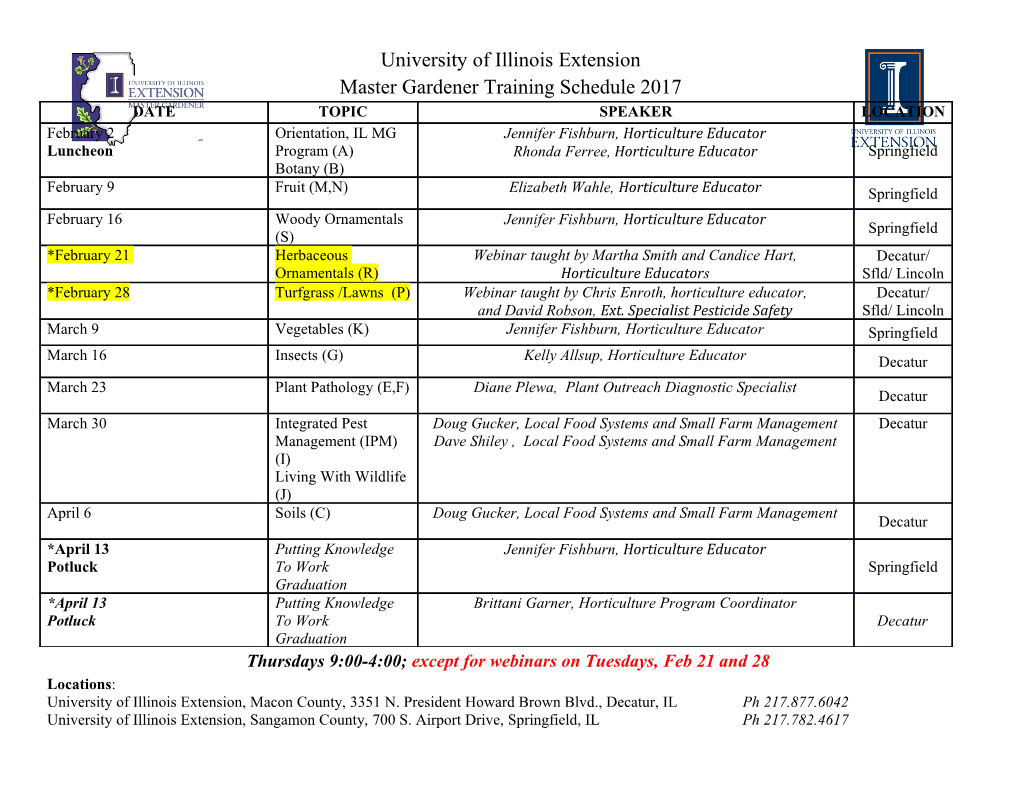
PERFORATION | FABRICATION | INNOVATION Since 1876, Hendrick has been innovating perforated metal solutions for YOUR a wide range of industries. Our expertise is unparalleled in the industry. The broad based knowledge that comes from working with multiple industries gives PERFORATION us a unique perspective on the latest manufacturing technologies and applications. AND Our capabilities go way beyond perforation. We offer an array of high-tech fabrication FABRICATION options that can eliminate labor, time, and provide cost-savings for your completed assembly. Plus, our extensive range of services go one step further with partial to EXPERTS complete turn-key contract assembly operations. Carbondale, PA Perforation & Fabrication Northeast Plant Elgin, IL Owensboro, KY Perforation & Fabrication Profile/Wedge Wire & Fabrication Midwest Plant Southern Plant With three ISO 9001 certified manufacturing locations, we can provide manufacturing flexibility to get product to you faster with minimized shipping costs. Plus, our large material inventory provides shortened lead times. 2 PUT HENDRICK’S BROAD-BASED EXPERTISE TO WORK ON YOUR NEXT PROJECT Perforating • Available in round, square, HENDRICK ADVANTAGES slotted, ellipse, hexagon and a variety of decorative patterns • Perforation sizes from 0.027” up to 6” in diameter. • 130+ years in business • Punch, laser or plasma capabilities Privately • Employee tenure averages Held 10+ years • Wide range of popular materials Company • Nimble—Quick Decisions in stock. Fabricating • Shearing • Vendor managed inventory Flexible • KanBan - Consignment Supply • Punching • JIT • Blanket order contracts Chain • Bending • Notching • Rolling • Procure >30M lbs. of raw material annually • Stamping Purchasing • Raw material consignment Leverage • Leveling programs • Access to metal during shortages • Degreasing • Water Jetting • Laser Cutting & Etching • Disciplined Cost Focus • Drilling • Solid Operating Results Financial • History of reinvestment Strength • Plasma Cutting • MIG & TIG Welding • Spot Welding • Hardware Insertion • In-house tooling capabilities Vertical (design and manufacturing) • Heat Treating Integration • In-house punch manufacturing • Turning • Tapping • Grinding • Polishing • Dedicated lean resources Commitment • PVC Coating • Continuous, best practice to Lean lean events company-wide Manufacturing • Assembly 3 CAPABILITIES Engineering and design support services From basic projects, to those requiring complex and challenging solutions, Hendrick provides quality driven design assistance. We promote collaboration with our customer’s engineers at each stage in the product life cycle. Services include: • Prototype design & build, product development, and production engineering support • Revision control and product data management throughout the production cycle • Design assistance for one-time or repetitive applications • We accept multiple AutoCad file formats Material options (no minimum) Design and value engineering assistance is offered, providing a cost-effective approach to production. We maintain a large inventory of popular materials in stock, in both sheets and coils, providing you with buying power that leads to very competitive pricing and shortened lead times. Plus, our no-minimum order policy offers the same fast delivery and lower pricing on small to medium volume orders. Tooling With hundreds of precision, high-speed perforating tools available, we can readily produce most hole pattern requirements. Aluminum Hendrick’s in-house manufacturing of tools 3003, 5052, 6061, plus more and punches assure that tooling can be Cold Rolled Steel made for custom jobs. Hot Rolled Steel Galvanized Steel G90, G60, E.G. plus more Stainless Steel 304, 316, 430, plus more Additional materials available copper, brass, monel, plastic and more 4 INDUSTRIES Quality materials for diverse applications INDUSTRIES WE SERVE Hendrick supplies perforated metal and fabrication to over 20 end markets across the globe, both directly and • Acoustical • Hammer & Powder Mill through our distribution channel partners. Whether you fit • Agricultural • HVAC one of our major industries served or a smaller, niche market, we have the manufacturing expertise and flexibility to provide • Architectural • Industrial Equipment quality materials for diverse and demanding applications. • Automotive • Medical • Commercial Lighting • Mining & Aggregate • Conveyor Flights • Recycling • Distribution • Retail • Electronic • Security • Environmental • Telecommunications • Filtration • Transportation • Food Processing A D F B E C A. Fan tray for telecomm chasis D. Speaker grill B. Medical test tube tray E. Automotive truck grill C. Truck step plate F. Washing machine drum 5 PERFORATING We can produce unlimited patterns from standard to intricate configurations in a variety of shapes. We also offer in-house cleaning/degreasing and deburring/polishing services. Hendrick’s full width, all-across perforation capabilties save time and money. Process capabilities There are different machine operations used to perforate materials, each with its own manufacturing advantages. Hendrick offers these options at our Pennsylvania and Illinois manufacturing locations. All-across, full width perforating press Fast, and the most economical perforating method, typically used for larger runs. Our high speed perforating presses are CNC punching Laser or plasma cutting capable of punching material up to 60” wide in thickness ranging from .002” to A cost effective method for punching Regardless of the material type or 0.25“. Punch hole size dimensions are from sheet metal in prototype, low volume thickness, we provide the versatility 0.027” to 1.0” in diameter. These presses or in production runs. Hendrick has high- to produce parts with more intricate are capable of punching up to 600 strokes precision equipment that can meet tight geometries and precise dimensions per minute. tolerances. Our 20 to 50-ton presses can using our laser or plasma cutting produce components that are up to 60" equipment. Plus, our punch/plasma wide and up to 3/8" thick, depending on combination machine can perform material. multiple operations that can reduce production costs. 6 FABRICATING Broad range of capabilities FABRICATING CAPABILITIES Hendrick offers complete end-to-end supply chain solutions with our broad range of fabricating capabilities. Regardless of size, • Shearing • Plasma Cutting volume or material, our fabrication options can eliminate • Punching • MIG & TIG Welding labor, time, and provide cost-savings for your completed assembly. • Bending • Spot Welding • Significant tool library • Notching • Hardware Insertion • Large to small components • Rolling • Heat Treating • Prototype to production • Leveling • Turning • Partial to complete turn-key contract assembly operations • Degreasing • Tapping • Multiple finishing options available • Water Jetting • Grinding • Laser Cutting & • Polishing Etching • Assembly • Drilling • Stamping 7 HOW TO ORDER Perforated material - ordering specifications Hendrick offers an unlimited number of pattern configurations in a wide range of materials. To assure quick and accurate quoting or delivery, please refer to these guidelines when ordering Hendrick’s perforated materials. Material – Indicate the type of material required and thickness or gauge. See page 4 for a list of Hendrick’s raw materials. Other metals and plastics are available. Quantity – Indicate number of sheets or linear length of coil required. Sheet Size – Provide width and length. We can accommodate any size up to 60" wide. Common sheet widths: 36", 48" and 60". Common sheet lengths: 96", 120" and 144". Specify hole specs: 1. Hole shape 2. Pattern (staggered holes or straight line) 3. The hole size in inches* 4. The hole centers (distance from the center of one hole to the center of the nearest hole in the next adjoining row) in inches.** See examples of shapes and patterns on the following pages. Provide open area: Provide the open area (total hole area, compared to sheet size) on the perforated sheet, indicated by percent. Typical open areas range from 2 to 80%, however 70% and higher can distort the material. Specify margins: 1. Specify “Minimum” or “No Margins” if not important. If margins are required, state the margins for each side of the sheet.*** End margins can be finished or unfinished end patterns. Provide additional information: 1. Forming – Provide forming operations that will be required to assure formability of the sheet. 2. Finishing – If additional finishing is required to achieve a decorative appearance, durability or protection. 3. End use – Our experienced engineering staff will review your design to assure all your end requirements are met. Regardless of order size, small to large, Hendrick partners with our customers to optimize designs for improved quality, functionality and cost–savings. *Industry standards recommend not making the hole diameter smaller than the material thickness. If you require a smaller hole, contact Hendrick to discuss your needs. **The web size (distance between holes) should not be smaller than the material thickness. *** Wider margins can lead to distortion and may require additional leveling, increasing costs. 8 PATTERN SAMPLES A wide choice of perforated patterns are available, in a variety of shapes, sizes and materials. The following pages provide a quick reference of Hendrick’s popular perforated pattern options. If you don’t see what you need, contact a sales representative to discuss your requirements
Details
-
File Typepdf
-
Upload Time-
-
Content LanguagesEnglish
-
Upload UserAnonymous/Not logged-in
-
File Pages20 Page
-
File Size-