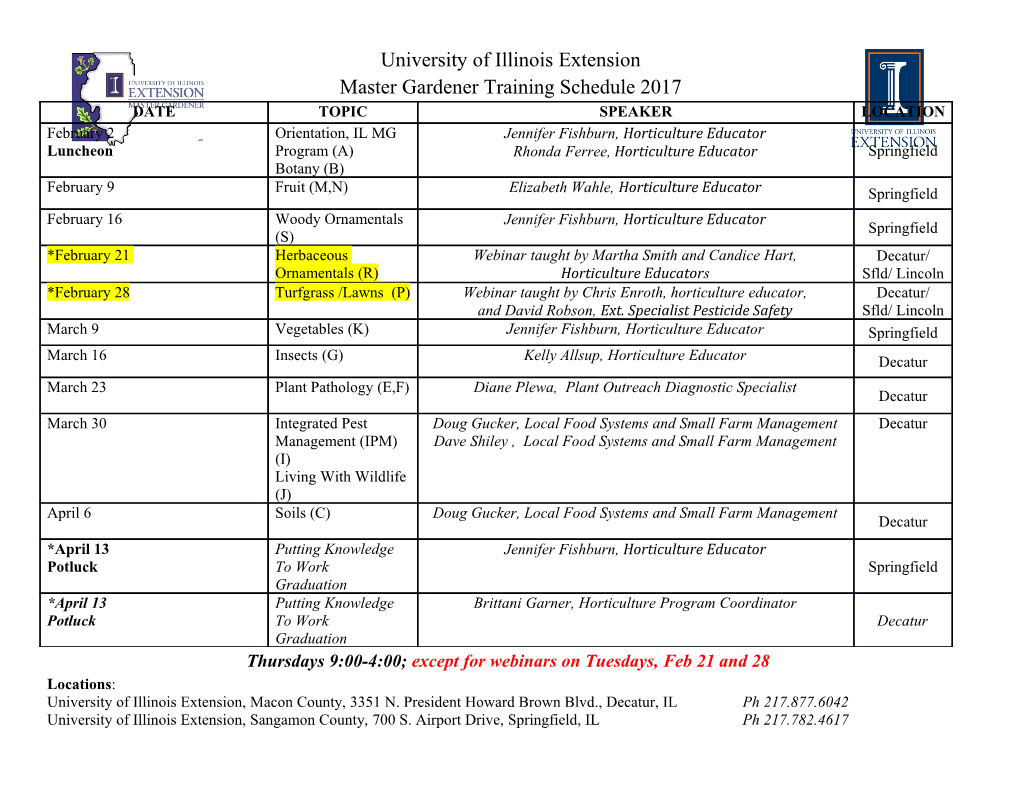
Generalized self-driven AC-DC synchronous rectification Title techniques for single- and multiphase systems Author(s) Zhong, WX; Choi, WP; Ho, WWC; Hui, SY IEEE Transactions on Industrial Electronics, 2011, v. 58 n. 8, p. Citation 3287-3297 Issued Date 2011 URL http://hdl.handle.net/10722/155631 ©2011 IEEE. Personal use of this material is permitted. However, permission to reprint/republish this material for advertising or promotional purposes or for creating new collective works for Rights resale or redistribution to servers or lists, or to reuse any copyrighted component of this work in other works must be obtained from the IEEE. IEEE TRANSACTIONS ON INDUSTRIAL ELECTRONICS, VOL. 58, NO. 8, AUGUST 2011 3287 Generalized Self-Driven AC–DC Synchronous Rectification Techniques for Single- and Multiphase Systems W. X. Zhong, W. P. Choi, Wing W. C. Ho, Member, IEEE,andS.Y.Hui,Fellow, IEEE Abstract—This paper extends the single-phase self-driven the dc–dc converters, the synchronous rectification techniques synchronous rectification (SDSR) technique to multiphase ac–dc have been applied to the three-phase full-bridge ac–dc converter systems. Power MOSFETs with either voltage- or current-sensing based on a three-phase fully controlled bridge [13] and even to self-driven gate drives are used to replace the diodes in the rectifier circuits. The generalized methodology allows multiphase SDSRs to the five-level converter [14]. While the self-driven technique be designed to replace the multiphase diode rectifiers. Unlike the uses the changing voltage polarity of the coupled windings to traditional SR that is designed for high-frequency power convert- control the switching of the power MOSFETs, other techniques ers, the SDSR proposed here can be a direct replacement of the tend to use control integrated circuits to provide the gating power diode bridges for both low- and high-frequency operations. signals. The SDSR utilizes its output dc voltage to supply power to its control circuit. No start-up control is needed because the body An attempt to replace a general-purpose diode bridge with diodes of the power MOSFETs provide the diode rectifier for the a synchronous rectifier for low-power and low-voltage (3–5 V) initial start-up stage. The generalized method is demonstrated in applications appears in [15] in which the synchronous rectifi- 2-kW one-phase and three-phase SDSRs for inductive, capacitive, cation technique is applied to a center-tap rectifier topology. and resistive loads. Power loss reduction in the range of 50%–69% A customized charge pump circuit is however needed in the has been achieved for the resistive load. proposal of [15] in order to provide a suitable dc power sup- Index Terms—Energy saving, mains-frequency synchronous ply for the gate drive. As such proposal aims at low-voltage rectifiers, self-driven synchronous rectifiers. applications, it is not suitable for high-voltage mains voltage operations. For a high-power and mains-frequency operation, I. INTRODUCTION a synchronous rectifier technique has been previously proposed [16]. It is based on the detection of the phase–phase voltage, and YNCHRONOUS rectifiers based on the use of power sophisticated logic and timing circuits are needed to provide S MOSFETs to replace the diodes in reducing the conduction the gating signals if the ac source has a significant source losses have been widely used in low-voltage high-current ap- inductance. However, the gating signals for the synchronous plications since 1990 [1]. Synchronous rectifier techniques are rectifiers based on voltage detection are not adequate because primarily applied to various versions of dc–dc converters such the diodes of a traditional bridge rectifier only turn off after as buck converters [2], [3], flyback and boost-buck converters their current reverse-recovery processes. [4], [5], half-bridge converters [6], [7], and LCC resonant It has been pointed out in [17] and [18] that it is more converters [8], [9]. To reduce the cost of the gate-drive circuits, appropriate to use at least one current-sensed gate drive in self-driven techniques have been an active research topic in each current loop of the synchronous rectifier for general power synchronous rectifiers [2], [7], [9], [10], although the gate con- applications unless there is an external circuit that will be trol integrated circuit for driving synchronous rectifiers is also used to cut off the current for the rectifier. In this paper, commercially available [11]. Other research aspects include the principle of ac–dc synchronous rectification based on the the use of the soft-switching technique [6], [9], [12]. Besides self-sensing and self-driven control circuit is generalized from single-phase systems to multiphase ones for both low- and high-voltage applications and for both low- and high-frequency Manuscript received May 6, 2010; revised August 24, 2010; accepted October 4, 2010. Date of publication November 9, 2010; date of current version operations. Power MOSFETs with either voltage or current July 13, 2011. This work was supported by the Center for Power Electronics, self-sensing and self-driven gate drives are used to replace City University of Hong Kong. the diodes in the rectifier circuits. New self-driven synchro- W. X. Zhong, W. P. Choi, and W. W. C. Ho are with the Center for Power Electronics, Department of Electronic Engineering, City University of Hong nous rectification (SDSR) circuits are designed to behave like Kong, Kowloon, Hong Kong. the traditional diode rectifiers, except that their conduction S. Y. Hui is with the Center for Power Electronics, Department of Elec- loss is much smaller than that of the diode rectifiers. This tronic Engineering, City University of Hong Kong, Kowloon, Hong Kong, and also with the Department of Electrical & Electronic Engineering, Im- principle is successfully and practically demonstrated in a perial College, SW7 2AZ London, U.K. (e-mail: [email protected]; three-phase synchronous rectifier for capacitive, inductive, and [email protected]). resistive loads, with the significant loss reduction exceeding Color versions of one or more of the figures in this paper are available online at http://ieeexplore.ieee.org. 50% when compared with a diode bridge at both 110 and Digital Object Identifier 10.1109/TIE.2010.2090835 220 V mains. Consequently, the thermal management and heat 0278-0046/$26.00 © 2010 IEEE 3288 IEEE TRANSACTIONS ON INDUSTRIAL ELECTRONICS, VOL. 58, NO. 8, AUGUST 2011 TABLE I LOGIC ASSIGNMENTS OF DIFFERENT CIRCUIT ELEMENTS CCSD gate drive is more complicated than the “self-sensing” VCSD gate drive, as shown in Fig. 1(b), it is proposed that one CCSD and one VCSD gate drive should be used in each current loop in the synchronous rectifier. In Fig. 1(b), a current- sensing resistor Rsen is used to provide the feedback signal for the CCSD gate drive. In principle, the ON-state resistance of the power MOSFET can be used as the current-sensing resistor if desired. A systematic way of generalizing an ac–dc SDSR system is shown as follows. Let X be a circuit component that can be one of the following: a diode (D), an inductor (L), a capacitor (C), a CCSD active switch (CCSD), and a VCSD active switch (VCSD). The location of the upper elements in a rectifier is defined by the subscript i of the circuit element symbol Xi.For the upper branch elements Xi i =1, 2,...,n. Fig. 1. (a) One conducting path via two diodes. (b) A conducting path via one For the lower branch elements Xj VCSD and one CCSD. j = n +1,n+2,...,2n sink requirements are reduced, and a more compact rectifier where n is the number of converter branches. For example, for can be achieved for general-purpose ac–dc applications. In a single-phase rectifier this paper, Section II outlines the generalized SDSR principle. The hardware implementation is illustrated in Section III using n =2. a three-phase SDSR as an example. The measurements on The numbers of the upper elements are one and two, and the the single- and three-phase SDSRs and their diode rectifier numbers of the lower elements are three and four, as shown in counterparts are included in Section IV. Finally, we conclude Fig. 1(a). in Section V. A logic value is assigned to each circuit element Xi or Xj (which can be an active switch, a diode, or other circuit II. GENERALIZED SDSR PRINCIPLE element), which is represented by A. Single-Phase Rectification System SXi,i=1, 2,...,n Starting with a single-phase diode rectifier, this section de- scribes the general principle behind the proposal. Fig. 1(a) SXj,j= n +1,n+2,...,2n. shows one conduction loop of a diode rectifier. As the input ac For the circuit element showing the capability of the resisting voltage reverses and the current starts to reverse, the diodes will instantaneous current change, a logic value of “1” is assigned. turn off after the current reverse recovery. This means that the Therefore, “1” is assigned to a CCSD active switch, a diode, power MOSFETs that replace the diodes in the SDSR should and an inductor. A VCSD active switch and a capacitor have no turn off when the sensed current begins to reverse. However, such capability of resisting the instantaneous current change. it should be noted that, as long as one MOSFET is turned Therefore, they have been assigned a logic value of “0.” Table I off, the current path is cut off. Therefore, the first principle shows the corresponding logic value for each circuit element. of this generalized method is that at least one of the power In a bridge rectifier, each current loop {X ,X } can be MOSFETs should have a “self-sensing” current-controlled self- i j identified by the branch location in the circuit, and an associated driven (CCSD) gate drive.
Details
-
File Typepdf
-
Upload Time-
-
Content LanguagesEnglish
-
Upload UserAnonymous/Not logged-in
-
File Pages12 Page
-
File Size-