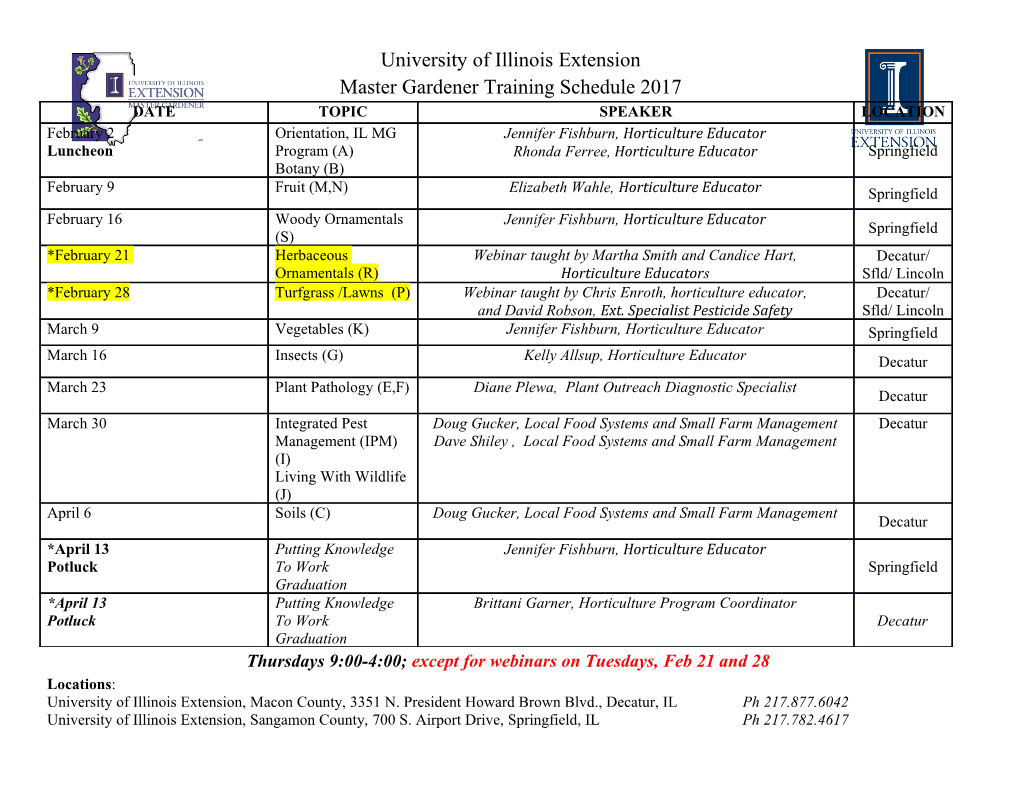
RecyclingRecycling TechnologiesTechnologies && ConsiderationsConsiderations (Introduction(Introduction toto MineralMineral ProcessingProcessing && ExtractiveExtractive MetallurgyMetallurgy inin Recycling)Recycling) Edgar E. Vidal and Patrick R. Taylor Kroll Institute for Extractive Metallurgy Colorado School of Mines G.S. Ansell Department of Metallurgical & Materials Engineering KIEM WhyWhy ShouldShould CompaniesCompanies Recycle?Recycle? Computer Monitor Recycling in China – ¾ The bottom line is Copyright Basel Action economics. Network ¾ But in addition, companies may derive positive benefits from addressing both: social responsibility and sustainable development issues. G.S. Ansell Department of Metallurgical & Materials Engineering KIEM WhatWhat TechnologyTechnology isis usedused inin Recycling?Recycling? ¾ Most recycle technology is based upon our understanding of both mineral processing and extractive metallurgy. ¾ Innovative advances in both technologies have been, and are being, made to address the unique resource recovery problems associated with both recycling and waste Computer Wire Recycling minimization. in China (Copyright Basel Action Network) G.S. Ansell Department of Metallurgical & Materials Engineering KIEM DUST EXHAUST TRUNK LINK COLLECTOR EXHAUST AIR Fe WIRE CROSSBELT INPUT MAGNET TWO DECK EXHAUST SCREEN WASTE FAN PRIMARY PRODUCT GRANULATOR CROSSBELT SECONDARY TERTIARY DUAL MAGNET GRANULATOR GRANULATOR ASPIRATOR BIN Fe COPPER OR ALUMINUM DUST GRAVITY WireWire ProcessingProcessing SystemSystem SEPARATOR (System(System Flowsheet)Flowsheet) TAILINGS SCREENERS TAILINGS With WASTE STONER RESIDUAL COPPER Technology CONCENTRATE ALUMINUM COPPER PRODUCT PRODUCT G.S. Ansell Department of Metallurgical & Materials Engineering KIEM 20002000 poundpound perper hourhour MechanicalMechanical WireWire RecoveryRecovery PlantPlant G.S. Ansell Department of Metallurgical & Materials Engineering KIEM SomeSome QuestionsQuestions ¾ What information do we need to obtain relative to a waste or recycle stream, both during the design and operational phases? ¾ Should we use mineral processing, hydrometallurgy, electrometallurgy and/or pyrometallurgy on a specific waste or recycle stream? G.S. Ansell Department of Metallurgical & Materials Engineering KIEM SomeSome QuestionsQuestions ¾ What is “liberation” and why is it important? ¾ Some materials do not require liberation for metal recovery, in this case what is the concept of “exposure”? ¾ What specific qualities of a waste or recycle stream might be exploited in order to separate and/or expose it; or to selectively recover a specific metal or metals? G.S. Ansell Department of Metallurgical & Materials Engineering KIEM Building an Economic Opportunity from a Resource Economic Opportunity Identified Resource •Metallic Mineral •Industrial Mineral •Energy Mineral Resource •Recycle Material Process Properties/ Characteristics G.S. Ansell Department of Metallurgical & Materials Engineering KIEM The ultimate goal is Process Supports production of metals and the Economic materials in their Opportunity economically purest form, Economic from the resource. Opportunity The goal of Process is Resource a product with the highest possible recovery at acceptable grade. Process Properties/ Characteristics G.S. Ansell Department of Metallurgical & Materials Engineering KIEM Properties/Characteristics support the Process Start with determining the Economic properties/characteristics of Opportunity the resource matrix and its components. •Size •Shape •Chemistry Resource •Density •Conductivity •Magnetic Susceptibility Process Properties/ Characteristics G.S. Ansell Department of Metallurgical & Materials Engineering KIEM CharacterizationCharacterization byby MicroscopicMicroscopic GrainGrain CountCount ¾Typical Heavy Mineral (beach sand) concentrate assemblage. ¾Ilmenite, rutile, zircon, etc., (valuable HM) as well as non-value minerals. ¾Characterization required to develop process scheme and to monitor process Photograph by Outotec Inc., Jacksonville FL 2007 success. G.S. Ansell Department of Metallurgical & Materials Engineering KIEM TwoTwo QuartzQuartz SandSand DepositsDeposits Optical Microscopy Characterization showing Potential Iron Inclusion Problems Both Deposits have nearly identical Fe content YES NO Pictures Outotec Inc., Jacksonville FL, 2007 G.S. Ansell Department of Metallurgical & Materials Engineering KIEM Complexity of Particles’ Characterization and Liberation ¾Requires sophisticated computer-controlled electron scanning. Always conducted as a (f) particle size ¾Scanning electron Microscope (1 - 0.005 μm) ¾QEM-Scan is commercial SEM based unit with very broad application including minerals ¾Mineral Liberation Analyzer (MLS) is also SEM based ¾Provides bulk mineral assemblage, a calculated bulk chemical analysis and particle-by-particle deportment of target metals G.S. Ansell Department of Metallurgical & Materials Engineering KIEM Example MLA *From CAMP-Corby Anderson G.S. Ansell Department of Metallurgical & Materials Engineering KIEM MineralMineral ProcessingProcessing andand ExtractiveExtractive MetallurgyMetallurgy ¾ Mineral Processing – the utilization of methods to separate valuable minerals (or metals) from waste minerals based on physical or surface chemistry properties ¾ Hydrometallurgy – the utilization of aqueous environments to “leach” metals from minerals (or other sources), to separate dissolved metals from each other or dissolved impurities, and to recover metals from solution. ¾ Pyrometallurgy – the utilization of high temperatures to modify the chemistry of minerals (or other sources), to reduce minerals to metals, and to refine metals. ¾ Electrometallurgy – the utilization of electricity to recover and/or to refine metals in aqueous or molten salt solutions. G.S. Ansell Department of Metallurgical & Materials Engineering KIEM MineralMineral ProcessingProcessing ¾ Mineral properties: chemistry, density, magnetic susceptibility, conductivity, surface chemistry, optical properties, etc. ¾ Comminution: Crushing, grinding, shredding (liberation) ¾ Sizing (screening, hydrocyclones, etc.) ¾ Gravity separation ¾ Flotation ¾ Electrostatic separation ¾ Dense media separation ¾ Magnetic separation ¾ Solid-liquid separation (Thickening and filtering) ¾ Waste treatment and minimization G.S. Ansell Department of Metallurgical & Materials Engineering KIEM HydrometallurgyHydrometallurgy ¾ Leaching – the selective dissolution of metals from minerals, ores, or other sources. ¾ Solid/liquid separation – thickening, filtering. ¾ Solution purification – solvent extraction, ion exchange, etc. ¾ Metal recovery - precipitation of metals or oxides – hydrogen reduction, cementation, pH changes, etc. ¾ Waste treatment and minimization. G.S. Ansell Department of Metallurgical & Materials Engineering KIEM PyrometallurgyPyrometallurgy ¾ Fuel and ore preparation – reductants, drying, calcination, roasting, agglomeration, etc. ¾ Reduction of metal oxides – iron reduction, etc. ¾ Volatile metals – vaporization, zinc production, refining processes, etc. ¾ Slags and refractories – impurity removal, heat and product containment, etc. ¾ Matte smelting – Copper smelting, nickel smelting, etc. ¾ Refining Processes – desulfurization, deoxidation, etc. ¾ Rare and Reactive Metals – Ferroalloys, metallothermic reactions, pure metals, halides, etc. G.S. Ansell Department of Metallurgical & Materials Engineering KIEM ElectrometallurgyElectrometallurgy ¾ Electrowinning – the utilization of electricity to recover metals from solutions. ¾ Electrorefining – the utilization of electrical energy to purify metals. ¾ Fused salt electrolysis – the recovery of metals from molten salts through electricity (aluminum, magnesium, sodium, etc.) G.S. Ansell Department of Metallurgical & Materials Engineering KIEM Extractive Metallurgist’s Toolbox ¾ Characterization of chemistry and properties. ¾ Energy & Mass Balances ¾ Chemical Thermodynamics ¾ Heterogeneous Kinetics ¾ Reactor Design ¾ Transport Phenomena (Heat, Mass and Momentum Transfer) ¾ Unit Operations in Mineral Processing, Hydro - , Pyro - and Electro - metallurgy ¾ Unit Operations in Recycle and Waste Processing G.S. Ansell Department of Metallurgical & Materials Engineering KIEM IntroductionIntroduction ¾ The art of extracting metals from ores dates back to the dawn of human civilization. ¾ Around 4000 B.C. man learned to produce copper and bronze by the smelting of copper and tin ores in a charcoal fire. ¾ A visitor to a modern metallurgical plant will be struck by the large number of complex operations. ¾ The many different metallurgical processes may be understood as the result of a relatively small number of fundamental principles. G.S. Ansell Department of Metallurgical & Materials Engineering KIEM OreOre (Resource)(Resource) ¾ An Ore (or Resource) is a material which can be mined (or processed) economically to serve as raw material for the production of metals. ¾ The economic aspect is an important point, which makes the limit between what is ore and what is worthless depending on the existing state of technology and by the market price for the metal in question. ¾ The price of the metal or commodity is the most important driver, along with the costs (capital and operating) to treat and recover the materials. G.S. Ansell Department of Metallurgical & Materials Engineering KIEM FlowFlow SheetsSheets ¾ The combination of processes which is CB Carbonate Source used in a given plant Stockpile Off Gas is illustrated conveniently by Rotary Kiln means of a
Details
-
File Typepdf
-
Upload Time-
-
Content LanguagesEnglish
-
Upload UserAnonymous/Not logged-in
-
File Pages73 Page
-
File Size-