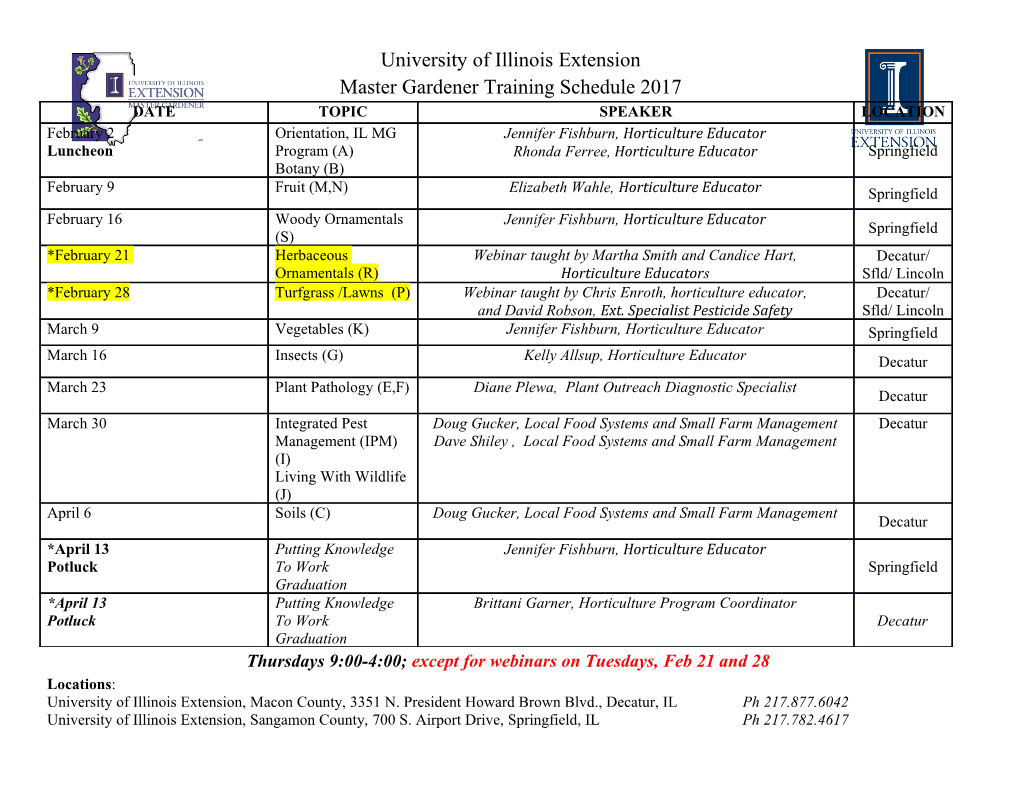
A Basics of Modeling and Control-Systems Theory This appendix collects some of the most important definitions and results of the theory of system modeling and control systems analysis and design. To avoid using any complex mathematical formulations, all systems are assumed to have only one input and one output. This appendix is not intended to serve as a self-contained course on con- trol systems analysis and design (this would require much more space). Rather, it is intended to synchronize notation and to recall some points that are used repeatedly throughout the main text. Readers who have never had the oppor- tunity to study these subjects are referred to the many standard text books available, some of which are listed at the end of this chapter. A.1 Modeling of Dynamic Systems General Remarks This section recalls briefly the most important ideas in system modeling for control. In general, two classes of models can be identified: 1. models based purely on (many) experiments; and 2. models based on physical first principles and (a few) parameter identifi- cation experiments. In this text, only the second class of models is discussed. General guidelines to formulate such a control-oriented model encompass the following six steps at least: 1. Identify the system boundaries (what inputs, what outputs, etc.). 2. Identify the relevant reservoirs (mass, energy, information, . ) and the corresponding level variables. 3. Formulate the differential equations for all relevant reservoirs as shown in eq. (A.1). 262 A Basics of Modeling and Control-Systems Theory d (reservoir content) = inflows outflows (A.1) dt − X X 4. Formulate the (usually nonlinear) algebraic relations that express the flows between the reservoirs as functions of the level variables. 5. Identify the unknown system parameters using experiments. 6. Validate the model with experiments other than those used to identify the system parameters. In step two, it is important to distinguish between slow (curve c) in Fig. A.1), relevant (curve b) and fast (curve a) dynamic effects (very large, relevant and very small reservoirs). The relevant time scales are defined by the main variable b) that is to be controlled. Type a) variables are simplified as being algebraic functions of the other variables and the inputs, while type c) variables are assumed to be constants. variables b) a) c) excitation time Fig. A.1. Classification of variables into “algebraic” (a), “dynamic” (b) and “static” (c). The first four steps are shown here in further detail by deriving a model of a cylindric water-tank system as depicted in Fig. A.2: 1. The input ism ˙ in(t), i.e., the inflowing water mass flow. The output is h(t), i.e., the measured height of the water level in the tank. 2. The only relevant reservoir is the mass m(t) of water in the tank. The dynamic effects in the measuring device are very fast and can there- fore be neglected. The water temperature (and therefore its density) is assumed to change very slowly such that it may be assumed to be constant. 3. The resulting differential equation is shown in (A.2). d m(t) =m ˙ (t) m˙ (t) (A.2) dt in − out 4. The input mass flow is assumed to be the control signal and can therefore be set arbitrarily by the controller to be designed. The outgoing mass flow can be expressed using Bernoulli’s law, shown in A.1 Modeling of Dynamic Systems 263 (A.3), assuming incompressible and frictionless flow conditions, resulting in (A.4). min h(t) F . m m(t) out A y(t) Fig. A.2. Water tank system, m(t) mass of water in tank, and corresponding height h(t), F tank-floor area, A = area of outflow orifice. m˙ out(t) = Aρv(t), v(t) = 2∆p(t)/ρ, ∆p(t) = ρgh(t) (A.3) p d d m(t) = ρF h(t) =m ˙ (t) Aρ 2gh(t) (A.4) dt dt in − The models obtained thus are (usually) nonlinearp and have non-normalized variables. Unfortunately, there is, in general, no “neat” controller design method for nonlinear systems, and non-normalized variables can lead to nu- merical problems and are hard to compare with one another. For these reasons, the model (A.4) must first be normalized using constant nominal values (“set points”), i.e., h(t) = hnx(t), m˙ in(t) =m ˙ in,nu(t) (A.5) such that the new variables x(t) and u(t) will be dimensionless and around 1 in magnitude. Using the definitions (A.5), (A.4) can be rewritten as d ρF h x(t) =m ˙ u(t) Aρ 2gh x(t) (A.6) n dt in,n − n p p Notice that if the set point is chosen to be an equilibrium point (which is usually the case), the nominal amounts of in-flowing and out-flowing water must be equal, i.e., m˙ in,n = Aρ 2ghn (A.7) In order to linearize the system, onlyp small deviations from its set points are analyzed, such that the following new variables x(t) = 1 + δx(t) with δx 1, u(t) = 1 + δu(t) with δu 1 (A.8) | | ≪ | | ≪ 264 A Basics of Modeling and Control-Systems Theory can be introduced. Expanding (A.6) into a Taylor series and neglecting all the terms of second and higher order yields a linear differential equation d 1 ρF h δx(t) m˙ (1 + δu(t)) Aρ 2gh 1 + δx(t) (A.9) n dt ≈ in,n − n 2 p which, using (A.7), can be simplified to d 1 ρF h δx(t) =m ˙ δu(t) Aρ 2gh δx(t) (A.10) n dt in,n − n 2 p or, by rearranging terms and again using (A.7) d τ δx(t) = 2δu(t) δx(t) (A.11) dt − where the time constant τ is defined by F 2h τ = n (A.12) A s g This equation shows that the system becomes slower when either the ratio F/A or the set point hn is increased. The gain of the system is 2 in its normalized form and equal to 2hn/m˙ in,n in its non-normalized representation. Example Cruise-Control Problem The objective of a series of examples is to design a robust cruise-control sys- tem,1 i.e., a control loop that keeps the vehicle speed at its set point despite unobservable disturbances (grading, wind, etc.) and which is robust with re- spect to changing system parameters (speed set point, vehicle mass, gear ratio, etc.) and to neglected dynamic effects (engine torque delays, sensors, etc.). In this section a mathematical model of the dynamic behavior of a simplified vehicle (see Fig. A.3) is derived. Nonlinear System Description First, the nonlinear and nonnormalized system equations are derived. The following assumptions are made in this step: 1. The clutch is engaged such that the gear ratio γ is piecewise constant. 2. No drivetrain elasticities and wheel slip effects need be considered, i.e., the following relations are valid: v(t) = rw ωw(t) and ωw(t) = γ ωe(t). 3. The vehicle must overcome rolling friction (the· force acting on the· vehicle is F = c m g) and aerodynamic drag (F (t) = 1/2 ρ c A v2(t)). r r · · a · · w · · 1 Of course, due to space limitations many important aspects of a real cruise-control system cannot not be addressed in this example. A.1 Modeling of Dynamic Systems 265 m/2 ωw + + Fr Fa (t) Fd (t) gear-box Θ γ w Θe v(t) rw engine ωe Te m/2 Fig. A.3. Simplified vehicle structure, vehicle mass m (wheel masses included) concentrated in the two axles. 4. All other forces are lumped into an unknown disturbance Fd(t). 5. The mechanical energy of a moving part is 1/2 m v2 (pure translation) and 1/2 Θ ω2 (pure rotation). · · · · The procedure outlined in Sect. A.1 is followed now. Step 1: The input to the system is the engine torque Te, which can be assumed to be arbitrarily controllable (the time delay caused by the engine dynamics is very small compared to the typical time constants of the vehicle speed and is therefore assumed to be an algebraic variable, see Fig. A.1). The system output is the vehicle speed v(t). Step 2: The relevant reservoirs are the kinetic energies stored in the vehi- cle’s translational and rotational degrees of freedom, i.e., 1 1 1 E = mv2(t) + 4 Θ ω2 (t) + Θ ω2(t) (A.13) tot 2 2 w w 2 e e Using the assumptions listed above, (A.13) can be simplified as follows 1 4Θ Θ E = m + w + e v2(t) (A.14) tot 2 r2 γ2r2 w w Obviously, the level variable is the vehicle speed v(t). Step 3: The flows acting on the system are the mechanical powers affecting the system, i.e., P+(t) = Te(t)ωe(t), and P (t) = (Fr + Fa(t) + Fd(t))v(t) (A.15) − The energy conservation principle yields the equation d Etot(t) = P+(t) P (t) (A.16) dt − − 266 A Basics of Modeling and Control-Systems Theory Inserting (A.14) and (A.15) yields 1 4Θw Θe d 1 m + 2 + 2 2 2v(t) v(t) = Te(t)v(t) (Fr + Fa(t) + Fd(t))v(t) 2 rw γ rw dt rw γ − (A.17) Step 4: This step simply consists of rearranging (A.17) to obtain d 1 1 M(γ, m) v(t) = T (t) c mg + ρc Av2(t) + F (t) (A.18) dt r γ e − r 2 w d w where 4Θ Θ M(γ, m) = m + w + e (A.19) r2 γ2r2 w w is the total inertia of the system.
Details
-
File Typepdf
-
Upload Time-
-
Content LanguagesEnglish
-
Upload UserAnonymous/Not logged-in
-
File Pages91 Page
-
File Size-