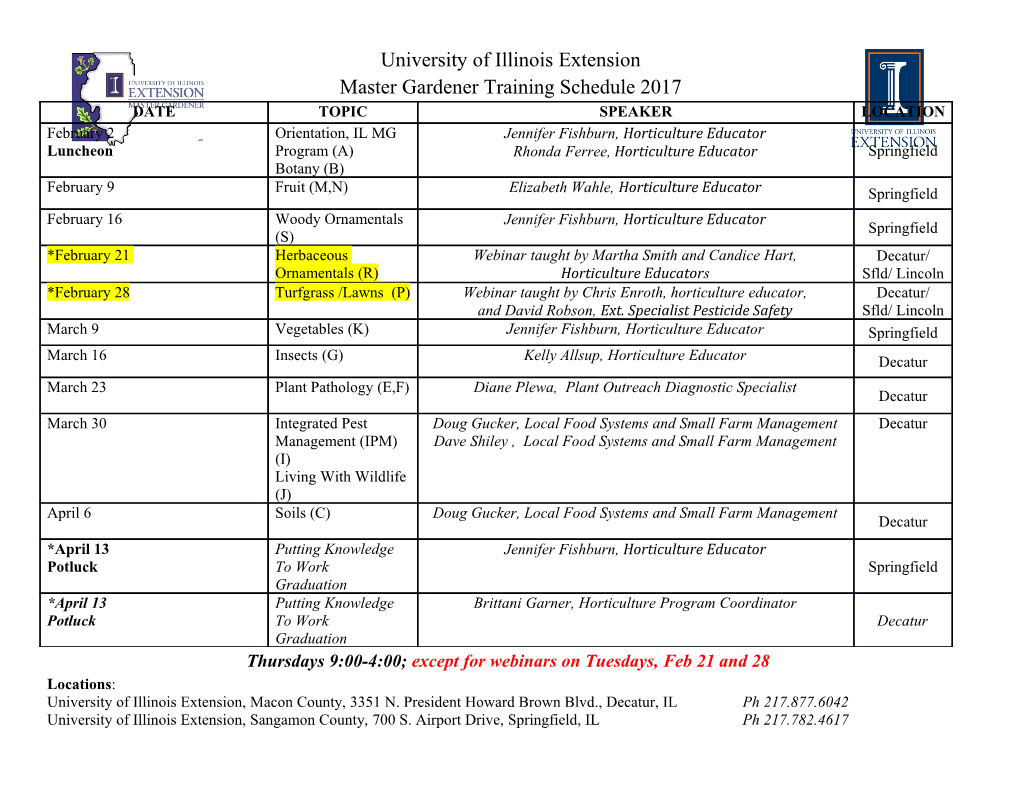
DOT HS 811 233 November 2009 Heavy Truck ESC Effectiveness Study Using NADS Final Report This document is available to the public from the National Technical Information Service, Springfield, Virginia 22161 This publication is distributed by the U.S. Department of Transportation, National Highway Traffic Safety Administration, in the interest of information exchange. The opinions, findings and conclusions expressed in this publication are those of the author(s) and not necessarily those of the Department of Transportation or the National Highway Traffic Safety Administration. The United States Government assumes no liability for its content or use thereof. If trade or manufacturers’ names or products are mentioned, it is because they are considered essential to the object of the publication and should not be construed as an endorsement. The United States Government does not endorse products or manufacturers. Technical Report Documentation Page 1. Report No. 2. Government Accession No. 3. Recipient’s Catalog No. DOT HS 811 233 4. Title and Subtitle 5. Report Date Heavy Truck ESC Effectiveness Study Using NADS November 2009 6. Performing Organization Code 7. Author(s) 8. Performing Organization Report No. Brown, T., Schwarz, C., Moeckli, J., & Marshall, D. N08-005 9. Performing Organization Name and Address 10. Work Unit no. (TRAIS National Advanced Driving Simulator The University of Iowa 11. Contract or Grant No. 2401 Oakdale Blvd. DTNH22-06-06-D-00043, Iowa City, IA 52242-5003 Task Order 1 12. Sponsoring Agency Name and Address 13. Type of Report and Period Covered U.S. Department of Transportation Final Report National Highway Traffic Safety Administration February 2007-August Office of Applied Vehicle Safety Research 2008 1200 New Jersey Avenue, S.E. 14. Sponsoring Agency Code Washington, D.C. 20590 NVS-322 15. Supplementary Notes Task Order Manager: Alrik L. Svenson Contracting Officer’s Technical Representative (COTR): Stephanie Binder This study was conducted by researchers at the National Advanced Driving Simulator (NADS) at the University of Iowa. The primary objective of this research project was to assess the effectiveness of tractor electronic stability control systems on heavy trucks in terms of reducing the incidences of rollovers and jackknifes. This study was completed using the NADS-1, a high-fidelity full motion simulator instrumented with a functioning 1999 Freightliner Century Class cab with an Eaton Fuller 9-speed transmission. A hardware-in-the-loop (HIL) solution was developed in partnership with Meritor WABCO to integrate commercial stability control systems into the simulation environment. The experiment is a split plot; the between-subjects independent variable is ESC Condition. Five study drives were completed by each participant; these drives were divided into two distinct groups: those designed to induce the potential for a rollover utilizing a high coefficient of friction roadway, and those designed to induce the potential for a jackknife using a low coefficient of friction roadway. Overall, potential benefits were found for both the RSC and the RSC+YSC systems under differing conditions for helping drivers maintain vehicle control. It was observed that the performance of both systems was highly dependent on driver’s speed. RSC showed strong reductions of rollovers in geometry-based situations such as tight curves and exit ramps. Additionally, drivers with the RSC+YSC system were six times more likely to avoid a jackknife than were drivers without a system when encountering similar conditions at event onset. 17. Key Words 18. Distribution Statement ESC, RSC, s tability control, heavy truck, safety benefit, roll This report is available at stability, yaw stability www.nhtsa.gov 19. Security Classification (of this report) 20. Security Classification (of this page) 21. No. of Pages 22. Price Unclassified Unclassified 208 i SI* (MODERN METRIC) CONVERSION FACTORS APPROXIMATE CONVERSIONS TO SI UNITS Symbol When You Know Multiply By To Find Symbol LENGTH in inches 25.4 millimeters mm ft feet 0.305 meters m yd yards 0.914 meters m mi miles 1.61 kilometers km AREA in2 square inches 645.2 square millimeters mm 2 ft2 square feet 0.093 square meters m 2 yd2 square yard 0.836 square meters m 2 ac acres 0.405 hectares ha mi2 square miles 2.59 square kilometers km2 VOLUME fl oz fluid ounces 29.57 milliliters mL gal gallons 3.785 liters L ft3 cubic feet 0.028 cubic meters m 3 yd3 cubic yards 0.765 cubic meters m 3 NOTE: volumes greater than 1000 L shall be shown in m3 MASS oz ounces 28.35 grams g lb pounds 0.454 kilograms kg T short tons (2000 lb) 0.907 megagrams (or "metric ton") Mg (or "t") TEMPERATURE (exact degrees) oF Fahrenheit 5 (F-32)/9 Celsius oC or (F-32)/1.8 ILLUMINATION fc foot-candles 10.76 lux lx fl foot-Lamberts 3.426 candela/m2 cd/m2 FORCE and PRESSURE or STRESS lbf poundforce 4.45 newtons N lbf/in2 poundforce per square inch 6.89 kilopascals kPa APPROXIMATE CONVERSIONS FROM SI UNITS Symbol When You Know Multiply By To Find Symbol LENGTH mm millimeters 0.039 inches in m meters 3.28 feet ft m meters 1.09 yards yd km kilometers 0.621 miles mi AREA mm 2 square millimeters 0.0016 square inches in2 m2 square meters 10.764 square feet ft2 m2 square meters 1.195 square yards yd2 ha hectares 2.47 acres ac km2 square kilometers 0.386 square miles mi2 VOLUME mL milliliters 0.034 fluid ounces fl oz L liters 0.264 gallons gal m3 cubic meters 35.314 cubic feet ft3 m3 cubic meters 1.307 cubic yards yd3 MASS g grams 0.035 ounces oz kg kilograms 2.202 pounds lb Mg (or "t") megagrams (or "metric ton") 1.103 short tons (2000 lb) T TEMPERATURE (exact degrees) oC Celsius 1.8C+32 Fahrenheit oF ILLUMINATION lx lux 0.0929 foot-candles fc cd/m2 candela/m2 0.2919 foot-Lamberts fl FORCE and PRESSURE or STRESS N newtons 0.225 poundforce lbf kPa kilopascals 0.145 poundforce per square inch lbf/in2 *SI is the symbol for the International System of Units. Appropriate rounding should be made to comply with Section 4 of ASTM E380. (Revised March 2003) ii EXECUTIVE SUMMARY Heavy trucks have long been the dominant mode of freight transport in North America, carrying an estimated 62 percent of the total value of freight in 2006 and accounting for most of the growth in the values of North American freight between 1996 and 2006. While the number of trucks involved in fatal crashes has decreased over the past twenty years and the number of heavy trucks involved in injury crashes has decreased over the past ten years, the numbers are still high, and the unique characteristics of heavy trucks make them particularly susceptible to single-vehicle crashes due to rollover and jackknife. Research examining electronic stability control systems on passenger vehicles and light trucks and vans suggests a dramatic reduction in the number of certain crashes caused by jackknife and rollover, but little research has been published on the potential safety benefits of electronic stability systems for heavy trucks. The primary objective of this research project was to assess the effectiveness of tractor electronic stability control systems on heavy trucks in terms of reducing the incidences of rollovers and jackknifes. This study was completed using the NADS-1, a high-fidelity full motion simulator instrumented with a functioning 1999 Freightliner Century Class cab with an Eaton Fuller 9­ speed transmission. A hardware-in-the-loop (HIL) solution was developed in partnership with Meritor WABCO to integrate commercial stability control systems into the simulation environment. The experiment is a split plot; the between-subjects independent variable is ESC Condition. Five study drives were completed by each participant; these drives were divided into two distinct groups: those designed to induce the potential for a rollover utilizing a high coefficient of friction roadway, and those designed to induce the potential for a jackknife using a low coefficient of friction roadway. Overall, potential benefits were found for both the RSC and the RSC+YSC systems under differing conditions for helping drivers maintain vehicle control. It was observed that the performance of both systems was highly dependent on driver’s speed. RSC showed strong reductions of rollovers in geometry-based situations such as tight curves and exit ramps. Additionally, drivers with the RSC+YSC system were six times more likely to avoid a jackknife than were drivers without a system when encountering similar conditions at event onset. The performance of the RSC+YSC in preventing rollovers was more mixed due in large part to the higher velocities present in those events for drivers in this study using this system. There was also an unexpected benefit for RSC in reducing jackknifes on the ramp, although the severity of jackknifes, when they occurred, was greater. It was also determined that speed during the event was a significant factor in predicting rollovers and jackknifes regardless of the presence or absence of a system. In general, the presence of a stability control system allowed the drivers to successfully negotiate the events at higher speeds than they would have been able to without. The RSC system proved to be more effective than the RSC+YSC system on the curve events, even on snow-covered roads due to greater reductions in speed. However, when a jackknife did occur, the yaw control applied by the RSC+YSC system was far more effective at keeping the tractor-trailer on or near the road during emergency maneuvers. It appeared that the systems were most effective at providing beneficial interventions in the scenarios that were based on road geometry (curve, dry exit, snow exit).
Details
-
File Typepdf
-
Upload Time-
-
Content LanguagesEnglish
-
Upload UserAnonymous/Not logged-in
-
File Pages208 Page
-
File Size-