical simulation of welding more robust in its treatment of problems with large mate- rial distortions [29]. Therefore, in this work, SPH method is applied to study the interfacial behavior of the explo- sion welding of Mg/Al plates. Vd High explosive Zhang and Wang [30] and Yan et al. [2] have success- Air flow fully obtained Mg/Al alloy plates with good bonding by explosive welding. However, only the microstructure and Flyer plate mechanical characteristics of Mg/Al alloys composite plate were investigated by experiments. Few studied the Base plate explosive welding process of Mg/Al alloys plate by simu- lation and researched its interfacial deformation behavior. Therefore, in this paper, the main aims are to numerically Vp β simulate the impact process of Mg/Al alloys plates; to S research the distribution of physical parameters such as Vcp contact pressure, velocity effective plastic strain, and shear Figure 1: Schematic drawing
Details
-
File Typepdf
-
Upload Time-
-
Content LanguagesEnglish
-
Upload UserAnonymous/Not logged-in
-
File Pages10 Page
-
File Size-