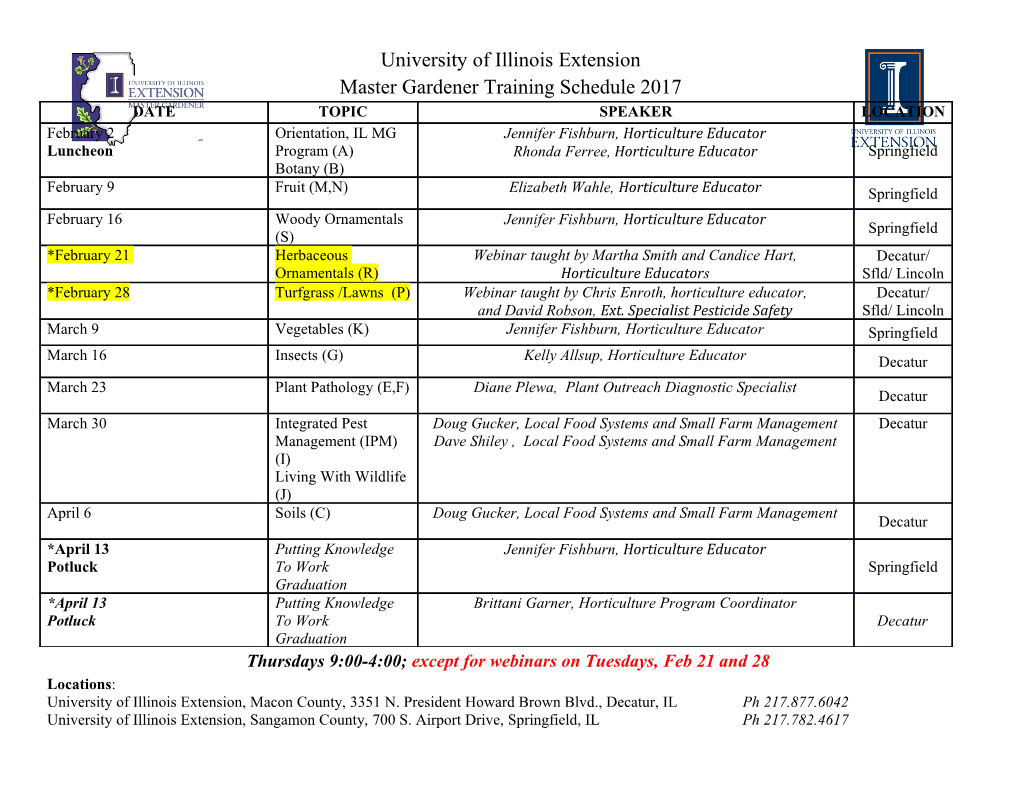
CHAPTER 2. DIRECT TORQUE CONTROL. PRINCIPLES and GENERALITIES. 2.1 - Induction motor controllers. 2.1.1 – Voltage/frequency. There are many different ways to drive an induction motor. The main differences between them are the motor’s performance and the viability and cost in its real implementation. Despite the fact that "Voltage/frequency" (V/f) is the simplest controller, it is the most widespread, being in the majority of the industrial applications. It is known as a scalar control and acts imposing a constant relation between voltage and frequency. The structure is very simple and it is normally used without speed feedback. However, this controller doesn't achieve a good accuracy in both speed and torque 2.1 Direct Torque Control. Principles and Generalities. responses mainly due to the fact that the stator flux and the torque are not directly controlled. Even though, as long as the parameters are identified, the accuracy in the speed can be 2% (except in a very low speed) and the dynamic response can be approximately around 50ms [LEO 1][LUD 2]. 2.1.2 – Vector controls. In these types of controllers, there are control loops for controlling both the torque and the flux [BOS 1]. The most widespread controllers are the ones that use vector transform such as either Park or Ku. Its accuracy can reach values such as 0.5% regarding the speed and 2% regarding the torque, even in stand still. The main disadvantages are the huge computational capability required and the compulsory good identification of the motor parameters [ROM 1]. 2.1.3 – Field Acceleration method. This method is based on avoiding the electromagnetic transients in the stator currents, keeping its phase continuous. Therefore, the equations used can be simplified saving the vector transformation in the controllers. It is achieved some computational reduction, overcoming the main problem in the vector controllers and then becoming an important alternative for the vector controllers [BED 5] [ROM 1] [YAM 1]. 2.1.4 - Direct Torque Control. In Direct Torque Control it is possible to control directly the stator flux and the torque by selecting the appropriate inverter state. Its main features are as follows [LUD 1] [VAS 2]: § Direct torque control and direct stator flux control. § Indirect control of stator currents and voltages. § Approximately sinusoidal stator fluxes and stator currents. § High dynamic performance even at locked rotor. 2.2 Direct Torque Control. Principles and Generalities. This method presents the following advantages: § Absence of co-ordinate transform. § Absence of voltage modulator block, as well as other controllers such as PID for flux and torque. § Minimal torque response time, even better than the vector controllers. Although, some disadvantages are present: § Possible problems during starting. § Requirement of torque and flux estimators, implying the consequent parameters identification. § Inherent torque and flux ripples. 2.3 Direct Torque Control. Principles and Generalities. 2.2 - Principles of Direct Torque Control. 2.2.1 - Introduction. As it has been introduced in expression 1.81, the electromagnetic torque in the three- phase induction machines can be expressed as follows [BOL 1][VAS 2]: 3 (2.1) t e = 2 Pys ´ is Where ys is the stator flux, i s is the stator current (both fixed to the stationary reference frame fixed to the stator) and P the number of pairs of poles. The previous equation can be modified and expressed as follows: 3 (2.2) t e = 2 P ys × is × sin (a s - rs ) Where rs is the stator flux angle and a s is the stator current one, both referred to the horizontal axis of the stationary frame fixed to the stator. If the stator flux modulus is kept constant and the angle rs is changed quickly, then the electromagnetic torque is directly controlled. The same conclusion can be obtained using another expression for the electromagnetic torque. From equation 1.83, next equation can be written: 3 Lm ' te = P y r ´ y s × sin(rs - rr ) 2 L L L2 s r - m (2.3) Because of the rotor time constant is larger than the stator one, the rotor flux changes slowly compared to the stator flux; in fact, the rotor flux can be assumed constant. (The fact that the rotor flux can be assumed constant is true as long as the response time of the control is much faster than the rotor time constant). As long as the stator flux modulus is kept constant, then the electromagnetic torque can be rapidly changed and controlled by means of changing the angle rs - rr [TAK 2] [VAS 2]. 2.2.2 - DTC Controller. The way to impose the required stator flux is by means of choosing the most suitable Voltage Source Inverter state. If the ohmic drops are neglected for simplicity, then 2.4 Direct Torque Control. Principles and Generalities. the stator voltage impresses directly the stator flux in accordance with the following equation: dy s = us dt (2.4) Or: Dy s = usDt (2.5) Decoupled control of the stator flux modulus and torque is achieved by acting on the radial and tangential components respectively of the stator flux-linkage space vector in its locus. These two components are directly proportional (Rs=0) to the components of the same voltage space vector in the same directions. Figure 2.1 shows the possible dynamic locus of the stator flux, and its different variation depending on the VSI states chosen. The possible global locus is divided into six different sectors signalled by the discontinuous line. v3(010) v2(110) 2 3 v3(FD,TI) v2 (FI,TI) v6(FI,TD) v4(011) v5(FD,TD) v1(100) 4 1 5 6 v5(001) v6(101) Figure 2.1. Stator flux vector locus and different possible switching voltage vectors. FD: flux decrease. FI: flux increase. TD: torque decrease. TI: torque increase. In Accordance with figure 2.1, the general table II.I can be written. It can be seen from table II.I, that the states Vk and Vk+3 , are not considered in the torque because they can both increase (first 30 degrees) or decrease (second 30 degrees) the torque at the same sector depending on the stator flux position. The usage of these states for 2.5 Direct Torque Control. Principles and Generalities. controlling the torque is considered one of the aims to develop in the present thesis, dividing the total locus into twelve sectors instead of just six [LUD 1]. VOLTAGE VECTOR INCREASE DECREASE Stator Flux Vk,V k+1,V k-1 Vk+2 ,V k-2,Vk+3 Torque Vk+1 ,V k+2 Vk-1,V k-2 Table II.I: General Selection Table for Direct Torque Control, being "k" the sector number. Finally, the DTC classical look up table is as follows: F t S1 S2 S3 S4 S5 S6 TI V2 V3 V4 V5 V6 V1 FI T= V0 V7 V0 V7 V0 V7 TD V6 V1 V2 V3 V4 V5 TI V3 V4 V5 V6 V1 V2 FD T= V7 V0 V7 V0 V7 V0 TD V5 V6 V1 V2 V3 V4 Table II.II. Look up table for Direct Torque Control. FD/FI: flux decrease/increase. TD/=/I: torque decrease/equal/increase. Sx: stator flux sector. F: stator flux modulus error after the hysteresis block. t: torque error after the hysteresis block. The sectors of the stator flux space vector are denoted from S1 to S6. Stator flux modulus error after the hysteresis block (F ) can take just two values. Torque error after the hysteresis block (t) can take three different values. The zero voltage vectors V0 and V7 are selected when the torque error is within the given hysteresis limits, and must remain unchanged. 2.6 Direct Torque Control. Principles and Generalities. 2.2.3 - DTC Schematic. In figure 2.2 a possible schematic of Direct Torque Control is shown. As it can be seen, there are two different loops corresponding to the magnitudes of the stator flux and torque. The reference values for the flux stator modulus and the torque are compared with the actual values, and the resulting error values are fed into the two- level and three-level hysteresis blocks respectively. The outputs of the stator flux error and torque error hysteresis blocks, together with the position of the stator flux are used as inputs of the look up table (see table II.II). The position of the stator flux is divided into six different sectors. In accordance with the figure 2.2, the stator flux modulus and torque errors tend to be restricted within its respective hysteresis bands. It can be proved that the flux hysteresis band affects basically to the stator-current distortion in terms of low order harmonics and the torque hysteresis band affects the switching frequency [VAS 2]. The DTC requires the flux and torque estimations, which can be performed as it is proposed in figure 2.2 schematic, by means of two different phase currents and the state of the inverter. Flux ref + - Torque ref + Selection VSI induction - Table motor flux sector VSI state stator flux torque estimators Figure 2.2. Direct Torque Control schematic. However, flux and torque estimations can be performed using other magnitudes such as two stator currents and the mechanical speed, or two stator currents again and the shaft position [LUD 1] [TAK 2]. 2.7 Direct Torque Control. Principles and Generalities. 2.2.3.1 - Stator flux and torque estimator using wm, isA and isB magnitudes. This estimator does not require co-ordinate transform. It is used the motor model fixed to the stationary reference frame fixed to the stator.
Details
-
File Typepdf
-
Upload Time-
-
Content LanguagesEnglish
-
Upload UserAnonymous/Not logged-in
-
File Pages25 Page
-
File Size-