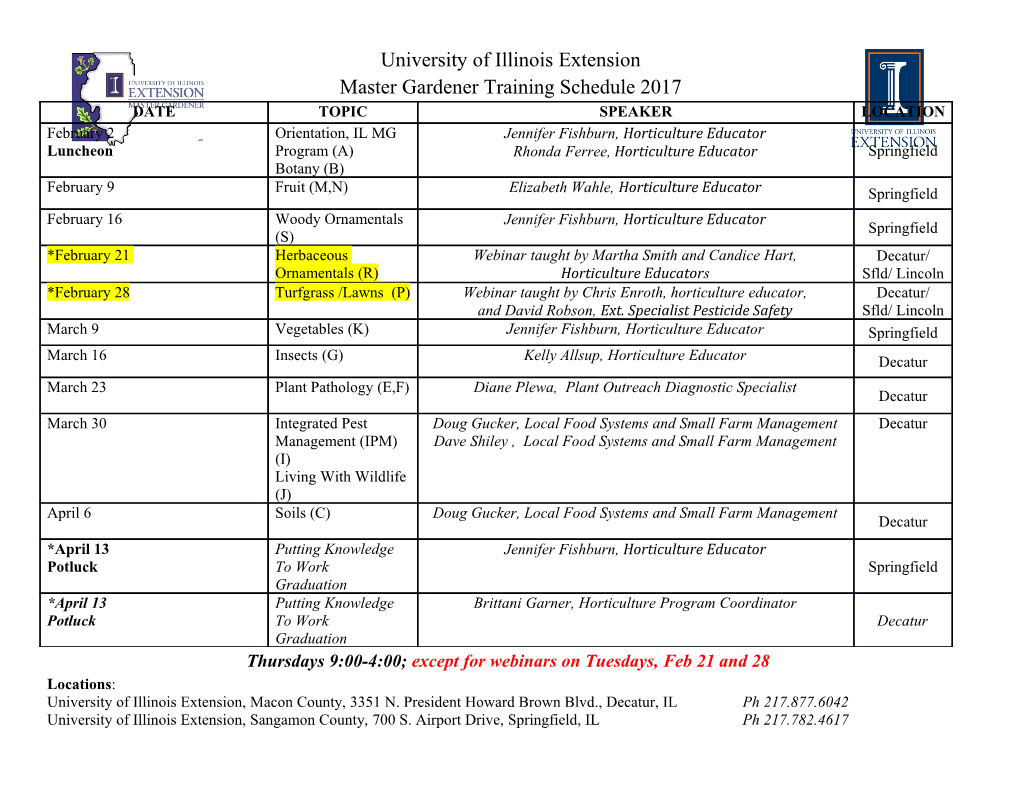
The Journal of the First Quarter - 2005 Reliability Analysis Center 5 Reliability Analysis of Avionics in the Commercial Reliability Theory Aerospace Industry Explains Human Aging and Longevity By: Jin Qin, Bing Huang, Joerg Walter, Joseph B. Bernstein, Michael Talmor Reliability Engineering, INSIDE University of Maryland, College Park 7 Abstract Data Collection Form, Fit, Function, The reliability of avionics using commercial-off- Return-for-service records were collected from and Interface - An the-shelf (COTS) items and products is a concern two major suppliers of avionics. Several types of Element of an Open for the aerospace industry. The results of collect- systems were included, such as a flight control System Strategy ing and analyzing field return records of avionics system, autopilot, flight director system, and are documented in this article. Our analysis symbol generator. Records from company A 14 shows that the exponential distribution is still include eight systems dating from 1982 to 2002. System Level Clues appropriate for describing the life of most avion- Company B’s records are dated from 1997 to for Detailed Part ics manufactured over the past 20 years. Results 2002 and include one system. Most of these Issues also show that failure rates decrease at the intro- records include the unit serial number, date sold, duction of products. An increasing trend in fail- return for service date, replaced IC types, and 19 ure rate can be noted, for systems made after quantities. Some of the original data were found New Markov Analysis 1994, suggesting the need for further investiga- to be insufficient for analysis. We compiled the Web Site tion. original records to weed out and discard the use- less ones; the remaining records had sufficient 19 Introduction data to support statistically significant conclu- RMSQ Headlines Microelectronic systems built with COTS are sions. We also made some assumptions to facil- now widely used in the aerospace industry and itate the statistical analysis. Our assumptions 21 are becoming increasingly important. After the were as follows. Future Events Department of Defense (DoD) changed the 22 acquisition process (one formerly based on mili- 1. Systems were grouped by type and the From the Editor tary standards and specifications) in 1994, mili- year of “date sold” assuming they were tary-specified avionics have become rare. The manufactured and used in the same year. 23 aerospace industry’s use of microelectronics is 2. For units with multiple returns, only the shrinking as a percentage of the entire market, so first return was calculated and analyzed. PRISM Column it must face the reality of a commercially-driven 3. It is assumed that all ICs replaced in serv- market. Commercial integrated circuit (IC) prod- ice have experienced failure. This 23 ucts’ life cycles are decreasing to 2-4 years assumption may have caused us to over- Upcoming June [Reference 6]. In contrast, the aerospace indus- estimate the number of failures. Training try assumes the life of a Line Replacement Unit 4. Censor time: the time to check the status (LRU) is more than 10 years. This discrepancy of system. It is set to April 30, 2002. will worsen given the continuing advancement in functionality and speed in the microelectronic Based on these assumptions, a C language pro- industry. To understand the impact of technolo- gram was used to select the useful records, check gy advancement on avionics, we needed to find the end status of the systems, and calculate the out what had happened in field operation. Field service hours. The method used to calculate the records of return-for-service of avionics in the service hours follows Figure 1, in which the dif- past 20 years were collected and analyzed, and ferent periods between sold date and return-to- the results are documented herein. service date are shown. RAC is a DoD Information Analysis Center Sponsored by the Defense Technical Information Center The Journal of the Reliability Analysis Center distribution of the time between equipment failures tends to the P1 P2 P3 exponential as the complexity and the time of operation increas- es; and somewhat less generally, so does the time up to the first SD BISD FD RTSD failure of the equipment.” SD – Sold Date, BISD – Begin In Service Date, Weibull Shape Parameter Histogram FD – Failure Date, RTSD – Return To Supplier Date Figure 1. Time Line of Field Records 16 14 The P1 interval between SD and BISD includes delivery time and 12 installation time. The unit service period (days), P2, is: 10 P2 = (RTSD - SD) - P1 - P3 (1) 8 6 Frequency P3 is the return time from customers to suppliers. If the unit did 4 not fail to the censor time, the service period is between BISD 2 and the censor time. Generally, there are only SD and RTSD in 0 the raw records. P1 and P3 are estimated based on the informa- tion given by the suppliers. Different suppliers have different P 0.3 0.5 0.7 0.9 1.1 1.3 1.5 1.7 1.9 2.1 2.3 2.5 2.7 2.9 3.1 3.3 3.5 3.7 1 Beta and P3. Once P2 is found, the unit service hours are calculated from: ServiceHours = Hon * P2. The Hon is the power-on hours Figure 2. Weibull Shape Parameter Histogram per day of system. Different companies give different Hon. In the microelectronic industry, due to the advance of technology, Data Analysis chips are becoming more and more complex following Moore’s Analysis of System Records from Company A. There are law. Additionally, avionics have complex structures. A flight records for about 21,535 systems sold between August 17, 1982 director system may consist of 460 digital ICs, 97 linear ICs, 34 and December 30, 2001 from company A. Categorized by sys- memories, 25 ASICs, and 7 processors. The number of compo- tem type and year of “date sold,” there are 87 groups of data, nents in such a system is huge. For these components, external which include 9 groups with zero failures and 6 groups with one failure mechanisms caused by random factors such as electrical failure. The statistical analysis process and results follow. overstress, electrostatic discharge, and other environmental and human interaction, and intrinsic failure mechanisms, which Probability plotting. As the generally accepted lifetime distribu- include dielectric breakdown, electromigration, and hot carrier tion in microelectronic industry, Weibull distribution is used to injection, can cause the components to fail. These failure modes analyze the service hours. To verify its usage, we plotted proba- combine together to form a constant failure rate process, as bility and calculated the correlation coefficient (CC) of Weibull Abernethy [Reference 2] stated that as the number of failure modes distribution and lognormal distribution respectively (Groups mixed together increases to five or more, the Weibull shape param- with 0 or 1 failure are omitted). Results show that the CC for 42 eter will tend toward one unless all the modes have the same shape groups of Weibull distribution was greater than the CC for the parameter and similar scale parameter. Some recent research that lognormal distribution. The CCs of Weibull distribution were focuses on intrinsic wearout failure mechanisms lends support to also compared with the 90% critical CC [Reference 1] to deter- the exponential distribution. Degraeve [Reference 4], Stathis mine if the distribution is appropriate or not. Results show that [Reference 7], and Alam [Reference 3] pointed out that the Weibull 62 of 72 groups CC was greater than the given critical CC. shape parameter of oxide breakdown is thickness dependent and goes to unity for ultra-thin oxides. As the Weibull shape parame- Parameter estimation. The parameters of Weibull distribution ter approaches 1, the intrinsic wearout becomes more random and are estimated by using the maximum likelihood estimation the device times to failure become statistically indistinguishable (MLE) method. The histogram of the estimated shape parame- from a random pattern of times to failure. ters is shown in Figure 2. It shows the values of most of the shape parameters are distributed between 0.6 and 1.1. We use the likelihood ratio test to verify the hypothesis of the exponential distribution – the special case of Weibull distribution Exponential distribution verification. Although the wide use with the shape parameter equals to 1. Setting the significance of exponential distribution has been questioned for a long time, level to 0.05, for systems grouped in different years, the likeli- it is unwise to blindly accept or reject it. The exponential distri- hood ratio test is done using the following steps. bution was theoretically shown to be the appropriate failure dis- β β≠ tribution for complex systems by R.F. Drenick [Reference 5]. a. H0: = 1; H1: 1 He stated that “Under some reasonably general conditions, the 2 First Quarter - 2005 The Journal of the Reliability Analysis Center ˆ ˆ b. Calculate the statistics T = 2( L - L 0 ) the trend of system reliability increase around 1994 and after that, Lˆ : global maximum log likelihood could be noted. System 1 shows the same trend around 1997. Lˆ : constrained maximum log likelihood at β = 1 0 Analysis of system records from company B. Records from c. If, T < χ2 (0.95, 1), accepts H , else rejects H . 0 0 company B are dated between January 14, 1988 and October 27, The hypothesis test results show that exponential distribution is 2001. Since the population size and the failure number of each acceptable for 56 groups. year are small, we statistically analyze the moving five-year’s records using the exponential distribution to get better results. System failure rate results. Since the exponential distribution is We also analyze all records of company A in the same way to appropriate for most of those systems, we use MLE to calculate compare the change in reliability.
Details
-
File Typepdf
-
Upload Time-
-
Content LanguagesEnglish
-
Upload UserAnonymous/Not logged-in
-
File Pages24 Page
-
File Size-