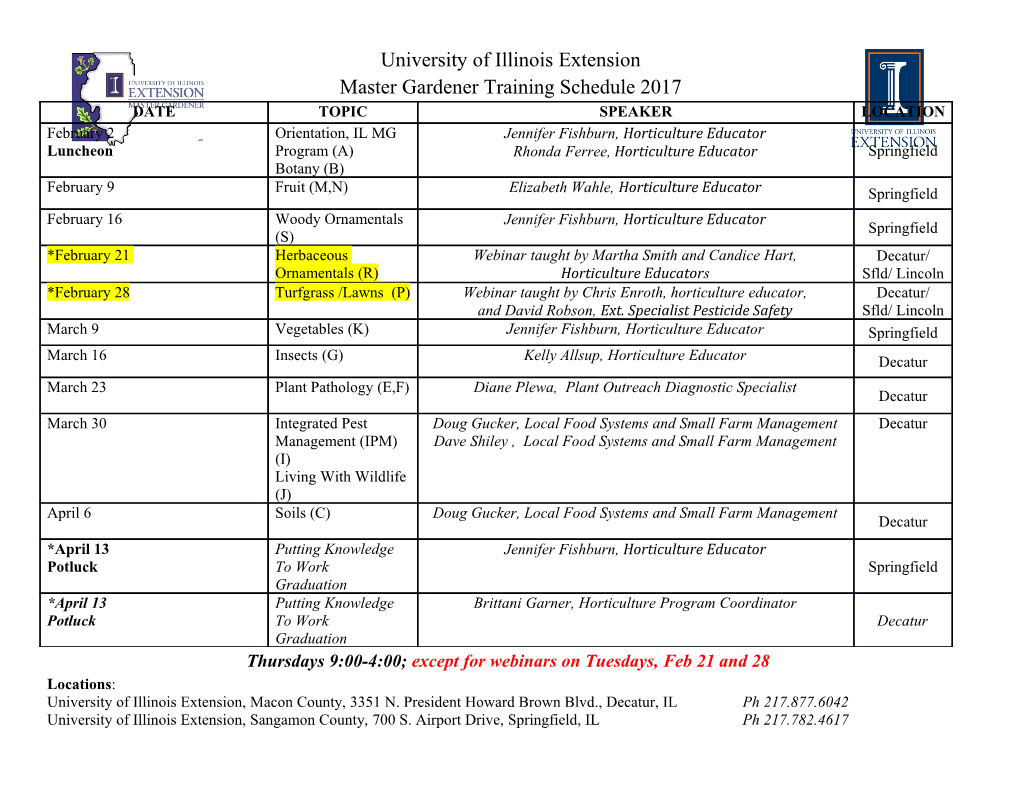
Purdue University Purdue e-Pubs International Compressor Engineering Conference School of Mechanical Engineering 1976 Design Considerations for Heat Pump Compressors J. F. Horn P. H. Scharf Follow this and additional works at: https://docs.lib.purdue.edu/icec Horn, J. F. and Scharf, P. H., "Design Considerations for Heat Pump Compressors" (1976). International Compressor Engineering Conference. Paper 192. https://docs.lib.purdue.edu/icec/192 This document has been made available through Purdue e-Pubs, a service of the Purdue University Libraries. Please contact [email protected] for additional information. Complete proceedings may be acquired in print and on CD-ROM directly from the Ray W. Herrick Laboratories at https://engineering.purdue.edu/ Herrick/Events/orderlit.html DESIGN CONSIDERATIONS FOR HEAT PUMP COMPRESSORS JAMES HORN, MANAGER HERMETIC COMPRESSOR DESIGN AND PROillCTION ENGINEERING PHILIP SCHARF, MANAGER HERMETIC CCMPRESSOR ENGINEERING COPELAND CORPORATION, SIDNEY, OHIO INTRODUCTION A typical application condition (Figure 4\ would be a 20°F outdoor ambient with an evaporating The increased cost of energy for heating purposes temperature of 5°F. For a compressor isolated in makes the heat pump system more and more attrac­ a separate compartment in the outdoor coil cabinet, tive. The economy of operation of the heat pump the ambient temperature would be about 45°F to 50° will create high demand for this equipment in the F. next few years. This may well be the fastest growing segment of the air conditioning industry. A severe environment condition would be a low evaporating temperature occurring along with a Good system design and use of reliable components high condensing temperature (see Figure 5). This is essential for the success of a heat pump. condition could result from an outdoor ambient Operating conditions are more severe and the temperature of 0° to -l0°F, and restricted air system will be utilized two to three times longer flow over the indoor coil. Here the compressor each year than a conventional air conditioner. could experience evaporating and condensing tempera~ures in the range of -l5°F and ll0°F, With these added requirements in mind we will respect1vely. explore the design of compressors developed especially for heat pump systems. (3) Pressure Ratios HEAT PUMP SYSTEM CONDITIONS The pressure ratio is defined as the absolute discharge pressure divided by the absolute evapora­ (1) Qperating Hours ting pressure. In air conditioning systems, the pressure ratio seldom exceeds 4 to 1. In heat In Northern climates, a heat pump compressor may pumps, the ratio may exceed 8 to 1 as indicated by be required to operate up to seven times longer Figure 6. each year than that required for air conditioning only (see Figure 1). The operating time for a Pressure ratios are a major consideration in heat typical location will be increased by a factor of pump compressor design. As the ratio increases, three. bearing lubrication and discharge valve tempera­ tures may be adversely affected. Figure 7 shows (2) Evaporating and Condensing Temperatures a worn rod-wrist pin bearing. This is a bearing that provides long life when operating on cooling A heat pump compressor must be capable of operating only systems but has a limited life at the higher under a wide range of system conditions - from air pressure ratios experienced under heating conditioning to extreme heat pump conditions. The conditions. Figure 8 shows a valve plate that has standard by which air conditioning compressors been operating at excessive discharge gas tempera­ have been rated for many years (see Figure 2), is ture. The deposits are products of oil breakdown. 130°F condensing temperature and 45°F evaporating Accumulation of such deposits will eventually temperature. prevent proper valve closing and result in loss of performance. At the A.R.I. standard for rating heat pumps (Figure 3), a heat pump system is very effective (4) Liquid Refrigerant Return and yields a high coefficient of performance. Here the condensing and evaporating temperatures are Compressors may be subjected to excessive liquid approximately ll0°F and 30°F respectively. This return during the defrost cycle if the system does condition and the air conditioning standard are not have adequate provision to control liquid flow ideal conditions for the compressor. to the compressor. Liquid flooding is character­ ized by a severe drop in compressor oil sump temperature. 194 Excessive liquid refrigerant in the compressor oil starves the pin bearing of oil. The wear shown in sump can have these damaging effects: Figure 7 was induced by operating the compressor in heating mode with the evaporating temperature Slugging - mechanical stress on valves, gaskets, at -l5°F and the oil sump temperature above 250°F. piston-rod assemblies; The bearing surface area must be increased to Loss of oil - violent "boiling" of the refrigerant compensate for less favorable lubrication. We have in the oil sump may carry the oil out in the form found from our development work that wrist pin of foam; bearing areas must be increased 20% to 40% from air conditioning only compressor designs. Dilution of the oil - floodback may dilute the oil to the extent that bearing failure will result; (2) Pistons Piston seizure - rapid change in temperature may A sudden drop in the oil sump temperature may result in loss of piston-to-cylinder clearance and cause the cylinder to "shrink" at a faster rate piston failure. than the piston, resulting in loss of running clearance and piston-to-cylinder seizure. Sudden (5) Low Ambient Temperature Operation temperature drops in the oil result from inadequate liquid control during the defrost cycle. Pistons Low outdoor ambients produce low evaporating with rings have greater running clearance and have pressures and light loads on the compressor. On the ability to survive such thermal shock. single phase motors, light loads impress high voltages on the n.n1 capacitor. (3) Oil Cold starts after a long shut dawn may be damaging The hazards of liquid refrigerant in the heat pump to a compressor if the crankcase heater is not compressor oil sump were listed under "heat pump completely effective. If liquid refrigerant is operating conditions". The oil crnmnonly used in allowed to accumulate in the oil sump it may dilute air conditioning systems mixes readily with liquid the oil and prevent adequate bearing lubrication. refrigerant and can be carried from the compressor If sufficient liquid accumulates it can result in when excessive floodback occurs. The heat pump mechanical damage to valves, gaskets, etc. compressor may frequently be subjected to exces­ sive liquid return, therefore, an oil that is (6) Fault Conditions- easily carried out of the compressor becomes a design concern. Loss of refrigerant - Heat pumps have more complex refrigerant circuitry and more opportunity for ''White oil" (a highly refined mineral oil) has an system leaks to occur. As refrigerant is lost anti-foaming quality that makes it a good candidate from the system, the load on the compressor is for heat pump compressors. System tests with reduced. The reduced load allows the motor to run strategically located sight glasses dramatically at increased speeds which increases the current in demonstrate white oil's ability to stay in the the auxiliary winding and may cause severe over­ compressor oil sump under flooding conditions that heating. This occurs at a time when the motor will carry out standard air conditioning oil. The cooling medium (the refrigerant) is in short compressor experiences less dilution of the oil supply. If the motor protector is responsive to and no loss of lubrication. this condition, it will shut the motor off before the motor temperature reaches a danger point. (4) Motor Protection However, if this condition goes undetected for an extended period of time, the life of the protector Since the heat pump compressor is called on to could be in jeopardy. Since heat pumps have operate three times longer each year and ttnder more auxiliary resistance heaters, which can supply the varied and adverse conditions, the role of the entire heating requirement, a malfunctioning heat motor protection system becomes more significant. pump system may go undetected for an extended A common and successful protection design for air period of time. conditioning systems is a device that senses the combined current of the main and auxiliary motor Blocked condenser - Dirty indoor air filters windings and is located to thermally respond to increase condensing temperature and the pressure high winding temperatures at low currents. ratio that the compressor must operate under. However, to fully protect the compressor at the various heat pump system conditions, additional HEAT PUMP COMPRESSOR DESIGN requirements must be placed on the motor protec­ tion system. (1) Connecting Rod-Wrist Pin Bearing Internal motor protectors are now available that High pressure ratios frequently experienced in can respond to high currents in the main and heat pump operation impose greater requirements on auxiliary windings independently. The protector the wrist pin bearings. The wrist pin is a low has two heaters, one in series with each winding surface velocity bearing that relies on load circuit. A comparison of the two types of motor­ reversal to aid in its lubrication. High pressure protector circuits can be seen in Figure 9. ratios reduce the load reversing action, which 195 The addition of the auxiliary winding heater pro­ (4) Low Ambient Qperation vides these benefits; Typical compressor performance curves with 10° Limits high auxiliary winding temperatures that superheat are shown in Figure 10. Note that these may occur from light loads and high line voltages; curves are cut off at the limit of safe operating temperatures with this amount of superheat. At Protects the compressor motor against sticking low ambient temperatures, the stresses resulting start relay contacts.
Details
-
File Typepdf
-
Upload Time-
-
Content LanguagesEnglish
-
Upload UserAnonymous/Not logged-in
-
File Pages9 Page
-
File Size-