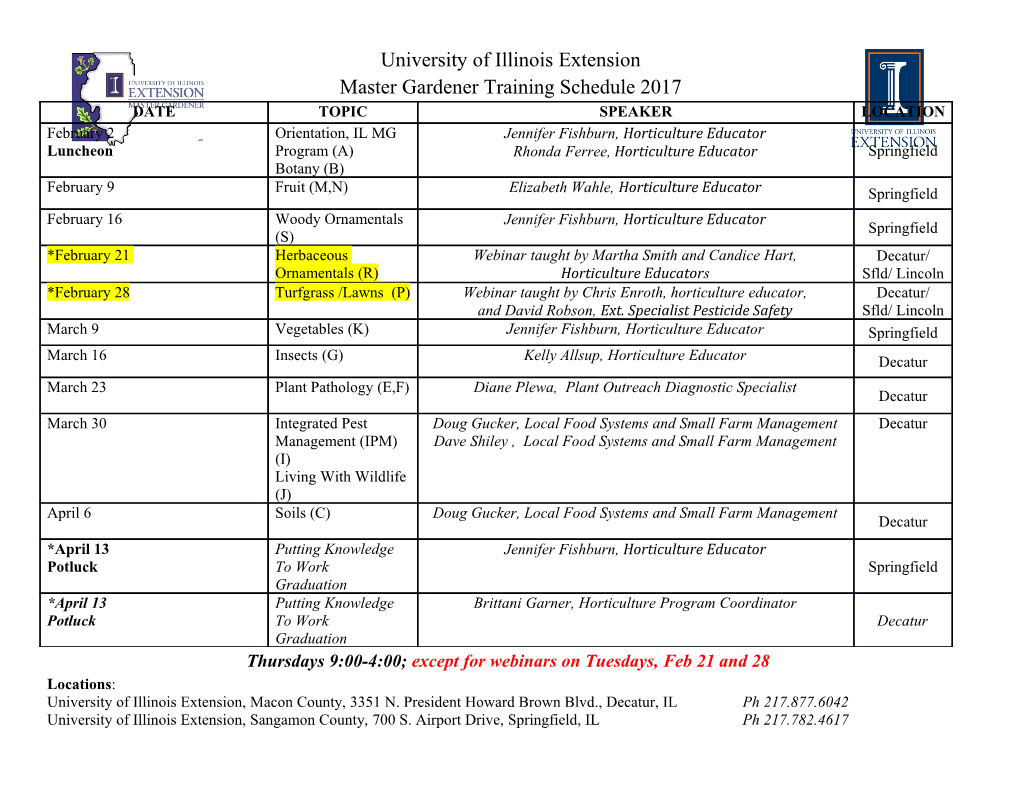
University of Wollongong Research Online University of Wollongong Thesis Collection University of Wollongong Thesis Collections 1997 A metallurgical investigation of the bath smelting of composite organic and ferrous wastes Stuart John Street University of Wollongong Recommended Citation Street, Stuart John, A metallurgical investigation of the bath smelting of composite organic and ferrous wastes, Doctor of Philosophy thesis, Department of Materials Engineering, University of Wollongong, 1997. http://ro.uow.edu.au/theses/1479 Research Online is the open access institutional repository for the University of Wollongong. For further information contact Manager Repository Services: [email protected]. A Metallurgical Investigation of the Bath Smelting of Composite Organic and Ferrous Wastes A thesis submitted in fulfilment of the requirements for the award of the degree Doctor of Philosophy from University of Wollongong by Stuart John Street, B.E (Hons), M.E (Hons) Department of Materials Engineering 1997 Candidates Certificate This is to certify that the work presented in this thesis was carried out by the candidate in the Department of Materials Engineering, University of Wollongong, and has not been submitted to any other university or institution for a higher degree. Stuart Street "I may not care but that doesn't mean I don't understand." - Homer.J.Simpson "The Simpsons" Acknowledgements It has been said that: "Sometimes a scream is better than a thesis" - Ralph Waldo Emerson (1803-1882) to all those that heard me scream, thanks. Abstract Bath smelting has recently been the focus of several large research and development programs investigating alternative ironmaking processes. Fundamental studies have contributed to the understanding of smelting- reduction processes however these have not been entirely applicable to the smelting of composite pellets. Recently, bath smelting has also been evaluated for its potential for processing metallurgical wastes, the driving force being to develop suitable alternatives to traditional disposal methods such as dumping in landfills; one such technology is the EnvlRONment process. In general, many pyrometallurgical waste processes have been developed but few have been commercialised successfully. It is evident many processes have suffered economically because of poor understanding and control of process fundamentals. Although the EnvlRONment process, which smelts composite organic and ferrous waste pellets in a single vessel reactor, had been developed to the pilot plant stage, the mechanisms of smelting-reduction were not fully understood. Pilot plant trials highlighted critical aspects of the process but did not provide sufficient information to quantify process fundamentals, clearly further investigation was warranted. Smelting, Xray, and thermogravimetric experiments provided foundation for an in-depth study of reaction kinetics and mechanisms, while also allowing other relevant issues of waste processing, using bath smelting technology, to be addressed. Supporting the experimental investigations an extensive heat transfer model was developed which was used to predict temperature profiles and smelting times. The bath smelting reactor was modelled in 2 distinct stages, a falling gas region and an in-slag smelting region, heating was determined to be controlled by internal resistance. The general smelting behaviour of composite pellets was observed during pilot plant and laboratory trials. Smelting of composite pellets, as performed in the EnvlRONment process, was simulated in the laboratory by smelting composite pellets in crucibles containing slag at 1500°C; to allow for accurate experimental interpretation, and to increase the degree of experimental control, process pellets were replicated by surrogate laboratory pellets with a simplified number of components. Cellulose was trialled as a surrogate component for organic waste. Further experiments were performed using Xray fluoroscopy and radiography techniques to observe the progress of the smelting-reduction reactions in slag at 1500°C. Examination of the smelting reaction with the Xray techniques also allowed observation of the effect of composite smelting on slag foaming. The kinetics and mechanisms of reduction of composite pellets was investigated using non-isothermal thermogravimetric techniques to 1200°C. Thermal analysis via this route was selected because the experimental techniques are the most suited means to investigate temperature dependant phenomena of self-reducing systems. Smelting experiments provided significant fundamental information relevant to an understanding of smelting reactions in composite smelting. Analysis and interpretation of the experiments corroborated with the heat transfer model predictions, which was used together with the thermogravimetric results to clearly identify reaction mechanisms and explain other process phenomena. Key process reactions in composite smelting were identified as: - thermal decomposition of volatiles - direct reduction and carburisation of iron - pellet ablation through melting and dissolution - reduction of dissolved oxides in slag. Predicted temperature profiles within the composite pellets suggest that much of the volatile matter is lost during the falling gas region by thermal decomposition. For the surrogate pellets containing cellulose upto 78% of the volatile matter is lost during the falling gas region. The heat transfer model predicted sensible melting times, for a 1.5cm diameter pellet a melting time of 92s was predicted, similar times were observed in smelting trials. An important finding of the heat transfer work was that although the in-slag smelting stage was based on a fully submerged object experimental observations show that an immersion crust does not form on the pellet during its initial contact with the slag bath, and that the composite pellet is not submerged during smelting. Thermogravimetry revealed the complexity of internal reduction in iron oxide- carbon systems when high and low volatility carbon sources contribute towards reduction. The contribution to reduction from the high volatility carbon being influenced by heating rate and the presence of secondary non-volatile material, measured charring levels for cellulose varied between 13 and 22%. The main steps in the thermogravimetric reaction profiles were attributed to thermal decomposition of cellulose between 280 and 320°C and stepwise reduction of hematite above 550°C. The dominant reduction mechanism in composite bath smelting was identified as internal reduction within the pellet. Approximately 90% of the total reduction occurs within the pellet, the extent of which is sufficient that much of the iron is also carburised before pellet ablation is complete. The other significant finding of the study was that slag foaming was shown not to be a critical issue for process control of composite smelting. CONTENTS Acknowledgements iv Abstract v Table of Contents viii CHAPTER 1 INTRODUCTION 1 CHAPTER 2 STEELWORKS DUST 6 2.1 Introduction. 6 2.2 Origin of Steelworks Dust. 7 2.3 Dust Characterisation. 12 2.4 Considerations for Recycling and Disposal of Steelworks Dust. 36 2.5 Dust Treatment Technology. 42 2.5.1 Encapsulation. 43 2.5.2 Pyrometallurgical Processes. 48 2.5.3 Hydrometallurgical Processes. 79 2.5.4 Miscellaneous. 83 2.5.5 Summary of Dust Treatment Technologies. 88 CHAPTER 3 BATH SMELTING OF IRON 93 3.1 Introduction. 93 3.2 Thermodynamics of Smelting. 95 3.2.1 Reduction of Oxides. 95 3.2.2 Reduction of Iron Oxides. 103 3.3 Bath Smelting Reactions. 111 3.3.1 Dissolution of Pellets in Bath Smelting. 111 3.3.2 Function of the Slag Layer. 129 3.3.3 Slag Foaming. 132 3.3.4 Reduction of Iron. 147 3.3.5 Function of Carbonaceous Material in Bath Smelting. 168 3.3.6 Post Combustion. 177 3.4 Bath Smelting Processes. 188 3.4.1 Corex Process. 193 3.4.2 DIOS Process. 197 3.4.3 AISI Process. 200 3.4.4 Hlsmelt Process. 201 3.4.5 LRP/Romelt Process. 205 3.4.6 Miscellaneous Processes. 207 CHAPTER 4 PILOT PLANT TRIAL OF THE BATH SMELTING OF COMPOSITE WASTE PELLETS 213 4.1 Introduction. 213 4.2 EnvlRONment Process History 213 4.3 Process Description. 217 4.4 EnvlRONment Process Thermodynamics. 228 4.5 EnvlRONment Process Commercialisation. 230 4.6 100kg DC Arc Furnace Pilot Plant Smelting Trial. 231 4.6.1 Trial Description 233 4.6.2 Carbon Balance 235 4.6.3 Discussion of the Pilot Plant Trial 237 4.6.5 Conclusion 243 CHAPTER 5 Reactor Stoichiometry and Enthalpy Balance Equations 245 5.1 Introduction 245 5.2 Model Development 245 5.3 Discussion 251 5.4 Conclusion 253 CHAPTER 6 HEAT TRANSFER CONSIDERATIONS 254 6.1 Introduction. 254 6.2 Model Formulation. 269 6.2.1 Modes of Heat Transfer in the EnvlRONment Process. 269 6.2.2 Heat Flow. 270 6.2.3 Heat Transfer Formulation. 272 6.2.3.1 Falling Gas Region. 272 6.2.3.2 In-Slag Smelting Region. 287 6.3 Discussion. 295 6.4 Conclusion. 325 CHAPTER 7 ENVIRONMENT PROCESS COMPOSITE PELLET CHARACTERISATION. 328 7.1 Introduction. 328 7.2 Characterisation Techniques. 329 7.3 Results and Discussion. 330 7.4 Conclusions. 337 CHAPTER 8 EXPERIMENTAL 346 8.1 Introduction. 346 8.2 Smelting Experiments. 347 8.2.1 Apparatus. 347 8.2.2 Materials. 349 8.2.3 Experimental Procedure. 351 8.3 Xray Fluoroscopy and Radiography Experiments. 362 8.3.1 Apparatus. 362 8.3.2 Materials. 365 8.3.3 Experimental Procedure. 365 8.4 Thermogravimetric Experiments. 368 8.4.1 Apparatus. 368 8.4.2 Materials. 377 8.4.3 Experimental Procedure. 377 CHAPTER 9 RESULTS 382 9.1 Smelting Experiments. 382 9.1.1 Introduction.
Details
-
File Typepdf
-
Upload Time-
-
Content LanguagesEnglish
-
Upload UserAnonymous/Not logged-in
-
File Pages564 Page
-
File Size-