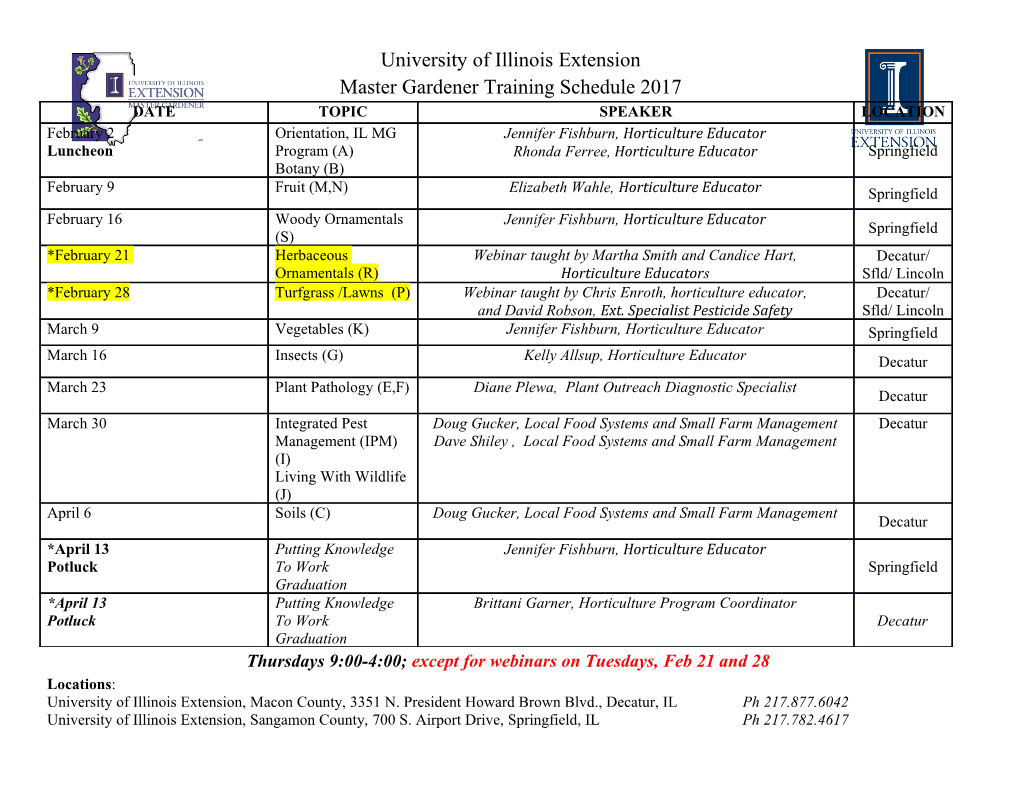
CRANFIELD UNIVERSITY LASZLO HETEY IDEALISATION ERROR CONTROL FOR AEROSPACE VIRTUAL STRUCTURAL TESTING SCHOOL OF ENGINEERING PhD THESIS CRANFIELD UNIVERSITY SCHOOL OF ENGINEERING PHD THESIS Academic Year 2008 - 2009 LASZLO HETEY IDEALISATION ERROR CONTROL FOR AEROSPACE VIRTUAL STRUCTURAL TESTING Supervisor: Dr. James Campbell March 2009 © Cranfield University 2009. All rights reserved. No part of this publication may be reproduced without the written permission of the copyright owner. ABSTRACT This thesis addresses idealisation error control for the nonlinear finite element method. The focus is on accurate failure prediction of mid-size aerospace structures. The objective is the development of technologies that shorten the certification process of new airplanes, by replacing expensive and time consuming testing with reliable calculation methods. The SAFESA (Safe Structural Analysis) approach was applied to the collapse analyses of stiffened metal panels. ABAQUS/Standard was thereby the utilised nonlinear solver. Because the original SAFESA procedure is tailored for linear analyses, the methodology needed an update. The first analysis case is a stiffened panel compression test which was arranged as a lecture demonstration at Cranfield University. The analysis behaviour is highly nonlinear due to the thin-walled properties of the panel. The second analysis investigates an Airbus compression panel. Until failure, the panel behaves geometrically less complicated because the major load bearing parts are thick-walled and bend smoothly. The main research work is the critical analysis of important modelling assumptions concerning the used material model, boundary conditions and geometrical imperfections. In both cases, the method helped to identify idealisation errors and to build a reliable FEM model. In order to deal with the nonlinear error sources, minor extensions to the original method had to be made. The major achievement is the development of the first expert system which applies the idealisation error control methodology. CAD data import, geometry visualization, a knowledge-based decision making advisor and audit trail functionality were implemented. The expert system leads the user through a step-by-step idealisation process. Each decision is documented and a confidence level must be supplied. This way, every uncertainty is flagged out as potential error source. An interactive interface was created, which provides the user with expert advice on how to treat the idealisation errors. The software has been validated and shown to meet the program objectives. i ACKNOWLEDGEMENTS I would like to thank my supervisor Dr. James Campbell for his guidance and assistance throughout this PhD program. Thanks to Prof. Rade Vignjevic for his advice during the research. Your comments helped me to progress and to focus on the important aspects of the project. I am grateful to the MUSCA project for the sponsoring and to Cranfield University for providing the working environment. Many thanks to Airbus UK for supplying the panel test data and Morten Ostergaard, John Smyth and Nigel Pready of Airbus UK for their help. I had the pleasure of being part of Cranfield University and cooperating with great researchers and helpful staff. My infinite thanks goes to Jason Brown for our late-night “special purpose” chats. He shared many secrets about mechanical engineering and how to take it easy in general. Thanks to Dr. Kevin Hughes for various kinds of support, Dr. Les Oswald for the grid computing support, Dr. Helen Lockett for explaining some ideas of her PhD thesis to me, Berry Walker for help with the panel tests, scanning and the test machine calibration and Marion Bastable for being the best secretary around. During this research I discussed results and problems with some brilliant researchers. Thank you, Prof. Alan Morris, Prof. Alan Rothwell, Prof. Jens Lang, Dr. Adrian Murphy, Dr. Matthias Heitmann, Dirk Schumann, Philipp Römelt, Christian Sandor and the QtOpenCascade team. In the last weeks of completing this thesis, several reviewers helped me with their comments on parts of the thesis. Thank you, Henrik Rudolf, Antoine Godbille, Ryszard Maciol, Andrea Calonghi and Caroline Bacle. Special thanks to Katrin Milde for proof reading this thesis. I had the pleasure of sharing an office with other PhD students of the Crashworthiness group. Thank you, Juan Reveles, Ravindran Sundararajah and Seimon Powell for helpful discussions and collective breaks. Finally, thanks to all open-source programmers for sharing their knowledge. Most importantly, I thank my girlfriend Barbara for her support and love. I would also like to thank my parents and family for providing moral support and simply letting me have a good time whenever I took a break at home. Thanks to all the people I met and enjoyed time during my three years on campus. Thank you Toni, Florian, Jenny, Philipp, Javier, Lucia, Andrea, Holger, Zhengjie, Chichi, Slavisa, Aurelie, Francesco, Oleg, Christian, Edmon, Beck, Daxon, Liyun, Stratos, Shuguang, Susan, Leonardo, Bonolo, Zsombor, Zsofia, Richard, Barnabas, Beata, Ryszard, Nicolai and my friends from the badminton club. ii CONTENTS 1. INTRODUCTION -------------------------------------------------------------------------1 1.1 MOTIVATION FOR THIS RESEARCH ..........................................................1 1.2 MUSCA PROJECT .................................................................................2 1.3 STATEMENT OF OBJECTIVES ..................................................................3 1.4 METHODOLOGY ......................................................................................4 1.5 LITERATURE REVIEW ..............................................................................5 1.6 THESIS STRUCTURE ...............................................................................9 2. NONLINEAR FEM AND SAFESA-------------------------------------------------- 10 2.1 FINITE ELEMENT METHOD ......................................................................10 2.1.1 Elliptic partial differential equations .................................................................. 10 2.1.2 Displacement-stress-strain relations ................................................................ 11 2.1.3 Principle of virtual displacement....................................................................... 12 2.1.4 Solution procedure ........................................................................................... 14 2.2 NONLINEAR FEM...................................................................................16 2.2.1 Sources of nonlinearity..................................................................................... 16 2.2.2 Newton-Raphson method................................................................................. 17 2.2.3 Modified Newton-Raphson method .................................................................. 19 2.2.4 Modified Newton-Raphson method with damping ............................................ 20 2.3 SAFESA ..............................................................................................22 2.3.1 Location in the FEM procedure ........................................................................ 22 2.3.2 SAFESA analysis steps.................................................................................... 24 2.3.3 Error sources and treatment............................................................................. 26 2.4 NONLINEAR FEM SOFTWARE .................................................................28 2.4.1 Pre-processors................................................................................................. 28 2.4.2 Nonlinear solvers.............................................................................................. 28 2.4.3 ABAQUS solution procedure............................................................................ 30 2.4.4 Shell elements.................................................................................................. 30 2.4.5 Material modelling ............................................................................................ 32 2.4.6 Joint modelling ................................................................................................. 35 2.4.7 Contact definition.............................................................................................. 37 2.4.8 Geometrical nonlinearity................................................................................... 39 3. CRANFIELD PANEL ANALYSIS--------------------------------------------------- 41 iii 3.1 INTRODUCTION ......................................................................................41 3.2 DESIGN CALCULATIONS ..........................................................................41 3.3 SAFESA PROCEDURE ...........................................................................42 3.4 SUPPORTING TEST DATA ........................................................................50 3.4.1 Geometry scan................................................................................................. 50 3.4.2 Material properties............................................................................................ 51 3.4.3 Joint deformation.............................................................................................. 51 3.4.4 Test machine calibration .................................................................................. 52 3.5 REFERENCE MODEL BUILDING ................................................................53
Details
-
File Typepdf
-
Upload Time-
-
Content LanguagesEnglish
-
Upload UserAnonymous/Not logged-in
-
File Pages204 Page
-
File Size-