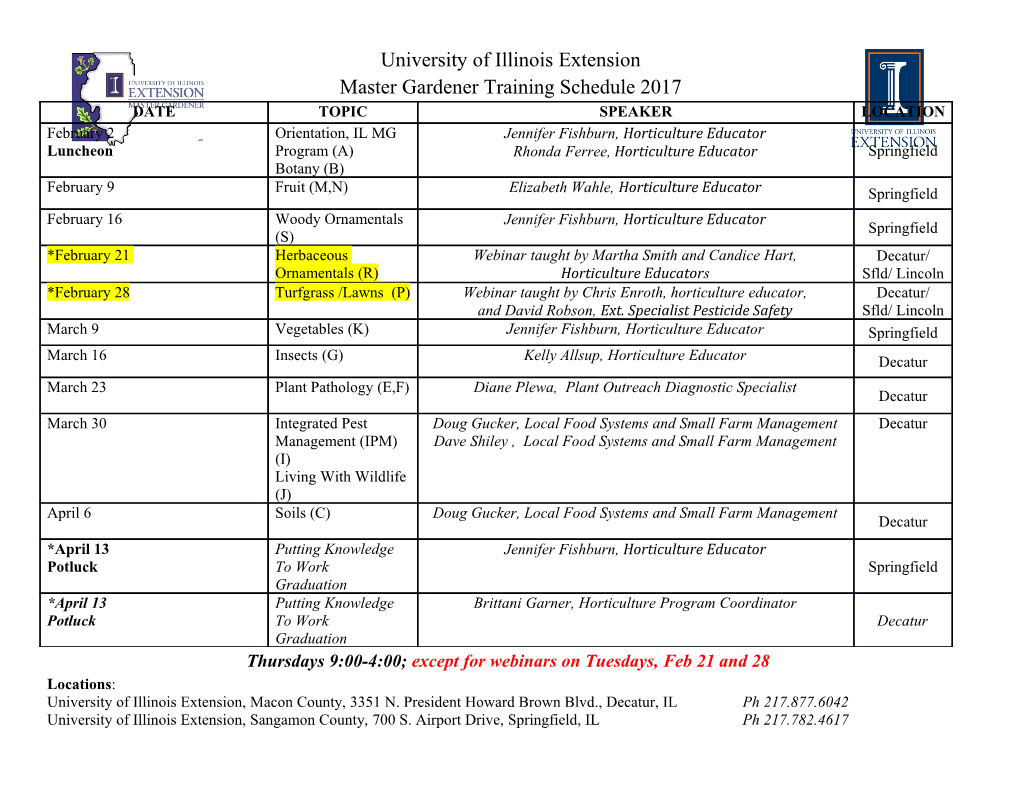
Advanced Materials Research Vols. 15-17 (2007) pp. 129-134 online at http://www.scientific.net © (2007) Trans Tech Publications, Switzerland Selective Oxidation during the Austenitic Annealing of a CMnSi Steel T. Van De Putte 1,a , Z. Zermout 2,b , D. Loison 3,c , S. Claessens 2,d , J. Penning 1,e 1Department of Metallurgy and Materials Science, Ghent University, Technologiepark 903, B-9052 Zwijnaarde, Belgium Tel.: ++32 (0)9 264 57 61, Fax: ++32 (0)9 264 58 33 2Industry Research Centre Gent – OCAS NV – ARCELOR, J. Kennedylaan 3, B-9060 Zelzate, Belgium Tel.: ++32 (0)9 345 13 66, Fax: ++32 (0)9 345 12 04 3Arcelor Research SA, Voie Romaine, BP30320, F 57283, Maizières-les-Metz, France Tel. : +33 (0)3 87 70 47 20 E-mail: [email protected], [email protected] , [email protected], [email protected], [email protected] Keywords : Selective oxidation, XPS, Surface state, Austenite Abstract Highstrengthmultiphase CMnSi steel is increasingly usedinpassenger cars.Si andMnalloying levels are typically inthe range of 1-2% inmass.While Si improves the mechanical properties,it considerably deteriorates the galvanisability of steel. Residual water vapour in the reducing gas atmosphereduringtheintercriticalor austeniticannealingresultsintheselectiveoxidationofSiand Mnat the steel surface.Besides MnandSi,C is oxidizedas well at the steel surface, leading tothe formation of CO gas and decarburisation of the steel surface. This decarburisation has a major influence on the phase composition in the steel surface region: it shifts the ferrite to austenite transformation to higher annealing temperatures, leading to differences in surface and bulk microstructure. The phase composition influences the solubility and diffusivity of all alloying elements near the surface. The evolution with temperature of the selective oxidation at the steel surface has been studied by interrupted annealing in a protective atmosphere containing residual water vapour.The influence of the annealing temperature onthe selective oxidation of MnandSi is characterizedbyXPS(X-rayPhotoelectronSpectroscopy)analysis. Introduction It is knownthat for a goodquality hot dip galvanising,anappropriate concentrationof metallic iron at the steel surface is necessary toallow the formationof aninhibition layer by reactionbetween the substrate iron and Al in the zinc bath. It is proved that selective surface oxidation during recrystallizationannealing considerablyhampersthe galvanisability[1,2,3,4]. Surface selective oxidationof a Si andMnalloyedhighstrengthsteel has already beenstudiedin variousconditions[5] butnot yetthoroughlyduringaustenitic annealing. Previously it was shown by Mahieu[6] that there is less external selective oxidationona CMnSi steel composition provided that the temperature is high enough to ensure a fully austenitic annealing. Due to the high carbon content the studied high strength steels however, the decarburizationof the surface regionduring annealing has tobe considered.The carbondepletion near the surface will cause the austenitisation to move up to higher temperatures. That might explainthe large difference inoxidationbehaviour for isothermal annealing at 850°C and950°C despitethefactthattheequilibrium bulkphaseis austenitefrom845°Con. The results presented in this paper are part of the continuation of the research of Mahieu. The purpose of this study is tomake a confirmationof what was earlier reportedandtoformulate an explaininghypothesis. All rights reserved. No part of contents of this paper may be reproduced or transmitted in any form or by any means without the written permission of the publisher: Trans Tech Publications Ltd, Switzerland, www.ttp.net. (ID: 157.193.118.1-11/01/07,09:02:44) 130 THERMEC 2006 Supplement Experimental The chemical compositions of the steels used inthis workare presented inTable 1.The first is a laboratorycasting,thesecondoneisanindustrial steelsuppliedbyArcelor. Table 1: Chemical compositions of the steels used in this work (concentrations in wt%). Material C Mn Si Al P Laboratorysteel 0.25 1.69 1.28 0.06 0.015 Industrialsteel 0.2 1.6 1.6 0.04 0.012 The surfaces of the coldrolledsteel sheets (thickness 1mm) were all grindedandmirror polished before the recrystallization annealing inorder toremove all influences of the steel processing.It can thus beassumedthat beforeannealingthesurfaceandbulkpropertiesareidentical. Smallcircular(10mmindiameter)samples arethenpunchedoutofthe polishedsteelsheetandheat treatedina N2–5%H 2 atmosphere witha dew point of -50°C.The heat treatments are performed in aninfraredfurnace directly connectedtothe XPS analysis chamber, providing a pseudoin-situXPS characterizationof the annealedsamples.The twotypes of annealing cycles usedin this study are represented in Figure 1. The laboratory steel was rapidly heated and maintained for 2 minutes at either 850°C or 950°C for 2 minutes, followed by a natural cooling in low vacuum (1 mbar) to prevent oxidationduringcooling.The selectionof the soaking temperatures is basedon the earlier study of Mahieu[6].The theoretical austenitisationtemperature calculatedby ThermoCalc software for the laboratory steel is 845°C, meaning that the equilibrium phase for both temperatures is austenite. For the industrial alloy an interrupted annealing with low heating speed (6°C/s) was chosen: samples were heatedtodifferent temperatures from 450°C to1000°C andnaturally cooled down in a low vacuum without soaking. The purpose of these annealing tests is to evaluate the evolution of the selective oxidation of the surface during the heating section of the continuous annealing process. The choice of a different annealing cycle for the two steels has no scientific reason. T 120s T 1000°C 850°C – 950°C 15°C/s 6°C/s 450°C 70°C/s Low vacuum Low vacuum 4°C/s … time time Figure 1: schematic representation of the used annealing cycles in a temperature versus time graph. Left the isothermal annealing cycle and on the right hand side the interrupted heating treatment. Directly after annealing, the samples are transferred under high vacuum (10 -9 mbar) to a XPS analyzer.XPS measurements were carriedout ona Microlab 320-D from Fisons/VG Scientific with a nonmonochromatic AlKα anode and a take off angle of 90°. Analysis quantificationwas based on sensitivity coefficients proposed by the manufacturer. After this first analysis,some samples are exposedtoambient air for about 2minutes andare thenanalyzedagain. Metallic ironat the steel surface after annealing will hereby be oxidized.The metallic ironunderneathanoxide layer will be protected from the high oxygen partial pressure and will remain metallic. This procedure allows distinguishing between oxidizable metallic iron present at the surface and metallic iron located underneatha thinoxide layer.For galvanising,only the metallic ironavailable at the steel surface will be able toreact withAl inthe zinc bathto form the inhibition layer necessary for goodquality galvanising. The surface of the annealed samples is afterwards studied by FEG (Field Emission Gun) SEM secondary electron (SE) imaging and EDX (Energy Dispersive X-ray) analysis. A primary acceleratingvoltageof5keVhas beenusedtoenhancesurfacesensitivity. Advanced Materials Research Vols. 15-17 131 Results High heating rate isothermal annealing The remarkable difference inoxidationstate of the surface after isothermal annealing at 850°C and 950°C,previously observedby Mahieu[6],couldbe confirmed. Figure 2 shows the XPS-spectra of Fe,MnandSi before andafter air exposure.The results of the quantificationof these spectra are presentedinTable 2. For quantificationthe sum of the concentrations of the elements Fe,Mn,Si,C andO was normalizedto 100%.The drop intotal ironcontent after air exposure is due toa higher oxygen concentration in the second analysis. The variations in concentration of Si and Mn after exposureareattributedtoastatisticaldeviationinthespectrumacquisition. 3/2 30 Fe2p 850°C Mn2p 850°C Si2p SiO 850°C Fe-met 3/2 4.5 2 850°C-air 10 Mn2p 850°C-air 850°C-air 25 950°C 950°C 950°C Mn SiO 950°C-air 2 4 950°C-air 4.0 950°C-air 20 8 1/2 Fe-ox Mn2p Counts/s) Counts/s) Counts/s) 4 4 15 4 6 3.5 10 5 4 3.0 Intensity(10 Intensity(10 Intensity(10 0 704 706 708 710 712 714 635 640 645 650 655 660 665 100 102 104 106 108 110 Binding energy (eV) Binding Energy (eV) Binding Energy (eV) Figure 2: The Fe, Mn and Si XPS spectra of samples annealed at 850°C and 950°C for 120s, before and after air exposure (air). Annealing was performed in N 2-5%H 2 with a dew point of -50°C. After annealing at 950°C ina N 2-5%H 2 atmosphere witha dew point of -50°C,the steel surface seems tobe less oxidizedthanafter annealing at 850°C: there is muchmore metallic ironpresent near the surface.Nevertheless none of this metallic ironis oxidizable: the XPS spectra before and after air exposure are almost identical whichindicates that the surface compositionandoxidation state have not changed.This means that after annealing at 950°C the steel surface is coveredwitha very thin andcontinuous oxide layer,protecting the metallic ironunderneath.This oxide layer can not be thicker thana few nanometer because a large amount of the underlying metallic ironis still detected by XPS. Although not presented, an Al peak was detected in the XPS spectra after annealing at 950°C. It is known that Al strongly segregates to the steel surface at very low dew points [3].Soevenwhile its bulkconcentrationis very low,Al canparticipate inthe covering oxide layer by formationof Al 2O3 or Al spinel oxides.However
Details
-
File Typepdf
-
Upload Time-
-
Content LanguagesEnglish
-
Upload UserAnonymous/Not logged-in
-
File Pages6 Page
-
File Size-