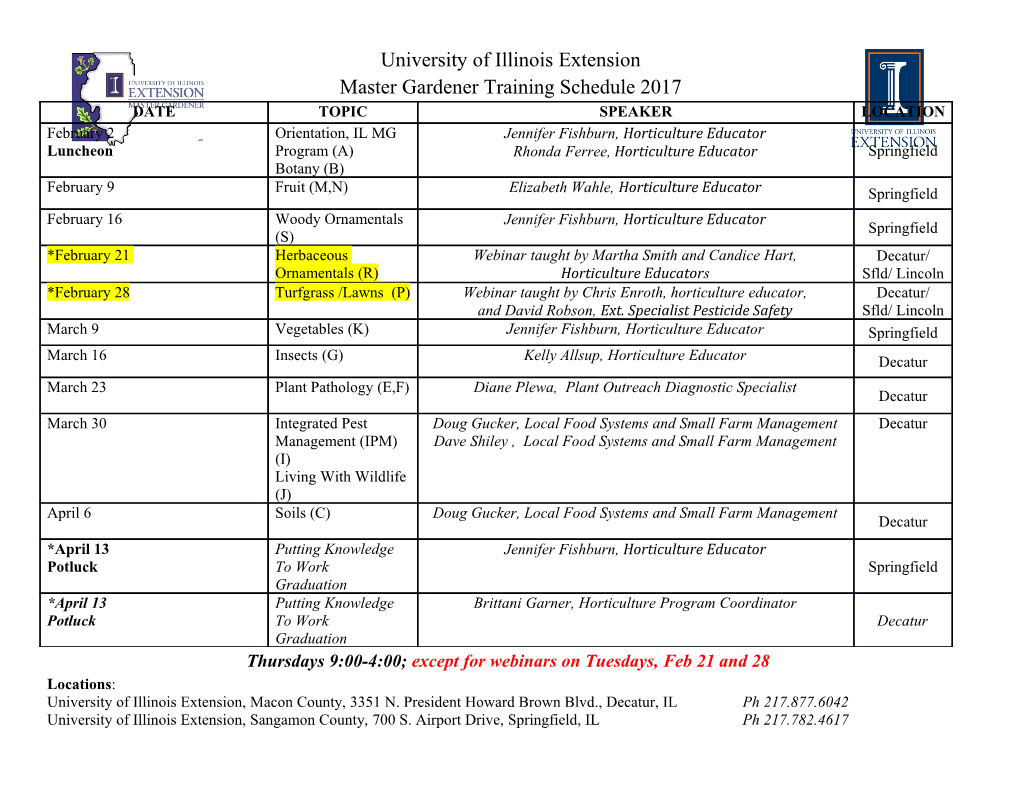
NON-INTRUSIVE CURRENT SENSING WITH GIANT MAGNETORESISTANCE SENSORS FOR POWER DISTRIBUTION MONITORING A Thesis Presented to the Faculty of San Diego State University In Partial Fulfillment of the Requirements for the Degree Master of Science in Electrical Engineering by Jonathan Thomas Hammer Fall 2018 iii Copyright c 2018 by Jonathan Thomas Hammer All Rights Reserved iv DEDICATION Dedicated to my family. v However difficult life may seem, there is always something you can do and succeed at. – Stephen Hawking vi ABSTRACT OF THE THESIS Non-Intrusive Current Sensing with Giant Magnetoresistance Sensors for Power Distribution Monitoring by Jonathan Thomas Hammer Master of Science in Electrical Engineering San Diego State University, 2018 With accelerating Smart Grid and automated Smart Building technologies, there is an ever-increasing demand for non-invasive, networked load monitoring. Magnetometers leveraging Giant Magnetoresistance (GMR) can be used to measure electrical currents via their inherent magnetic fields. Research is conducted to characterize these sensors and investigate their usefulness in a wireless embedded system for the purposes of energy management in power distribution equipment. An example embedded system design is proposed as a non-intrusive power monitoring solution. The goal of such a system is that it can be installed without opening the electrical equipment or removing the faceplate, so that power management can be employed without requiring qualified electricians. This work investigates realistic scenarios for employing GMR sensors in power distribution load centers with multiple circuits. Research is done to assess how multiple current sources create magnetic fields in panelboards, and how an array of GMR-based magnetic field sensors may be used to capture power load events. Methods for collecting and processing multi-channel sensor data are discussed, particularly techniques for eliminating signal crosstalk between the channels. Through several experiments on two purpose-built testbeds, a calibration method is developed for the sensor array. Using the calibrated sensor array, measurements of electrical currents are made with a percent error ranging from 0.82% to 15.88% for active loads. vii TABLE OF CONTENTS PAGE ABSTRACT .................................................................................... vi LIST OF TABLES.............................................................................. ix LIST OF FIGURES ............................................................................ x GLOSSARY .................................................................................... xiii ACKNOWLEDGMENTS ..................................................................... xvi CHAPTER 1 INTRODUCTION ..................................................................... 1 1.1 Submeter Load Monitoring ..................................................... 1 1.2 Non-invasive Energy Management ............................................. 2 1.3 Magnetoresistance .............................................................. 4 1.4 Sensing Current ................................................................. 9 1.5 Measuring Power................................................................ 9 2 DISCOVERY........................................................................... 11 2.1 Ratiometric Response ........................................................... 11 2.2 Front-End Circuit Design ....................................................... 13 2.3 Omnipolar Response ............................................................ 14 2.4 Model............................................................................ 16 2.5 Circuit Breaker Form Factor .................................................... 17 3 EXPERIMENTS ....................................................................... 19 3.1 Test Bench 1 ..................................................................... 19 3.2 Test Bench 2 ..................................................................... 22 3.2.1 Load Sequence Test ....................................................... 26 3.2.2 Simultaneous Loads Test .................................................. 29 3.2.3 Simultaneous Loads Test with Differing Loads .......................... 32 4 CORRECTION TECHNIQUES ...................................................... 34 4.1 Orientation....................................................................... 34 4.2 Sensitivity Matrix Calibration .................................................. 37 4.2.1 Calibration Steps........................................................... 39 viii 4.2.2 Inverse Sensitivity Matrix Correction Results............................ 40 4.3 Independent Component Analysis.............................................. 47 5 EMBEDDED DEVELOPMENT...................................................... 52 5.1 Design ........................................................................... 52 5.2 Applications ..................................................................... 54 6 Conclusion and Future Work .......................................................... 56 BIBLIOGRAPHY .............................................................................. 57 APPENDIX SENSOR ARRAY CALIBRATION ARTIFACTS ....................................... 60 ix LIST OF TABLES PAGE 2.1 Ratiometric Response of GMR Sensor................................................ 12 2.2 Ratiometric Saturation of GMR Sensor ............................................... 12 4.1 Summary of GMR Sensor Orientation Analysis ..................................... 37 4.2 Current Measurement at n = 5300 (Quiescent) from Simultaneous Loads Test with Differing Loads ...................................................... 45 4.3 Current Measurement at n = 7300 from Simultaneous Loads Test with Differing Loads ........................................................................ 45 4.4 Current Measurement at n = 9300 from Simultaneous Loads Test with Differing Loads ........................................................................ 45 4.5 Current Measurement at n = 11300 from Simultaneous Loads Test with Differing Loads ........................................................................ 46 A.1 Scaling Vector from Load Sequence Test ............................................. 61 A.2 Sensitivity Matrix from Load Sequence Test ......................................... 62 x LIST OF FIGURES PAGE 1.1 Current transformers for measuring current. (Left) Electricians hand- held clamp meter [11]. (Right) Split-core current transformer [12]. ............... 3 1.2 Line splitter for plug load monitoring with current clamp [14]. .................... 4 1.3 Eaton Smart Breaker [18]. Below the Eaton logo reads “REMOTELY OPERATED OVER WIFI”. ........................................................... 5 1.4 Layers of GMR composite material. The outer layers are ferromagnetic (FM) and the inner layer is nonmagnetic (NM). The Ferromagnetic (FM) layers have antiparallel magnetic moments. All electrons in the non- magnetic (NM) conduction layer are subjected to strong scattering in absence of external magnetic field. ................................................... 5 1.5 GMR material in presence of external magnetic fields. (Left) External magnetic field oriented up causes ferromagnetic (FM) layers to align up and reduces the scattering of electrons with up spin in the nonmagnetic (NM) conduction layer. (Right) External magnetic field oriented down causes FM layers to align down and reduces scattering of electrons with down spin in the NM conduction layer. .............................................. 7 1.6 Resistance of GMR material versus applied magnetic field [21]. Notice the omnipolar response. ............................................................... 8 1.7 (Left) SOIC8 packaged GMR sensor and (Right) Functional diagram of GMR sensor [21]. The axis of sensitivity to magnetic fields is parallel to the plane. ............................................................................ 8 2.1 Schematic of front end-amplifier circuit for GMR current sensor. The GMR sensor is internally configured as a Wheatstone half-bridge. ................ 13 2.2 GMR sensor output voltage versus external magnetic field in Oersteds [29]. An omnipolar response is shown. Notice the hysteresis, which places two aliases of the response about the origin. ................................. 14 2.3 Oscilloscope capture of four GMR current sensor outputs. The operat- ing point allows the center of the “V” to be crossed, leading to reduced linearity and malformed sine waves. ................................................. 15 2.4 Various DC magnetic operating points of the GMR sensor [28]. The magnetic bias is indicated by (p). (a) shows no magnetic bias. (b) shows a slight magnetic bias. (c) shows enough magnetic bias to prevent signal distortion. .............................................................................. 16 xi 2.5 Cross section of Eaton BR 15A breaker [31]. Annotated is the place- ment of a stick-on GMR sensor and the theoretical magnetic field of the current in the conductor. .............................................................. 18 3.1 Experiment 1 Test Bench. Two circuits are loaded with various settings of a “dummy load” resistor box along with multiple combinations of heat lamps to vary the load. ........................................................... 20 3.2 GMR Sensors directly on conductor, arranged perpendicular to each other.
Details
-
File Typepdf
-
Upload Time-
-
Content LanguagesEnglish
-
Upload UserAnonymous/Not logged-in
-
File Pages78 Page
-
File Size-