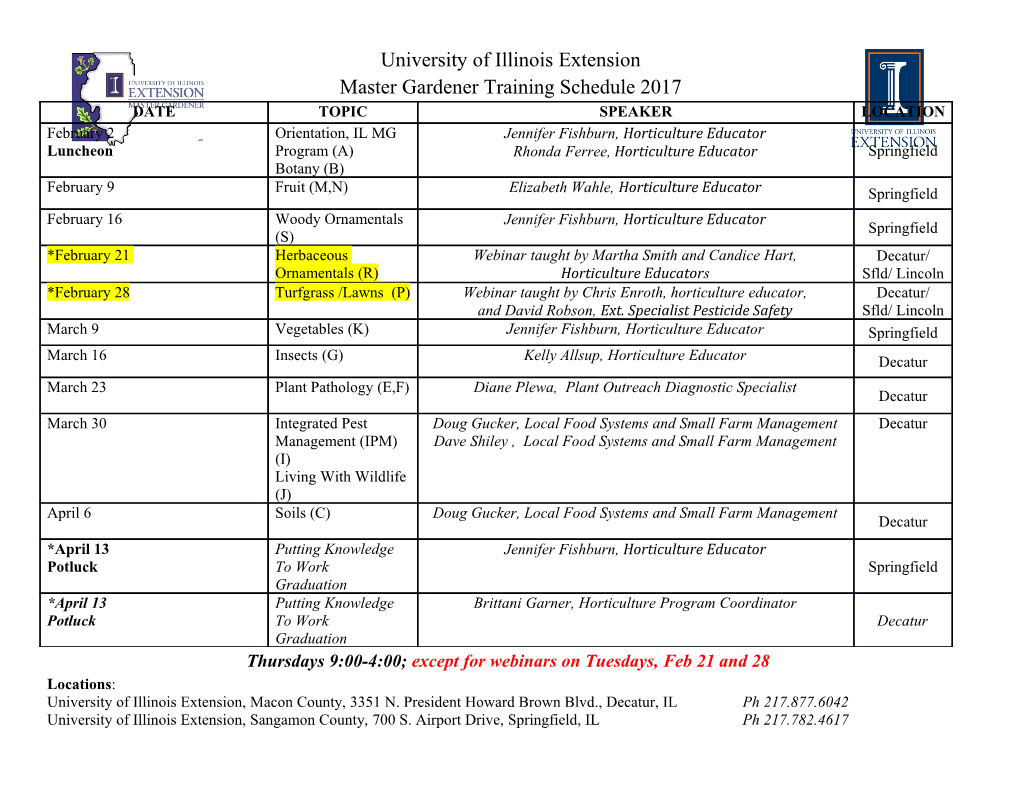
3,234, 66 United States Patent Office Patented Feb. 8, 1966 2 The following example serves to illustrate the values 3,234,166 obtained when the present invention is not followed, all BENZENE-S8:UBLE AND BENZENENSOLUBLE parts being by weight unless otherwise identified. CiS-14 POLYISOPRENE Kenneth (C. iiecker, Aron, Ohio, assignor to The Good Example l-Control year Tire & Ruber Company, Aron, Ohio, a corpora A latex is made by first making a gel-free 96% cis-1,4 ties of binic polyisoprene cement in benzene containing 10% solids Ng Drawing. Fied Ar. 4, 1962, Ser. No. 84,953 and then adding to the cement 5.5 parts of potassium Claira. (C. 260-29.7) oleate, 0.2 parts of the tetra sodium salt of ethylene di amine tetra acetic acid (Versene), the amount of each This invention relates to an improved latex of a solu O material being based on 100 parts of rubber. This mix tion-polymerized diene rubber, a process for its manu ture is then vigorously stirred into 1000 parts of distilled facture and uses thereof. Water to bring about the complete emulsification of the A gum rabber film laid down from a man-made rubber rubber cement in the water. latex and particularly from a latex made from a benzene The benzene is stripped from the emulsion using a soluble polydiene and particularly polyisoprene contain laboratory size disc evaporator which operates by revolv ing at least 50% of cis-1,4 polyisoprene is deficient in ing metal discs through the emulsion, exposing new sur certain physical properties and particularly with respect faces to the atmosphere and thus evaporating the benzene. to the moduli at elongations ranging from 50% to 100%. The resulting latex has a solids content of about 32% and Many attempts have been made to improve the moduli is concentrated by centrifuging through a laboratory size by conventional methods well-known to the latex chemist, De Lavall centrifuge machine to 62.7% total solids. This but the results obtained are not desirable for many latex, which is a low viscosity, low surface tension liquid eaSOS. and completely free of gel, is compounded as follows: It has now been discovered that an improved latex Parts of a solution-polymerized diene rubber may be made in a Ingredients: (dry weight) facile, efficient, and economical manner by providing a (1) Sulfur ---------------------------- 2.0 benzene-soluble solution-polymerized diene rubber with (2) Zinc mercaptobenzothiazole ---------- 3.0 a desirable content of a benzene-insoluble, highly cross (3) Zinc diethyldithiocarbamate ---------- 1.0 linked, solution-polymerized diene rubber, generally (4) Antioxidant (mixture of styrenated referred to as “gel,” and then converting this mixture to a 30 latex in a conventional manner. phenols) ------------------------ 1.0 In the accepted commercial practice of manufacturing (5) Diphenyl guanidine ----------------- 0.6 artificial latex dispersions of rubber, the procedure con (6) Zinc oxide ------------------------- 3.0 sists primarily in milling the rubber for a period of time (7) Latex (62.7% solids) ---------------- 100.0 and at a certain temperature to break down any gel con 3 5 Items 1 to 6 were added to the latex as water disper tent present and then dissolving the milled rubber in any sions or emulsions, following the normal way of com suitable solvent, such as benzene, to form a benzene ce pounding liquid rubber latex systems. This mass was ment or solution of the rubber. The cement is then then cooled to 55 F. and 1.0 part sodium silicofluoride emulsified with water with the aid of surfactants to form as a 20% water dispersion was added with slow stirring the desired dispersion of small particles of rubber con 40 into the latex, care being taken not to generate air bubbles taining solvent in a continuous phase of water. The sol in the mixture. The completed compounded latex was vent is then stripped from the globules of emulsified rub poured onto a glass surface and scraped to a uniform ber by a controlled heating operation or by evaporation thickness. Within three minutes, the liquid latex mass at room temperature (70 F.), followed by concentrating coagulated into a uniform film, which, after drying, was the dispersion of rubber particles to a desired total solids, 020 inch in thickness. This film was then cut into sec which usually is in the order of about 60%. tions and cured in a circulating hot air oven for periods In the manufacture of a solution-polymerized diene of time shown in Table I below. Stress/strain values rubber, for example, polyisoprene rubber, having a pre were determined on conventional dumbbell specimens of ponderance of 14 linkages of either the cis- or trans .125 inch wide at the center test area. A standard in variety, the rubber is formed in a solvent polymerization stron machine, operating at 5 inches/minute was used to system and the conditions of catalysis are adjusted so 50 obtain moduli and ultimate tensile and elongation prop that a clear cement of, for example, cis-1,4 polyisoprene erties. Table I contains the data on this experiment, which rubber is produced. It is not obvious to one skilled in we refer to as the control. this art how the moduli of a film laid down from such a TABLE I latex can be improved. It has been discovered, as may be appreciated from the Moduli (p.s.i.) Ultimate Ultimate At 22°F. Wuganization - - Teasile Elongation disclosure of the present invention, that when a certain Time in Minutes (p.S.i.) (percent) percentage of gelled rubber of the type referred to above 50% 100% is associated with the benzene-soluble rubber as, for ex ample, by being mixed with a cement of the benzene 2 70 95 5,200 940 5 8 120 5,330 880 soluble or ungelled rubber and these rubber phases, in 85 25 6,000 854) timately mixed with each other in the cement and then 9) 30 6,000 830 converted to a latex with water in the presence of an 90 30 5,000 830 emulsifying agent, rubber films produced therefrom are greatly improved in certain properties over the control. 65 The following examples serve to illustrate the values The control rubber is the rubber film made from the latex obtained when a rubber latex is made in accordance of the benzene-soluble rubber. with the present invention: The gelled rubber phase may also be intimately asso ciated with the ungelled rubber phase by forming the Example 2-21% gel rubber later gelled rubber phase in situ during the formation of the A second latex was made in substantially the same ungelled phase during solution polymerization of the 70 way as described in Example 1, except that during the monomers selected to form the diene rubber desired. solution polymerization of isoprene the 96% cis-1,4 3,234,166 3. A. polyisoprene polymer contained 21% by weight of ben The following example shows a method for the produc zene-insoluble, tough, high molecular weight cis-1,4 tion of a cis-1,4 polyisoprene cement containing a high polyisoprene, which is also referred to as polyisoprene percentage of gel, all parts being by weight unless other gel and 79% benzene-soluble cis-1,4 polyisoprene. The wise indicated. latex was made and compounded and the films tested as 5 Example 4 in Example 1. The Table II contains the data on this experiment. The catalyst system used to bring about the polym TABLE II erization of isoprene is made by reacting 1.0 milliliter of 0.323 molar titanium tetrachloride and 1.0 milliliter of Moduli (p.s.i.) Ultimate Ultimate At 22°F Wucanization Tensie Elongation O 0.323 molar triisobutyl aluminum in heptane. This Time in Minutes (p.S.i.) (percent) catalyst is then added to 20 milliliters of isoprene con 50% 100% fined in a glass-lined reactor provided with a stirrer and a cooling means and allowed to react to completion. At 70 95 4,450 900 82 20 5,300 820 the end of the reaction time, a 52% yield of polymer is 90 3) 5,600 780 obtained, of which 28% of the polymer is a gel dispersed 95 35 6,000 780 in the solvent. 98. 35 6,000 780 The polymerization of isoprene may be caried out in the presence of polymerization systems which promote Example 3-28% gel rubber latex the production of a gel content in the finished polymer A third latex was made in substantially the same main 20 ranging from about 20% to about 65%, using tempera ner as described in Example 2, except that during the tures ranging from about 25 C. to about 100° C. at nor solution polymerization of isopreine the 96% cis-1,4 poly mal ambient pressures. The amount of catalyst em isoprene contained 28% of benzene-insoluble gel and ployed may range from about .5 milliliter to about 5 mil 72% of benzene-soluble cis-1,4 polyisoprene. Vulcanized liliters per mol of isoprene. A gel content as high as films were made and tested in the same manner as about 100% may be obtained if a blanket of nitrogen is described above. Table EI contains the data of this series not provied over the reaction mixture. of Samples. The polymerization of the isoprene may be carried TABLE I out in any suitable solvent for the resulting polymer, in cluding hexane, heptane, octane, isooctane, nonane, Moduli (p.S.i.) Ultimate Ultimate 30 decane, benzene, naphtha, toluene, mineral spirits, cyclo At 22° E Wulcanization Tehsile Elongation Time in Minutes.
Details
-
File Typepdf
-
Upload Time-
-
Content LanguagesEnglish
-
Upload UserAnonymous/Not logged-in
-
File Pages3 Page
-
File Size-