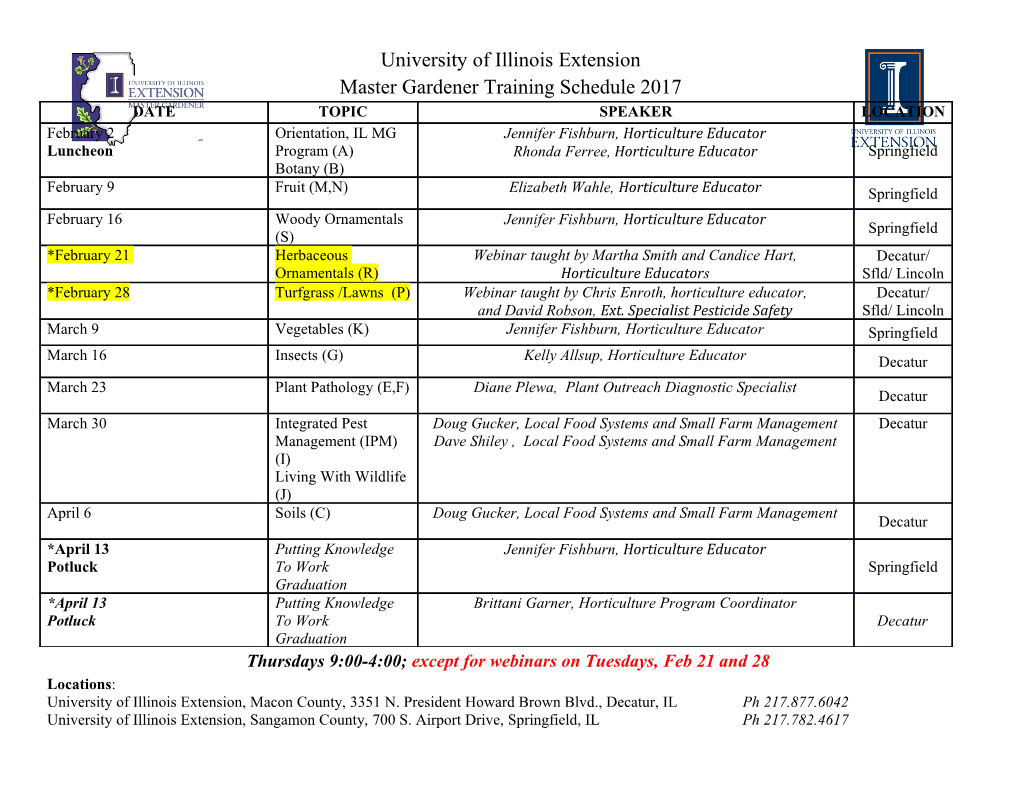
Power Electronics and Drives CHAPTER FIFTEEN AC DRIVES 15.1 INTRODUCTION AC drives is a term used to refer to equipment designed to control the speed of an a.c. motor. They receive a.c. power and convert it to an adjustable frequency, adjustable voltage output for controlling motor operation. Inverters and other types of frequency changers are typical examples of modern a.c. drives which are also called adjustable frequency drives. A typical inverter receives 400 V a.c., three-phase, 50 Hz input power and in turn provides the proper voltage and frequency for a given speed to the motor. The three common inverter types are the variable voltage inverter (VVI), current source inverter (CSI), and pulse width modulation (PWM). Another type of a.c. drive is a cycloconverter. These are commonly used for very large motors used in steel industry and mils. The cycloconverters is an arrangement of poly-phase rectifiers in which the firing delay is cyclically varied to synthesise an a.c. output, instead of the set delay for producing a controllable d.c. for the d.c. motor previously mentioned. A feature of a.c. drives is the ability to increase or decrease the voltage and frequency to a motor gradually. This accelerates the motor smoothly with less stress on the motor and connected load. Smoothing is a feature that can be added to the acceleration/ deceleration operation. This feature smoothes the transition between starting and steady-state operation. There are several types of a.c. motors used in industrial applications that need real drives to suit a given task. In all types of drives, motors and load have stored energy which can be either regenerated or dissipated as the load speed falls. One third of the world's electricity consumption is used for running induction motors driving pumps, fans, compressors, elevators and machinery of various types. In general, the speed of a.c. motors depends on the frequency of the supply voltage and the number of magnetic poles per phase in the stator. Early speed controllers depended 649 Power Electronics and Drives on switching in different numbers of poles and control was only available manually and in crude steps. Modern electronic drives make continuously variable frequency supplies possible permitting closed-loop speed control. This chapter is intended to provide a basic understanding of a.c. drive terms, types and theory of operations. Benefits of AC drive Large energy savings at lower speed. Increased life of rotating components due to lower operating speed. Reduced noise and vibration level. Reduction of thermal and mechanical stresses. Lower kVA. High power factor. 15.2 TYPES OF AC MOTORS The types of a.c. motor available in industry are classified according to the supply as single-phase and poly-phase motors. These two types may also be classified according to the principle of operation into induction type and synchronous type as follows: 1- single-phase motors (a) Induction type-squirrel cage (i) Split-phase (ii) Capacitor start (iii) Permanent split capacitor (iv) Capacitor start / capacitor run (v) Split-phase start / capacitor run (vi) Shaded pole (b) Induction type-wound rotor (i) Repulsion (ii) Repulsion start (iii) Repulsion induction (c) Single-phase synchronous (i) Hysteresis (ii) Reluctance (iii) Permanent magnet (d) Single-phase universal motor (AC and DC) 2- Poly-phase motors (a) Induction type (i) Wound rotor (ii) Squirrel – cage (b) Synchronous 656 Power Electronics and Drives These motors are summarised in the following diagram (Fig.15.1) , Split –phase Capacitor start Squirrel Permanent capacitor -cage Capacitor start capacitor run Shaded -pole Single-phase Induction Wound Repulsion Universal rotor Repulsion start Repulsion induction AC and DC Synchronous Hysteresis AC Reluctance Motors Permanent magnet Induction Wound rotor Poly-phase Synchronous Squirrel -cage Fig.15.1 Types of a.c. motors. 15.3 THREE-PHASE INDUCTION MOTOR : REVISION OF EQUATIONS The three-phase induction motors ( also called asynchronous motors) are the most widely used electric motors in industry. The popularity of this type of motors in most industrial applications is because of their simple, robust construction because they can build without slip-rings or commutator, rugged, relatively cheap, require little maintenance and have self-starting torque. An induction motor of a medium size may have an efficiency as high as 90 percent and power factor of nearly 0.9. The physical size of such a motor for a given output rating is small as compared with d.c. and a.c. synchronous motors of same rating. There is another distinguishing feature of induction motor is that it is a singly excited machine, i.e. only the stator winding is connected to the a.c. supply, no electrical connection from the supply to the rotor is needed. Finally It can be manufactured with characteristics to suit most industrial requirements. 656 Power Electronics and Drives Beside the above numerous advantages of the induction motor, it has two main inherent disadvantages: 1. Its starting torque is inferior to d.c. shunt motor. 2. It is essentially a constant speed motor and its speed cannot be changed easily. The speed of an induction motor is determined by the supply frequ- ency and number of poles, with a few percent regulation from no-load to full-load. However, the speed is frequency dependent and consequently these motors are not easily adapted to speed control. A wide range of speed control is only possible by using expensive power electronic circuit with advanced digital control. We usually prefer d.c. motors when large speed variations are required due to its inexpensive methods of control. 15.3.1 Basic Principles of Three-Phase Induction Motor with Sinusoidal Supply Voltages Like any electric motor, a three-phase induction motor has a stator and a rotor. The stator carries a three-phase winding (called stator winding) while the rotor carries a short-circuited winding (called rotor winding). Only the stator winding is fed from three-phase supply. The rotor winding derives its voltage and power from the externally energized stator winding through electromagnetic induction and hence such a machine is often called the induction machine. The induction motor may be considered to be a transformer with a rotating secondary in the sense that the power is transferred from the stator (primary) to the rotor (secondary) winding only by mutual induction. Hence, it can, therefore, be described as a “transformer type” a.c. machine in which electrical energy is converted into mechanical energy. When the stator windings are connected to a set of balanced three- phase voltages and the rotor circuit is closed, the resulting three-phase current establish a rotating mmf wave that results in a flux wave of constant amplitude rotating at constant speed known as the synchronous speed. The value of the synchronous speed is fixed by two parameters: (a)The supply frequency, (Hertz), (b)The number of poles p for which the primary is wound. The synchronous speed of the rotating magnetic field is given by The number of poles p must be an even integer since for every north pole there is a corresponding south pole. The following Table-15.1 shows motors speeds for motors with different numbers of poles working with different a.c. supply frequencies. 656 Power Electronics and Drives Table 15.1. Synchronous speed of induction motor for different number of poles. Rotor Speed (rpm) Number of 2 4 6 8 10 12 poles (p) Frequency 3000 1500 1000 750 600 500 f = 50 Hz Frequency 3600 1800 1200 900 720 600 f = 60 Hz An induction motor runs at a shaft speed n that is less than the synchr- onous speed at which the stator rotating field is rotate. The speed difference is called the slip speed. The ratio of slip speed to synchronous speed is the most important variable in induction motor operation and is called the per-unit slip s, and is given by: where s is the slip in per unit, ns is the synchronous speed in rpm, and n is the rotor speed. Since the rotor current is proportional to the relative motion between the rotating field and the rotor speed, the rotor current and hence the torque are both directly proportional to the slip. For particular cases, the slip of the motor will have the following special values: When the motor is running at synchronous speed , i.e. and . At standstill and . If the motor is rotating at synchronous speed in the reverse direction, then and . Squirrel cage motors are built with the slip ranging from about 3 – 20%. Motors with a slip of 5% or higher are used for hard-to-start applications. A motor with a slip of 5% or less is called a normal slip motor. A normal slip motor is often referred to as a constant speed motor because the speed changes very little with variations in load. At full load the per-unit slip usually 5% for a small motor because . 656 Power Electronics and Drives 15.3.2 Development of Circuit Model (Equivalent Circuit) Standstill Operation At standstill, the motor can be considered as a static transformer with primary (stator) winding and secondary (rotor) winding. If the stator is fed from a three-phase supply with voltage V1 is the phase voltage, the air gap field produced rotates at synchronous speed ns . This field induces emfs E1 and E2 in both the stator and rotor winding respectively. The magnitudes of these emfs are given by, assuming unity winding factor (kw =1) , where is the effective transformation (turns) ratio between the stator and rotor winding which is usually greater than unity and is typically in the range 1.1 – 1.3.
Details
-
File Typepdf
-
Upload Time-
-
Content LanguagesEnglish
-
Upload UserAnonymous/Not logged-in
-
File Pages71 Page
-
File Size-