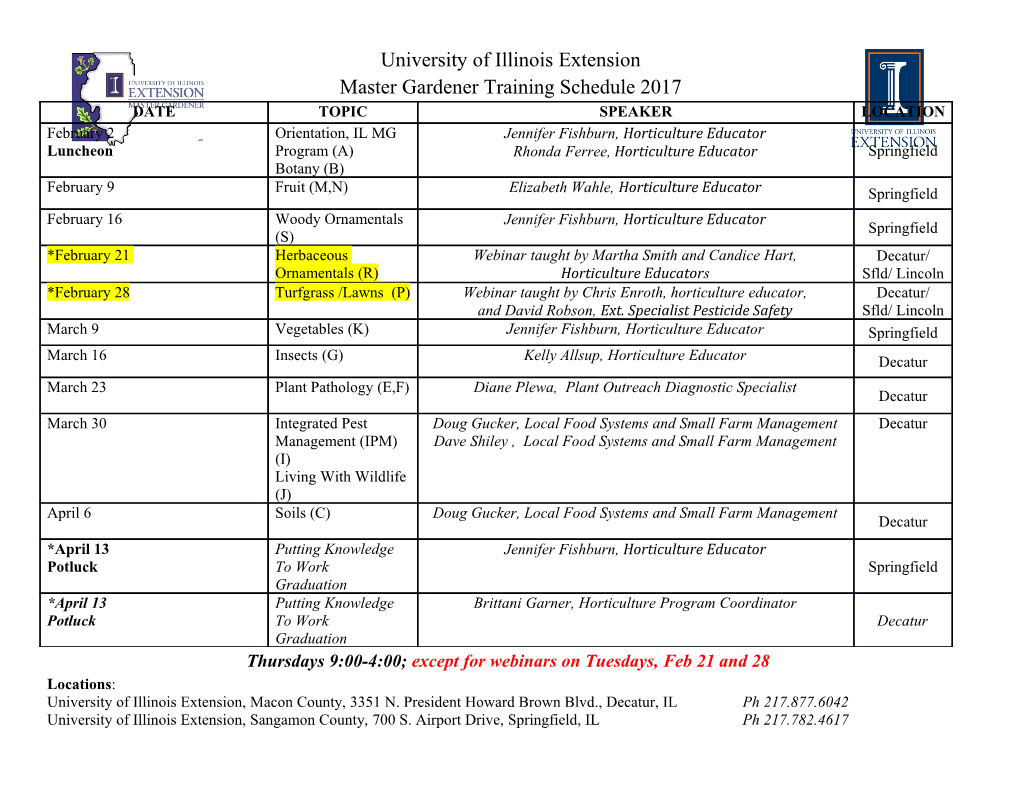
SURFACE PREPARATION OF BUILDING SUBSTRATES A Durability + Design Collection Surface Preparation of Building Substrates A Durability + Design Collection Copyright 2013 by Technology Publishing Company 2100 Wharton Street, Suite 310 Pittsburgh, PA 15203 All Rights Reserved This eBook may not be copied or redistributed without the written permission of the publisher. D SPONSORED BY ® ii Contents iv Introduction Surface Preparation: A Primer 1 by Jayson L. Helsel, KTA-Tator, Inc. Peeling Away the Years: Taking on the Job of Getting Old Coatings Off 5 by Deborah Slaton, Wiss, Janney, Elstner Associates Building a Formula for Removing Coatings from Masonry Surfaces 9 by Kenneth A. Trimber, KTA-Tator, Inc. Six Key Points You Should Know about Concrete Surface Preparation 17 before Coating Application by Fred Goodwin, BASF Construction Chemicals Department of Defence: Protecting Wood Exteriors 22 by Jayson L. Helsel, KTA-Tator, Inc. A Firm Foundation, Part 2: Surface Preparation and Test Methods 25 by Charles H. Holl, Dayton Superior Corp. Cleaning Exotic Woods 31 by Diane Calabrese and Brett Martin Low Cost Dust Barrier Solutions ZipPoleTM 4-Pack Sets up in minutes. No tape, no ladders, no damage. The ideal starter kit at a great low price. Create a temporary dust barrier up to 30 feet long. Poles extend from 4’ 2” to 10’ 3”. Includes: I Four 10’ ZipPoleTM low-cost steel poles I TTwowow 7’ Standard Zippers I One Carry Bag ZipDoor TM Kit ZipWall ® urns anT y doorway into a dust Double-Sidedouble-Sided TapeTape barrier in minutes. ver anCo any opening, And it’’ss rreusable!eusable! NEW!NNEEW built-in or fixture with WW! ® I Standard: for doors up to 3’ x 7’ ! plastic sheeting and ZipWall I Commercial: for doors up to 4’ x 8’ double-sided tape. (flame retardant)etar I Roll size:Roll I Made of 4 mil plastic 2” x 60’ & 1 ”x 60’ I Heavy duty zippers pre-installed I Double-sided: I Helps youou meet EPPAA RRP Side 1 - like painter’s tape NEW!NNEEW equirr ements WW! Side 2 - holds sheeting ! I 14 day rating NEW!NE EWWW! FREE TRIAL ! Get a sample roll of ZipWall TTape.ape. Visit: wwwV .zipwall.com/ddwp ® For more information call 1 800 718 2255 or visit www.zipwall.com iv Introduction This eBook consists of articles from Durability + Design (D+D), durabilityanddesign.com, the Journal of Architectural Coatings (JAC), and Paint and Wallcovering Contractor (PWC) on the subjects of coatings removal and surface preparation of building substrates. More articles on this topic may be found online at durabilityanddesign.com. Photo courtesy of Sponge-Jet Inc. Cover photo courtesy of istock Getting It Right 1 By Jayson L. Helsel, P.E. KTA-Tator, Inc. Surface Preparation: A Primer Editor’s Note: This article apeared in urface preparation, together with the related process of removing existing coatings, always JAC in October/November 2008. Sranks as one of the most critical steps in successful coatings application. The objectives of these processes are twofold: to clean and roughen the substrate according to the specified require- ments. The methods used to prepare surfaces for coating application may clean and roughen simultaneously— as with abrasive blast cleaning. At other times, these steps must be performed separately, as with chemi- Various removal, cal stripping. In either situation, cleaning and roughening must be treated as two distinct acceptance criteria. For example, there may be situations where the level of cleaning is adequate, but the roughness may be cleaning methods insufficient or excessive to facilitate proper adhesion of newly applied coatings. Alternatively, the surface are tailored to roughness may be adequate, but the level of cleaning may be inadequate. meet challenges of substrate type and condition, service requirements 2 Sur face-preparation methods Surface-preparation methods can range from simple solvent cleaning to hand and power-tool cleaning; from dry and wet abrasive-blast cleaning to chemical stripping; and from water jetting to other, more non- traditional methods, such as sponge jetting and cryogenic blast cleaning with dry ice pellets. The degree of cleaning required for a given project specification depends on the service environment (the environment in which the coating system must provide sufficient performance), the composition and prop- erties of the coating system, and the intended service life of the installed coating. Hand-tool cleaning Hand-tool cleaning, typically employed in relatively minor touch-up repairs for maintenance painting activities, is done with wire brushes, scrapers, and other tools that do not depend on electric or pneumatic power to operate. Hand tools are only intended to remove loosely adhering materials; when the substrate is steel, this includes corrosion products, old paint, and mill scale. Hand tools used on steel are not intended to roughen the substrate and pro- duce a surface profile or “anchor” pattern to facilitate adhesion of newly ap- plied coatings. For softer substrates such as wood, hand tools may produce sufficient roughening for paint application. Power-tool cleaning Power-tool cleaning is typically performed with grinders, pneumatic chisels, needle scalers, rotopeen tools, and other mechanisms that require an electric or pneumatic power source to operate. Most of these tools can remove both loosely and tightly adhering corrosion products, paint, and mill scale from steel surfaces. Some of these tools can also produce a small anchor pattern on Coatings-removal and surface-preparation processes are tailored to the steel surfaces. Additionally, these tools can be equipped with vacuum ports needs of a given project. Abrasive-blast methods employing proprietary and hoses for attachment to filtered vacuums so that the fine, airborne parti- sponge-type media were used for the coatings removal projects shown in cles that are created during surface-preparation activities are collected at the the photos on this and previous page. point of generation. Previous page and above: Exterior of a brick building before coatings removal Power-tool cleaning is typically employed for maintenance repairs of small (above) and after removal (previous page). areas, but can also be used when methods such as abrasive blast cleaning are Below: Coatings removal in progress. Photos courtesy of Sponge-Jet Inc. not an option. Dry abrasive blast cleaning Blast cleaning with dry abrasive media is one of the most common methods for preparing a surface for coat- ing. Abrasive blast cleaning can be used to roughen an existing coating for subsequent overcoating, or to completely remove everything from the substrate, including the existing corrosion products, coating, and mill scale. Abrasive blast cleaning is the most productive of all surface-preparation methods, in volume terms. Thou- sands of square feet of surface can be prepared for coating in a single work shift. The hardness and mass of the abrasive media, combined with the velocity of the abrasive as it exits a nozzle at high speed, gen- erates high levels of energy. As the abrasive media impact a surface, they can remove existing coating lay- ers, corrosion, and mill scale, while simultaneously generating a surface profile or anchor pattern. The level of cleanliness that is achieved is ultimately determined by the distance that the nozzle is held from the surface and the “dwell time” that the operator employs. The depth and shape of the surface pro- file is determined by the type and size of the abrasive media employed, as well as the hardness of the sur- face being prepared. Therefore, selection of the correct type and size of abrasive media is critical. Selecting an abrasive size that is too small will generate a surface profile that is too shallow, and selecting a too-large abrasive will create a surface profile that is too deep. The abrasive type and size ultimately selected should be tested before production to verify that the specified surface profile depth and shape can be achieved. 3 Typically, harder abrasives—those designed to achieve complete coating removal and an adequate pro- file—include steel grit, steel shot, and mineral abrasives such as coal slag and garnet. Softer abrasives, which are typically used to remove loose coatings and other loose material from a substrate, include alu- minum/magnesium silicate, corncobs, walnut shells, limestone, or some mineral sands. Another mineral abrasive—usually used in the form of beads—is glass. Although not frequently em- ployed, glass-bead blasting can be used to clean and prepare certain glass, plastic, rubber, and metal surfaces. The manufacturers of glass-bead abrasives should be consulted for specific applications suitable for their materials. An alternative to blasting with traditional dry abrasives is “sponge blasting,” which uses proprietary blast media and equipment manufactured by Sponge-Jet Inc. According to Sponge-Jet, the sponge media “is an open-celled, water-based polyurethane impregnated with abrasives.” A variety of sponge abrasive materials are available to achieve various levels of cleaning. The nature of the sponge material can allow for greatly reduced levels of dust and airborne contaminants during the blasting process. Shot blasting for concrete floors Another variation of dry abrasive blast cleaning is shot-blast cleaning with self-contained centrifugal wheel blast units. Such units employ a vacuum system to contain the abrasive and debris, and are well suited for use on large, horizontal surface areas such as concrete floors. The machines prepare a strip of surface rang- ing from several inches up to 30 inches in width in one pass. This method of surface preparation can re- move any existing coatings, in addition to roughening the concrete surface. Pressurized water cleaning Pressurized water cleaning is a good method for cleaning surfaces, but it cannot etch a profile into the sur- face. Water jetting, however, can restore an existing surface profile. The common levels of cleaning are: • LPWC: Low-Pressure Water Cleaning (up to 5,000 psi); • HPWC: High-Pressure Water Cleaning (5,000–10,000 psi); • HPWJ: High-Pressure Water Jetting (10,000–30,000 psi); and • UHPWJ: Ultra-High-Pressure Water Jetting (>30,000 psi).
Details
-
File Typepdf
-
Upload Time-
-
Content LanguagesEnglish
-
Upload UserAnonymous/Not logged-in
-
File Pages40 Page
-
File Size-