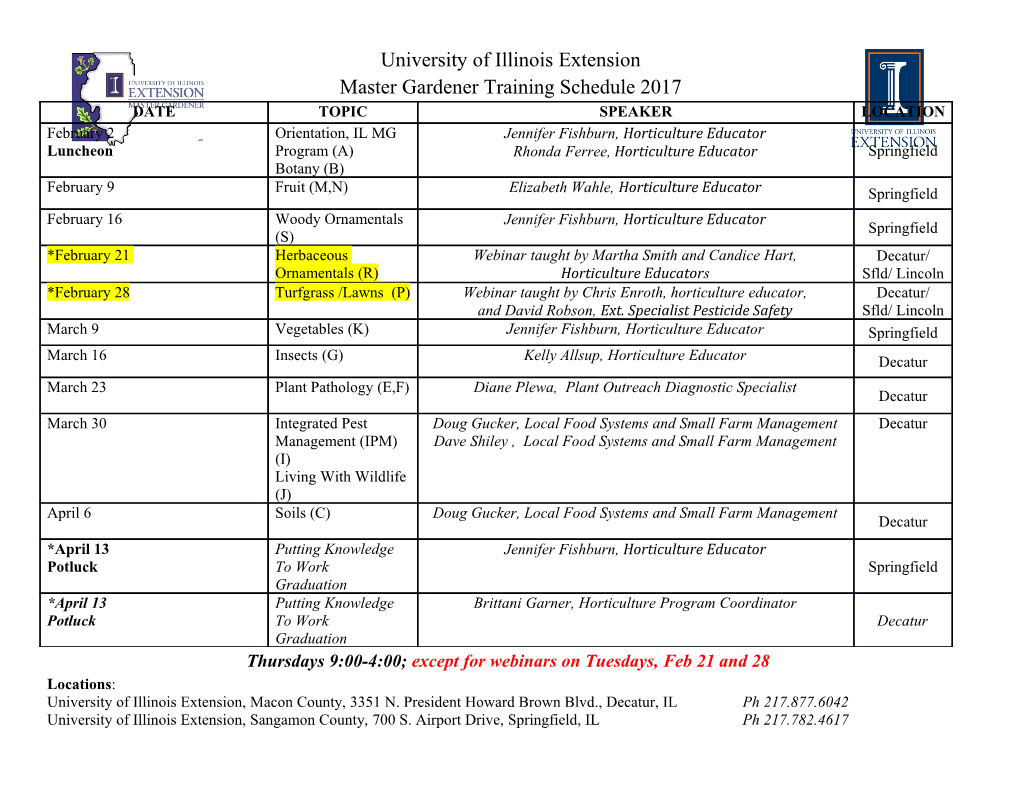
Waste Reduction Guidelines for the Composite Industry A Step-by-step Approach to Developing a Comprehensive Waste Reduction Program funded by the Missou fl' Department of Natural Resources This manual was developed by Environmental Technical Services (ETS), 18846 Highwood Estates Drive, Pacific, MO 63069 in consultation with Bridging The Gap, Inc., 435 Westport Road. Kansas City, MO 641 11 For more information on services available, contact John Unser, ETS, (3 14) 273-6687, email ets@inlink com or Mad Crabtree, BTG, (816) 561-1087, email eec@bridgingthegap org Table of Contents Introduction .............................................................................................................................. 1 The Composite Industry.. ................................................................................................... 1 Manufacturing Methods ............................................................................................................. .2 Waste Generation in Missouri Composite Industry .................. ........ ............ 3 Benefits of Waste Reduction . ........................................ .......................... 3 Industry Success Stories .............................................................................................................. 5 Developing a Waste Reduction Plan for your Company ......................................................... 6 Phase One: Start-up ................................................................................................................... 7 Phase Two: Waste Assessment.. ............................................................................................... 10 Phase Three: Develop a Waste Reduction Plan .......................................................................... 18 Phase Four: Implementation .......................... ................................................................... 23 Conclusion ............................................................................................................................... 27 References................................................................................................................................ 28 List of Figures Figure 1 - Composite Shipments Since 1991 ......................................... ........................ 1 Figure 2 - Distribution of Solid Waste Stream .................. ................................ 3 Figure 3 - Development of a Waste Reduction Program ....................... ........................ 6 Figure 4 - Sample Kick-off Memorandum ................................................................................. 10 Figure 5 - Sample Start-up Memorandum ......................................................................... List of Tables Table 1 - Composite Manufacturing Methods .............................................................................. 2 List of Appendices Appendix A - Step-by-step Worksheets Appendix B - Case Study - Company ABC Appendix C - Waste Reduction Ideas for the Composite Industry Appendix D - Recycling in the Composite Industry Appendix E - Companies Supporting Waste Reduction and Recycling Appendix F - Other Resources i Introduction The Composite Industry Composite materials offer many superior properties that have enabled composites' manufacturers to gain significant market share in a variety of industries. Benefits such as high strength to weight ratios and excellent resistance to environmental exposures provide significant advantages over conventional materials. A composite material contains a reinforcement (such as fibers) supported by a binder (matrix) material. Examples of the products manufactured with composites include bathtubs, vanities, recreational boats, truck hoods, automobile parts, small appliances, storage tanks, and aircraft parts. Composite use has grown continuously since its introduction in the 1960's Figure 1 graphically shows the increase since 199 1. The Society of Plastic Industries (SPI) Composite Institute has predicted a record high of 3.22 billion pounds of composite materials will be shipped in 1996. hcraft/Aerospace/Mihtary 0th I AppCance/BLlsmxs Eqqment Consumr Products ElectmaL'Ekctrom h4aX-m CorroslowReslstant Equpment ComtnctPn Transportatmn Figure 1 - Composite Shipments Since 1991 Many types of materials are used in the fabrication of composite structures. Carbon, aramid, glass, or ceramic fibers may comprise the reinforcement component. Examples of fiber forms are: chopped, unidirectional tape, cloth, roving, and performs The matrix or resin material can be a polyester, vinyl ester, epoxy, polymide, or bismaliamide just to mention a few. The composite industry's most dominant matrix and reinforcement combination is polyester resin and glass fibers, known more commonly as Fiberglass Reinforced Plastics (FRP). In the aerospace industry the most common material combination is carbodepoxy. These two materials make up roughly 90% of the composite market. 1 Manufacturing Methods Many manufacturing methods are used to produce composite structures. Examples of processing methods include: filament winding, pultrusion, resin transfer molding (RTM), injection molding, compression molding, wet lay-up, spray-up, resin infusion, and hand lay-up using prepreg and autoclave cure. Table 1 compares the pro2esses. FRP is typically fabricated using wet lay-up or spray-up. Aerospace structures are primarily fabricated using hand lay-up of prepreg and autoclave cure. This process is expensive, and due to defense cutbacks, the aerospace industry is investigating lower cost fabrication. The waste generated by each of the manufacturing methods varies and each method may generate several waste streams. A waste steam is defined as a unique discarded material that must be handled separately. A recent study done for the Air Force ranked several composite manufacturing methods based on the amount of waste generated. The processes were ranked in the following order, from most wasteful to least wasteful: hand lay-up using prepreg and autoclave cure, filament winding, compression molding, RTM, and pultrusion. The study did not include wet lay-up, spray-up or resin ihsion. Considering their ranking methodology, these methods would fall between the methods of filament winding and compression molding. The rankings for the processes are included in Table 1. A high negative number represents less generated waste Table 1 - Composite Manufacturing Methods Waste Manufacturing Method Fiber Relative Cost Generation Unique Waste Streams Volume Ranking' Pultrusion 4555% LOW -30 Excess resin, scrapped parts, cured trimming Resin transfer molding 4560% Moderate -1 8 Flashing, scrapped parts, curec trimming Wet lay-up 40-50% LOW -1 3 Cured trimming, cured excess resin Compression mdding 40-50% LOW -1 1 Flashing, scrapped parts, outdated materials Resin infusion 50-60Yo LOW -9 Vacuum bagging material, cured trimming Spray-up 4040% LOW -9 Overspray, cured trimming, cured excess resin, scrapped Pa* Filament winding 50-60% Moderate -7 Excess resin, scrapped parts, cured trimming Autoclave cure - hand lay-up 5560% High 0 Scrap prepreg, cured trimming, vacuum bagging material, prepreg backing, outdated materials, scrapped parts 2 Waste Generation in Missouri Composite Industry In 1997 Environmental Technical Services (ETS) conducted a survey limited to the companies that fabricated composite structures in Missouri. A total of 155 surveys were mailed and 32 were returned. Survey results indicate spray-up to be the dominant manufacturing process. Cured trimmings and overspray represent over 60% of the solid waste stream as seen in Figure 2. These two types of waste should be the primary focus of most industry waste reduction strategies Wooden Used Scrapped waste Part trimming 55.9% Cardboard 15.1% Figure 2 - Distribution of Solid Waste Stream The ETS survey determined the amount of waste generated by the Missouri Composite Industry Survey results indicated that each employee would generate an average of 7,345 pounds or 3 7 tons of waste per year The total waste generated by the Missouri Composite Industry would then be 85 9 million pounds or 42,968 tons per year This calculation is based on the average of seventy-eight employees per company and a total of 1 50 composite manufacturers. Considering these figures, an impressive 58.8 million pounds or 29,433 tons of scrap composites could be available for recycling each year Benefits of Waste Reduction Companies across the country report significant success with waste reduction campaigns, and many have saved thousands of dollars a year by implementing procedures such as ones described in this manual By reducing the waste generated in your manufacturing process, your company can save money, increase productivity, attract customers, and help protect the environment. 3 Economic Advantages 0 Waste reduction can reduce material and supply costs and increase efficiency through cost effective work practices. 0 Hauling and waste disposal costs are slashed when waste volume is reduced 0 According to a survey by the New Jersey Department of Environmental Protection, companies that prepared waste reduction plans projected savings of $7.40 for every $1 .OO invested. Enhanced Corporate Image Environmentally conscious companies attract customers. Many consumers consider a company’s environmental record when making purchase decisions. 0 Environmentally conscious companies enjoy an enhanced public image in the local community. 0 Companies conducting waste
Details
-
File Typepdf
-
Upload Time-
-
Content LanguagesEnglish
-
Upload UserAnonymous/Not logged-in
-
File Pages95 Page
-
File Size-