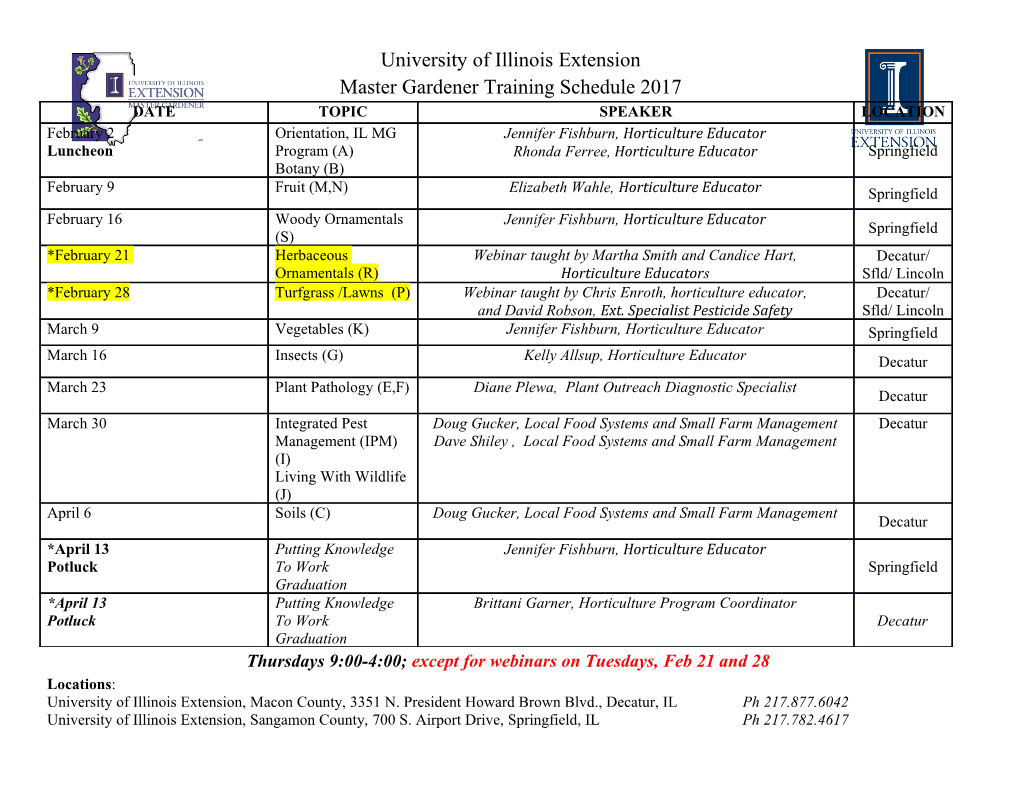
Dipl.-Ing. Nicolas Coniglio Aluminum Alloy Weldability: Identifi cation of Weld Solidifi cation Cracking Mechanisms through Novel Experimental Technique and Model Development BAM-Dissertationsreihe • Band 40 Berlin 2008 Die vorliegende Arbeit entstand an der BAM Bundesanstalt für Materialforschung und -prüfung. Impressum Aluminum Alloy Weldability: Identifi cation of Weld Solidifi cation Cracking Mechanisms through Novel Experimental Technique and Model Development 2008 Herausgeber: BAM Bundesanstalt für Materialforschung und -prüfung Unter den Eichen 87 12205 Berlin Telefon: +49 30 8104-0 Telefax: +49 30 8112029 E-Mail: [email protected] Internet: www.bam.de Copyright © 2008 by BAM Bundesanstalt für Materialforschung und -prüfung Layout: BAM-Arbeitsgruppe Z.64 ISSN 1613-4249 ISBN 978-3-9812354-3-2 Aluminum Alloy Weldability: Identification of Weld Solidification Cracking Mechanisms through Novel Experimental Technique and Model Development Dissertation zur Erlangung des akademischen Grades Doktor-Ingenieur (Dr.-Ing.) genehmigt durch die Fakultät für Maschinenbau der Otto-von-Guericke-Universität Madgeburg am 02.06.08 vorgelegte Dissertation von Dipl.-Ing. Nicolas Coniglio Thesis Committee: Prof. Dr.-Ing. A. Bertram Prof. Dr.-Ing. T. Böllinghaus Prof. C.E. Cross Prof. S. Marya Date of Examination: 23 October 2008 Abstract Abstract The objective of the present thesis is to make advancements in understanding solidification crack formation in aluminum welds, by investigating in particular the aluminum 6060/4043 system. Alloy 6060 is typical of a family of Al-Mg-Si extrusion alloys, which are considered weldable only when using an appropriate filler alloy such as 4043 (Al-5Si). The effect of 4043 filler dilution (i.e. weld metal silicon content) on cracking sensitivity and solidification path of Alloy 6060 welds are investigated. Afterwards, cracking models are developed to propose mechanisms for solidification crack initiation and growth. Cracking Sensitivity. Building upon the concept that silicon improves weldability and that weldability can be defined by a critical strain rate, strain rate-composition combinations required for solidification crack formation in the Al- 6060/4043 system were determined using the newly developed Controlled Tensile Weldability (CTW) test utilizing local strain extensometer measurements. Results, presented in a critical strain rate – dilution map, show a crack – no crack boundary which reveals that higher local strain rates require higher 4043 filler dilution to avoid solidification cracking when arc welding Alloy 6060. Using the established crack - no crack boundary as a line of reference, additional parameters were examined and their influence on cracking characterized. These parameter influences have included studies of weld travel speed, weld pool contaminants (Fe, O, and H), and grain refiner additions (TiAl3 + Boron). Each parameter has been independently varied and its effect on cracking susceptibility quantified in terms of strain rate – composition combinations. Solidification Path. Solidification path of the Al-6060/4043 system was characterized using thermal analysis and phase identification. Increasing 4043 filler dilution from 0 to 16% in Alloy 6060 arc welds resulted in little effect on thermal arrests and microstructure, no effect on solidification range, refinement in grain size from 63 to 51 μm, centerline columnar grains disappearance, and decreased cooling rate from 113 to 89 °C/s. Moreover, in order to make direct comparison with literature, castings of controlled mixtures of alloys 6060 and 4043 were also investigated, thereby simulating weld metal composition under controlled cooling conditions. Castings showed a different trend than welds with small increases in silicon content (i.e. increase in 4043 filler dilution) resulting in huge effect on microstructure, no effect on liquidus temperature, drop in solidus temperature from 577°C to 509°C, increase in quantity of interdendritic constituent from 2% to 14%, and different phase formation. Binary β-Al5FeSi, Mg2Si, and Si phases are replaced with ternary β-Al5FeSi, π−Al8FeMg3Si6, and a 5 Abstract low melting quaternary eutectic involving Mg2Si, π, and Si. Also, variation of the cooling conditions in castings revealed the existence of a critical cooling rate, above which the solidification path and microstructure undergo a major change. Cracking Model. Implementing the critical conditions for cracking into the Rappaz- Drezet-Gremaud (RDG) model revealed a pressure drop in the interdendritic liquid on the order of 10-1 atm, originating primarily from straining conditions. Since, according to literature, a minimum of 1,760 atm is required to fracture pure aluminum liquid (theoretical), this demonstrates that cavitation as a liquid fracture mechanism is not likely to occur, even when accounting for dissolved hydrogen gas. Instead, a porosity-based crack initiation model has been developed based upon pore stability criteria, assuming that gas pores expand from pre-existing nuclei. Crack initiation is taken to occur when stable pores form within the coherent dendrite region, critical to crack initiation being weld metal hydrogen content. Following initiation, a mass-balance approach developed by Braccini et al. (2000) revealed that crack growth is controlled by local strain rate conditions. Finally, a simplified strain partition model provides a link between critical strain rates measured across the weld and predicted at grain boundaries within the mushy zone. Although based on simplified assumptions, predicted and measured critical strain rate values are of the same order of magnitude. However, because of a longer mushy zone experienced at higher 4043 filler dilution related to a reduction in cooling rate, these models predict a lower weldability with increasing filler dilution, in contradiction with experimental observations. Combining the crack initiation and growth models suggests that hydrogen and strain rate, respectively, determine crack formation. An hypothetical hydrogen – strain rate map defines conceptually the conditions for cracking, suggesting better weldability at low weld metal hydrogen content. With the aid of the modified varestraint test (MVT) and a controlled hydrogen contamination system, results, presented in the form of ram speed – hydrogen map, revealed that hydrogen has little effect on crack growth, providing support to the proposed cracking models. However, a drop in weldability corresponding to the peak in weld metal hydrogen supersaturation suggests a different solidification cracking mechanism, where cavitation supports crack growth. 6 BAM-Dissertationsreihe Acknowledgements Acknowledgements The present work was funded by and carried out at the Bundesanstalt für Materialforschung und –prüfung (BAM) laboratory in Berlin, Germany, during the 2005-2008 time frame. I am grateful to Prof. C.E. Cross for having directed my thesis research. I am also grateful to Prof. Dr.-Ing. H. Herold and Dipl.-Ing. M. Streitenberger for my enrolment in the doctoral thesis program at the Institute for Materials and Joining Technology, Otto-von- Guericke-Universität Magdeburg, and to Prof. Dr.-Ing. T. Böllinghaus for the organization of the thesis defense. I am grateful to BAM for internal support of this project, and specifically wish to thank R. Breu, P. Friedersdorf, A. Hannemann, C. Hesse-Andres, F. Köhler, M. Lammers, M. Marten, T. Michael, M. Richter, K. Scheideck, K. Schlechter, W. Österle, G. Nolze, I. Dörfel, R. Neumann, and H.-J. Malitte. Also, material donated by Outokumpu Stainless and Metallurg London was greatly appreciated. I thank A. Cichon for the logistical support. I thank the thesis committee, Prof. Dr.-Ing. A. Bertram, Prof. Dr.-Ing. T. Böllinghaus, Prof. C.E. Cross, and Prof. S. Marya, for evaluating the thesis manuscript. Finally, this thesis is dedicated to Siegfried and Sonia Ramaut, my sister Charlène, my mother Evelyne, and my grand-mother Anna, to thank them for their support during all these years. 7 Table of Contents Table of Contents Abstract ................................................................................................................................5 Acknowledgements..............................................................................................................7 1 Introduction ................................................................................................................11 1.1 Aluminium Alloy Application ..................................................................................11 1.2 Al-Mg-Si Alloy System...........................................................................................12 1.3 Objectives and Methodology.................................................................................12 2 Background ................................................................................................................15 2.1 Solidification Cracking Phenomenon.....................................................................15 2.1.1 Solidification Cracking Characteristics...........................................................15 2.1.2 Solidification Cracking Models.......................................................................19 2.1.3 Liquid Fracture Mechanism ...........................................................................38 2.1.4 Semi-Solid Material Behavior Characterization..............................................46 2.1.5 Weldability Characterization ..........................................................................48
Details
-
File Typepdf
-
Upload Time-
-
Content LanguagesEnglish
-
Upload UserAnonymous/Not logged-in
-
File Pages208 Page
-
File Size-