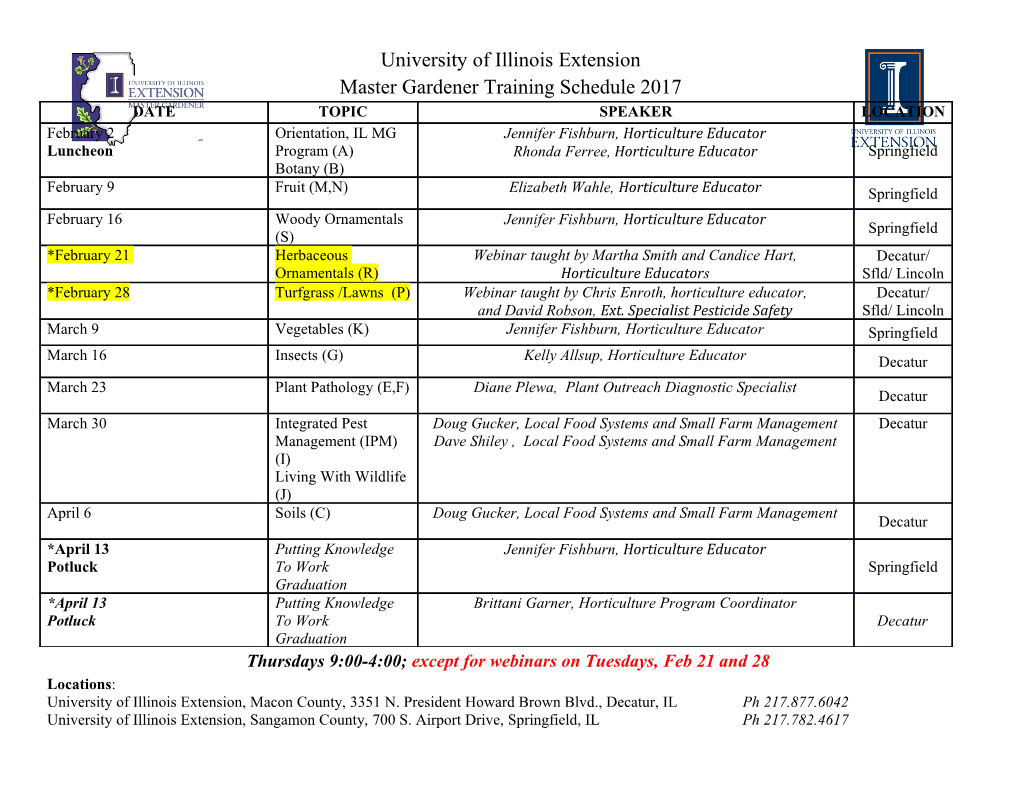
In-Space Condition-based Autonomous Inspection for 12th International Symposium for NDT in Aerospace October 6, 2020 George Studor NASA Engineering and Safety Center NDE Technical Discipline Team Sep 22, 2020 version 1 Bio • George Studor • NASA Engineering and Safety Center(NESC) • 35 Years with NASA and 20 years with USAF • NESC Technical Discipline Teams(TDTs) - Consultant with Analytical Mechanics Associates(AMA): • NDE TDT: In Space Inspection • Avionics TDT: Wireless Sensors/Avionics • Robotic Spacecraft TDT: Natural Systems in System Engineering • Industry Involvement: Workshops with Oil & Gas Industry/DOE • In Space Inspection Workshops (2012, 2014, 2017…. 2021) • Passive Wireless Sensor Technology Workshops (9) 2 Motivation Apollo 13 – No Views of the damage “Houston, we’ve got a problem” then, after the SM was released… "There's one whole side of that spacecraft missing!“ MIR Spectre impact/leak – No Time Only 24 minutes to find/plug leak before having to shut the hatch. 3 AERCam – Manual deploy and operation – Dec 1997 - A Bird’s Eye View for EVA Astronauts - Inspections of Shuttle and Space Station Exterior “someday” Mini-AERCam “Mini AERCam Inspection Robot for Human Space Missions” AIAA Space 2004 Conference Steven E. Fredrickson*a, Steve Duran*b, Jennifer D. Mitchell*c NASA Johnson Space Center, Houston, Texas 77058 4 5 6 More Motivation • Columbia – suspected impact to Wing Leading Edge, but NO on-board impact sensors, inspection sensors or repair options. AF Maui image 1/28/03 Columbia Breakup over TX - 2/1/03 7 Space Shuttle Thermal Protection Systems Inspections: Challenges: Needed Damage Survey & Focused Inspections - Planning/Operations for Robotic Arms - Sensor Engineering Operations and Image Analysis - Crew Time and RMS Time detracts from Mission 1:47 8 WingBiggest Leading Threat Edge comes Impact from Detection System Micro-Meteoroids and Orbital132 Debris(MMOD) Channels Impacts that can cause Critical Damage to the Re-entry Thermal Protection Systems Challenges: • Ground Engineering & Operations Physical Optics Corp/Volodymir Romanov & Victor• Wiring Plessky to the Sensors Compton Imaging Tomography (3D Backscatter) 9 • Battery Cert and Replacement Inspection-Only vs Condition-based Inspection Late Focused Un-Dock Dock WLE Impact Inspection 2 wks 6 months later Condition Monitoring-based Inspection Use as is Analysis Repair Monitoring Analysis + Focused Inspection Discard Inspection Discard Discard Replan Replan Replan Less workload, more risk reduction Inspect Early High workload, Less risk reduction (Initial Condition) Establish Baseline Survey Inspection to Detect Damage (Compare with Baseline) Inspection Discard Only Replan 10 International Space Station – Low Earth Orbit Inspections ISS Inspection Examples: - Periodic Whole Vehicle Surveys - EVA Translation Paths - Windows - Solar Arrays/Masts - Radiator Cooling Systems Visiting Vehicles: - Soyuz - Cargo Vehicles Soyuz - Commercial Crew Vehicles - SpaceX - Boeing No Impact Event Monitoring SpaceX Dragon 2 Boeing CST100 Starliner 11 International Space Station Inspections Detecting the damage vs finding the damage Periodic ISS Solar Array 120’ Masts (8) General Surveys MMOD Impacts – Periodic Inspection Ammonia Leak - Ongoing Module Leaks to Vacuum – ongoing 2018 Soyuz EVA Configuration and Hole = Translation Paths 12 Mfg Defect International Space Station ISS life Extension From: 2024 To: 2030 356’ x 240’ Orion Spacecraft(LM) for beyond ISS Lunar Gateway Space Station Restore-L Mission Satellite Servicing in Low Earth Orbit Will there be an Inflatable Space Station? 13 Detecting Damage vs Characterizing Damage Entry Holes are often Narrow, sometimes Deep and rarely Perpendicular to the Surface X-Ray CT 26 Lunar Mission Risks Greater than Low Earth Orbit Low Earth Orbit Beyond Low Earth Orbit Risks: Orbital Debris Risks: Critical Thruster Firings, Micro-Meteoroid and Radiation Van Allen Protection to 36K miles 240,000 miles! Communication will take about 2.5 seconds each way 15 Artemis III: Landing on the Moon 16 “Gateway” Lunar Space Station - High Cost means they will be Infrequent Missions - Radiation means crews have Limited Occupation - Remote & Autonomous Ops & Maintenance needed - Lead Time/Cost Rescue Missions – Failures are Costly - Hotter/Faster Re-Entry: TPS Less Tolerant of Damage 17 In Space Inspection • Scheduled When Prudent: • Periodic Surveys • Establish Initial Configuration after Mission Configuration Event. • Assessments of Unacceptably High Risk if not detected. • Validate Models of the system, structure or environments. • Support for planned external operations: EVAs, Docking, Robotics And • Triggered when Conditions Warrant (Conditions-based): • Camera surveys or Astronaut observations detect a “Region of Interest” • Structural Sensors indicate an impact or pressure decay • System Sensors indicate performance deterioration or anomaly. • Natural or Induced Environment Changes • Events produce Uncertainty in the Spacecraft External Condition. 18 New Tools Needed: • Efficient Manipulators and Human-like Robotics • Inspection in Difficult to Access Areas • Free-flying Inspection platforms • Sensors/Wireless Sensors to Trigger Inspections 19 Compact Robotic Manipulator Inspection with Roll-a-Tube Boom Wrist - Lightweight & Bulky Rigid Boom Sensor - Compact for Transport Shuttle Arm Inspection - Multiple Configurations Elbow Joint http://www.rolatube.com/satellite- deployment-booms/ Deployable Compact Boom Stowage Shoulder http://www.rolatube.com/nuclear-inspection-booms/ 20Joint Robonaut 2B heading back to ISS https://spectrum.ieee.org/automaton/robotics/space-robots/nasas-robonaut-to-return- to-iss-with-legs-attached 21 NASA Astrobee IVA (Internal) Testbed on ISS NASA/Ames/Astrobee Working Group: [email protected] AMES “Micro Gravity Test Facility” Astrobee in Japanese Kibo Module for Astrobee 22 What do we need Snake Inspector to do? Internal Functionality Snake Inspector 1. Stereo vision and articulating head with lighting, designed in stiffness at various sections along the length Entry hole Equipment Rack 2. SLAM - Simultaneous Location and Modeling Software - builds the 3d model as it goes in and subsequently determines position and orientation of all parts very accurately. Housing/control 3. Articulating snake robot - mechanical or piezo-control of the entire snake length- not just the tip as in a typical endoscope. Sensors that sense contact and feed controls to alleviate it. Area to be inspected 4. Snake real-time location - know/display the location of the entire snake - plot against accurate 3D model built in #1. 5. Self-following Software - each segment of the snake knows where and how to turn as it follows the head or backs out of a complex physical path. 6. Very small size, weight and power and works well Zero-g (assumed) 7. Length of at least 2 meters and diameter 3/8" or less – go through existing penetrations such as the holes for sending fire extinguishing 8. Minimum crew involvement/training - easy to use, hands-free, possibly remotely operated from ground. 9. Ability to change imagers at the end, and/or add sensors/wireless sensors at the tip. 10. Ability to grab items at the tip. 23 Autonomous Inspection with a Free-flying Small Spacecraft Inspector Why a Free-flyer vs a Robotic Manipulator? • Avoid Robotic Manipulator infrastructure/operations • Minimal or No Crew Operations • Autonomous Ops means Minimal Earth-based Support • Continuous Monitoring • More View Angles and Distances • Faster response and more stable/no oscillations Condition Monitoring – Wireless/Optical Comm from sensors/systems • Events and Trends to Address Risks Sooner • Avoid Inspections if not required • Data from Hazardous Zones • Data from Difficult to access areas • Need Damage Characterization Capability if results warrant: • External: Free-flyer, Robotic Manipulator, Crawler, Tethered Sensor • Internal: Free-Flyer, Micro-Crawler or Humanoid Robot with tools 24 Example: Continuously Monitoring Gateway at “safe” distance (NASA’s Version of a Smart Home Security Camera System) “Events” may Trigger additional Characterization: Multi-spectral & 3D Imaging RF/Light for ID, Location, Sensing RF: RF: Solar Array Orion Impact and Health Dynamics – When to do it? RF: Manipulator RF: Loads and Module Leak Dynamics 25 Free-flying Autonomous Spacecraft Inspector for Orion • Solar Array Tip Cameras likely can see if there is damage • MMOD damage depth not possible with fixed cameras • Complex flight path to survey the “backshell” surface - then damage characterization as necessary CubeSat Imaging: MMOD Entry Hole - 3D Maps of Damage Cubesat - Image Processing TPS Backshell Inspector - GN&C Input Cubesat RF: Position RF Sensors Cubesat Laser Comm: Solar Array - Command Sequence Updates Tip Cameras - “Answer” Downlink 26 Condition-based Autonomous Inspection is Reasonable and Practical • Piggy-back off other Autonomous Systems and Sensing • Small Satellite and Cubesat Missions • Free-flyer testbed on ISS - Astrobee • Aircraft • Automobiles/Military Ground • Underwater Inspection ROVs • Security Camera Systems • Advanced On-board Image Processing • Inspection Drones 27 Aerospace Corp Aerocube 10 (A&B): Prox Ops & Pointing and On-board Image Processing Photo at 26 meters! https://aerospace.org/article/cubesats-get-close-proximity-operation-interesting-implications Aerocube 7 and 11: Aerocube 8D: 28 Laser Communications Ion-Electrospray Propulsion Leverage Industry – Inspection Drones • Inspection with Image Downlink • Command as well
Details
-
File Typepdf
-
Upload Time-
-
Content LanguagesEnglish
-
Upload UserAnonymous/Not logged-in
-
File Pages44 Page
-
File Size-