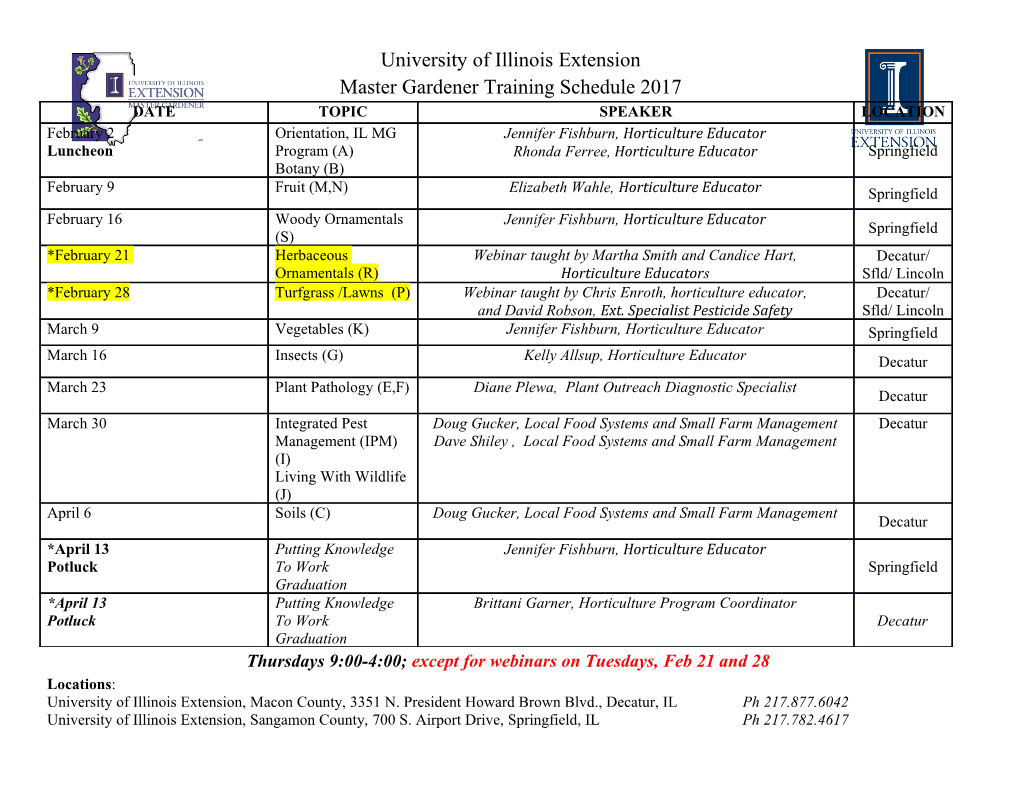
Metallographic preparation of Cast iron Application Notes Iron is one of the most diverse met- als and alloyed with carbon and other elements it offers an enormous variety of cast iron and steel alloys. Cast iron has been produced in China as early as 600BC and in Europe it was first known in the 14th century. With the development of coal fired blast fur- naces the properties of iron improved and a better castability opened new fields of applications for products in every day life. With the industrialisa- tion cast iron became an important construction material as buildings from the 19th century show: the domes of in the automotive and engineering in- train stations, market halls, and green dustry. In addition, specific cast irons houses of botanical gardens, bridges are the material of choice for sea water and the Eiffel Tower still document the pump housings, rolling mill rolls and substantial application of cast iron dur- parts for earth moving equipment. ing that time. As the morphology of graphite has a major influence on the mechanical The term cast iron refers to those iron- properties of cast iron, metallographic carbon-silicon alloys which contain quality control of grey iron is an in- 2.5% - 4% carbon and usually 1-3% tegral part of its production process. Austempered ductile silicon. Cast iron is an important engi- Using standard reference comparison iron, Beraha color etch, neering material with a number of ad- charts and/or image analysis tech- DIC, 500x vantages, mainly good castability and niques, the morphology, size and dis- machinability and moderate mechani- tribution of the graphite is determined cal properties. on an unetched, polished sample. Depending on the specification, the Because of its economical advantages sample is then etched to check the cast iron is used for many applications structure of the matrix. Difficulties during metallographic preparation Cutting: White cast iron is very hard and size can be difficult. The matrix of and therefore difficult to cut. ferritic and/or austenitic cast irons is Grinding and polishing: Graphite is prone to deformation and scratching. soft and retaining it in its true shape Solution - Cubic boron nitride cut-off wheel - Thorough diamond polishing on hard polishing cloths and final oxide polishing. Fig.1: Grey iron with flake graphite, 200x Fig. 2: Same as Fig.1, showing correct polish 200x insufficient polish 28.02.2019 R05 / 62140306 Fig. 6: Exhaust manifold, Production and compacted graphite iron application of cast irons Production Austempered ductile iron (ADI) is a ductile Cast irons are melted in a cupola- or induc- iron austenitized at 840-950°C and then tion furnace charged generally with pig quenched to 250-400°C where it is held un- iron, cast iron scrap, steel scrap and vari- til the matrix is changed to ausferrite. This is ous additions. The alloy composition and a mixture of needle-like ferrite and a carbon the cooling rate will influence whether the saturated retained austenite, which gives the iron will solidify grey or white. ADI iron a high strength and ductility. The A fast cooling rate results in a white solidi- microstructure looks like bainite but has no fication and the formation of iron carbide carbides. (Fe3C or cementite). At the eutectoid trans- High-strength ADI irons are mainly used formation a fast cooling rate promotes the Fig. 4: Grey iron with flake graphite in 200x for wear resistant parts for heavy trucks, formation of pearlite, whereas a slow cool- pearlitic matrix farm and earth moving equipment. Applica- ing rate promotes the formation of graphite tions of ductile ADI irons are for parts with and ferrite. evenly dispersed graphite flakes in a pearl- dynamic stress such as axle journals, gear The microstructure of grey cast irons can itic matrix (see Figs. 3 and 4). drives, crankshafts, pull hooks and wheel have either a pearlitic and/or ferritic matrix Grey iron has a high damping capacity, hubs. with free graphite in the shape of flakes, excellent sliding properties and thermal nodules or temper carbon respectively. conductivity, which makes it suitable for For making Compacted graphite iron (CG) Through alloying and heat treatment the machine bases, damping plates for pianos, the same raw material is used as for mak- properties of cast iron can be adjusted for engine blocks, flywheels, piston rings, ing ductile iron. By carefully controlling the certain applications, for instance, alloying brake discs and drums. amount of magnesium added to the melt with molybdenum and nickel improves for nodulizing approx. 80% of graphite is their heat and corrosion resistance. Ductile iron with spheroidal graphite formed as compacted graphite, the rest as In the following the individual cast irons (SG), also called nodular or spheroidal nodules. will be briefly described and their major iron, is made from the same raw material The quality control of compacted iron is fields of application mentioned. as grey iron but requires higher purity. very important as the formation of graphite The melt should be free of Pb, As, Sb, Ti, is critical. A slightly higher percentage of and Al and have very little phosphorus nodules can be tolerated, but the formation and sulphur. By adding trace amounts of of flakes has to be avoided as they would magnesium to the melt before casting, the lower or even eliminate the beneficial prop- graphite forms in a spherical shape instead erties of the compacted iron. of flakes. Compacted graphite iron has better Ductile iron has greater strength and duc- strength, ductility, alternating stress fatigue tility than grey iron of similar composition. strength and higher resistance to oxidation Ductile iron has good machining qualities than grey iron; and it is better to cast, easier and is used for heavy duty gears, pistons, to machine, has better damping qualities rolls for rolling mills, gear cases (Fig.10), Fig. 3: Grey iron with fine flake graphite, 100x unetched valves, tubes and door hinges. Pearlitic ductile iron is the initial material for cam- Grey iron with flake graphite (FG) has and crankshafts which are surface hard- between 2.5-4% carbon, 1-3% silicon and ened for wear resistance (Fig. 8). 0.2-1% manganese. Carbon and silicon promote the formation of graphite flakes and ferrite. Phosphorus in small amounts increases the fluidity of grey iron. It also forms a ternary phosphorus eutectic called “steadit”, which constitutes a web like structure increasing the wear resistance. In the flake form, graphite provides notches within the metallic matrix and consequently lowers the tensile strength, especially when the flakes are very large. In unalloyed grey iron the best mechanical properties can be achieved with fine and Fig. 5: Filter head of ADI cast iron for the Fig.7: Part of a wheel cassette of austempered hydraulic system of a pressure die casting ductile iron machine for plastics Fig. 8: Crankshaft, ductile iron Fig. 9: White cast iron, pearlite with ledeburite 200x Austenitic cast iron, etched with 3% Nital 200x + modified Beraha’s reagent and thermal conductivity and retains the good retention of strength and hardness is easier to cast and therefore suitable for shape better under temperature changes at elevated temperatures. Due to its large precision casting of complicated shaped than ductile iron. masses of carbides, especially when al- parts with a narrow wall thickness. Applications: cylinder heads for high turn- loyed, white cast iron has an excellent The main properties of austenitic cast irons ing diesel motors, axle- and gear cases, resistance against wear and abrasion. It is are: corrosion resistance against sea water exhaust manifolds (Fig. 6), housings of used for shot-blasting nozzles, rolling mill and alkaline media and high strength and turbo chargers. rolls, crushers, pulverizers and ball mill scale resistance at high temperatures. liners. They are used specifically for applications White cast iron contains 1.8-3.6% carbon, in the maritime environment, for instance 0.5-1.9% silicon and 1-2% manganese. By chilling grey or ductile iron on the out- for large pump housings and other parts of A fast cooling rate prevents the precipita- side and letting it cool slowly inside, it is desalination plants, or bushings and linings tion of carbon as graphite. Instead the car- possible to produce parts with a hard sur- in chemical plants, compressors for ag- bon, which is in solution in the melt, forms face of white cast iron with a ductile core gressive gases, housings for gas turbines iron carbide (Fe3C, also called cementite). (chilled cast). and turbo chargers. The structure of white cast iron consists of pearlite and ledeburite (Fig. 9), a eutectic Malleable iron with tempered of pearlite, converted from austenite, and graphite (TG) cementite. Ni-hard alloys (8-9% Cr, 5-6% Malleable iron is made by heat treating Ni) have a martensitic matrix with chro- white cast iron. Through a two stage, long mium carbides. time heat treatment (tempering) white cast iron is converted to ferritic or pearlitic mal- White cast iron has a high compressive leable iron. The carbon of the iron carbide strength and alloyed versions have a first goes into solution, and through slow cooling then precipitates in irregular nod- ules called temper carbon. Pearlitic malle- able iron can be hardened. Increasingly malleable iron is replaced by nodular iron for economical reasons, especially since the fields of application are very similar. Austenitic cast iron Cast irons with at least 20% nickel and 1-5.5% chromium have an austenitic matrix with graphite in form of flakes or nodules. Austenitic cast iron can be an economic alternative to stainless steel as it Ferritic malleable iron 200x Fig.10: Differential housing of ductile iron Difficulties in the preparation of cast iron Alloyed white cast irons are very hard (HV Time constraints often make it difficult to 600) and can be difficult to cut, especially maintain consistent preparation results large sections.
Details
-
File Typepdf
-
Upload Time-
-
Content LanguagesEnglish
-
Upload UserAnonymous/Not logged-in
-
File Pages6 Page
-
File Size-