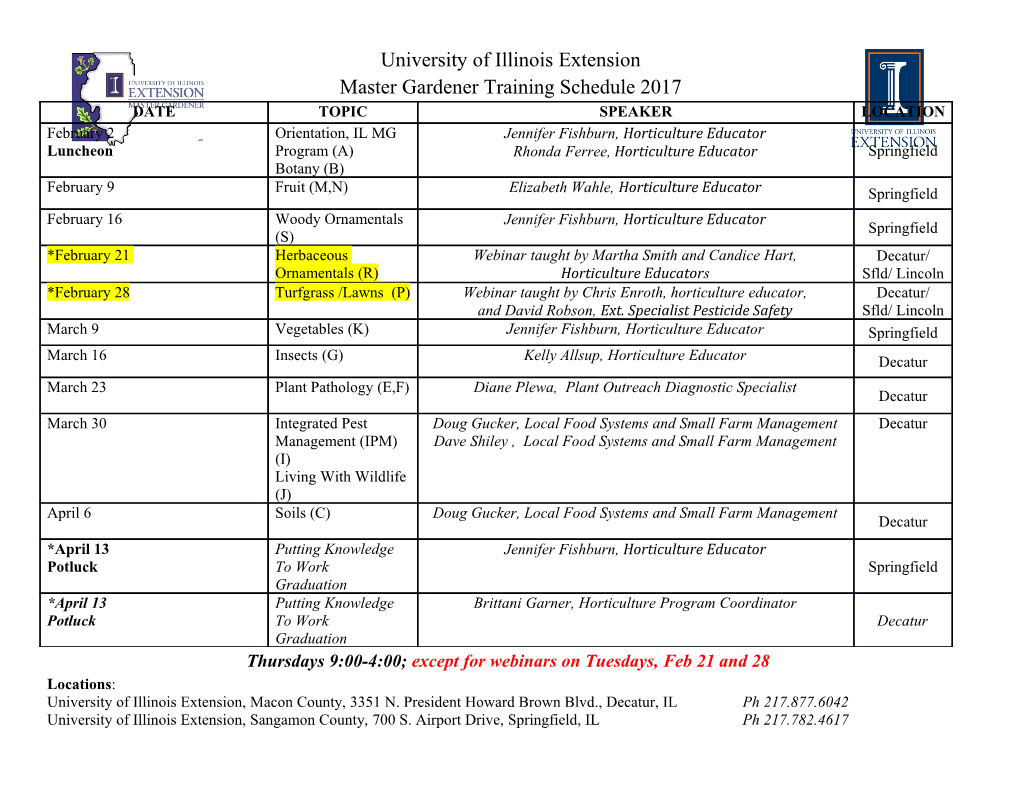
Silicon fabrication process pdf Continue The manufacturing process used to create integrated circuits This article needs additional quotes to verify. Please help improve this article by adding quotes to reliable sources. Non-sources of materials can be challenged and removed. Find sources: Semiconductor Manufacturing - JSTOR Newspaper News Books (September 2008) (Узнайте, как и когда удалить это сообщение шаблона) Масштабирование (узлы процесса) 010 мкм - 1971 006 мкм - 1974 003 мкм - 1977 1,5 мкм - 1981 0 1984 800 нм - 1987 600 нм - 1990 350 нм - 1993 250 нм - 1996 180 нм - 1999 130 нм - 2001 090 нм - 2003 0 65 нм - 2005 045 нм - 2007 032 нм - 2009 022 нм - 2012 014 нм - 2014 010 нм - 2016 007 нм - 2018 005 нм - 2020 Будущее 003 нм - 2022 002 нм - No 2023< Половина узлов Плотность CMOS Устройство (много ворот) Мур закон полупроводниковой промышленности Nanoelectronics vte НАСА Гленн исследовательский центр чистой комнате Внешнее изображение Фото интерьера чистой комнате 300mm fab в ведении TSMC полупроводникового устройства изготовления является процесс, используемый для производства полупроводниковых устройств , как правило , metal-oxide-semiconductor (MOS) devices used in integrated circuits (IC) chips that are present in everyday electrical and electronic devices. This is a multi-step sequence of stages of photolithographic and chemical processing (such as surface passivation, thermal oxidation, planar diffusion and compound insulation), during which electronic circuits are gradually created on a plate of pure semiconductor materials. Silicon is almost always used, but different semiconductor compounds are used for specialized applications. The entire manufacturing process, from the beginning to the packaged chips ready for shipment, takes six to eight weeks and is performed in highly specialized semiconductor plants, also called foundries or fabs. All the manufacture takes place in the clean rooms of these fabs. In more advanced semiconductor devices, such as modern 14/10/7 nm nodes, manufacturing can take up to 15 weeks, with an industry average of 11 to 13 weeks. Production at modern production facilities is fully automated and carried out in an airtightly sealed nitrogen environment to increase yields (the percentage of microchips that function properly in the plate), with automated materials processing systems taking care of transporting plates from machine to machine. transported inside FOUPs, special sealed plastic boxes. All machines and FOUPs contain an internal nitrogen atmosphere. The air inside the machine and FOUPs is usually kept cleaner than the surrounding air in a clean room. This internal atmosphere is known as a mini-environment. Manufacturing plants need a lot of liquid nitrogen to maintain the atmosphere inside the machines and FOUPs, which are constantly cleaned with nitrogen. The size of a particular semiconductor process has certain minimum size and interval rules for functions on each layer of the chip. Often, new semiconductor processes can simply reduce emissions to reduce costs and improve productivity. Early semiconductor processes had arbitrary names such as HMOS III, CHMOS V; later are called by size, for example, by 90 nm of process. By industry standard, each generation of the semiconductor manufacturing process, also known as the technology hub, is equipped with a minimum size of the process object. Technological nodes, also known as technological processes or simply nodes, are usually indicated by the size of nanometers (or historically micrometers) of the length of the transistor gate process. History See also: List of examples of the semiconductor scale, Moore's Law, the integrated MOS scheme, the semiconductor industry and the density of the 20th century transistor First transistors for field effects of oxide metal (MOSFETs) were manufactured by Egyptian engineer Mohamed M. Atallah and Korean engineer Douon Kang at Bell Labs between 1959 and 1960. Initially, there were two types of MOSFET technologies: PMOS (p-type MOS) and NMOS (n-type MOS). Both types were developed by Atalla and Kahng when they originally invented MOSFET, making both PMOS and NMOS devices on 20 microns and 10 microns scales. An improved type of MOSFET technology, CMOS, was developed by Chi-Tan Saha and Frank Wanlass at Fairchild Semiconductor in 1963. CMOS was commercialized by RCA in the late 1960s. Semiconductor manufacturing has since spread from Texas and California in the 1960s to the rest of the world, including Asia, Europe and the Middle East. The 21st century semiconductor industry is a global business today. Leading semiconductor manufacturers tend to have facilities around the world. Samsung Electronics, the world's largest semiconductor manufacturer, has facilities in Korea and the United States. Intel, the second largest manufacturer, has facilities in Europe and Asia as well as in the United States. TSMC, the world's largest clean foundry, has facilities in Taiwan, China, Singapore and the United States. Kvalcomm and Broadcom are among the largest semiconductor companies that outsource their production to companies such as TSMC. They also have objects scattered in different countries. Since 2009, the node has become a commercial name for marketing purposes, indicating a new generation of process technology, with no relation to the length of the gate, metal step or gate step. For example, the 7 nm GlobalFoundries process is similar to Intel's 10 nm thus, the usual notion of a process node has become blurred. In addition, the processes of the TSMC and Samsung 10 nm are only slightly denser than Intel's 14 nm in transistor density. They are actually much closer to The Intel 14 nm process than they are to Intel's 10 nm process (like Samsung's 10 nm fin step processes just like that of Intel's 14 nm process: 42 nm). As of 2019, 14 nanometer and 10 nanometer chips are in mass production by Intel, UMC, TSMC, Samsung, Micron, SK Hynix, Toshiba Memory and GlobalFoundries, with 7 nanometer processors in the mass production of TSMC and Samsung, although their definition of a 7 nanometer node is similar to the 10-nanometer intel process. The 5 nanometer process began in Samsung in 2018. By 2019, the highest-density transistor is the 5 nanometer N5 TSMC with a density of 171.3 million transistors per square millimeter. In 2019, Samsung and TSMC announced plans to produce 3 nanometer nodes. GlobalFoundries decided to stop the development of new nodes beyond the 12 nanometers to save resources, as it determined that the creation of a new phacto to handle sub-12nm orders would be beyond the financial capacity of the company. According to the 2019 version, Samsung is a leader in advanced semiconductor scaling, followed by TSMC and then Intel. A list of steps is a list of processing methods that are used many times throughout the construction of a modern electronic device; this list does not necessarily imply a specific order. The equipment for these processes is manufactured by a handful of companies. All equipment must be tested before the semiconductor plant starts. Waffle wet treatment cleans cleaning with solvents such as acetone, trichloroethylene and ultra-clean water Piranha solution RCA pure surface of the passivation Photolithography Ion implantation (in which dopants are built into the plates creating regions of increased or reduced conductivity) Dry etching of the reactive-ion etching of the atomic etching (ALE) Moist etching plasma ash Thermal Processing Fast Thermal Annal furnace annals thermal oxidation chemical vapor deposition (CVD) Atomic deposition layer (ALD) Physical deposition of steam (PVD) Molecular radiant epitaxy (MBE) Laser lift (for LED production) Electrochemical deposition (ECD). See Electroplastic-Mechanical Polishing (CMP) waffle testing (where electrical performance is tested using automatic testing equipment, laser pruning can also be carried out at this stage) Die training through silicon through production (for three-dimensional integrated circuits) waffle mounting (waffle installation mounted on a metal frame using Dicing tape) backgrinding and polishing (for three-dimensional integrated circuits) plates for thin devices such as smart card or PCMCIA cards or communication plates styling, it can also occur during the dicing plate, in a process known as Bone Before Grind or DBG (27) Communication and Styling (for 3D Integrated Circuits and MEMS) Redistribution of The Production Layer (for WLCSP Packages) Bumping (for Flip Chip BGA, and WLCSP packages) Die cutting or waffle dicing IC packaging attachment Die (die attached to lead frame by conductive paste or die : Wire Communication, Thermosonic Communications, Flip Chip or Tape Automated Communication (TAB) IC encapsulation of molding (using special molding compounds) baking electroplay (a copper plate leads lead shots with tin, to make solder easier) Laser markings or silkscreen printing trim and shapes (separates lead frames from each other, and bends lead frame, and comparisons of the size of the semiconductor manufacturing nodes with some microscopic objects and visible light wavelengths. than about 10 micrometers, the purity of semiconductors was not as big a problem as today's in the manufacture of devices. As the devices become more integrated, cleanrooms should become even cleaner. Today, manufacturers are pushed with filtered air to remove even the smallest particles, which could come to rest on waffles and contribute to defects. Workers at a semiconductor plant are required to wear clean suits to protect devices from
Details
-
File Typepdf
-
Upload Time-
-
Content LanguagesEnglish
-
Upload UserAnonymous/Not logged-in
-
File Pages3 Page
-
File Size-