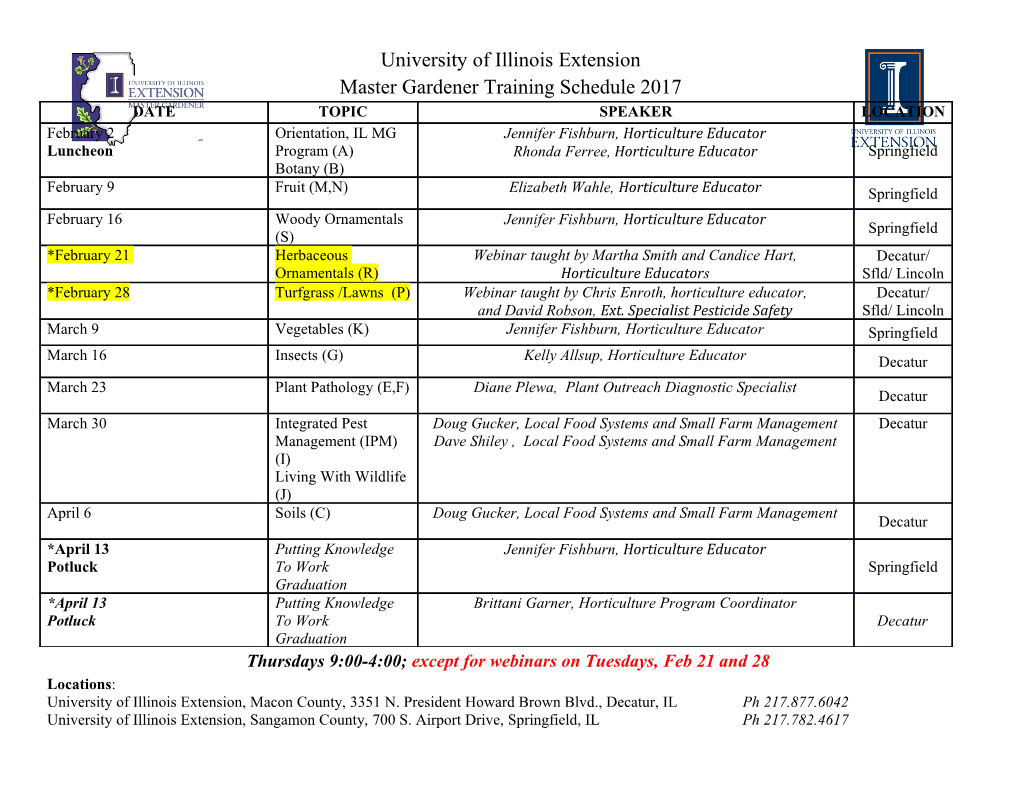
DRILLING Measurements at the Bit: A New Generation of MWD Tools Measurements-while-drilling technology has moved down the drillstring to enlist the bit itself as a sensor. Drillers time information about petrophysics and drilling mechanics without a lag between bit and sensors. This technical ciency of directional drilling, enhance real-time formation evaluation, and ultimately create a more productive well. a a a a a a a aa a a a a Steve Bonner a a a a aa aa a a a a Trevor Burgess a a Brian Clark aa a aa a a a a a a a aa a Dave Decker a Jacques Orban Kick-off aaa a a a a a a point Bernhard Prevedel a a First build aaa a a a a a a a a a a Sugar Land, Texas, USA a (5.5 ft /100 ft) a a aa aa a Martin Lüling a a a G aa aa e a a Second build a aa a a aa a a a aa Ridgefield, Connecticut, USA o a a a a a m (10 ft /100 ft) e a a a a tr a Tangent aa a a a a a a a a a ic Jim White s section e c aaa a ti a a aa a a a a a Aberdeen, Scotland a a a o a a a a a a n a a Horizontala Target entry point tolerance a a a a a a aa aa a aa a a aaa a a a a a a a In this article, IDEAL (Integrated Drilling Evaluation and a aaa a aa a a a a a aa a a Logging), GeoSteering tool, PowerPak, RAB (Resistivity- a a a a a a a at-the-Bit), RWOB (Receiver, Weight on Bit and Torque a a a Geosteering section a a aa a a a tool), PowerPulse, CDR (Compensated Dual Resistivity a a a aaa a a a tool), SFL (Spherically Focused Resistivity Log), AIT (Array Induction Imager Tool), CDN (Compensated Den- a a aa a a a a a a a a a sity Neutron tool) and FMI (Fullbore Formation MicroIm- ager) are marks of Schlumberger. aaa a a aa For help in preparation of this article, thanks to David Allen, Schlumberger Well Services, Sugar Land, Texas, nA typical horizontal well plan. Geometric drilling refers to USA; Philippe Faure, Dominic McCann, Samantha drilling along a fixed, predetermined trajectory, generally based Miller, Bernard Montaron and Kanai Pathak, Anadrill, on offset data and a stratigraphic model. Decisions about steer- Sugar Land, Texas, USA; Richard Rosthal, Schlumberger ing are based only on real-time information about bit direction Logging While Drilling, Sugar Land, Texas, USA; and David Hill, Schlumberger Well Services, New Orleans, and inclination. Geosteering refers to navigating the borehole Louisiana, USA. using geologic information in real time. Geosteering is possible 1. Betts P, Blount C, Broman B, Clark B, Hibbard L, with logging-while-drilling sensors, which are integrated into Louis A, Oosthoek P: “Acquiring and Interpreting Logs drill collars 40 to 100 ft [12 to 30 m] above the bit and steerable in Horizontal Wells,” Oilfield Review 2, no. 3 (July motor. Geosteering becomes more efficient with measurements 1990): 34-51. at the bit. Logging While Drilling. Schlumberger Education Ser- vices: Houston, Texas, USA, 1992. Conventional drilling of high-angle and hor- properties—are remote from the bit, crucial 2. For a review on horizontal drilling methods: izontal wells is like piloting an airplane from drilling decisions are delayed and data may Burgess T and Van de Slijke P: “Horizontal Drilling the tail rather than the cockpit. Information require more complex interpretation. In par- Comes of Age,” Oilfield Review 2, no. 3 (July 1990): required to land the well in the target forma- ticular, course corrections are delayed by 22-33. tion is derived from sensors 50 ft [15 m] or lag in measurements needed to make steer- more behind the bit or at the surface. ing decisions, resulting in less drainhole in Because these measurements—about well the pay zone. Also, maximum drilling effi- trajectory, drilling efficiency and formation ciency requires information about mechani- 44 Oilfield Review Locked assembly Rotary mode for vertical, tangent or horizontal sections Steerable assembly Rotary or sliding mode and geologists now have real- progress promises to improve effi- Locked Steerable cal power delivered to the bit, which is nTypical bottomhole assemblies for horizontal drilling. A rigid, inferred from surface measurements, or locked, assembly is used for drilling a vertical, tangent or degrading its accuracy. And resistivity mea- straight horizontal section. Rigidity increases with the number of stabilizers. This type of assembly permits only gradual changes surements from logging-while-drilling in the vertical angle of the well trajectory. A steerable assembly (LWD) sensors in drill collars are limited to with a downhole motor inside a bent housing can vary well tra- formation resistivity less than 200 ohm-m.1 jectory vertically and to the left and right, and can change Despite these limitations, horizontal and angle more quickly than a locked assembly. a a a a a a a a a high-angle drilling have proved successful, a especially in simple geologic settings— a aa a a a uncomplicated layer-cake structure. Nearly a aa a a aa a a a aa all these wells start vertically, with a con- a a a a a ventional rotary bottomhole assembly (BHA) aa a a a a a a a a (previous page).2 The drillstring and bit are a Sliding mode a aa a a a a a rotated from the surface either by a rotary a a a a a a a a a table on the derrick floor or a motor in the a a aa aa a aa a a traveling block, called a topdrive. Drilling a Rotary mode this way is called rotary mode. To kick off a aa a a a a a aa a a from vertical, the rotary assembly is a a a aa a a a replaced with a steerable motor—usually a a a a positive displacement motor, driven by mud Increased diameter due to a a aa a a a a a a a a a flow, in a housing bent 1° to 3° (above, outward tilt of steerable motor (scale exaggerated) aaa a a aa right). When mud is flowing, the motor rotates the bit, but not the drillstring. This nHow well trajectory is changed. In rotary mode, both the bit type of drilling is called sliding mode, and drillstring rotate and the bit cuts a straight path parallel to because the drillstring slides along after the the axis of the drillstring above the bent sub. In sliding mode, bit, which advances in the direction of the only the bit rotates and the hole follows the axis of the bent hous- housing below the bend (right). The larger ing below the bend. the angle of the bent housing, the sharper vertical. Large changes in direction are adjustments in inclination can be made with the curvature of the trajectory. The direction made by lifting off bottom and reorienting conventional rotary assemblies only by in which the bit is pointing, called toolface, the bent sub by rotating from surface. Small pulling out of the hole and varying the size is measured and sent to surface by measure- changes are made by varying weight on bit, and placement of stabilizers. Most horizon- ment-while-drilling (MWD) equipment for which changes the reactive torque of the tal sections, and some tangent sections, are real-time control of bit orientation. Mea- motor and hence toolface orientation. drilled with a steerable motor while rotating surements include azimuth, which is the Once sufficient inclination has been built, the drillstring from surface. In this mode, the compass bearing of the bit, and inclination, straight or tangent sections can be drilled in steerable motor behaves like a rotary BHA, which is the angle of the bit with respect to several ways. One is with a conventional maintaining both azimuth and inclination. rotary, or “locked,” assembly, which is rigid enough to allow fast, straight drilling. Small adjustments in inclination can be made by April/July 1993 varying weight on bit or rotary speed. Large 45 However, the presence of the steerable motor allows the driller to make course cor- XX00 rections without tripping the drillstring out Actual trajectory of the hole. Generally, the driller tries to make as much hole as possible using a rotary assembly or a steerable motor in rotary mode. Rotation of the drillstring Proposed geometric trajectory reduces the risk of getting stuck and allows vertical depth, ft True Reservoir XX25 faster drilling than in sliding mode. X700 X900 X100 X300 X500 X700 X900 Overcoming Limitations in Horizontal distance, ft Horizontal Drilling Today, the ability to drill horizontally is nThe risk of steering geometrically with inadequate information about reservoir dip— undisputed, and records for the longest hori- less drainhole in the pay zone. This North Sea well was successfully drilled beyond hori- zontal section are broken nearly as soon as zontal, but the reservoir dipped more than expected. Only about 15% of the drainhole was in the pay zone. they are set.3 Yet, the efficiency of drilling and steering horizontally is limited by the distance between the bit and measurements. Bulk density In drilling, for example, one way to define efficiency is the ratio of time spent making hole to the total rig time, including opera- Rad (deep) resistivity Rps (shallow) resistivity tions such as trips or hole conditioning.
Details
-
File Typepdf
-
Upload Time-
-
Content LanguagesEnglish
-
Upload UserAnonymous/Not logged-in
-
File Pages11 Page
-
File Size-