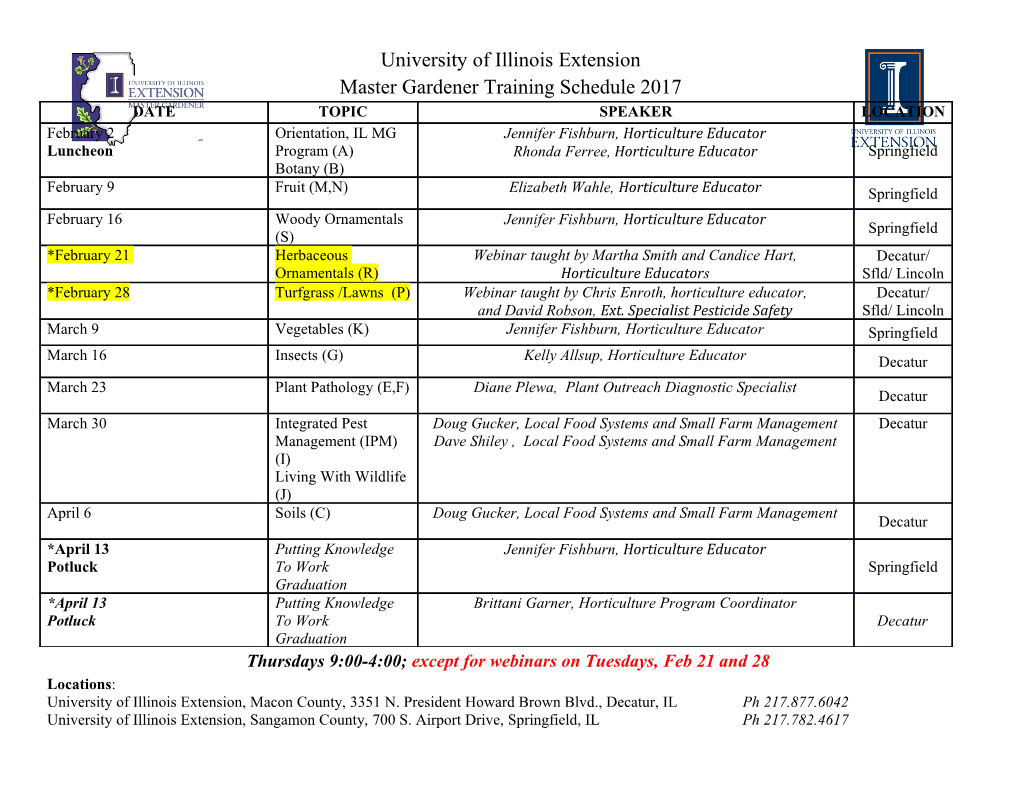
2014 Bearcats Baja Rear Suspension System A Baccalaureate thesis submitted to the Department of Mechanical and Materials Engineering College of Engineering and Applied Science University of Cincinnati In partial fulfillment of the Requirements for the degree of Bachelor of Science In Mechanical Engineering Technology By: Zack Freije April 2014 Thesis Advisor: Dean Allen Arthur 2014 Bearcats Baja – Rear Suspension System Zack Freije Rear Suspension Copyright © 2007 SAE International ABSTRACT Each vehicle is evaluated in terms of ergonomics, functionality, and producibility. To this end, design Baja SAE is an annual intercollegiate engineering design reports must demonstrate both sound engineering competition organized by the Society of Automotive principles as well as economic feasibility for Engineers, and serves as a capstone project for senior production. Mechanical Engineering Technology students at the University of Cincinnati. The 2014 Bearcats Baja team An off-road vehicle’s suspension system serves three vehicle is a complete new build from the ground up. This primary functions: to maintain tire contact with the design freedom allows for drastic improvements over the ground while the vehicle navigates rough terrain, to 2013 rear suspension system performance. Extensive reduce impact forces transferred to the driver, and to research was conducted to determine the key provide optimal vehicle handling dynamics. (1) performance metrics for the system. Several design options were considered and a final design was selected RESEARCH based on system integration, manufacturability, system weight, cost, and design specifications required to meet Full compliance with all relevant Baja SAE rules is the performance metrics. Failure modes were required. The applicable rules have been supplied in established based on 2013 in-use performance results. Appendix B. (2) FEA optimization was performed side by side with the 2013 system to establish a baseline for improved stress A list of reference material used for concept and handling while optimizing weight. The final design was application of design are given in Additional Sources. produced with a 22% cost savings, 7% weight reduction, and was verified to within 0.5° for toe/camber angle and Great attention was placed on the design and within 1/16” for all setting dimensions relative to performance of the 2013 rear suspension system during established design specifications. competition. In addition, a careful survey of design choices was conducted for all the top 10 teams during INTRODUCTION competition in 2013. Time was spent discussing the merits of these choices with the competing teams to gain Baja SAE is an annual intercollegiate engineering design a better understanding of the engineering justification. competition run by the Society of Automotive Engineers (SAE). Teams of students from Universities around the Five primary design choices were identified for further world design and build small off-road vehicles powered study: by engines with identical specifications. Single rear inboard brake – eliminates need for All teams must adhere to the rules and pass SAE’s heavy bearing carrier to support caliper, reduces technical and safety inspections. At each competition total vehicle weight. there are design evaluations and multiple dynamic events followed by a four-hour endurance race. Dynamic Trailing arm integrated bearing carrier – a simple events for 2014 include maneuverability, rock crawl, and and lightweight bearing carrier can be welding into suspension & tracking. The endurance race carries the the trailing arm to reduce weight, complexity and single largest point total. These events require a hardware. suspension that is agile as well as robust. Custom aluminum wheel hub – a simple and Furthermore, each team is competing to have its design lightweight hub can be manufactured for custom selected by a theoretical power sports manufacturing backspacing. Can eliminate rotor mounting bosses company with the stated intent of a 4,000 unit annual and hardware. production volume. Each team is responsible for all phases of the research and development process, from Narrow rear chassis/Longer control arms – fundraising to designing, manufacturing and testing. Reduce length of heavy frame tubes. Increase 2 length of lateral links to provide better control over camber change rate. Minimize size of heim joints/Mount in double shear – Heim joints can be reduced in size if proper calculations are made to determine the worst case forces. Mount them in double shear to reduce bending moment on the threads. Example pictures for these design cues are given in Appendix C. Figure 3 – Pitch Conditions The primary levers for improving rear suspension 20-30% antisquat is preferred. This increases the normal performance are: force at the tires and improves acceleration. Antisquat also increases suspension stiffness, producing jacking forces similar to an anti-roll bar without reducing body Toe Settings roll. Camber Settings Pitch Settings ROLL AXIS Roll Axis TOE SETTINGS Figure 4 – Roll Center Height Figure 1 – Toe Conditions Low roll center height is ideal as this leads to lateral acceleration weight transfer via body roll. Roll center Positive toe is preferred. For a rear wheel drive car, rear axis ideally slopes down towards the front of the vehicle toe-out leads to overseer which promotes a faster which allows for weight transfer to the front of the vehicle maneuverability response. Static toe or no change in toe during a turn. This allows more grip on the steering tires angle over the suspension travel is preferred. Dynamic and allows the rear end to break free and slide which or changing toe leads to bump steer. creates oversteer. CAMBER SETTINGS DESIGN SELECTION - Early design concepts that were rejected include: dual a-arm, torsion bar, inboard shock, single tube trailing arm, toe control link. It was observed at competition that failure of any part of a dual a-arm setup would result in disengagement of the drive axle, rendering the vehicle immobile and costing valuable time being towed into the pits. The 2013 Bearcats vehicle sustained complete failure to one of the lateral links during an endurance race, but was able to complete a lap and drive into the pits under its own power. It was determined that torsion bars add weight and complexity Figure 2 – Camber Conditions and attempt to correct for problems with the initial suspension design. Toe control links added weight and Negative camber is preferred. Negative camber leads to complexity, but were unnecessary because the straight line stability. Static camber or no change in suspension could be designed such that optimal toe was camber angle over the suspension travel is preferred. achieved without them. The single tube trailing arm was a lead option until it was determined that SAE chassis PITCH SETTINGS rules made the desired mounting location impossible. It was also considered that a single tube would have 3 greater potential to fail due to buckling after impacting DESIGN SPECIFICATIONS - The following constitutes a stationary objects on course. complete list of the selected design specifications to achieve with this rear suspension system design. The selected design incorporates a semi-trailing arm and a pair of lateral links. This is similar to the suspension Vertical Wheel Travel: 10.6” (269.2mm) used on an Integra Type R. This is the third year Recessional Wheel Travel: 0.5” (12.7mm) Bearcats Baja has used and improved this general Static Ground Clearance: 11” (279.4mm) design. Jounce Ground Clearance: 4” (101.6mm) Static Roll Center: 8” (203.2mm) Motion Ratio: 0.5 Sag: 33% of total travel Total Track Change: 4” (101.6mm) Track Change in Roll: 0” (0mm) Static Toe: 0 deg Toe Change Rate: 0.5 deg/in Static Camber: -0.5 deg Camber Change Rate: 0.25 deg/in Percent Anti Squat: 20%-30% System Weight: 50 lbs (22.7 kg) SYSTEM INTEGRATION – To accomplish the design specifications, both system integration and rules Figure 5 – Selected Design compliance were key factors. System integration required collaboration with braking, drivetrain, chassis, and front suspension systems. To reduce the weight for the rear suspension, the brakes were moved inboard, allowing for elimination of the purchased bearing carrier. A new custom bearing carrier was integrated into the trailing link. The Rear Roll Hoop was lengthened, lowering the drivetrain and vehicle CG, and optimizing the angle of the axles for increased power transfer and reduced plunge travel. In addition, the Rear Roll Hoop was made laterally narrow rearward of the gearbox to allow for longer trailing links which provide the desired camber change rate. Initial design concepts for trailing link geometry and mounting locations were rejected due to rules compliance for the Roll Hoop. Figure 6 – Axle Section View WEIGHT - The wheels and tires represent 61% of the DESIGN GOALS total system weight. However, weight was increased by 2% over last year for reliability. Previously, Douglas Blue PRIMARY OBJECTIVES Label (0.125” wall) were used, however all were bent during normal use. To improve this, ITP T9 Pro (0.190” Improve handling response* wall) were selected which are considerably stronger and Reduce Weight weigh 0.38 lbs more per corner. The same lightweight Reduce Cost 23x7-10 Carlisle 489 tires were selected due to their performance at competition. Selecting a stiffer wheel will *Handling Response - Dynamic handling is subjective, mitigate the negative impact of the 2-ply tire. and prior to testing, is largely theoretical with respect to design. Each driver will have a handling preference and A reduction of 4 lbs (7% of total system weight) was each overall vehicle will respond differently to the same achieved by replacing the Polaris Sportsman 300 design. Course design and conditions also play a factor. bearing carrier with a custom carrier that was integrated Holistic handling response takes into account the into the trailing link. The new bearing carrier was interaction between the front and rear suspension designed around a Honda TRX420 which allowed for designs.
Details
-
File Typepdf
-
Upload Time-
-
Content LanguagesEnglish
-
Upload UserAnonymous/Not logged-in
-
File Pages34 Page
-
File Size-