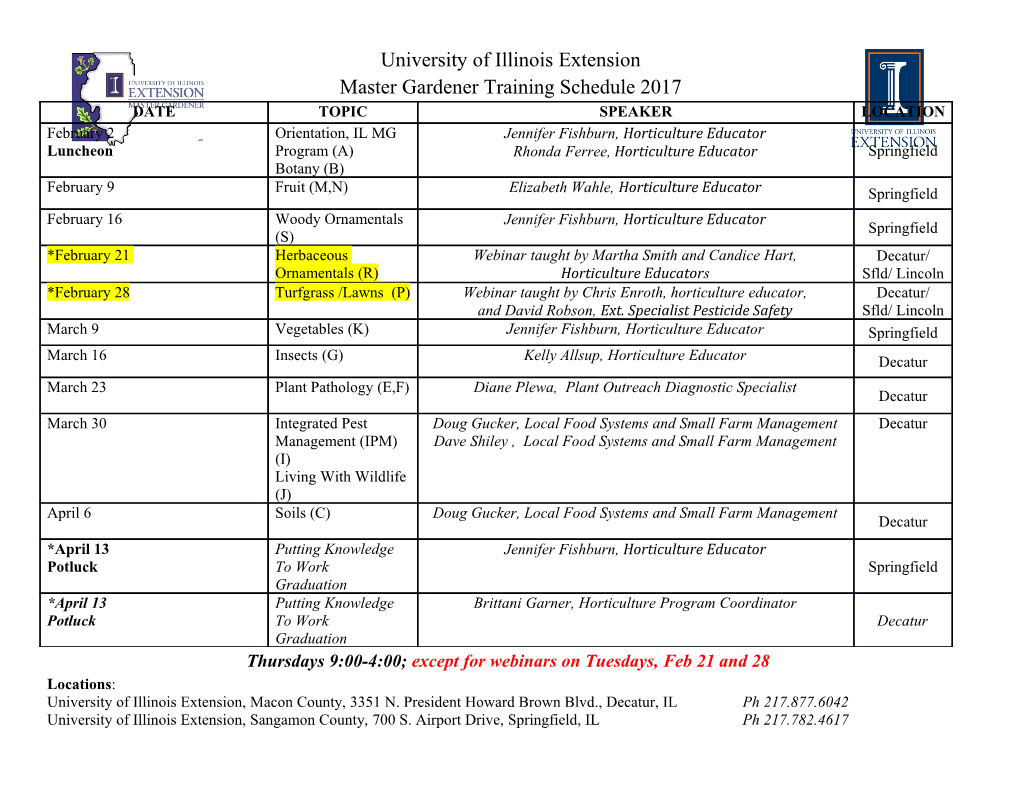
A CUSTOM PRINTED CIRCUIT BOARD DESIGN FOR MICROCONTROLLER EDUCATION by RYAN ANDREW TAYLOR D. JEFF JACKSON, COMMITTEE CHAIR KENNETH G. RICKS MONICA ANDERSON A THESIS Submitted in partial fulfillment of the requirements for the degree of Master of Science in the Department of Electrical and Computer Engineering in the Graduate School of The University of Alabama TUSCALOOSA, ALABAMA 2011 Copyright Ryan Andrew Taylor 2011 ALL RIGHTS RESERVED ABSTRACT Much time and effort has been spent attempting to discover the best approach to the problem of microcontroller education. In electrical and computer engineering (ECE) curricula, much consideration is given to the topic of hardware interfacing. For the potential computer engineer, this is an important concept to master, in view of its significance in the current state of technology. Unfortunately, in many curricula, the student is introduced to digital circuitry and immediately thrust into interfacing, due to the pressures of time in a traditional four-year academic career. Often, the student’s understanding of the basics of microcontroller operation and control are not to a satisfactory level before the student is expected to use a processor to control other, more complex, systems. This research attempts to compile a solution to allow a student to be well versed in microcontroller operation while he or she begins to work with additional interfacing requirements. A prototype printed circuit board (PCB) has been assembled that works in close harmony with the National Instrument ELVIS prototyping system that attempts to alleviate this problem. This prototype daughter card rests on top of the breadboarding area of the ELVIS system and allows the student full access to all of the tools and contacts that would be available without the card. The student is required to make the connections necessary for a fully-functional microcontroller system, as opposed to the method of using a pre-fabricated microcontroller development board. When using a board such as this, the student may not fully understand the ii individual components and their interconnections. This process of connecting components requires the student to understand the physical interface between the microcontroller and the peripheral device(s). Anticipated results from this research are an increased aptitude in peripheral interfacing and a greater level of success in more complex courses following in the curriculum. By allowing the student to interact with the interfacing process on a lower level, a more complete understanding of microcontroller-based systems and peripheral interfacing is obtained. iii DEDICATION This thesis is dedicated to all those who have supported me and my goals of achieving this milestone of my life. Specifically, I would like to dedicate it to my family and friends who helped me in some way during the time taken to complete this work. iv LIST OF ABBREVIATIONS AND SYMBOLS CMOS Complementary metal-oxide semiconductor DAC Digital-to-analog converter DC Direct current DIP Dual-inline package ECE Electrical and Computer Engineering EEPROM Electrically-erasable programmable read-only memory I2C Inter-Integrated Circuit IC Integrated circuit IDE Integrated development environment I/O Input and/or output LCD Liquid-crystal display LED Light-emitting diode LQFP Low-profile quad-flat pack MCU Microcontroller unit MCUPC Microcontroller Unit Peripheral Card MCU SLK Microcontroller Student Learning Kit NI National Instruments NI ELVIS National Instruments Educational Laboratory Virtual Instrumentation Suite PCB Printed Circuit Board v PWM Pulse width modulation QFP Quad-flat pack SPDIP Shrink plastic dual-inline package SPI Serial Peripheral Interface TTL Transistor-transistor logic vi ACKNOWLEDGMENTS I am appreciative of the opportunity to thank all those who have held some role in the compilation of this thesis. There are many who have helped me get to this point in my career, and I would like to thank a subset of them at this time. First and foremost, I would like to thank my Lord, for without His blessings, I would have nothing. Throughout my life, up to an including my time spent toward this goal, I have had the opportunity to work for my Master in His Kingdom and to enjoy the blessings and responsibilities that He has bestowed upon me. It is my hope that my Lord continues to find favor with me and my family for the remainder of my days on this earth. I thank my mother and father, Glenn and Teresa Taylor, for their faithful love, support, and willingness to help me in whatever way possible. Without the two of them, I would not have the opportunities that I have now. I thank my brother, Nick, and his family for their encouragement as well. Also, I thank the members of my graduate committee, Dr. Kenneth Ricks, Dr. Monica Anderson, and my committee chair, Dr. Jeff Jackson, for their tireless assistance and guidance through the compilation of this work. Countless times have I requested their direction and their wisdom, and never once have they failed me to this end. My progress is where it is today in no small part to their efforts. Finally, for the members of my family and for all those who have chosen to be a part of my life in some way, I thank you always for your consideration and for your love. vii CONTENTS ABSTRACT .................................................................................................................................... ii DEDICATION ............................................................................................................................... iv LIST OF ABBREVIATIONS AND SYMBOLS ........................................................................... v ACKNOWLEDGMENTS ............................................................................................................ vii LIST OF TABLES .......................................................................................................................... x LIST OF FIGURES ....................................................................................................................... xi 1. BACKGROUND AND MOTIVATION FOR MCUPC DESIGN ............................................. 1 2. THE MCUPC DESIGN .............................................................................................................. 7 3. IMPLEMENTATION OF THE MCUPC DESIGN ................................................................. 10 A. ADVANTAGES OF THE MCUPC ........................................................................................ 10 B. COMPONENTS SELECTED .................................................................................................. 16 C. PCB ARTIST ........................................................................................................................... 34 D. REQUIRED DESIGN SPECIFICATIONS ............................................................................. 36 E. IMPLEMENTATION .............................................................................................................. 38 4. INTRODUCTORY LABORATORY ASSIGNMENTS .......................................................... 41 5. ADVANCED LABORATORY ASSIGNMENTS ................................................................... 47 6. IMPLEMENTATION OF MCUPC SYSTEM AND MEASUREMENT OF RESULTS ....... 52 REFERENCES ............................................................................................................................. 55 APPENDIX A. REVISION 2.0 LAYOUT OF MCUPC .............................................................. 57 viii APPENDIX B. COMPLETE LABORATORY ASSIGNMENTS ............................................... 59 ix LIST OF TABLES 1. Pinout Diagram for the Microchip MCP23017 16-Bit I/O Expander ....................................... 22 2. Comparison of microcontroller selection.................................................................................. 25 3. Pinout Diagram for the PIC24HJ64GP502 microprocessor ..................................................... 27 4. Pinout Diagram for the MAX548ACPA+ DAC 8-DIP IC ....................................................... 32 5. Pinout Diagram for the Microchip Technologies 24LC515-I/P ............................................... 33 6. Pinout Diagram for Crystalfontz America CFAH1602B-TMI-JT Character LCD Module..... 34 7. Cost breakdown of components for five MCUPC laboratory systems ..................................... 52 x LIST OF FIGURES 1. Example printed circuit board with no recognizable traces ...................................................... 12 2. Subset of MCUPC showing traces ............................................................................................ 13 3. Subset of electrical engineering flowchart displaying prerequisite flow .................................. 14 4. Overhead view of NI ELVIS workstation ................................................................................ 15 5. Image of microprocessor unit orientation on MCUPC ............................................................. 16 6. Overhead view of Dragon12-Plus MCU from EVBplus/Wytec ............................................... 17 7. Overhead view of unpopulated MCUPC daughter card – Revision 2.0 ................................... 17 8. Pololu 270-Point Breadboard .................................................................................................... 19 9. Futurlec small 4x3 matrix-output keypad ................................................................................
Details
-
File Typepdf
-
Upload Time-
-
Content LanguagesEnglish
-
Upload UserAnonymous/Not logged-in
-
File Pages110 Page
-
File Size-