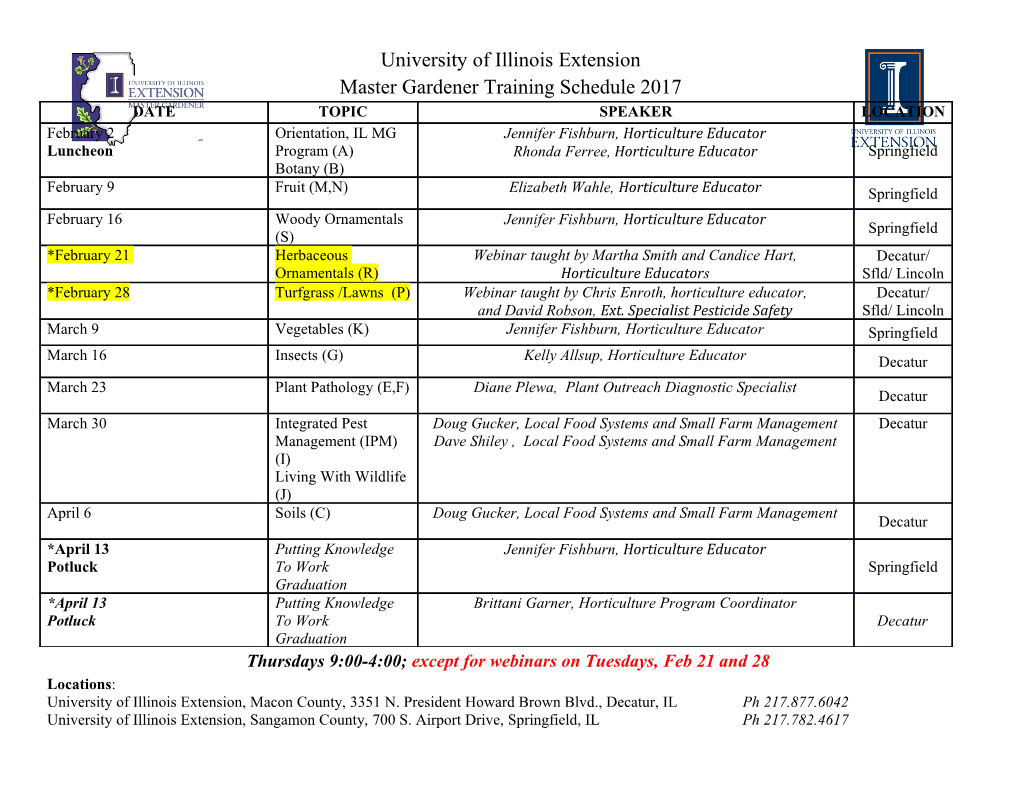
RESEARCH ARTICLE Damping Package Design Using Structural Corrugated Board PREFACE API 2015 Qi Zhang Katsuhiko Saito Kobe University Kobe University [email protected] [email protected] Katsushige Nagaoka TSK Coporation [email protected] ABSTRACT Packaging is designed to protect products from shock and vibration during transport. In recent years, paper cushioning materials, such as corrugated board and pulp molded packaging, are being increasingly used because they are environmentally friendly and easy to recycle. However, because no efficient packaging-design method yet exists for paper cushioning material, packaging engineers must rely on previous experience and the so-called trial-and-error method to design packaging. One reason for this situation is that, for most cases, the paper cushioning material used for protective packaging has a complicated structure and deforms after being subjected to repetitive shock and vibration. To address this shortcoming, we propose a damping design method for corrugated-board packaging that includes shock-absorbing and vibration damping elements. To verify that the resultant packaging functions as intended, we test three types of packaging in the following way: First, we use an existing design method to create cushioned packages and examine them via free-fall drop tests. Next, to test the robustness of packaging against vibration (i.e., for packaging destined for various modes of transport), we study the three packaging types by subjecting them to (i) vibration-only tests and (ii) drop-plus-vibration tests. For vibration-only tests, the packaging with highest static stress gives the best result, its “vibration fatigue” accounts for approximately 52% of the worst result given by packaging with the lowest static stress. In the drop-plus-vibration tests, the best packaging is that with the lowest static stress; its “vibration fatigue” is approximately 31% of the worst packaging, which has an intermediate value of static stress. This approach allows us to determine the packaging with the best shock-absorbing and vibration damping characteristics. Damping package design using structural corrugated board 19 KEY WORDS paper cushioning material, structural corrugated board, cushioning package design, vibration test INTRODUCTION However, for paper cushioning material, no studies yet exist for efficient and accurate methods Expanded plastic cushioning material and to design shock-absorbing and vibration damping paper cushioning material are two main cushion- packaging, so packaging engineers must still rely ing materials used for protective packaging. For on previous experience and the so-called trial-and- expanded plastic, methods to design shock-absorb- error method to design packaging. In recent years, ing and vibration damping packaging are widely paper cushioning material, such as corrugated applied because the cushion curves and methods to board and molded pulp, have seen increasing use analyze the frequency response function (FRF) are because they are environmentally friendly and easy highly developed. For example, Ge et al.1 compared to recycle. Meanwhile, expanded plastic cushion- the cushion curves of flat foam and corner foam ing material is being increasingly replaced by paper (with shear force) and recommended that the con- cushioning material because of increasing stringent ventional cushion curve should be shifted toward environmental regulations and to improve the man- higher static loading for corner foam by approx- ufacturer’s image. Thus, a strong demand exists for imately 23%–35%. Kitazawa et al.2 investigated a method to design cushioned packaging that uses how various combinations of peak acceleration paper cushioning material. and velocity affect the repetitive-shock-induced To address this need, the present study proposes damage to products because of cumulative fatigue. a method to design damping packaging that uses Wang et al.3 address vibration damping packag- corrugated board in shock-absorbing and vibra- ing design in a study about a double-substructure tion damping package. To verify that the packaging multi-coordinate coupled system and measure the works as intended, we test three types of packaging system-level FRFs to predict the substructure- in three ways: First, we use an existing method to level FRFs. The trend of the latter was found to be design the package6 and test shock-absorbing perfor- consistent with that of the directly measured sub- mance by using free-fall drop tests. Next, we focus on structure-level FRFs. Lamb et al.4 discuss how to vibration damping packaging design (i.e., for pack- separate the linear component of a system’s FRF aging destined for transport) and apply (i) vibration- by using a reverse multiple-input–single-output only tests and (ii) drop-plus-vibration tests. Analyz- (RMISO) algorithm. The RMISO-based technique ing and comparing the “vibration fatigue” reveals estimates the linear component of the FRF, which the optimum packaging for each use. allows traditional modal-parameter-extraction techniques to be used to analyze nonlinear cush- DESIGN OF CUSHIONED PACKAGING ioning systems. Finally, Zhang et al.5 proposed a damping design that combines both shock-absorb- ing and vibration damping packaging and used a Cushioning characteristics of structural multibody dynamics simulation to analyze the corrugated board subjected to shear force vibration response of the packaging. Journal of Applied Packaging Research 20 Material Shear Force For these tests, we used single-wall A-flute cor- When using corrugated-board cushioned pack- rugated board. Both surface liner and reverse liner aging, the space between the product and the outer were 210 g/m2 with over 263 N ring crush com- box is supported by a structural pad made of corru- pressive strength; the medium paper was 120 g/m2 gated board. For actual packaging with corrugated with over 96 N ring crush compressive strength. board, the cushioning pad is made from a corru- All materials used in these tests were exposed to gated board to keep the pad stable and facilitate a temperature of 23 °C and a relative humidity of the fabrication process. Some amount of space is 50% for over 24 h. The corrugated board lies in the left (see lower-left corner in Fig. 2) that generates a plane defined by the machine direction and trans- shear force when shock occurs. verse direction (see Fig. 1), which are the two direc- tions most often solicited to support products. The Test specimen transverse direction is often solicited in cushioned The test specimens of corrugated-board packaging because it has much higher compressive padding are designed as shown in Fig. 3 and Fig. strength than the machine direction and so is able to 4. The upper and lower flaps generate shear if the absorb more shock energy. package is dropped, which leads to more realis- tic data from the tests. The length of corrugated board that absorbs the shock energy in the drop test is 100 mm × 2 = 200 mm and the upper and lower flaps are separated by 40 mm (see Fig. 4). Test equipment Fig. 4 shows a schematic diagram of the dynamic compression test apparatus used to analyze the response of the cushioning material. The test apparatus uses an adjustable weight on Fig. 1: Coordinate system for corrugated board top of which is mounted an acceleration sensor. When the weight drops onto the test specimen, the acceleration sensor records the acceleration as a function of time at a sampling rate of 0.05 ms filtered by a 300 Hz low-pass filter. In addition, a displacement sensor records the displacement of the top edge of the test specimen as a function of time during compression (see Fig. 4). The weight is dropped from a height of 60 cm above the top surface of the packaging. Fig. 2: Example of cushioning pad and direction of shear force Damping package design using structural corrugated board 21 Fig. 3: Structure of test specimen Fig. 4: Test specimen (left) and apparatus for dynamic compression test (right) Dynamic Compression Tests Fig. 5 also shows some photographs of test Conduct dynamic compression tests using specimens after the tests. Specimen I(1.13 N/cm) the specimen and equipment in Fig.4, the weight is too stiff to absorb significant shock energy, is drop on the specimen from 60cm and peak whereas specimen II(2.11 N/cm), which has a lower acceleration value is obtained by the accelera- peak acceleration, is more suitable for cushioning. tion sensor mounted at the top of the weight. In Specimen III has a static load of 3.58 N/cm, which order to obtain peak acceleration values gener- is over the dead line, so the test specimen “bottoms ated by different weights, we change the weight out” (i.e., the upper flap collides with the lower flap). after every 5 tests (for an average value) and each The results in Fig. 5 show that the lowest test uses a new specimen. Fig. 5 shows the cush- peak acceleration occurs for a static load per ioning-property graph obtained from the data for unit perimeter of 2.84 N/cm, so this is the ideal dynamic compression. The horizontal axis gives value for this parameter and for design of cush- the static load per unit perimeter. When design- ioned packaging. In contrast, the peak accelera- ing cushioned packaging from expanded plastic tion increases for a static load per unit perimeter material, the cushion curve is commonly used. greater than 2.84 N/cm because the corrugated The horizontal axis of the cushion curve gives the test specimen cannot absorb the shock; therefore, static stress (i.e., weight divided by bearing area). the weight contacts the metal block below the However, for corrugated board, the bearing area packaging (e.g., specimen III). Thus, a static load is hard to determine owing to the thinness of the per unit perimeter greater than 2.84 N/cm is not board and the shear force generated by the flaps.
Details
-
File Typepdf
-
Upload Time-
-
Content LanguagesEnglish
-
Upload UserAnonymous/Not logged-in
-
File Pages15 Page
-
File Size-