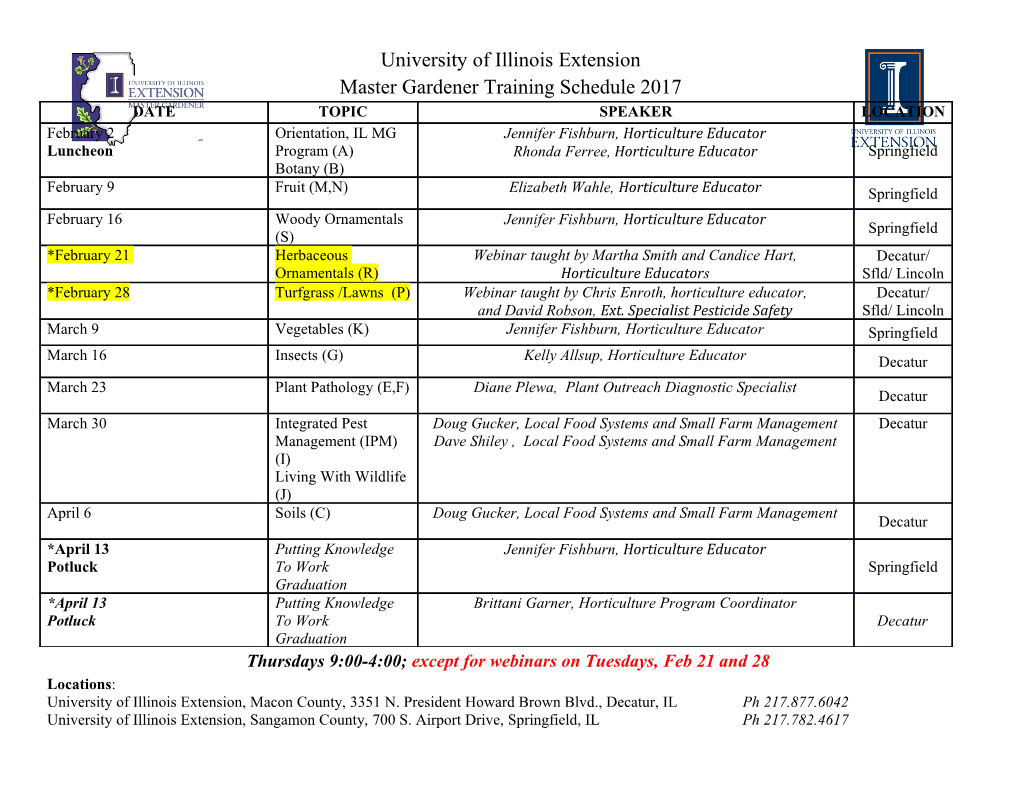
Available online at www.sciencedirect.com ScienceDirect Procedia Materials Science 6 ( 2014 ) 1770 – 1779 3rd International Conference on Materials Processing and Characterisation (ICMPC 2014) Comparative study of surface roughness and cylindricity of aluminium silicon nitride material using MRA GMDH & pattern recognition technique in drilling B.M.Umesh Gowdaa*, H.V.Ravindraa, S.Prathik Jainb, Mohinder N Raja, G.V.Naveen Prakeshc, G.Ugrasend aDept. of Mechanical Engg., P.E.S. College of Engineering, Mandya, Karnataka-571 401, INDIA bAssistant Professor, Dept. of Aeronautical Engg., Dayananda Sagar College of Engineering, Bnagalore, Karnataka-560 078, INDIA cProfessor, Dept. of Mechanical Engg, Vidya Vardhaka College of Engineering,Mysore Karnataka-570 002 INDIA. dAssistant Professor, Department of Mechanical Engineering, B.M.S. College of Engg., Bangalore, Karnataka-560 019, INDIA Abstract Drilling is one of the oldest and the most widely used of all machining processes, comprising about one third of all metal- machining operations. The present work consist of drilling an aluminum silicon nitride composite forged plate using high-speed steel drill bit and was carried by varying the cutting speed and feed. Theoretical analysis in the present work involved monitoring of drilled hole status of composite based on surface roughness and cylindricity using the independent variables machining time, tool tip temperature, vibration, flank wear (both average and maximum), cylindricity and cutting conditions by sophisticated methods of signal analysis like Multiple Regression Analysis (MRA), Group method Data Handling Technique (GMDH) and Pattern Recognition Technique (PRT) like Back Propagation Neural Network (BPNN) was used. Comparisons of the three theoretical methods for estimation of surface roughness and cylindricity with measured one were carried out. The influence of network architecture is used to know the drilled hole status based on surface roughness and cylindricity was studied. ©2211 2014-8128 Elsevier © 2014 Ltd. TheThis Authors.is an open Published access article by Elsevierunder the Ltd. CC BY-NC-ND license (Selectionhttp://creativecommons.org/licenses/by-nc-nd/3.0/ and peer-review under responsibility ).of the Gokaraju Rangaraju Institute of Engineering and Technology (GRIET). Selection and peer review under responsibility of the Gokaraju Rangaraju Institute of Engineering and Technology (GRIET) Keywords: MRA, GMDH, PRT, BPNN 1. Introduction Drilling is one of the oldest and the most widely used of all machining processes, comprising about one third of all metal-machining operations. It is used to create or to enlarge a hole in a work piece by the relative motion of a cutting tool, called a drill or drill bit. __________________ * Corresponding author. Tel.: +91-8232-220043; fax: +91-8232-222075. E-mail address: [email protected] 2211-8128 © 2014 Elsevier Ltd. This is an open access article under the CC BY-NC-ND license (http://creativecommons.org/licenses/by-nc-nd/3.0/). Selection and peer review under responsibility of the Gokaraju Rangaraju Institute of Engineering and Technology (GRIET) doi: 10.1016/j.mspro.2014.07.207 B.M. Umesh Gowda et al. / Procedia Materials Science 6 ( 2014 ) 1770 – 1779 1771 The choice of a drilling method depends on the size, tolerance, and surface finish needed, as well as the production requirements. Several factors influence the quality of drilled holes. The most obvious ones are the cutting conditions (cutting speed and feed rate) and cutting configurations (tool material, diameter, and geometry). Aluminum Matrix Composites (AMC) refers to a class of light weight and high performance aluminum centric material systems. In the present work Aluminum Silicon Nitride (AlSiN) is a Metal Matrix Composite (MMC) have higher thermal conductivity of 170 – 230 W/mK and low material density of 3.3 g/cm3 makes it ideal for weight sensitive applications. Past researchers stated that the machining of Al/SiC materials with different drill bit was difficult due to the presence of reinforced SiC-particulates in the metal matrix composite and it was found that at spindle speed 1300 rpm with 0.025 mm/rev feed rate is recommended for better surface finish using pure carbide drill bit, Alakesh Manna and Kanwaljeet Singh (2011). To predict the effects of thermal distortion of the drill and workpiece on the diameter and cylindricity of dry drilled holes. The model predicts that thermal expansion of the drill is the dominant effect and leads to oversized holes with diameters that increase with depth, Matthew Bono and Jun Ni (2001). The effect of cutting parameters on the hole quality (circularity and hole diameter) and tool wear during the drilling of super alloy Inconel 718 and proposed that cutting speed and feed rate played a great role in the variation of deviation from circularity values. As the feed rate increased, deviation from circularity values also increased, Turgay Kivak et al. (2012). HSS twist drills with different geometry for drilling of carbon/epoxy composites and stated that the delamination develops along the fiber direction and is developed in two phases, the chisel edge action phase and the cutting edge action phase, Sedlacek J and M. Slany (2010). The cutting of metal, high temperatures are generated in the region of the tool cutting edge, and these temperatures have a controlling influence on the rate of tool wear, it was observed that the influence of cutting speed is the most effective parameter that effects tool temperature than other parameters, Ali Fata (2011). The optimum cutting parameters to optimize the surface roughness of the hole and its diameter accuracy in the dry drilling process based on the selected setting parameters. The selected cutting parameters for this study were the cutting speed, feed rate, and the hole depth. The effect of these parameters on the hole diameter accuracy and its surface roughness are measured and analysed. In this study it is revealed that feed rate is prominent factors which affect hole diameter in the dry drilling of aluminum alloy 6061, Ahmad Fauzi and B Ahamed (2010). A vibration monitoring is the most widely used technique because most of the failures in the machine tool could be due to increased vibration level, Jagadish. M.S and H.V. Ravindra. A Multiple Regression model to predict the in-process surface roughness of a machined workpiece in turning operation. The model was developed to use machining parameters, such as feed rate, spindle speed, depth of cut, and vibration as predictors. They have shown that feed rate had the greatest correlation coefficients and other primary variables were much smaller than feed rate, Luke huang and Dr. Joseph C. Chen (2001). The use of algorithms of the Group Method of Data Handling (GMDH) in solving various problems of experimental data processing, Lvakhnenko A.G. and G.A.lvakhnenko (1995). GMDH is a powerful tool for mathematical modeling that can be used to solve a wide variety of different real-time problems and GMDH was recommended to solve small and medium- sized problems, Dolenko et al. (1996). HSS twist drills with different geometry for drilling of carbon/epoxy composites stated that delamination develops along the fiber direction. It is developed in two phases, the chisel edge action phase and the cutting edge action phase. The feed rate and drill diameter are seen to make the largest contribution to the overall performance, the candle stick drill and saw drill cause a smaller delamination factor than twist drill. The confirmation tests demonstrated a feasible and an effective method for the evaluation of drilling induced delamination factor in drilling of composite material, Tsao C.C. and H. Hocheng (2004). An Artificial Neural Network (ANN) model can be used as a prediction tool flank wear for determining the delamination for any given set of input machining parameters, namely, speed, drill size and feed, Krishnamoorthy, et al. (2011), Panda et al. (2006). Drilling operations on mild steel work piece by high-speed steel (HSS) drill bits over a wide range of cutting conditions. Important process parameters have been used as input for BPNN and drill wear has been used as output of the network. It was concluded that inclusion of chip thickness as input to the neural network not only reduces mean square training error but also it is achieved at a much less number of iteration, Panda et al. (2006). 1772 B.M. Umesh Gowda et al. / Procedia Materials Science 6 ( 2014 ) 1770 – 1779 2. Experimental Work The experimental work consists of drilling aluminium silicon nitride composite using High-Speed Steel drill bit. The machining was carried out in an automatic drilling machine tool. The experiments were conducted for different cutting speeds and feeds combinations. The cutting speeds considered are 11.309 m/min, 15.39 m/min and 21.36 m/min. Feeds considered are 0.095 mm/rev, 0.190 mm/rev and 0.285 mm/rev. In all the cutting conditions for each hole vibration velocity was measured using Shock Pulse Meter and temperature at tool tip using heat spy was measured during drilling process. And surface roughness, cylindricity and circularity are measured using handysurf meter, digital caliper and tool maker’s microscope respectively. Machining was stopped at regular intervals of time and both average and maximum flank wear was measured using tool makers microscope. Experimental set-up is as shown in the Fig. 1 and location of shock pulse meter sensor probe is shown in Fig. 2. The work material specifications are shown in Table. 1 and tool material specifications are given in Table 2. Fig. 1. Experimental set-up Fig. 2. Location of SPM sensor Table 1. Composition of work material Table 2. Drill bit specification Tool material HSS Work material AlSiN Diameter of the drill bits 10mm Hardness 54.3BHN used Al Remaining Chisel edge angle 120◦ to 135◦ Cu 0.479% Helix angle or rake angle 30◦ Mg 0.762% Point angle 118◦ Si 0.684% Lip clearance angle 12◦ Fe 0.246% Mn 0.028% Ni <0.05% Pb 0.024% Sn 0.011% Ti 0.015% Zn 0.008% B.M.
Details
-
File Typepdf
-
Upload Time-
-
Content LanguagesEnglish
-
Upload UserAnonymous/Not logged-in
-
File Pages10 Page
-
File Size-