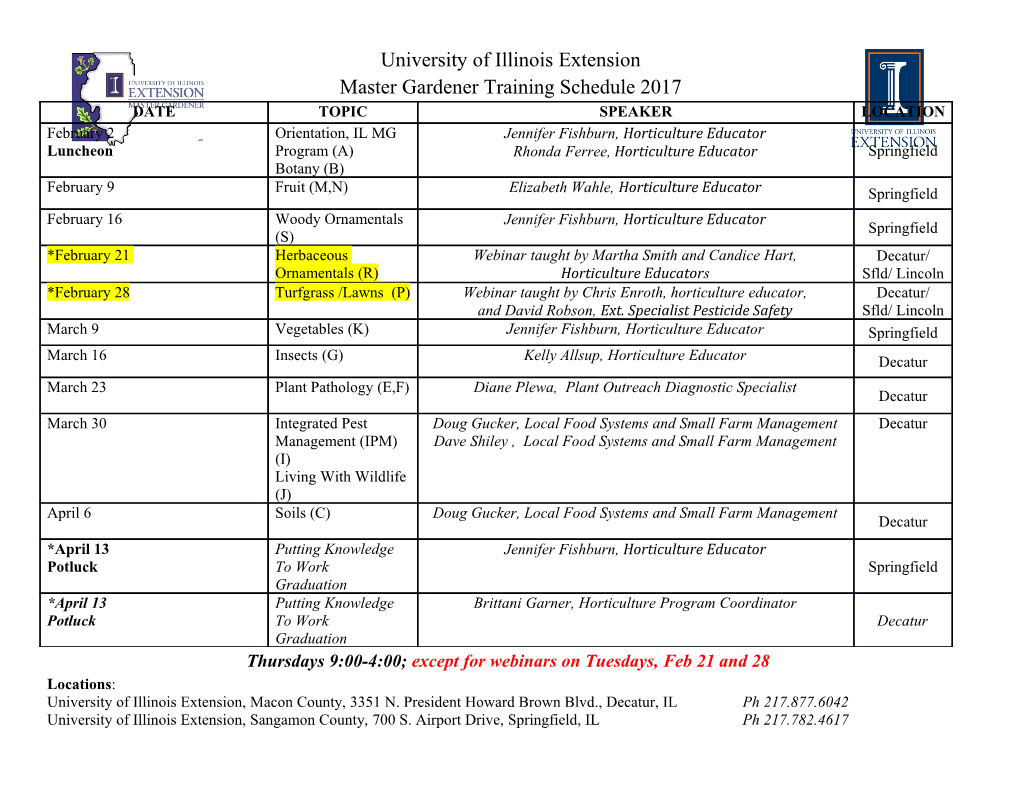
SUSPENSION SYSTEM Suspension - set of elements connecting wheel axles with vehicles’ body • A vehicle suspension is required to perform effectively under a range of operating conditions including high levels of braking and accelerating, cornering at speed and traversing rough terrain – manoeuvres which are required to be done in comfort and with safety. • Suspension system connects vehicles body with wheel and its tire and allow vertical movement of the wheel in relation to body. • The wheels, through the suspension linkage, must propel, steer, and stop the vehicle, and support the associated forces. Suspension system 1. To provide good ride and handling performance – this requires the suspension to have vertical compliance providing chassis isolation and ensuring that the wheels follow the road profile with very little tire load fluctuation; 2. To ensure that steering control is maintained during maneuvering – this requires the wheels to be maintained in the proper positional attitude with respect to the road surface; 3. To ensure that the vehicle responds favorably to control forces produced by the tires as a result of longitudinal braking and accelerating forces, lateral cornering forces and braking and accelerating torques – this requires the suspension geometry to be designed to resist squat, dive and roll of the vehicle body; 4. To provide isolation from high frequency vibration arising from tire excitation – this requires appropriate isolation in the suspension joints to prevent the transmission of ‘road noise’ to the vehicle body. Types of suspension system • Each spatial body with six degrees of freedom can be constrained with suitable elements – like rod links – to reduce the number of DoF • A suspension system should provide one degree of freedom for the wheel. This can be done in different ways for example by adding 5 rod link – each of which would “fix” one degree of freedom. • In real suspension systems links constrain wheel carriers – which can be “carry” one or more wheels. Types of suspension system Factors which primarily affect the choice of suspension type at the front or rear of a vehicle are engine location and whether the wheels are driven/undriven and /or steered /unsteered. In general, suspensions can be broadly classified as dependent or independent types. Dependant suspension system (rigid). Both wheels are mounted to jointed, rigid axle which is fixed with frame or body by means of spring elements. Independant suspension system. Each wheel is fixed to the body (or frame) individually. Dependant suspension system is used in majority of trucks, and in some passenger cars as a suspension of rear driving axle The advantage of a dependant suspension system is its simplicity, which is especially important in vehicles with significant load on axles Independant suspension system has more advantages comparing with dependent suspension systems, and therefore their more frequent usage, especially in trucks, can be observed in recent years. Most significant advantages are: • Reduction of unsprung mass of the vehicle. • Favourable suspension kinematics in terms of driving stability. • Possibility of very soft spring elements application Dependent suspension Solid-axle, leaf-spring • A solid axle is one in which wheels are mounted at either end of a rigid beam so that any movement of one wheel is transmitted to the opposite wheel causing them to steer and camber together • Solid beam axles are commonly used on the front of heavy trucks where high load-carrying capacity is required • wheel alignment is readily maintained, minimizing tire wear • The major disadvantage of solid steerable axles is their susceptibility to tramp-shimmy steering vibrations • When a live solid axle is connected to the body with nothing but two leaf springs, it is called the Hotchkiss drive, • Leaf springs are not suited for taking up the driving and braking traction forces. • These forces tend to push the springs into an S-shaped profile • The driving and braking flexibility of leaf springs, generates a negative caster and increases instability JAZAR, R. N. 2008. Vehicle Dynamics: Theory and Application, Springer US. Dependent suspension Solid-axle, leaf-spring • To reduce the effect of a horizontal force and S- shaped profile appearance in a solid axle with leaf springs, the axle may be attached to the chassis by a longitudinal bar - anti-tramp • Although an anti-tramp bar may control the shape of the leaf spring, it introduces a twisting angle problem when the axle is moving up and down, • Twisting the axle and the wheel about the axle is called caster • If the right wheel goes over a bump, the axle is raised at its right end, and that tilts the left wheel hub, putting the left wheel at a camber angle for the duration of deflection. JAZAR, R. N. 2008. Vehicle Dynamics: Theory and Application, Springer US. Rigid Axles with Longitudinal and Lateral Links • The elements which control the motion of a rigid rear axle must allow translation in the vertical direction as well as rotation about the vehicle’s longitudinal axis. To enable these motions, the axle must be connected to the vehicle’s body with at least one ball joint and one link element. • The lightweight, frictionless coil springs which provide the springing function for these designs do not play a role in controlling the axle’s motion in the lateral or longitudinal directions. • Lateral forces are transmitted between the axle and the vehicle’s body by a Panhard rod or one of the other types of linkages. The motion of a Panhard rod causes the vehicle’s body to shift laterally during compression and rebound. This lateral motion can be eliminated by using a Watt’s linkage for lateral control. HEIßING, B. & ERSOY, M. 2010. Chassis Handbook: Fundamentals, JAZAR, R. N. 2008. Vehicle Dynamics: Theory and Driving Dynamics, Components, Mechatronics, Perspectives, Application, Springer US. Vieweg+Teubner Verlag. Dependent suspension Solid-axle • In other cases, there have been problems, such as axle tramp, particularly when high tractive force is used. To locate the axle more precisely, or more firmly, sometimes additional links are used, such as the longitudinal traction bars above the axle, opposing pitch rotation • In other cases, the leaf springs have been retained as the sole locating members but with the springing action assisted by coils, giving good load spreading into the body. • with the readier availability of coil springs, in due course the rear leaf-spring axle finally disappeared from passenger cars, typically being replaced by the common with four locating links, this system being used by several manufacturers. • In response to the shortcomings of leaf spring suspensions, the four-link rear suspension • The lower control arms provide longitudinal control of the axle while the upper arms absorb braking/driving torques and lateral forces. • Occasionally, the two upper arms will be replaced by a single, triangular arm, but it remains functionally similar to the four-link. • The ability to use coil springs (or air springs) in lieu of leaf springs provides better ride and NVH by the elimination of the coulomb friction characteristic of leaf DIXON, J. 2009. Suspension Analysis and Computational springs. Geometry, Wiley. Dependent suspension Solid-axle • The basic geometry of the four-link system is retained in the T-bar system with the cross- arm of the T located between longitudinal ribs on the body, allowing pivoting with the tail of the T, connected to the axle, able to move up and down in an arc in side view. • The rigid axle is sometimes fitted with a rigid tube going forward to a cross member in which it can rotate as in a ball joint. This, perhaps confusingly, is called a ‘torque tube’, presumably because it reacts to the pitch effect of torque in the driveshafts acting on the wheels. It does give very good location of the axle in pitch. Additional lateral location is required at the rear, such as by a Panhard rod DIXON, J. 2009. Suspension Analysis and Computational Geometry, Wiley. Undriven Rigid Axles • Undriven rigid axles, used at the rear of front-drive vehicles, have the same geometric location requirements as live rigid axles, but are not subject to the additional forces and moments of the driveaction, and can be made lower in mass. • lateral location can be optained by the long diagonal member. This form eliminates the lateral displacements in bumpof the Panhard rod. If the longitudinal links are fixed rigidly to the axle then the axle acts in torsion as an anti-roll bar, the system then being a limiting case of a trailing-twist axle. DIXON, J. 2009. Suspension Analysis and Computational Geometry, Wiley. Semi-dependent systems • In this form of suspension, the rigid connection between pairs of wheels is replaced by a compliant link. This usually takes the form of a beam which can bend and flex providing both positional control of the wheels as well as compliance. Such systems tend to be very simple in construction but lack scope for design flexibility. Independant suspension: A broad term for any automobile suspension system that allows each wheel on the same axle to move vertically (i.e. reacting to a bump in the road) independently of each other. Note that “independent” refers to the motion or path of movement of the wheels. It is common for the left and right sides of the suspension to be connected with anti-roll bars or other such mechanisms. The anti-roll bar ties the left and right suspension spring rates together but does not tie their motion together.
Details
-
File Typepdf
-
Upload Time-
-
Content LanguagesEnglish
-
Upload UserAnonymous/Not logged-in
-
File Pages43 Page
-
File Size-