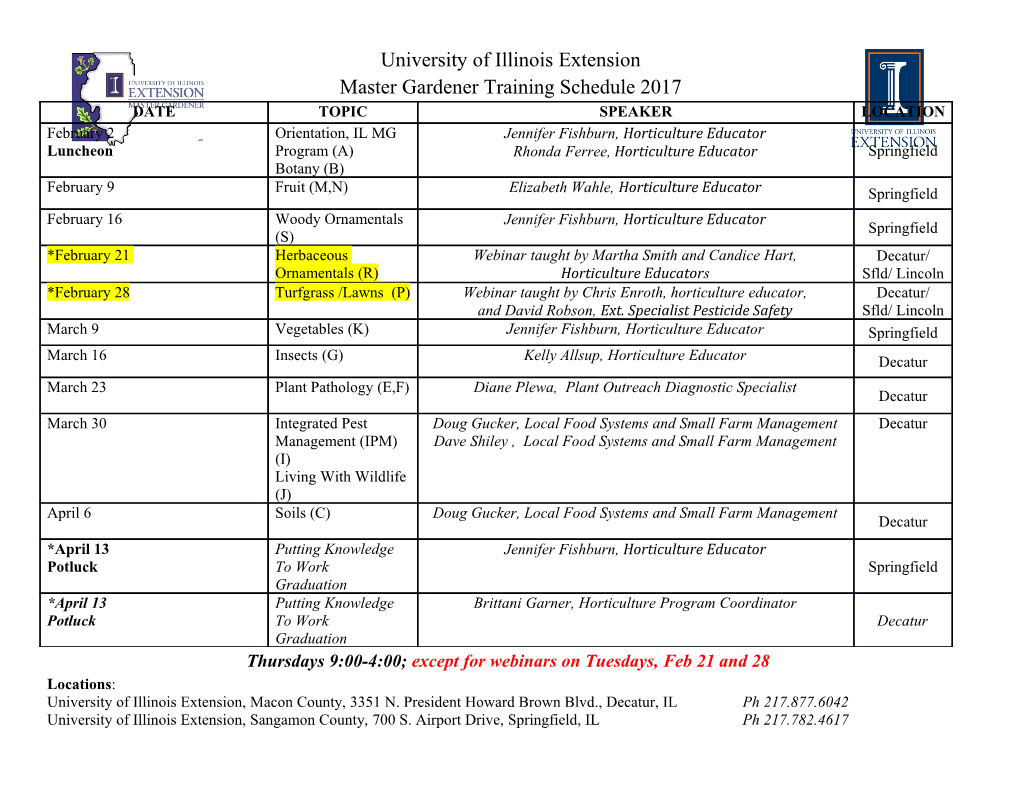
July 9, 1968 J. F. HERINK S. A. 3,391,991 PRODUCTION OF SODIUM TRIPOLYPHOSPHATE Filed Aug. 8. 1966 P4 4. SODM SR 12 G - AIR coa SESQUCARBONATE MY H2O - I - H2O O2N2 2 6 O P4 BURNER 8, H2O 4. R SODUM X-SSESQUICARBONATE is CO2 ho H2O 24 2 5R MONOSODIUM PHOSPHATE SOUTON Na Nos 26 8 2O 22 S. S. MONOSODUM PHOSPHATE SOLUTION MONOSODUM PHOSPHATE 3O DISODIUM PHOSPHATE SOLUTION H2O + COMBUSTION GAS STPP PRODUCT | WVEVTORS JOHN F. HERNK 'a-232.HAROLD J. COMERSA-2 3,391,991 United States Patent Office Patented July 9, 1968 2 mixture to at least 250 C., removing uncombined water 3,391,991 therefrom and recovering STPP from the heated reaction PRODUCTION OF SODIUM TRPOLYPHOSPHATE mixture. John Fred Herink, Rock Springs, and Harold J. Comer, Green River, Wyo., assignors to FMC Corporation, The use of aqueous slurries of sodium sesquicarbonate New York, N.Y., a corporation of Delaware in place of soda ash in the above process has been found Filed Aug. 8, 1966, Ser. No. 570,804 to have many advantages. Among these is that sodium 4 Claims. (CI. 23-107) sesquicarbonate does not result in as violent a reaction with phosphoric acid as Soda ash when forming a so The present invention is concerned with the formation dium phosphate solution. In addition, the sodium sesqui of sodium tripolyphosphate and, more specifically, to the carbonate, which contains 2 moles of water of crystalli manufacture of sodium tripolyphosphate in which the re 10 Zation per mole of sodium sesquicarbonate, requires the quired sodium values are derived from sources other than use of much less water since the water in the sesquicar Soda ash. bonate crystal is utilized in the process. Further, the In the formation of modern heavy-duty detergent com slurry of sodium sesquicarbonate which has a maximum positions sodium tripolyphosphate (STPP) has come into 5 pH of about 9.4 is much less alkaline and more easily widespread use as a phosphate “builder' in order to in handled than the comparable solution or slurry of soda crease the cleaning ability of these detergent composi ash which has a pH of about 12. tions. The general method for producing STPP is to re In carrying out the present invention a slurry of So act phosphoric acid (herein used to mean either the an dium sesquicarbonate and water is made up. The precise hydride POs or the acid itself) and sodium carbonate 20 ratio of sesquicarbonate to water is determined by the (soda ash) together in an aqueous solution until the specific gravity of the mixture which is desired to Sup mole ratio of sodium to phosphorus is of the order of ply the proper amount of sodium values per unit amount about 5:3. The reaction results in formation of an aque of phosphorus. In general a weight ratio of sodium ses ous mixture containing monosodium orthophosphate and quicarbonate to water of about 1:1 has been found de disodium orthophosphate in a mole ratio of about 1:2. sirable. This slurry is then reacted with either phosphoric The aqueous mixture is then passed through a heating acid or anhydrous phosphoric, acid, i.e., P2O5, to form zone and its temperature is increased to remove free a solution of monosodium phosphate. This reaction Oc water. At a temperature of about 250 C. or higher STPP curs in accordance with the following equation: is formed. The soda ash used in this process can be produced by 30 HO-2NaCO3 NaHCO2H2O) a number of methods including the classical Solvay or -- 3PO-> 6NaH2PO4-4CO2 ammonia-soda process or the sesquicarbonate system de The resulting monosodium phosphate Solution nor scribed in U.S. Patent 3,028,215 issued on Apr. 3, 1962 mally has a pH ranging from about 4.0 to about 4.6 and to William R. Frint. In this latter process crude trona a specific gravity on the order of about 1.5 to 1.7. To is dissolved in an aqueous solvent and the solution is this solution is then added additional amounts of the filtered and purified to remove natural impurities in the sodium sesquicarbonate slurry to convert enough of the mineral trona. Thereafter the solution is cooled and con monosodium phosphate to disodium phosphate in order centrated to precipitate monoclinic sodium sesquicarbon to obtain a solution whose sodium to phosphate mole ate crystals. These crystals are separated by a centrifugal ratio is about 5:3. This reaction occurs in accordance with separator from the mother liquor and are recovered as 40 the following equation: a centrifuge cake. The sesquicarbonate centrifuge cake is passed into a calciner and calcined in a nonreactive atmosphere at high temperatures until it is converted into dense soda ash (Na2CO3). The resulting solution should have a monosodium phos One drawback to using soda ash as a reactant with phate content of about 17%, a disodium phosphate con phosphoric acid is that the resulting reaction is difficult tent of about 40% and a specific gravity on the order of to control because substantial amounts of both carbon about 1.6. This solution is then fed into a heating Zone, dioxide and heat are evolved. In this reaction a concen such as a spray dryer, rotary kiln or fluidized bed where trated soda ash solution, which has a pH of about 12 or the water of solution is evaporated and the mixture of above, must be reduced by reaction with the phosphoric 50 imonosodium phosphate-disodium phosphate can react at acid to a pH of about 4.0-4.6 evolving copious amounts temperatures of at least about 250 C. to form the STPP of CO2 and releasing the large heat of neutralization. As product. Where desired, an oxidizing agent such as so a result there is a need for a system wherein a sodium dium nitrate may be added to the solution of monoso phosphate mixture can be made up under more easily dium phosphate and disodium phosphate to oxidize any controllable conditions and with less heat of neutraliza 55 organics or sulfides present in the mixture fed to the tion. heating zone. It is an object of the present invention to produce In the above description of the invention the slurry STPP in which the sodium values therein are supplied of sodium sesquicarbonate was added to the phosphoric by compounds other than soda ash. acid in two separate stages. While this two stage tech It is a further object of the present invention to re 60 Inique is preferred since it assures obtaining an initial act phosphoric acid with a sodium salt in which the re monosodium phosphate solution having the correct pH action is more readily controlled and in which less heat and specific gravity prior to conversion of a portion of of neutralization is evolved. the monosodium phosphate to disodium phosphate, it is This and other objects will be apparent from the fol to be understood that all of the required amount of Ses lowing disclosure. 65 quicarbonate can be added in one step. We have now found that STPP can be formed in a The invention will now be described by reference to the more readily controlled reaction by reacting phosphoric attached drawing which is a diagrammatical sketch of the acid with an aqueous slurry of sodium sesquicarbonate preferred process. in mole proportions sufficient to form a sodium phos As shown in the drawing a slurry of sodium sesquicar phate mixture having a sodium to phosphorus mole ratio bonate and water is prepared in mixing tank 2 and is on the order of about 5:3 and a specific gravity of from conveyed through line 4 to a holding tank 6. A portion about 1.5 to about 1.65, heating said sodium phosphate of the sodium sesquicarbonate slurry is then removed 3,391,991 3 4. from holding tank 6 through line 8 and passed into a spray dryer required 43 lbs. of natural gas to convert the phosphorus burner 10. In this unit phosphorus is ad mixture to about 1000 lbs. of STPP product. Overhead mitted into the top of the burner 10 through line 12. Air, from the spray dryer 929 lbs. of water and 740 lbs. of necessary to support the combustion of the phosphorus combustion gas was removed. is admitted through line 14 into the top of burner 0 along with the phosphorus. The phosphorus is burned Example 2 and produces the anhydride of phosphoric acid (P2O5) Elemental yellow phosphorus was burned in a phos in burner 10. The phosphoric acid anhydride is then re phorus burner with excess oxygen to form gaseous P2O5. acted with the sesquicarbonate slurry from line 8 to form The resultant POs was absorbed in an aqueous mono a monosodium phosphate solution. This solution is re sodium phosphate solution having a specific gravity of moved from the base of burner 10 through line 16 and O 1.605 and containing about 65.5% monosodium phos placed in a holding tank 18. The solution in holding tank phate. The monosodium phosphate solution was main 18 has a specific gravity of about 1.6 and its pH between tained at 99 C. and was recycled in the phosphorus 4.0 and 4.6. Incremental addition of sodium sesquicar burner at a ratio of about 230 parts per part of phos bonate or water to holding tank 18 may be necessary to 5 phorus burned. There was also added to the recycle stream adjust the pH or specific gravity of the solution. The 2.425 parts of sodium sesquicarbonate per part of phos monosodium phosphate solution is removed from hold phorus burned.
Details
-
File Typepdf
-
Upload Time-
-
Content LanguagesEnglish
-
Upload UserAnonymous/Not logged-in
-
File Pages4 Page
-
File Size-