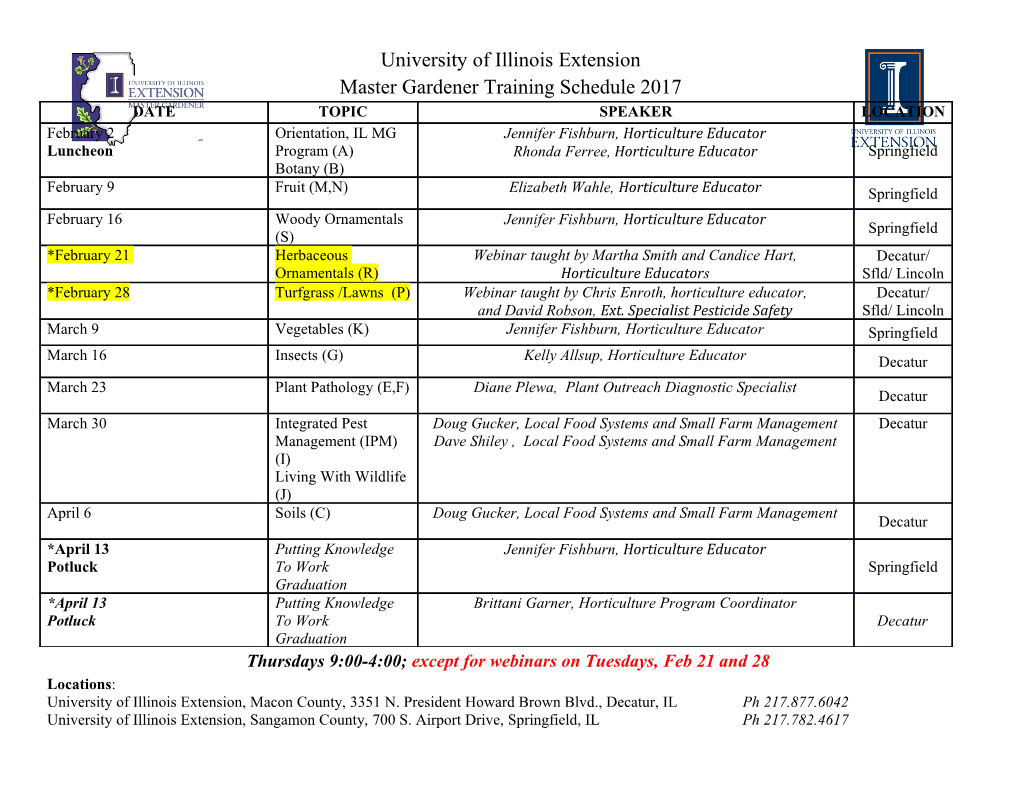
The Pennsylvania State University The Graduate School College of Engineering PRODUCTION OF PHENYLPYRUVIC ACID AND PHYTASE BY MICROBIAL FERMENTATION A Dissertation in Agricultural and Biological Engineering by Hasan Bugra Coban @2014 Hasan Bugra Coban Submitted in Partial Fulfillment of the Requirements for the Degree of Doctor of Philosophy December 2014 The dissertation of Hasan Bugra Coban was reviewed and approved* by the following. Ali Demirci Professor of Agricultural and Biological Engineering Dissertation Advisor Chair of Committee Virenda Puri Distinguished Professor of Agricultural and Biological Engineering Paul H. Patterson Professor of Animal Science Ryan J. Elias Associate Professor of Food Science Paul Heinemann Professor of Agricultural and Biological Engineering Head of the Department of Agricultural and Biological Engineering *Signatures are on file in the Graduate School ABSTRACT Feed and food additives are very popular in industry to increase the quality of diets. They have been used for various applications such as nutritional quality enhancing, coloring, flavor enhancing, antimicrobial effects, thickening, stabilization, increasing shelf-life, and calorie reducing. Phenylpyruvic acid (PPA) and phytase are just two of the important feed and food additives. PPA and phytase have important applications in the industry. PPA is being experimentally used as a substitute for phenylalanine in feeds to decrease excessive nitrogen accumulation in the manure to prevent negative effects on the environment. PPA is also used for kidney patient’s diets to decrease urea accumulation in the body. Additionally, PPA is a very important compound for cheese and wine production to generate a specific taste and aroma. Phytase breaks down phytate, which serves as an anti-nutrient agent by binding divalent ions, amino acids, and proteins in the intestine. Also, phytase is an important additive in monogastric animals’ diet to decrease excessive phosphorus accumulation in the manure, which may cause changing flora and fauna. Therefore, the purpose of this research was to enhance PPA and phytase productions in bioreactors by optimizing growth and fermentation medium parameters, also conducting various fermentation modes. Additionally, the effect of two microparticles (talcum and aluminum oxide) on fungal phytase production was studied. For PPA fermentation, strain selection was first performed using four microbial strains (Morganella morganii, Zygosaccharomyces rouxii, Proteus vulgaris, and Corynebacterium glutamicum) based on a literature search and P. vulgaris was selected as the best microorganism based on PPA production level in shake-flask fermentation, (358 mg/L). Thereafter, growth parameters such as temperature, pH, and aeration were optimized for PPA and biomass production in the bioreactors by using Response Surface Methodology (RSM). Optimum conditions were determined as 34.5°C, 5.12 pH, and 0.5 vvm aeration for PPA production and 36.9oC, pH 6.87, and 0.96 vvm aeration for biomass production. Under optimum conditions, 1054 mg/L PPA and 3.25 g/L biomass productions were obtained. ANOVA results showed that all of growth factors evaluated were significantly (p<0.05) effective on biomass production, however aeration was not a significant (p<0.05) factor for PPA production. iii Additionally, concentration levels of fermentation medium ingredients such as glucose, yeast extract, and phenylalanine were optimized by RSM. The optimum ingredient concentrations for PPA production were determined as 119.4 g/L for glucose, 3.68 g/L for yeast extract, and 14.85 g/L for phenylalanine, whereas 163.8 g/L glucose, 10.75 g/L yeast extract, and 9.84 g/L phenylalanine were the best for biomass production. PPA and biomass concentrations increased to 1349 mg/L and 4.35 g/L, respectively, under these respective optimum conditions. Furthermore, fed-batch and continuous fermentation were conducted to further enhance PPA production. It was determined that addition 4 g of phenylalanine into the reactor at 30 h of fermentation increased PPA concentration to 2958 mg/L. Also, PPA productivity was increased to 259 mg/L/h in continuous fermentations, which is almost 5 times higher compared to productivity in batch fermentation. Additionally, PPA and biomass production, glucose and phenylalanine consumption by P. vulgaris were predicted with modified Gompertz and modified logistic models. The models over-predicted PPA and biomass productions however lower-predicted phenylalanine and glucose consumption data. The modified Gompertz model predicted the experimental data with lower root mean square error (RMSE) and mean average error (MAE) values compared to modified logistic model for all predictions. For phytase fermentation, first phytase producer microorganisms were screened by evaluating four different strains (Lactobacillus plantarum, Lactobacillus acidophilus, Lactobacillus amylovorus, and Aspergillus ficuum) and A. ficuum was selected as the most productive strain among them. The highest phytase activity was measured as 1.02 U/ml in shake- flask fermentation. A. ficcum phytase activity increased to 2.27 U/ml in bioreactors by optimization of growth parameters. For phytase production these were determined to be 33°C, pH 4.5, and 0.9 vvm aeration and all the factors were significantly effective on phytase production. Also, optimum pH and temperature values were determined as 5.5 and 55oC, respectively for A. ficuum using a phytase assay. Additionally, the lowest phytase activity loss was seen under 4oC storage conditions for 1 week. However, -20oC storage conditions provided lower activity loss for A. ficuum phytase when storage was more than 1 week of storage period. Thereafter, phytase fermentation medium ingredients such as glucose, Na-phytate, and CaSO4 were optimized in the next study. Maximum phytase activity was measured as 3.45 U/ml with 126 g/L of glucose, 14 g/L of Na-phytate, and 1.1 g/L of CaSO4. iv Furthermore, the effect of glucose and phytate additions on phytase activity were evaluated in fed-batch fermentations. Maximum phytase activities were measured as 3.84, 4.63, and 4.83 U/ml, when 45 g of glucose, 5 g of Na-phytate, and 10 g of Na-phytate was added into the bioreactors, respectively, at 96 h of the fermentations. Also, continuous fermentation of phytase increased the productivity almost 7-fold compared to batch fermentation. Additionally, the effects of aluminum oxide and talcum were studied on phytase production with A. ficuum. It was reported that phytase activity remarkably increased by addition of 15 g/L of aluminum oxide and talcum to 2.01 and 2.93 U/ml, respectively, compared to the control (1.02 U/ml) in shake-flask fermentations. Moreover, microparticle addition provided small pellets and prevented bulk fungal growth in the fermentation broth. The highest phytase activity was measured as 6.49 U/ml by addition of 15 g/L of talcum in bioreactors at 96 h of fermentation. Also, the effect of talcum addition on fed-batch and continuous fermentations were studied. Phytase activity increased from 4.912 to 9.587 U/ml and from 3.3 to 6.3 U/ml in fed-batch and continuous fermentations, respectively, by addition of 15 g/L talcum. Moreover, maximum phytase productivity was measured as 0.621 U/ml/h at 0.1 h-1 dilution rate with 15 g/L of talcum added continuous fermentation. Finally, phytase production and glucose consumption were predicted with modified Gompertz model and modified logistic model. Modified Gompertz model predicted phytase activity slightly more successfully compared to modified logistic model. Lower MAE and RMSE values were obtained for the prediction of glucose by the modified logistic model compared to the modified Gompertz model, however higher R2 and slope values were obtained by the modified Gompertz model. In conclusion, PPA production increased almost 10 fold in fed-batch studies compared to shake-flask fermentations. Similarly, phytase productions increased almost 5 and 10 fold in fed- batch and microparticle added fed-batch fermentations, respectively, compared to shake-flask fermentations. These studies clearly demonstrated that PPA and phytase productions were significantly enhanced by optimization and using novel fermentation methods. Also, mathematical models provided better understanding of microbial kinetics for both fermentations. With these enhancements, industrial productions of PPA and phytase by using submerged fermentation are now closer to reality than before. v TABLE of CONTENTS LIST of FIGURES……………………………………………………………………………… xiii LIST of TABLES……………………………………………………………………………...... xvi ACKNOWLEDGEMENTS…………………………………………………………………….. xix 1. INTRODUCTION ....................................................................................................................... 1 2. LITERATURE REVIEW ............................................................................................................ 4 2.1. Amino Acids ............................................................................................................ 4 2.1.1. Amino Acid Production .................................................................................... 6 2.1.2. Microbial Production of Amino Acids ............................................................. 7 2.1.3. Applications of Amino Acids ........................................................................... 9 2.1.4. Determination and Quantification of Amino Acids .......................................... 9 2.1.5. Essential and Non-essential Amino
Details
-
File Typepdf
-
Upload Time-
-
Content LanguagesEnglish
-
Upload UserAnonymous/Not logged-in
-
File Pages241 Page
-
File Size-