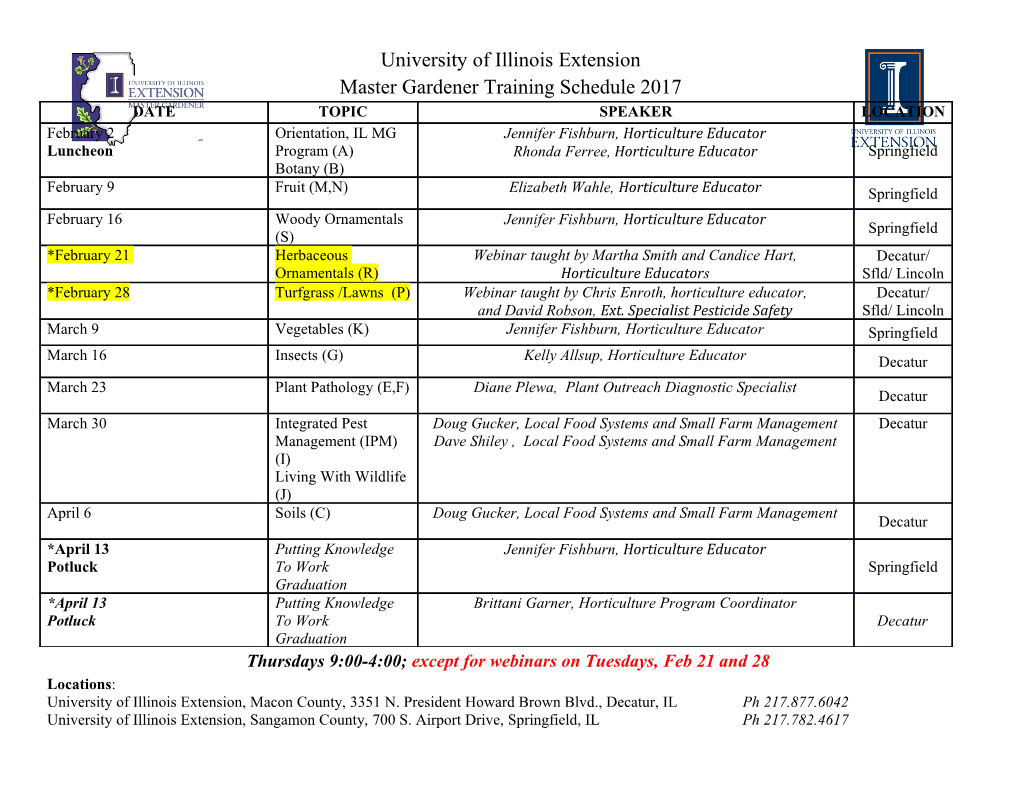
FEATURE ARTICLE Custom fabricated picking and suspension ring New Kosciuszko Bridge – Transforming the New York City Skyline The Kosciuszko Bridge, named in honor of notorious locally for its state of structural The new Kosciuszko Bridge is designed Polish military engineer and Revolutionary disrepair and severe congestion. as a cable-stayed structure, the first of its War hero Tadeusz Kosciuszko, carries I- In May 2013, the New York State kind in New York City. The approach span 278 over Newtown Creek, the dividing line Department of Transportation (NYSDOT) piers and connector abutments, not between the New York City boroughs of awarded a design-build contract to the discussed in this article, are supported Brooklyn and Queens. At the time of the joint venture of Skanska USA Civil primarily by driven piles, along with a bridge’s construction in 1939, Newtown Northeast, Kiewit Infrastructure Company limited number of micropiles at several Creek was an industrial hotbed lined with and ECCO III Enterprises (SKE), in abutments constructed under low- petroleum refineries, coal handling conjunction with design partner HNTB headroom conditions. At the center pylon, facilities, metal processors, and chemical New York Engineering and Architecture. rock-socketed drilled shafts of and fertilizer manufacturers. The waterway The project scope includes design and unprecedented size and capacity within the became one of the largest shipping hubs in construction of a new eastbound bridge metropolitan area were the signature feature the Northeast, and to accommodate the and improvements along a 1.1 mi (1.8 km) of the project’s deep foundation work. maritime traffic, the existing Kosciuszko segment of the Brooklyn-Queens Bridge was constructed with a fixed span Expressway (BQE), as well as demolition of Subsurface Profile 125 ft (38.1 m) above the mean high water the existing bridge. With the exception of In the area of the center pylon, on the west level. This resulted in a structure that now some minor replaceable items, the bridge bank of Newtown Creek, the general soil features nonstandard roadway grades on has a required 100-year design service life. profile consists of approximately 20 ft (6m) both approach spans, inadequate sight A new westbound (Brooklyn-bound) of urban fill overlying a thin organic clay distances across the main span and bridge, built within the footprint of the layer, then glacial deposits composed of entrance ramps with insufficient merge existing Kosciuszko Bridge, will be silty sand with gravel and a lower clay layer lengths. Serving more than 160,000 completed under a separate contract. known as the Raritan Formation. Beneath vehicles per day, the bridge has become lies a layer of decomposed rock, consisting AUTHOR Nolan S. Kealy, P.E., Foundations Manager, Skanska-Kiewit-ECCO III Joint Venture DEEP FOUNDATIONS • SEPT/OCT 2015 • 87 heavy metals in concentrations exceeding critical to the project schedule to allow the Once the casings were sealed and this phase of the work had to be performed employed to determine the depth of acceptable limits set forth by the New York use of reverse circulation drilling (RCD) grouted, RCD was used to excavate each 6.5 as a two-shift operation during the dead of sediment present at the tip of each State Department of Environmental methods to excavate the socket length. ft (2 m) rock socket. The pile top rotary table winter in order to maintain the project completed shaft. Five individual bottom Conservation (NYSDEC). Above the water Installation methods were revised to spun a 67.5 ton (61 tonne) drill string, schedule. Temperatures typically rose locations per shaft were probed, with the table, the soils were also classified as highly incorporate an oversized 8 ft (2.4 m) including a full-faced roller cutting bit above freezing for only a few hours each requirement that 50% of the base of each corrosive, with an expected steel loss of diameter shaft supported by polymer slurry. attached to the bottom. In the reverse day, requiring a significant effort to keep shaft have less than 0.5 in (13 mm) of 4.56 mils (0.12 mm) per year. A 162,000 gal (613 m3) slurry plant was circulation process, compressed air is pumps running and prevent supply and sediment and no location exceeding 1.5 in mobilized to the site to batch and hold KB injected into the bottom of the drill string, discharge piping from icing up. (38 mm) at the time of concrete placement. Drilled Shaft Construction International’s Enhanced SlurryPro CDP creating a pressure differential that airlifts Due to the depth of the shafts, rein- To meet these criteria, each shaft was To support the nearly 300 ft (91.4 m) tall system. A Liebherr LB44 hydraulic rotary cuttings back to the surface. Flowrates on forcing cages were constructed in three airlifted, removing any fines leftover from center pylons, a total of eight drilled shafts drill rig was used to install surface casing the order of 2,000 gpm (7,570 Lpm) are sections, using internal template rings the RCD and exchanging the entire fluid were required — four at each footing. Each and excavate the overburden. The typically generated by this type of system. attached to “hourglass” stiffening frames. column with fresh water. Further, during shaft required a nominal resistance of temporary 8.5 ft (2.6 m) casing was However, strict environmental regulations The fully assembled cage contained 18 No. construction of the first shaft, after a 22,000 kips (97,861 kN) in compression installed 40 ft (12.2 m) and seated into the prohibited any water to be supplied from or 18 75 ksi (517 MPa) vertical bars, with successful Mini-SID inspection was and 2,900 kips (12,900 kN) in tension. The upper clay layer to prevent any possibility of discharged into the nearby Newtown Creek bundled bars in the upper 60 ft (18.3 m) achieved, a 72-hour waiting period was shafts were cased through the overburden vertical migration of shallow contaminates without first being treated to bring heavy and weighed nearly 50 tons (45.5 tonnes). imposed and the shaft inspection process soils using a 7 ft (2.1 m) inner diameter cas- into the lower aquifer. metals, pH and solids down to acceptable Custom designed and built lifting rings were repeated. This demonstration alleviated ing, with a 6.5 ft (2 m) diameter rock socket During the drilling process, each shaft levels. Instead, all flushing water was used to pick and suspend the cage sections concerns that the shafts could fall out of drilled 13 ft (4 m) below the casing tip. was profiled multiple times using a supplied from nearby hydrants and during splicing and concrete placement. specification if a weekend or unexpected SoniCaliper® provided by Loadtest to recirculated in a continuous loop, settling Although the concrete supplier’s ready- downtime period occurred between the confirm verticality of the open hole. Depths out the rock cuttings in a lined detention mix plant was located only about 2 mi (3.2 km) time of the Mini-SID inspection and to rock varied from 147 ft (44.8 m) to 170 ft pond. Further complicating the installation, from the site, local Brooklyn traffic would concrete placement. (51.8 m), but careful control of the drilling frequently push delivery times to 45 A “Chicago Method” Osterberg Cell (O- process yielded minimal vertical deviations minutes or more. A 6,000 psi (41.3 MPa) cell) load test, performed on the first ranging from 0.34% to 0.76%. Once rock self-consolidating concrete (SCC) mix, completed production shaft, was then was encountered, it was drilled and leveled developed for previous Skanska pro- carried out to confirm the design end- with conventional tooling. This was a time jects, was chosen for its ease of worka- bearing assumptions. This variation on the consuming, but critical step in the construc- bility and extended placement time. traditional O-cell test places the hydraulic tion process. Casing was then lowered into jack at the shaft tip with a circular bottom the open hole in sections ranging from 50 ft Quality Control plate of a reduced diameter compared to the (15.2 m) to 80 ft (24.4 m) using a Liebherr Since the shaft design relied on end rock socket. Unit end-bearing values are LR1350 service crane. Two full-penetration bearing to provide nearly 80% of its able to be verified by a single 6,000 kip welded splices were required per shaft, with capacity, ensuring cleanliness of the (26,689 kN) capacity O-cell jack, which the fully-deployed casing string weighing as rock socket bottom prior to pouring applies load onto the smaller diameter plate much as 48.5 tons (44 tonnes). This casing concrete was paramount. A miniature using the available side shear capacity and Overburden drilling adjacent to the existing bridge was surveyed into place, then twisted and shaft inspection device (Mini-SID) was dead weight of the shaft above as a reaction. seated into the bedrock. The seal in rock of undisturbed natural bedrock that has Once the project was awarded, SKE was confirmed when a head differential in been chemically weathered. The result is an began a soil boring program to provide a the slurry level of about 10 ft (3 m), created extremely stiff green clayey soil with SPT more comprehensive study of the by pumping down the inside of the casing, values from 50 to over 100 blows per foot subsurface conditions than the contract bid could be maintained. (0.3 m). The competent rock below borings provided. Additional borings in the One caveat of this installation method consists of Fordham Gneiss with pegmatite area of the drilled shaft footings confirmed was that once the casing was installed, an inclusions.
Details
-
File Typepdf
-
Upload Time-
-
Content LanguagesEnglish
-
Upload UserAnonymous/Not logged-in
-
File Pages4 Page
-
File Size-