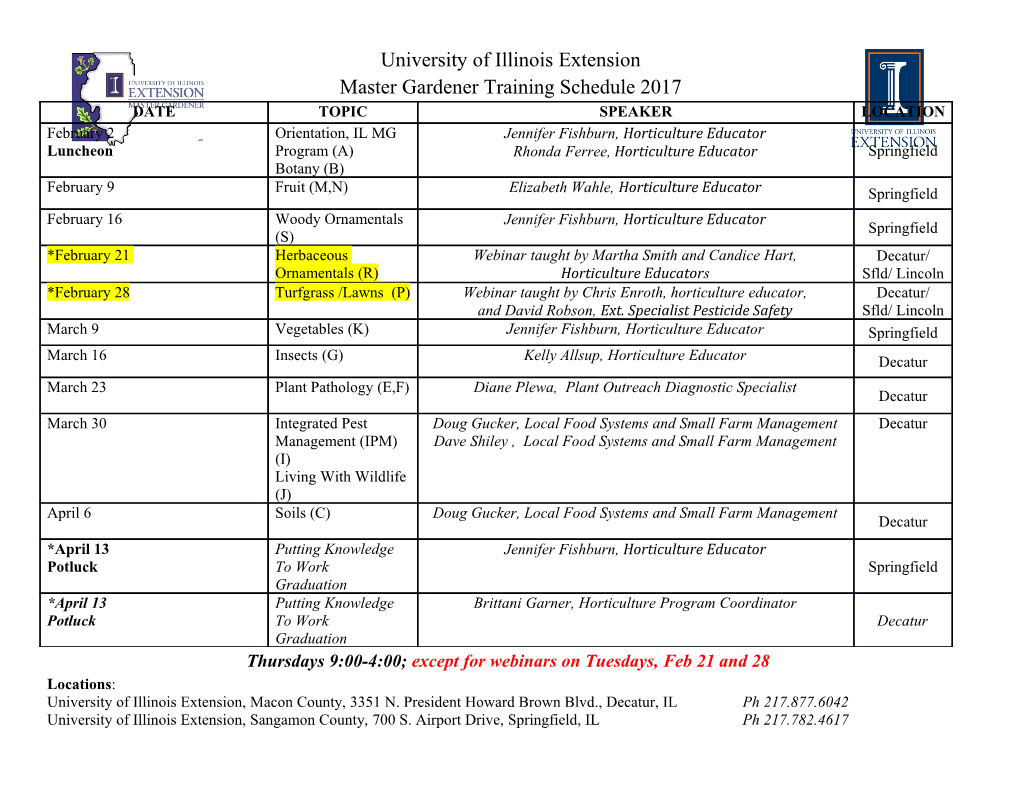
RESTRICTED A.P. 3302, PART 1 SECTION 19 CHAPTER 2 SERVOMECHANISMS ParaRraph Introduction 1 Speed Control of a D.C. Motor 6 Action of Human Operator 8 An Improved Method of Speed Control 9 Position Control Systems 14 Behaviour of a Simple Servomechanism 18 Response and Stability of Servomechanisms 20 Viscous Damping 23 Velocity Feedback Damping 26 Velocity Lag 32 Error-rate Damping 35 LJ,e of Stabilizing Networks 39 Transient Velocity Dam ping 42 Integral of Error Compensation 44 Summary of Stabilization Methods 48 Power Requirements of a Servomechanism 49 Components in a Servomechanism 52 Summary .. 55 A.L. 18 (Mar. 62) RESTRICTED RESTRICTED PART 1, SECTION 19, CHAPTER 2 SERVOMECHANISMS Introduction Only an elementary outline of the basic 1. The discovery that heat (from coal or principles involved and a general idea of oil) can be converted into mechanical energy the purpose and applications of control brought about the industrial revolution systems can be attempted in this chapter. and machines which could use this energy t~ Further information is given in Part 3 of produce useful results were quickly invented these notes. and improved. By controlling such machines, man was able to release large quantities 4. Chapter 1 has shown that d.c. remote of energy with very little expenditure of indication and a.c. synchro systems can energy on his own part. operate between shafts separated by a At first, machines were simple and a human considerable distance, but cannot supply being was quite capable of controlling in torque amplification: the torque delivered to detail the various operations that went to the load can never exceed the input torque. complete any process. But as time has For this reason, and because the error passed, machines and processes have become increases when large torques are transmitted, more complicated and results have had to remote indication and synchro systems are be produced more quickly and more accur­ employed to turn dials and pointers, to ately. Thus it has come about that in many move control valves or to actuate similar cases, man has proved to be an imperfect low-torque loads. controller of the machines he has created. Automatic control systems, on the other It is natural therefore that, wherever possible, hand, can supply the large torques required the human controller should be replaced to move heavy loads, and only a very small by some form of automatic controller. torque need be applied to the input shaft. Remote operation is not inherent in servo­ 2. Automatic control systems can include mechanisms but it can be obtained if synchro electron.ic, electro-mechanical, pneumatic, devices are made part of the system. hydraulic and mechanical devices. Such devices are used to perform diverse functions: 5. From any process there is an end-product f<_>r example, the automatic piloting of an which can be ca11ed the output. The pro­ aircraft, the control of a guided missile, duction of the output depends on the process, the movement of a radar aerial, keeping a and how the process is affected by the input. telescope trained on a star, and so on. A control system acts in such a way that the Nevertheless, regardless of the nature of the output can be controlled in the optimum quantities handled, the resulting arrange­ manner to give a desired result which bears ments have a strong family likeness to each a definite relationship to the input to the other and behave in very similar ways. A system. common theory is therefore applicable to all forms of automatic control. Speed Control of a D.C. Motor The title of this chapter is "Servomech­ 6. Fig. 1 shows an arrangement (known as anisms". A servomechanism, in fact, is the "Ward-Leonard" system) that is used merely a particular type of automatic control for controlling the speed of a d.c. motor system whose output is the position of a driving a load. shaft. It is however the most common The motor armature current is supplied type ?f control system in radio engineering, by a d.c. generator which, in turn, is driven and smce the theory which has been developed at constant speed. The d.c. motor is in its design is now used for all types of separately excited, the field current being control systems, it is convenient to confine held constant. The generator is also separ­ the discussion to servomechanisms. ately excited, but its field current can be varied by adjusting the controller potentio­ 3. A complete treatment of servomechanisms meter. Any variation in the generator is far beyond the scope of these notes. field current varies the generator output A.L. 18 (Mar. 62) RESTRICTED RESTRICTED A.P. 3302, PART 1, SECT. 19, CHAP. 2 CONSTANT SPEED DRIVE GENERATOR SUPPLIES ~ G II c:::> lr MOTOR I I ARMATURE I I CURRENT I I CONTROLLER POTENTIOMETER ~ I I',, CALIBRATED IN REVS/MIN. I I I' C~~ANTri__r-11! l ~ CO~~ANT VOLTAGE~ lllc VOLTAGE GENERATOR MOTOR FIELD FIELD VARIABLE. CONSTANT. Fig. I. SIMPLE SPEED CONTROL OF A D.C. MOTOR voltage and hence the armature current Action of Human Operator to the motor: thus the speed of the motor 8. It is interesting to discuss at this point is varied. If the generator field current is the actions that a human operator would increased, the generated voltage increases, take to maintain a constant speed (Fig. 2). as does the armature current and hence the The first action of a human operator is to motor speed. Therefore the controller poten­ collect the information or data on which he is tiometer could be calibrated with a scale in to act. He has in mind a picture of the out­ revolutions per minute and set for whatever put speed required and at the same time he motor speed is required. notes the actual output speed. His sole With this arrangement, the speed of the function is to compare the two impressions output shaft represents the 'outpl!t': the and so to adjust the system as to reduce the 'input' is the setting of the potentt<;meter. difference, or error, between them: he does The input can therefore be set to gtve the this of course by adjusting the controller desired output which the system should hold potentiometer. He is thus, in this con­ constant. nection, primarily an error-measuring device, and the amount of error determines how he 7. In practice, however, speed is not held causes the motor to use energy from the exactly constant even though ideally the generator to produce the required output speed of a separately-excited .motor .is speed. Note that the human operator pro­ determined by the voltage applied to Its vides a feedback link between output and armature. Variations in speed arise from input. a variety of reasons. In particular, variations of load conditions will cause varying motor speeds and the output is no longer that An Improved Method of Speed Control demanded by the input. 9. In practice, a more effective and efficient This system is not good enough if speed control of output speed can be obtained by control to within a fraction of one per cent replacing the human operator with an auto­ is required. matic control system as shown by the arrange- OPERATOR'S 1 AS Af'~ E~~L T OF CONTROLLED C~~['\R.Jv~G INPUT IMPRESSIONS I ACTUAL II OUTPUT · I _______ _yi~~_£.E.£p~A_EK_!:.!.N.f _____SP~ED j~ ACTUAL SPEED Fig. 2. HOW A HUMAN OPERATOR CONTROLS MOTOR SPEED RESTRICTED RESTRICTED SERVOMECHANISMS MOTOR CONSTANT SPEED ARMATURE DRIVE. CURRENT II II ll %~~STANT Ill VOLTAGE CONSTANT DC MOTORe VOLTAGE · 0 FIELD (±) TACHO·GENERATOR VOLTAGE e t 8 2 APPLIED VOLTAGE e 1 Fig. 3. AN IMPROVED METHOD OF SPEED CONTROL ment of Fig. 3. The response of the auto­ by the tacho-generator decreases and the matic system is better than that of a human generator field current increases; the gener­ operator and the automatic arrangement ated voltage thus increases as does the is not subject to fatigue. motor armature current, and the motor speeds up until it reaches the demanded 10. Tachometer-generator. In Fig. 3, the speed. It follows that if for any reason actual motor speed is measured by connecting the load speed tends to change from that a device known as a tachometer-generator or demanded, the correct restoring action will tacho-generator to the output shaft: this automatically be taken. produces a voltage proportional to the speed at which it is driven, i.e. the actual output 12. The operations of the circuits shown speed. The tacho-generator in the circuit of in Fig. 1 and Fig. 3 differ considerably in Fig. 3 is a separately-excited d.c. generator detail. with a constant field and it is so constructed In Fig. 1 the· output depends primarily that it produces a generated e.m.f. which is on the input demand, but the accuracy of exactly proportional to the rotational speed control is limited because there are no means of its armature. On load, the terminal of controlling other factors that affect the voltage is still proportional to speed, pro­ output (such as variation in output load). vided the load current is small enough for The accuracy of control therefore depends armature reaction to have no effect. D.C. on the linearity of the system. Such systems tacho-generators usually have quite a small are referred to as open-loop control systems. maximum-load current, because the armature An open loop control system is characterized is wound with many turns of fine wire, and by the lack of error comparison; that is, the commutator has a large number of there is no feedback of information from segments to ensure a relatively smooth d.c.
Details
-
File Typepdf
-
Upload Time-
-
Content LanguagesEnglish
-
Upload UserAnonymous/Not logged-in
-
File Pages22 Page
-
File Size-