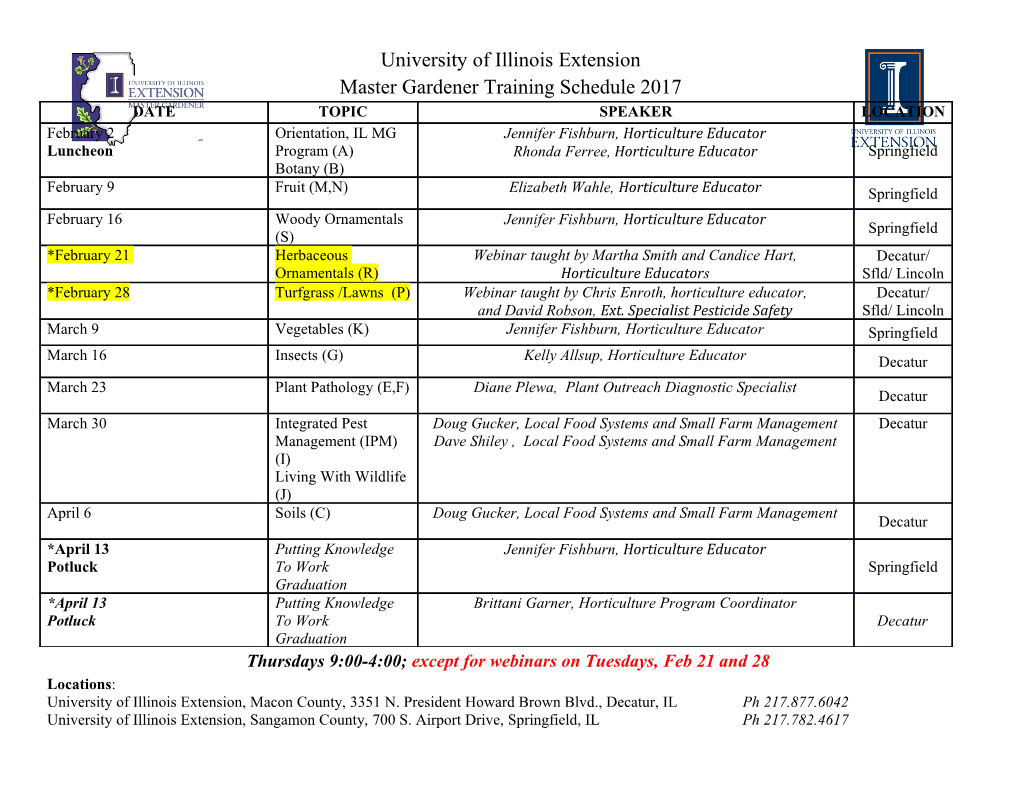
CISRA – Since 1984 ell for Industrial Safety & Risk Analysis hemical Engineering Department entral Leather Research Institute C ouncil of Scientific & Industrial Research The Genesis The rapid technological and industrial growth has its own disadvantages; the manufacture, storage and transport of man-made chemicals invariably pollute the atmosphere. The massive industrial complexes bring with them the palpable danger along with employment potential and modern consumer durable and other day-to-day comforts. The major examples are petrochemicals, drug and agrochemical industries. When the production is large, the problems created also turn large and so are the magnitude of the accidents. This seems to be a global phenomenon. Bhopal, Chernobyl, Mexico City, Three Mile Island and Seveso stand immortal testimony to the magnitude of the chemical industrial disasters and their immediate and after effects. The onus of identifying such disasters and use the same science and technology to prevent them fell on the scientists all over the world. The Cell for Industrial Safety and Risk Analysis (CISRA) is the brain-child of Dr. G. Thyagarajan, the then Director of the Central Leather Research Institute (CLRI), who was also in the investigation committee of the Bhopal Gas Tragedy in India. His vision and Dr. K.V. Raghavan’s efforts resulted into the setting up of CISRA as part of the Chemical Engineering Division of CLRI. It was initiated with senior scientists like Dr. M.M. Mallikarjunan and Dr. P.G. Rao and a host of young chemical engineers and chemists. The CISRA came into existence in 1985 at the CLRI, Chennai as an advisory body on industrial safety in 1987 and later it was transformed into a professional cell with the following objectives: • Create awareness about the importance of industrial safety • Development of infrastructure facilities and engineering expertise in hazard and risk analysis • Creation of information and database on chemical hazards • Technical education on chemical hazards and risks • Technical consultancy on hazard/ consequence / risk analysis • Research and Development in process hazards and cascade or domino effects. Areas of Expertise Risk Analysis Within a short span of five years, the CISRA group developed high level expertise in Maximum Credible Accident and Consequence Analysis (MCAC), Hazard and Operability (HAZOP) studies, Fault Tree Analysis (FTA), Risk Analysis (RA) and Equipment/Instrument Reliability Analysis. Though there were changes taking place in the organization and in the core group of CISRA, the expertise was very effectively transferred equally to almost all the scientists of chemical engineering. A competent team of specialists in modeling and simulation, chemical reaction engineering, thermodynamics, transport phenomena, probability analysis, chemical hazard analysis and allied fields work in CISRA. Thermochemical Studies CISRA also houses a special team of chemical engineers and chemists with excellent academic and research background in thermochemistry, reaction kinetics, polymer chemistry and computer science. The team contributes for several major consultancy assignments of CISRA. The research interests are in the studies on runaway phenomenon in polymerization, oxycarbonylation, nitration and other exothermic reactions. Exclusive consultancy programs are offered to chemical industries in assessing intrinsic safety, hazardous processes, special thermal properties, development of safety protocols, scale-up of hazardous reaction systems, degradation of chemical compounds and design of vent systems etc. Services are offered in: • Chemical screening • Relief sizing and explosion venting • Reactor safety • Calorimetry • Process development Infrastructure For a group that has started with the lofty goals set above, to achieve the target, the infrastructural facilities were very essential. Further, this was an area, which was virgin in Indian industrial field and to impress on the industry and the statutory authorities the cell required computers and software to work. The Netherland Organization (TNO) at Apeldoorn and internationally known group of Risk Analysts came forward to promote CISRA with their software EFFECTS initially. The cell has an impressive infrastructure as follows: Specialized Library CISRA library houses more than 1000 publications on the following topics Physical, Thermodynamic and Transport Properties CHRIS Material Safety Data Sheets for more than 3000 Chemicals Hazard Identification Consequence Analysis Reactive Chemical and Process Hazards Quantitative Risk Analysis Emergency Preparedness The library contributes to several important journals on safety. Bretherick, internationally known expert on Reactive Chemical Hazards had donated his life time collection of books, reports and communications on Reactive Chemical Hazards to CISRA. • INFRASTRUCTURE Software for Risk Analysis • Properties Estimation Physical, thermodynamic, transport and safety properties of organic and inorganic chemicals • Hazard Identification & Consequence Analysis FETI (Fire, Explosion & Toxicity Index) HAZOP-PC (Prima Tech) Effects I Effects - II (TNO) CISCON (CISRA) WHAZAN -II, Safety Audit PC PHAST RISK-Micro (DNV Technica) SAFETI (DNV Technica) ALOHA (EPA) CAMEO DEGADIS AUDIT PC Specialties of the Software The above mentioned software are meant for Consequence Analysis which is also known as Maximum Credible Accident and Consequence Analysis (MCAC) and their damaging effects as follows: • Thermal radiation effects of pool, jet and flash fires, BLEVE etc., • Classification of atmospheric stability • Vapor cloud formation and movement • Unconfined and confined vapor cloud explosions • Passive and dense gas dispersions in atmosphere • Dense gas dispersions with chemical transformations in the atmosphere • Thermal behavior of partially and totally fire engulfed tanks/vessels • Cascade or domino effects • Gravitational settling of dispersed particles • INFRASTRUCTURE In addition, the HAZOP Software provides guidance and assistance in carrying out HAZOP and the documentation of the proceedings. This exclusive software had been very productively applied in the long and brainstorming HAZOP sessions and also for the Training programs conducted by CISRA. Similarly, the Audit PC reels out host questions to conduct the Safety Audit methodically for each and every segment in a plant and its operation. Though not all, the relevant questions can be employed in making the job of an auditor easier. Onsite and Offsite Emergency Planning for chemical industries, industrial areas and clusters to identify areas covered and to frame proper guidelines and action plans, software like ALOHA (Area Location of Hazardous Chemical Atmosphere) and PHAST Risk-Micro are used. Hazard Evaluation Laboratory Laboratory for Thermal Analysis The use of micro calorimetric methods for evaluation of chemical reaction hazards is gaining worldwide importance. CISRA is equipped with the most modern micro calorimetric facilities in India. They include: • High pressure Differential Scanning Calorimeter (HP-DSC) • Differential Thermal Analyser (DTA) • Thermogravimetric Analyser (TGA) • Accelerating Rate Calorimeter (ARC) • Reaction System Screening Tool (RSST) • Reaction Calorimeter (RC) A Table at the end shows the range of properties, which can be evaluated experimentally at CISRA. With the commissioning of the thermochemical laboratory, CISRA has joined the select band of Industrial Safety laboratories in the world with potential to integrate the micro-calorimetric techniques with the consequence analysis of runaway chemical reactions. Thermal Analysis System The Differential Thermal Analysis system consists of Differential Scanning Calorimeter (DSC), Differential Thermal Analyzer (DTA) and Thermo Gravimetric Analyzer (TGA). With plug-in mountings for the interchangeable cells, the module cabinet consists of operating software needed for controlling the system and to perform experiments and store the results, a random access memory with battery backup, the system assures integrity of operation and data. HAZARD EVALUATION LABORATORY The major application of Thermal Analysis Systems include:- • Heat and Temperature transition • Oxidative stability • Thermal stability kinetics • Specific heat of compounds • Reaction exothermicity Reaction Hazard Screening: Chemical samples (1 - 10 g size) can be investigated using the Accelerating Rate Calorimeter (ARC). This screening test provides the following information: • Chemical/Thermal screening • Exotherm onset information • Hazard quantification • Pressure/Temperature data ARC tests produce high sensitivity, full time temperature data of all exothermic processes or reactions under controlled adiabatic conditions. The results may be extrapolated to any industrial scale situation viz. production, storage and transportation. ARC is the world’s benchmark calorimeter for assessing the intrinsic safety of reactions systems. Its application areas cover reactor stability, contamination effects, chemical compatibility checks, process energy optimization, relief vent sizing and evaluation of thermal performance of catalysts, inhibitors and accelerators. Small quantities of liquid solid samples are subjected to programmed temperature increase in ARC to determine the point at which the sample starts generating its own heat. The ARC facility at CISRA consists of a spherical bomb suspended inside a calorimeter jacket, heaters, temperature and pressure sensors, micro processor control unit and power
Details
-
File Typepdf
-
Upload Time-
-
Content LanguagesEnglish
-
Upload UserAnonymous/Not logged-in
-
File Pages26 Page
-
File Size-