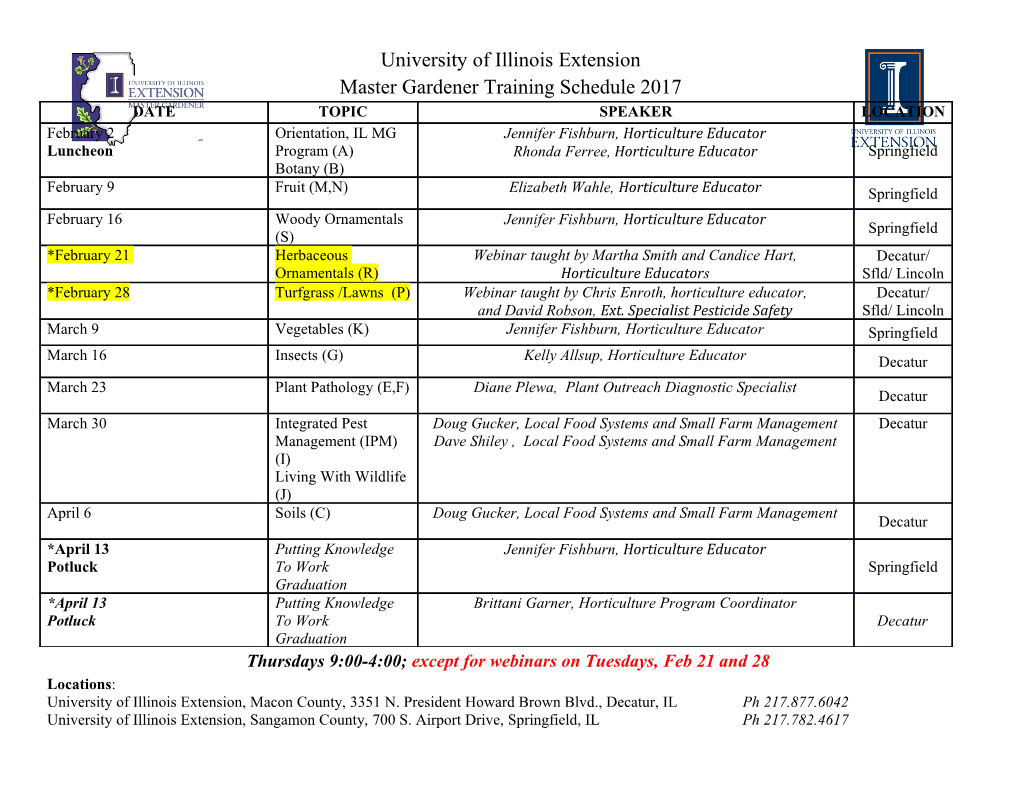
Rapida RDC 106 – High performance in die-cutting Rapida RDC 106 Tailored die-cutting solutions for future-oriented in-house production As a print provider, you must be able to promise greater performance and flexi- bility than ever before, because that is the only way to survive on an increasingly competitive market. Not only for the actual printing, but also with regard to finishing. You need industrial solutions which make your life easier. And that, in turn, calls for ideas and creativity. Also from us as your press manufacturer. The rotary die-cutter Rapida RDC 106, or inmould labels for paint buckets – with developed on the basis of our proven Rapida our Rapida RDC 106, all your die-cutting, medium-format press, incorporates the very embossing, creasing or perforating needs are latest die-cutting technology for a sheer handled in ultimate quality in a single pro- boundless scope of applications. Whether duction pass. folding cartons, elegant presentation folders 02 Highlights Technical features such as the DriveTronic • Modern sheet transport concept of the feeder and infeed, Venturi sheet guiding, Rapida sheetfed offset presses is the key to universal gripper systems and the AirTronic high substrate flexibility and a broad delivery lay the foundations for maximum sub- production spectrum strate flexibility and die-cutting speeds up to • Optimised design geared to reducing foun- 15,000 sheets per hour. Handling becomes dation loads for a positive effect on die- intuitive thanks to the intelligent TouchTronic cutting quality and significantly quieter operating concept at the ErgoTronic control operation console. You can choose from a whole range • Precise adjustment of the die-cutting of different configurations and equipment pressure in the finest possible steps packages. Depending on your individual needs • Simple handling of the die-cutting formes and requirements – for products in the highest and minimum storage space requirements quality, die-cut with absolute precision and care. • Intuitive operating concept of the Rapida platform permits flexible personnel assignment Rapida RDC 106 – Benefits at a glance • Integration into a company workflow • High level of automation for fast job changes (production data acquisition) and makeready savings in case of repeat jobs • “365 / 7 / 24” service hotline and remote thanks to the magnetic cylinder and a register maintenance pin system for tool-free forme changes • Significantly enhanced efficiency for short runs thanks to extremely fast makeready compared to flat-bed die-cutters, paired with high production speeds for long runs 03 Rapida RDC 106 DriveTronic dedicated drives for ultimate ease of operation A rotary die-cutter can only ever be as good as its feeder. After all, precise sheet separation is a basic prerequisite for smooth production. Koenig & Bauer is here able to offer you the best solution on the market: DriveTronic dedicated drive technology for the feeder and infeed. 04 Feeder and infeed The shaftless DriveTronic feeder adapts to whatever substrate you use. And the sidelay- free infeed DriveTronic SIS then aligns every single sheet calmly and effortlessly. Without the slightest risk of setting or pulling errors. DriveTronic feeder • Feeder motions controlled via 4 servo motors • Continuous, stepless pile lifting with auto- matic speed compensation (paper / board) • Automatic format setting • Automatic pile side edge alignment • Front-edge pile height sensing with automatic compensation of the feeder head height • Skew-sheet correction at the feeder head during production DriveTronic SIS (Sensoric Infeed System) • Antistatic loosening and separating air • Patented KBA sheet infeed system • Electronically controlled lateral sheet Suction-belt feed table alignment • Suction-belt feed table with stainless, • Integration into automatic format setting antistatic structured surface, a single feed eliminates all need for operator intervention belt and multi-chamber vacuum system • Gentle sheet positioning with the highest • Electronically controlled sheet deceleration possible accuracy to ensure optimum sheet arrival speed at the • Patented Venturi system before the feed line front lays for smooth sheet infeed • Pneumatic drive elements for precise Infeed positioning of the sheet, even at maximum • Swing infeed accelerates the sheet smoothly speed for transfer to the feed drum • Pile side edge alignment via the SIS sensor • Motorised remote adjustment with Drive- Tronic infeed for front lays, feed line and Sheet monitoring front lay cover height • Ultrasonic double-sheet detector, also for • Photoelectric infeed sensors with motorised inhomogeneous materials setting from the control console or infeed • Multiple-sheet detector display • Optical skew-sheet sensors • Touchscreen display with direct function • Optical front lay sensors with electropneu- keys for reliable and intuitive operation matic overshoot blocking Non-stop operation at the feeder • Manual non-stop system with individual rods for uninterrupted production during pile changes • Fully automatic non-stop system with sensor- monitored rake, suitable for pile logistics integration • Sensor monitoring for pile transport and pile reunion • Pile insertion possible from all three sides 05 Rapida RDC 106 Rapida performance in die-cutting – the game changer The basic design of the process unit is very similar to that of a Rapida 106 printing unit. On our rotary die- cutter, too, double-size cylinders and transfer drums provide for reliable sheet transport through to the delivery. The magnetic die-cutting cylinder is the heart of the process unit. This system permits precise, tool-free mounting • Magnetic cylinder with high holding force for of an endless variety of dies to suit every con- mounting of ceivable application. After embossing, creasing - complete formes with register punching and die-cutting, the cutting waste is removed - creasing and embossing plates cleanly at the stripping station for disposal. - individual die segments The Rapida RDC 106 can be configured with up - formes of any size within the format range to four process units – for optimum tailoring to • Laser-based scanning for automatic pre- your individual needs. setting of the forme thickness eliminates time-consuming fine adjustment steps Process unit • Double-size back cylinder: Mounting of pro- Process unit: Creasing/embossing tector jackets as protection for the cylinder • Absolutely exact cylinder positioning in 1 μm surface and to provide the counter-die for steps, separately for each side, provides for creasing/embossing ultimate accuracy and perfect results • High-precision magnetic cylinder running in • Automatic plate positioning for fast and play-free bearings for mounting of the die- simple job changes cutting forme • Pneumatic pressure on/off switching • Cast frame for high torsional rigidity and • Magnetic back cylinder stability • Simple adjustment of the lateral and cir- Process unit: Die-cutting cumferential register via the operator panel • Absolutely exact cylinder positioning in 1 μm (touchscreen) steps, separately for each side, provides for ultimate accuracy and perfect results Magnetic cylinder • Protector jackets with quick-action • Precision-ground magnetic cylinder with per- clamping system for fast and user-friendly manent magnets and register pin system for replacement fast and exact forme positioning without the • Temperature control within the unit to use of tools ensure constant die-cutting pressure 06 Process unit Process unit: Stripping Automatic forme changing • Die-cutting and partial or complete removal • Tool-free die-cutting forme change requires of the cutting waste in one machine pass approx. 2 minutes per unit • Plotter-drawn stripping formes • Use of CNC-manufactured dies for absolute • Forme and stripping cylinder function accuracy and minimum tolerances even with according to the die/counter-die principle; the smallest radii and contours 2 female dies on the vacuum cylinder and 1 • Laser sensor scans the die-cutting forme to male die on the forme cylinder enable automatic presetting of the forme • Quick-action clamping system and automatic thickness cylinder positioning for fast, tool-free forme • All relevant air and format settings can be changes saved at the ErgoTronic operator panel and • Double-size stripping cylinder with vacuum recalled for repeat jobs and blower air for stable mounting and reliable separation of the die-cut blanks and Sheet guiding waste • Reliable sheet transport over the whole sub- • Removal of the die-cutting waste by way of a strate range from 0.03 to 0.6mm thickness conveyor system or by extraction • Universal gripper system for reliable sheet transport • Gentle, air-cushioned sheet guiding with blower modules and Venturi guide plates • Air settings can be saved at the operator panel and recalled for repeat jobs 07 Rapida RDC 106 AirTronic delivery with full preset capabilities The AirTronic delivery of the Rapida RDC 106 has been designed specifically for high-speed production on the most varied substrates. Even sensitive substrates can thus be handled with ease at full production speed. 08 Delivery New, aerodynamic gripper carriages optimise Sheet brake the air flows and avoid turbulences. At the • Dynamic sheet brake with speed- same time, a sophisticated Venturi sheet compensated suction belts for smooth guiding system provides for a stable sup- and precise pile formation porting air cushion and smooth sheet travel. • Automatic format adjustment The dynamic
Details
-
File Typepdf
-
Upload Time-
-
Content LanguagesEnglish
-
Upload UserAnonymous/Not logged-in
-
File Pages24 Page
-
File Size-