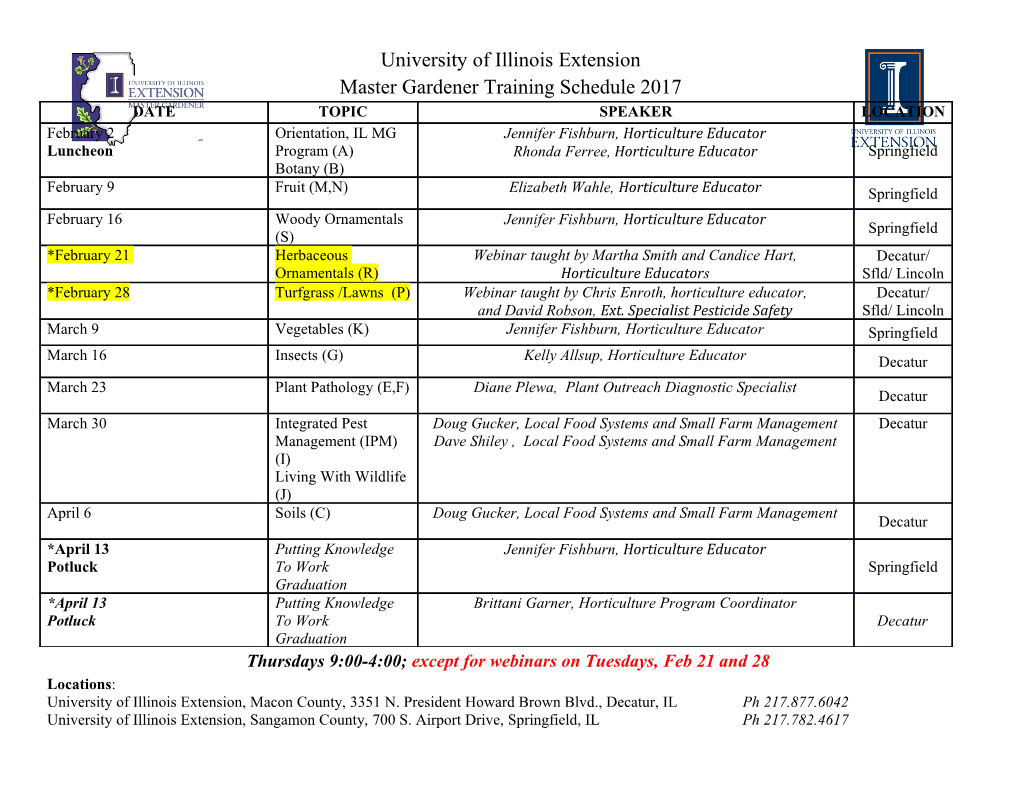
PAPER EXPERIMENTING AND SIMULATING THERMOELECTRIC COOLING OF AN LED MODULE Experimenting and Simulating Thermoelectric Cooling of an LED Module http://dx.doi.org/10.3991/ijoe.v11i4.4692 Mika Maaspuro Aalto University, Aalto, Finland Abstract — Use of a thermoelectric component (TEC) for an mounted on the hot side. TEC is a small size and a LED module cooling will be studied. The issue will be relative inexpensive component. Therefore TECs are approached by revealing the operation of a thermoelectric widely used in many applications. component known also as Peltier element, and the main equations describing its behaviour. An experimental setup TEC has some significant drawbacks. It does not fit well including an LED module, a TEC, an heatsink and a fan will be build. Heat dissipation and the electrical performance in high efficiency devices. Efficiency is related to figure- measurements of the hole experimental setup will be of-merit ZT, which for present day TEC is close to 1 [2]. conducted. The benefits and the limitations of TEC used in Efficiency is the highest at negligible output power level cooling, will be revealed. Cooling effect versus used but reduces at higher levels [3]. TEC generates Joule electrical power will be studied. 3D thermal simulations for heating according to its ohmic resistance and the electric the experimental setup using a FEM simulation software current which flows through it. This heat must be will be presented. Alternatively, a standard circuit simulator removed also by the HS or the HSF mounted on the TEC. will be used. A spice model, which imports TEC's Use of TEC as an active cooling device for LEDs has parameters from the data sheet, will be developed. The spice been studied by authors [4-6]. In those studies, TEC is simulation results are compared with the experimental results. used with passive cooling devices. Compared with passive cooling alone, the addition of TEC makes it Index Terms — FEM-simulations, LED thermal manage- possible to reach much lower LED junction temperature. ment, thermoelectric cooling. Using TEC as part of a cooling system can be a practical solution in some specific applications of LED lighting. Applications were the lighting device should remain at I. INTRODUCTION very low temperature. Applications where extremely Thermal management is important for maintaining a stable light levels and fast lighting control are requested. stable light production and lifetime of an LED. Reduction Applications where long operation life and maintenance in the LED junction temperature increases the light free operation are requested. The most common production and extends the lifetime. Proper thermal application of TEC in LED lighting might be a light management requires the use of heat dissipation device. source for microscopy use where both the light intensity These can be either passive or active devices. The active and the wavelength stability are requested. heat dissipation devices, practically cooling devices, are fans, microchannel coolers, heat exchangers and thermoelectric components (TEC). Usually active heat II. THERMOELECTRIC COMPONENT dissipation requires the use of some passive cooling devices, most often heatsinks. A heat pipe is a very TEC is able to generate temperature difference !T efficient cooling device. Using a heat pipe with TEC has between its cold and hot side. While the electric current been studied by [1]. A heatsink (HS) as a single cooling flows through the component, the cold side gets cooler device is widely used as well. Heatsink with a fan (HSF) and the hot side warmer. By reversing the direction of the is a widely used cooling arrangement. This study focus electric current, reverse the cold and sides as well. Just a on the cooling arrangements which use either HS, HSF or few equations are needed to describe the operation of TEC with HSF. TEC. The equations for the heat flow through the cold qc and the hot side qh are: TEC has some good characteristics. The cooling effect is fast. Without moving parts, TEC provides silent and maintenance-free operation. TEC can cool LED even !T 1 2 qc = + #m T c I ! I Rm (1) below the ambient temperature. This is not possible by " m 2 using HS or HSF. TEC is a solid state device of high reliability having MTBF higher than 100 000 hours. Its !T 1 2 q = + # T I + I R (2) MTBF is in the same range as LED's. TEC features high h m h m " m 2 stability and it is accurately controlled by the electric current which flows through it. The effective use of TEC While an electric current I flows through the component, requires HS, HSF, or some other heat convection device a voltage V will be measured over it. iJOE ‒ Volume 11, Issue 4, 2015 47 PAPER EXPERIMENTING AND SIMULATING THERMOELECTRIC COOLING OF AN LED MODULE reached at low air speed and therefore the fan is operated V = #m T h !#m T c =#m !T (3) at 0.5W. The hole setup stands on bars which are thermally isolated from the setup and from the -1 Where "m is the Seebeck coefficient, #m the thermal environment. For temperature measurements, there are resistance of the element and Rm is the electrical fixtures for type K thermo-couples on each aluminium resistance of the element. TEC is made of N pellets, plate and on the heatsink. Resolution in the temperature which are made of suitable semiconductor material, most measurements is ± 1 °C, but accuracy is better than this. often bismuth telluride. These pellets are arranged by pairs, each of them has one n-type and one p-type The setup uses an LED driver, which is controlled by component. All the pellets are connected electrically in computer software via DALI, Digital Addressable series and thermally in parallel. This means the total "m' = Lighting Interface. The benefit of DALI control in this N$"m, Rm' = N$Rm and #m' = #m/N. Equations (1-3) are experiment is that power settings can be done and able to explain the basic operation of TEC. Normally, repeated accurately. The maximum electrical power the some other equations are presented to better qualify the driver can source for the LED module is 15.2 W. TEC. The general quality of TEC is the figure-of-merit, Measurements have been done at four input electrical ZT which is defined as power levels. # " ZT = m m (4) Rm High ZT is desired. For a high value of ZT, both the Seebeck coefficient and thermal resistance should be maximized and at the same time Rm should be minimized. Another measure for the quality of TEC is the coefficient of performance COP. This is defined as qc Figure 1. The LED module, the aluminium plates, the TEC, the COP = 2 (5) heatsink, the fan, and the thermocouples. The system is standing on a m I!T+ I Rm thermally isolated bars. It can be seen from Equ. 5 that Joule heating generated by the electrical resistance Rm is the major reason which reduces COP. COP gives a measure of how much heat can be absorbed on the cool side at certain temperature difference !T and electric current I. Material characteristics are temperature dependent [7]. The review study of bismuth telluride [2] shows that maximum ZT can be even 1.5 for p-type and 1.2 for n-type material, and the maximum is reached at elevated temperatures. III. EXPERIMENTAL WORK For the experimental work, a setup shown in Fig. 1. has been manufactured. It has an LED module mounted on a thick aluminium plate. The LED module is type Xlamp CXA2011 (Cree). The aluminium plates serve as a heat spreaders and they are made wide enough that temperature sensors can easily be mounted on it. The TEC module can be mounted on the aluminium plate. The TEC module is type TEC1-12706 (Hebei I.T Co. Ltd. Shanghai). It has dimensions of 40 mm x 40 mm x 3.9 mm and its Qmax is specified to 57 W. Above the Figure 2. The measured setups. a) LED, aluminium plate and heatsink. TEC, there is another aluminium plate. A finned heatsink b) LED, aluminium plate and fan. c) LED, two aluminium plates, TEC, heatsink and fan. TIM is used between the LED and the plates and is mounted on the aluminium plate. The heatsink has between the plates and the TEC and between the plate and the heatsink. dimensions of 60 mm x 60 mm x 35 mm. Small amount The heatsink has size of 60 mm x 60 mm x 35 mm. The aluminium of thermal interface material (TIM) is used between the plates have size of 50 mm x 50 mm x 5 mm. surfaces. Standard silicone based cream has been used. Top of the heatsink is a fan. The maximum electrical power of the fan is 2 W. An efficient cooling effect can be 48 http://www.i-joe.org PAPER EXPERIMENTING AND SIMULATING THERMOELECTRIC COOLING OF AN LED MODULE (TIM). Fig. 5 shows how the junction temperature changes versus the electric current of the TEC with four LED power levels. At all power levels, the minimum junction temperature will be reached at electric current between 2 and 2.5 A. In Fig.6, these results are compared with the case where only the heatsink and the fan are used. Fig. 6 shows the benefit the TEC provides. It can be seen that due to the added aluminium plate, the TEC and the additional TIM layer in case c, some cooling effect of TEC is needed to reach the same cooling effect of case b. By using the optimal TEC electric current the junction temperature can be reduced at every power level of the LED.
Details
-
File Typepdf
-
Upload Time-
-
Content LanguagesEnglish
-
Upload UserAnonymous/Not logged-in
-
File Pages8 Page
-
File Size-