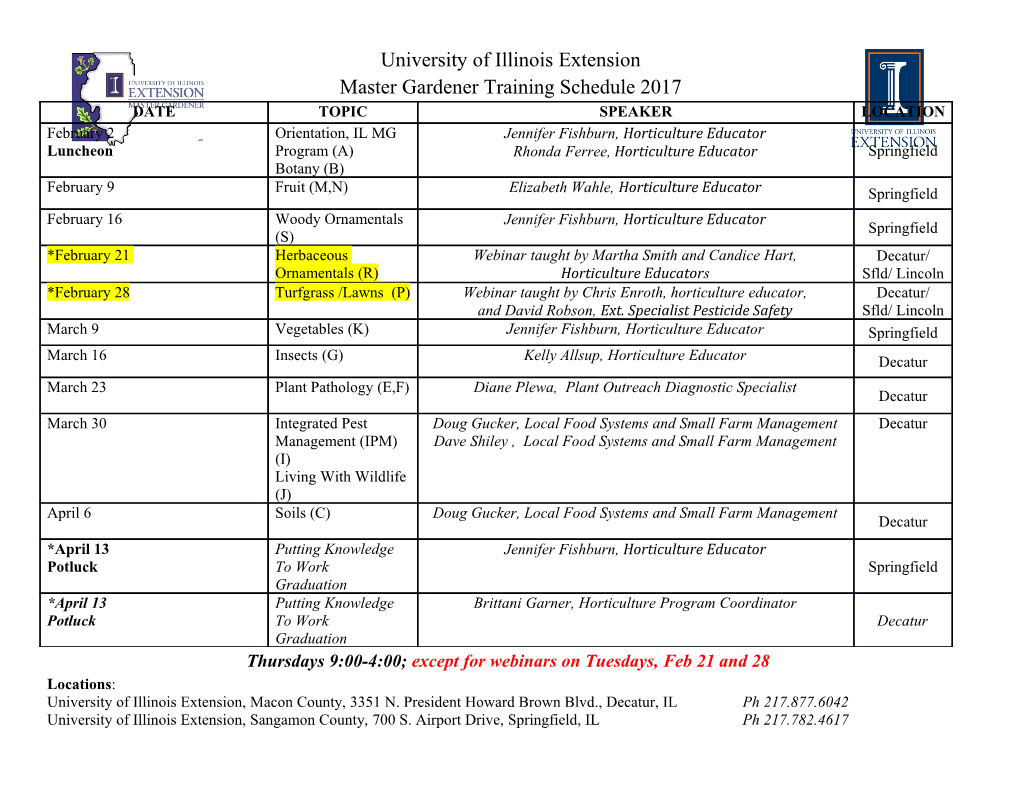
Predictive Equipment Maintenance Oil Analysis Handbook Third Edition Copyright © 2017 Spectro Scientific. All rights reserved. FluidScan® and LaserNet Fines® are registered trademarks of Spectro Scientific Inc. While every effort is made to assure the information in this document ois accurate, Spectro Scientific does not accept liability for any errors or mistakes that may arise. Specifications are subject to change without notice. | 3 Preface Welcome to the third edition of the In-service Oil Analysis Handbook. It has been a few years since the publication of the first edition of Spectro Scientific’s In-Service Oil Analysis Handbook. Our original goal was to compile a comprehensive reference book of common in-service oil analysis techniques to help readers understand and choose the right technique and instrumentation for their needs. We had to limit the scope in the first two editions because of the amount of effort needed to cover all the topics. In-service oil analysis for condition based maintenance covers a wide array of topics. I am pleased to say that in this third edition, we are much closer to our goal. We reorganized the structure of the content for better clarity and we added articles to cover more topics and instruments associated with oil analysis. Also, we rewrote several articles including the latest developments on the market. As we learned more from our customers about their successes using on site oil analysis, we developed case studies that you can find in this edition. This work is not possible without the time and effort from the contributing authors: Patrick Henning, Daniel Walsh, Robert Yurko, Ken Caldwell, Thomas Barraclough, Maria Bartus, Randi Price, John Morgan, Aifeng Shi and Yuegang Zhao from Spectro Scientific and Ray Garvey from Emerson Process Management. Special thanks to Pat Henning, Chief Technology Officer of Spectro Scientific for updating the entire technology section and to Sandra Schiller for managing the project. In-service oil analysis technologies have advanced in the past few years. Innovations in new products have brought on-site oil analysis into the hands of reliability professionals and mechanics. Simple analytical tools enable engineers to make maintenance decisions quicker and with more confidence. We are so pleased to share the recent developments in this field and look forward to more progress down the road. Yuegang Zhao 4 | Oil Analysis Handbook for Predictive Equipment Maintenance Contents Preface ............................................................................3 Section 1: Introduction Chapter 1: In-service Oil Analysis for Condition Based Maintenance .................7 Chapter 2: Oil Sampling Best Practices.............................................14 Section 2: Technologies Chapter 3: Elemental Analysis......................................................23 3.1: Rotating Disc Electrode OES (RDE-OES) .........................................24 3.2: Elemental Analysis: FPQ-XRF for Large Particles...................................31 Chapter 4: Particle Analysis........................................................37 4.1: Dynamic Equilibrium – Large Wear Particles in Oil Lubricated Systems.................37 4.2: Ferrography – Particle Size and Morphology Analysis ..............................39 4.3: Particle Count . .41 4.4: Ferrous Particle Analysis ....................................................43 4.5: LaserNet Fines® – Particle Count, Particle Shape Analysis and Ferrous Particle Analysis ...44 Chapter 5: Infrared Spectroscopy ..................................................52 5.1: Direct Infrared Spectroscopy Based on Grating Optics ..............................53 5.1.1: FluidScan Introduction ..................................................53 5.1.2: TAN-TBN Measurement Using Infrared Technique.............................57 5.1.3: Water Measurement Using the Infrared Technique . 64 5.1.3.1: Dissolved Water Measurement.....................................64 5.1.3.2: Free Water and Total Water Measurement............................66 5.2: Filter Based Infrared Techniques ..............................................70 Chapter 6: Viscosity ...............................................................72 6.1: Laboratory Kinematic Viscometers .............................................72 6.2: Solvent-free Portable Viscometer ..............................................74 Chapter 7: Fuel Dilution in Engine Oil ...............................................79 | 5 Section 3: Oil Analysis Practices and Success Stories Chapter 8: Lubricant Mix Up – How to Catch it with Oil Analysis.....................85 Chapter 9: Route-Based Oil Analysis ...............................................88 Chapter 10: Oil Analysis for Mining Equipment Maintenance ........................92 Chapter 11: Oil Analysis for Servicing On-the-Road Transporation Vehicles..........94 Chapter 12: Oil Analysis for Offshore Drilling Reliability Service .....................96 Chapter 13: Oil Analysis for Municipal Water Treatment Maintenance...............98 Chapter 14: Oil Analysis for Industrial Plant Reliability Management ...............100 Chapter 15: Oil Analysis for Reliability Service .....................................105 Chapter 16: Oil Analysis for Engine Generator Maintenance........................108 Chapter 17: Oil Analysis for Shipboard Maintenance ..............................111 Chapter 1: In-Service Oil Analysis for Condition Based Maintenance | 7 Section 1: Introduction Chapter 1: In-service Oil Analysis for Condition Based Maintenance The practice of in-service oil analysis or used oil analysis and the presence of large ferrous particles. Over the years started over a century ago on locomotive engines. Now different techniques and instruments have been deployed in it is one of the most important components of condition the field or in commercial laboratories but essentially they based maintenance (CBM), a practice of assessing a all provide the information mentioned above. Even though all machine’s condition by periodically gathering data on wear particle analysis techniques can be applied to different key machine health indicators to determine maintenance types of assets, specific issues are different for industrial schedules. Billions of dollars are spent every year rotating machines than from rotating engines. Reciprocal replacing machinery components that have worn out due engines tend to generate fine wear particles and engine to insufficient lubricant performance. Knowing how to oils can be dark due to soot (nano-sized carbon particles interpret changing lubricant properties can increase both as combustion byproduct). Elemental analysis is primary the uptime and the life of mission critical assets. The or sometimes the only analysis performed in a commercial existence or amount of debris and particles from wearing oil lab that assesses engine wear conditions because parts, erosion and contamination provide insights about concentrations of different wear metal elements indicate the issues affecting performance and reliability. wear severity of moving parts in an engine. Slower moving rotating machines, such as gearboxes, tend to generate Lubricants, fuels and other key fluids analyses provide larger wear particles. As most of them are made of steel, critical early warning information indicative of machine large ferrous particle analysis is fairly common and easy to failure. By analyzing and trending data, one can schedule perform on oils from these assets. maintenance before a critical failure occurs. The results are higher equipment availability and productivity, lower Contaminants in oil can be in solid or liquid form. Solid maintenance costs, lower total cost of ownership (TCO), contaminants such as sand and dirt are commonly fewer outages, optimal equipment performance and a monitored by particle counting and sizing techniques. greener operation. Liquid contaminant for industrial rotating machines is mostly water. For diesel or gas engines, however, it can be What is In-service Oil Analysis? water, coolant or fuel. A fairly common fluid contaminant across all asset types is the accidental or purposeful Lubricating oil is the life blood of oil wetted machinery. use of an incorrect lubricant when topping off old oil. All In-service oil analysis can provide information about machine contaminants can significantly reduce the useful life of the wear condition, lubricant contamination as well as lubricant oil and increase machine wear. They need to be prevented condition (Figure 1). Reliability engineers and maintenance proactively with proper seals and filtration systems and they professionals can make maintenance decisions based on need to be monitored regularly. diagnoses of oil analysis results. Monitoring lubricant degradation helps one decide if the oil Machine wear analysis is is no long fit for use and if it needs to be changed. One key essentially the analysis oil property is viscosity. The viscosity is typically measured of particles in the oil. at 40C for rotating machines and at 100C for engines. For oil Machine wear can be in rotating machines, oxidation and acidity of the oil (Total classified into adhesive Acid Number or TAN) are monitored to determine if the oil (sliding) wear, abrasive is still fit for use and to prevent corrosion. For engine oils, (cutting) wear, fatigue oxidation, nitration, sulfation and total alkaline additive wear, and corrosive wear. reserve in oil (Total Base Number or TBN) are monitored. For A full
Details
-
File Typepdf
-
Upload Time-
-
Content LanguagesEnglish
-
Upload UserAnonymous/Not logged-in
-
File Pages120 Page
-
File Size-