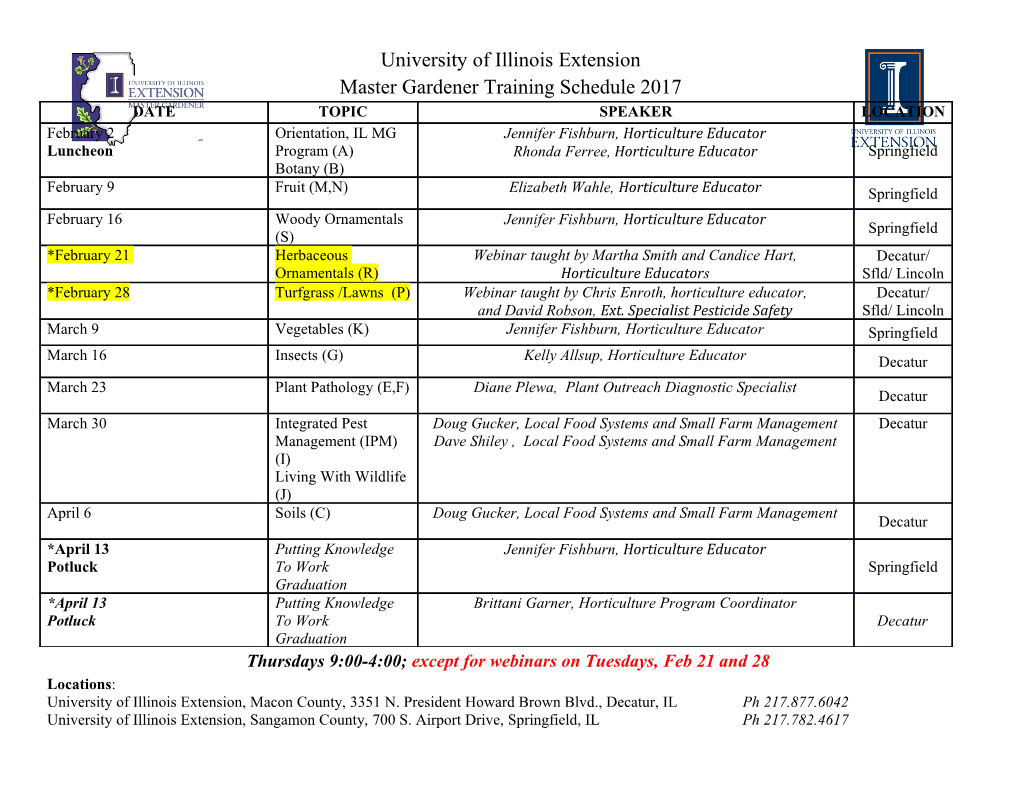
International Journal of Mechanical Engineering and Technology (IJMET) Volume 10, Issue 01, January 2019, pp. 1751-1761, Article ID: IJMET_10_01_174 Available online at http://iaeme.com/Home/issue/IJMET?Volume=10&Issue=1 ISSN Print: 0976-6340 and ISSN Online: 0976-6359 © IAEME Publication Scopus Indexed BEHAVIOUR OF THREADED CYLINDER TOOL IN THE FRICTION STIR WELDING OF AL-ZRB2 AND AL-SIC COMPOSITE P. Jayaseelan and T. V. Christy*. Department of Mechanical Engineering, School of Engineering & Technology, Karunya Institute of Technology and Sciences, Karunya Nagar, Coimbatore – 641114, India *Corresponding author ABSTRACT Friction St ir w elding i s a s olid s tate j oining pr ocess of us ing w ithout any filler material. I n t his w ork, t wo bas e m aterials l ikely A l-MMC’s ar e us ed namely Silicon Carbide and Zirconium di-Boride are used. Hardness Rockwell Value and Tensile Strength Tests are evaluated to the various tool material respect to Al-ZrB2 and Al-SiC. Threaded Cylinder Tool made of the materials likely OHNS, HCHCr, H13 are carried out in the process with D/d Ratio are used. The process is carried out with three different tool materials and two different base material mainly aluminium reinforced Zirconium diboride (Al-ZrB2) and Silicon Carbide (Al-SiC). The Micrograph of each four zones for the tool material and base material is shown. This paper mainly focusing on which the tool material shows a maximum tensile and hardness value for two base materials. Keywords: Friction Stir Welding; Threaded Cylinder; Tool Material; Al-ZrB2, Al-SiC D/d Ratio. Cite this Article: P. Jayaseelan and T. V. Christy, Behavior of Threaded Cylinder Tool in the Fr iction St ir Wel ding of A l-Zrb2 and A l-Sic C omposite, I nternational J ournal of Mechanical Engineering and Technology, 10(01), 2019, pp.1751–1761 http://iaeme.com/Home/issue/IJMET?Volume=10&Issue=1 1. INTRODUCTION Friction Stir Welding is initially developed by “The Welding Institute” (TWI) in December 1991. Friction Stir Welding is a Solid state joining process that creates a frictional heat between the plates or where the tool i s pl unged. T he poor w elds are caused b y detrimental phases can be avoided in this type of welding. Tool plays a major part in the non-consumable welding process. By t he r otational of t he t ool, pl astic def ormation occur s bet ween t he contact s urfaces. Tool geometry, tool profile, and tool material are plays an important role in completing the successful welded joints. The four main process parameter includes speed of the rotation, traverse speed, plunging depth and tilt angle. The length of the tool is slightly smaller than the thickness of the plates. Especially, Friction stir welding is originally adapted for welding the Aluminium alloys. http://iaeme.com/Home/journal/IJMET 1751 [email protected] P. Jayaseelan and T. V. Christy This welding process does not require any filler material. According to the macro view, the four different zones are classified and considered. They are unaffected zone or Base metal (BM), Heat- Affected zone (HAZ), Thermo-mechanically heat affected zone (TMAZ), and stirred zone (SZ) or Nugget Zone (NZ). Basically Zones are divided by its microstructure and temperature variations. Especially, the Weld Zone has higher amount of temperature compared to the Thermo- mechanically affected zone. Then, the thermos-mechanically affected zone has higher temperature t han ov er t he ot her and s o on. E ach zones having t he di fferent microstructure properties and strength. Here, this process is mainly focused on the Aluminium reinforced Silicon Carbide and Zirconium diboride are mainly focused with three different threaded tool material known as H 13, OHNS, HCHCr. D /d ratios and pr ocess parameter are assessed and tabulated. Comparing the strength between the Al-SiC and Al-ZrB2 are shown in the following tables. 2. EXPERIMENTAL PROCEDURE: 2.1. Friction Stir Welding Tool Friction stir welding tool consists of round shoulder and pin was used. Basically pin will have the factor of different profiles such as threaded, tapered, conical etc...So selecting the proper tool for the base material is a play. Proper design and dimensions should be followed then the profile was to be done accordingly. Proper selection of tool will provides a proper weld quality. Rotating shoulder along with the pin is fixed into the CNC machine and operated numerically. Selection of appropriate tool and tool design plays an important role in the FSW process. In this case, we used the Threaded Cylindrical tool as shown in Figure 1. 2.2. Tool Material Used FSW tool plays an important role and selection of tool material achieves proper weld quality and long-durable purpose. For this study we discussed H13, OHNS, and HCHCr for the Al-ZrB2 and Al-SiC. Selecting good material for the tool will have high dur ability t han the other material. Using tool material, should withstand the peak temperature of the welding process, so that the welding process can be done. The FSW process only done, if the tool withstand from thermal properties. Comparing one tool material with other materials should be done, so that we came to know that which material exhibits the high strength. The tool should be designed with all this concern including its material, mechanical and thermal properties. In this case, we using the three various tool profiles are Oil Hardened Normalized Steel (OHNS), High Carbon High Chromium steel ( HCHCr) and H 13 St eel. A ccording t o K Palani, C E lanchezhian, K aranam Avinash, C Karthik, Karra Chaitanya, Karthick Sivanur, K Yugandhar Reddy shows that, the non- consumable FSW tool was designed based on the requirements with the dimensions of shoulder diameter and prolonged pin diameter. 2.3. Choice of Tools In this case, we us ed t hree di fferent non- consumables t ool m aterials was us ed t o f ind out the amount of deformation and at the end of the process, proper weld should be obtained only if the grains are uniformly distributed. Here the three different tool materials used are i) High Speed Steel (H13 steel), ii) Oil Hardened Normalized Steel (OHNS), iii) High Carbon High Chromium steel (HCHCr) are tool materials carried out in the FSW process to find out which tool material and profile possess in such a way of equally distributed grains in the microstructural characterization. The tool is designed in such a way that followed by the shoulder diameter to the prolonged pin diameter in terms of D/d ratio.The following Table 1.shows the tool profile, tool material and corresponding D/d ratio are shown as below. http://iaeme.com/Home/journal/IJMET 1752 [email protected] Behavior of Threaded Cylinder Tool in the Friction Stir Welding of Al-Zrb2 and Al-Sic Composite Table 1. Shows Tool Profile, Tool Material, D/d Ratio Tool Tool Profile Tool Material D/d ratio no. 1 Threaded Cylinder H13 2 2 Threaded Cylinder OHNS 3 3 Threaded Cylinder HCHCr 4 2.4. Process In this pr ocess, the m aterial used was A luminium metal matrix composites (MMC’s) Al-10% ZrB2 and SiC with the dimension of the plates are 100 mm x 50 mm x 6 mm manufactured by in- situ stir casting process was employed as weldments for the Friction stir welding. The enforcements such like Aluminium reinforced with Zirconium diboride and Silicon Carbide is known for improved wear resistance and tensile strength but reduced corrosion resistance. As we know that, FSW basically a welding technique for welding the Aluminium and MMC’s due to withstand the high melting point, hardness and stability. The microstructure of Al-ZrB2 and Al- SiC is shown in Figure 3 and 2. According to K Palani, C Elanchezhian, K H V Saiprakash, K Sreekanth, Dayanand, Keshav Kumar, Deepak Kumar that the better microstructural results were observed in friction stir processing joints relate to the friction stir welded joints and the addition of nanoparticles improved the surface and joint properties and also they discussed Aluminium alloys in addition to nanoparticle Al2O3 and SiC showed the sound defect free joints compared to other joints. Proper selection of tool material is necessary so that we obtain a good quality of welds. Figure 1 – Threaded Cylinder 1 – H13, 2 – OHNS, 3 – HCHCr Figure 2 – Optical Micrograph of Al-ZrB2 http://iaeme.com/Home/journal/IJMET 1753 [email protected] P. Jayaseelan and T. V. Christy 2.5. Parameter Used Welding parameters used in this case are shown in table 3. Parameter includes downforce or axial load, rotational speed, tilt angle and traverse speed. Here 1000 rpm, 25 mm/min, 3.8-4.3 kN were applied and used in this process. By the parameters used, H13 showed the superior results when compared to the other two tools materials. In general, parameters plays an important role in defect free joint, as the nominal parameters should use for obtain the good quality weld. Figure 3 – Optical Micrograph of Al-SiC Table 2 Shows Tool Configuration Factor 1 Factor 2 Factor 3 Response 1 Run A:Profile B:Material C:D/d Selected Tool 1 3 2 1 1 2 2 2 2 2 3 1 2 3 3 Figure 4 – FSW Welded Al-ZrB2 and Al-SiC with corresponding tool Used 3. EXPERIMENTAL PROCEDURE: 3.1. Mechanical Characterization Tests like Tensile strength and Hardness test are conducted to the friction stir welded specimens are Al-SiC, Al-ZrB 2 are prepared as per ASTM E08 standard.
Details
-
File Typepdf
-
Upload Time-
-
Content LanguagesEnglish
-
Upload UserAnonymous/Not logged-in
-
File Pages11 Page
-
File Size-