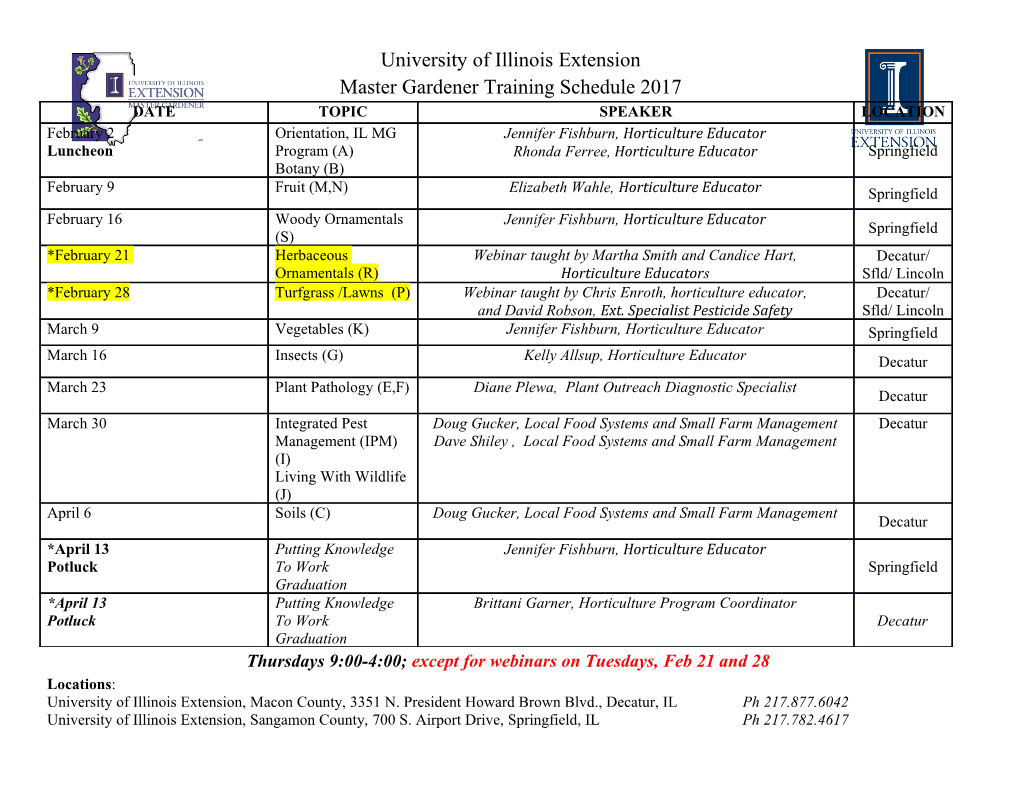
Title Page Dynamics of Spinning Triangle Geometry and Its Effects on Yarn Quality by Noman Haleem (M.Sc. Engineering) Submitted in fulfilment of the requirements for the degree of Doctor of Philosophy Deakin University June, 2017 Acknowledgements I owe gratitude to a number of people for their help and support in completion of my PhD thesis . Professor Xungai Wang for providing me an opportunity to study at Deakin University. I am also thankful for his advice and continuous support during my PhD candidature . Dr. Christopher Hurren for critical but constructive feedback on my experimental work and thesis draft. I am also thankful for his inspiration and advice for 3MT thesis competition . Dr. Xin Liu for training and support in testing of yarn specimens, friendly advice on experiments and constructive feedback on thesis revisions . Dr. Stuart Gordon (CSIRO Manufacturing, Geelong) for his tremendous support and facilitation in resin casting, micro CT and yarn spinning experiments. I would specially thank Stuart for accompanying me in several visits to external facilities for experiments and meetings . Professor Saeed Najar (Amirkabir University, Iran) for friendly discussions and critical input on the spinning triangle analysis and micro CT of yarns during his one year sabbatical visit to Deakin University . Mark Freijah and Phil Henry (CSIRO Manufacturing, Geelong) for their friendly support and facilitation in yarn spinning experiments . Alex Orokity for his tremendous support in mechanical workshop, training and facilitation in designing the clear rubber rollers . Graeme Keating for technical support in textile and yarn spinning laboratory iii . Scott Barnes (CSIRO Manufacturing, Geelong) for allowing to use high speed camera . Ladies in the CSIRO testing Lab for their help in yarn testing . Robynne Hall and Damien Elderfield (School of Engineering) for development of sample holders for micro computerized tomography . Neale Gibbsons for installing and maintaining compact spinning system on ring spinning frame to allow compact spinning experiments . Dr. Sherry Mayo (CSIRO Clayton, Melbourne) for her useful advice on yarn micro CT scanning experiments . Dr. Andrew Stevenson (Australian Synchrotron, Melbourne) for his useful advice and support in micro CT scanning experiments . Dr. Levi Beeching (Australian National University, Canberra) for CT scanning of yarn specimens using helical CT technique . Dr. Asadul Haque (Monash University, Melbourne) for helping to optimize the micro CT scanning parameters on regular micro CT scanning system . Dr. Matthew Foley (The University of Sydney, Sydney) for his advice and conducting multiple trials of yarn micro CT experiments on their CT system . Januar Gotama, Mel Dell'Olio and Tri Nguyen (CSIRO Highett) for their help in optimizing the resin processing recipe . Christine Rimmer and Helen Woodall for support on administrative and HDR matters iv . Sandy Benness and John Robin for support on IT matters I wish to acknowledge support from the Australian Research Council (ARC) and Shandong Ruyi Group through an ARC Linkage project (LP120200536). This work was also supported by the Multi-modal Australian ScienceS Imaging and Visualisation Environment (MASSIVE) (www.massive.org.au). Finally, I am wish to express gratitude to my family for their continued support, patience and encouragement during the years of my PhD. v List of Figures Figure 2.1: Yarns produced from a) staple fibres and b) continuous filaments ................ 8 Figure 2.2: (a) Working principle and various components of ring spinning system (b) formation of spinning triangle between front delivery roller and twisting point[11] ....................................................................................................... 11 Figure 2.3: Illustration of various yarn irregularities a) neps b) thick and thin places c) slubs [21] ...................................................................................................... 15 Figure 2.4: Pictorial comparison of hairy yarn versus non-hairy yarn[29] ..................... 17 Figure 2.5: Poor control on fibres lying at the extreme ends of the spinning triangle [26] ...................................................................................................................... 18 Figure 2.6: Path length difference of the fibres lying at the edge (Fe) and centre (Fc) of the spinning triangle ........................................................................................... 21 Figure 2.7: Patterns of stress distribution in spinning triangle zone with left offset (d = - 1.244), right offset (d = 1.244) and no offset (d = 0) configurations [51] ... 22 Figure 2.8: Geometrical model of spinning triangle (a) with a raised part [62] (b) concentric fibre circles at front roller nip [59] ............................................. 26 Figure 2.9: An image of spinning triangle taken using micro CCD camera [26] ........... 28 Figure 2.10: Some of the spinning triangle images captured through transparent roller arrangement [63] .......................................................................................... 29 Figure 2.11: The idealized helical model of yarn structure [71] ..................................... 30 Figure 2.12: Trajectory of tracer fibre within a yarn[74] ................................................ 32 Figure 2.13: Yarn cross sectional images (a) cotton yarns of various fibre fineness (b) viscose filament yarn (c) plied nylon filament yarn [85] ........................... 35 Figure 2.14: Cross sectional view of compact spun yarns produced on different compact spinning systems [88] ................................................................................ 36 Figure 2.15: Fibre trajectories in modified ring spinning system a) deformed axis b) loops c) local reversion [100] .............................................................................. 38 Figure 2.16: Working principle of micro computerized tomography system ................. 39 Figure 2.17: Volumetric model of cotton yarn produced by micro CT method (a) longitudinal and (b) cross sectional views [110] .......................................... 40 vi Figure 2.18: Various compact spinning systems (a) Rieter K46 perforated bottom cylinder [75] (b) Zinser perforated aprons [76] (c) Sussen compact spinning system [24] (d) Rocos compact spinning system [113] ........................................... 43 Figure 2.19: The arrangement of complete condensing spinning system [126] ............. 47 Figure 2.20: An overview of different components of Siro spinning system[135] ........ 49 Figure 2.21: Solo spinning attachment shows a specially designed grooved roller with mounting aids [146] ..................................................................................... 51 Figure 2.22: Left offset diagonal spinning by connecting fibrous strand to adjacent spindle[150]..................................................................................................... 53 Figure 2.23: Schematic diagram of different groove configurations to direct fibre flow[157] ...................................................................................................... 57 Figure 2.24: Pictorial illustration of spinning without (a) and with (b) contact surface[162] ...................................................................................................................... 58 Figure 2.25: False twister installed in yarn path of a conventional ring spinning system[165] .................................................................................................. 60 Figure 2.26: An air nozzle applied in yarn path of conventional ring spinning process[176] ...................................................................................................................... 62 Figure 2.27: Three roving feeding arrangement using a composite roving guide at classical ring spinning frame [191] .............................................................. 65 Figure 2.28: cross sectional comparison between cluster spun yarns (left) and core spun yarns (right) [192] ........................................................................................ 67 Figure 2.29: Illustration of twist insertion mechanism by magnetic levitated ring [201] ...................................................................................................................... 68 Figure 3.1: Images of the spinning triangle as taken from direct observation technique [26] ............................................................................................................... 78 Figure 3.2: Images of the spinning triangle taken through clear plastic roller a) appropriate image b) fibre slippage due to plastic roller ................................................. 79 Figure 3.3: A concept of clear rubber top roller for observing the spinning triangle during yarn spinning ................................................................................................ 81 Figure 3.4: Concentric arrangement of plastic tube and mould to cure polyurethane rubber layer .............................................................................................................. 84 Figure 3.5: Effect of resin components and mixture degassing on transparency of the rubber cot...................................................................................................... 85 Figure 3.6: Different components of clear rubber roller ................................................. 86 vii Figure
Details
-
File Typepdf
-
Upload Time-
-
Content LanguagesEnglish
-
Upload UserAnonymous/Not logged-in
-
File Pages246 Page
-
File Size-