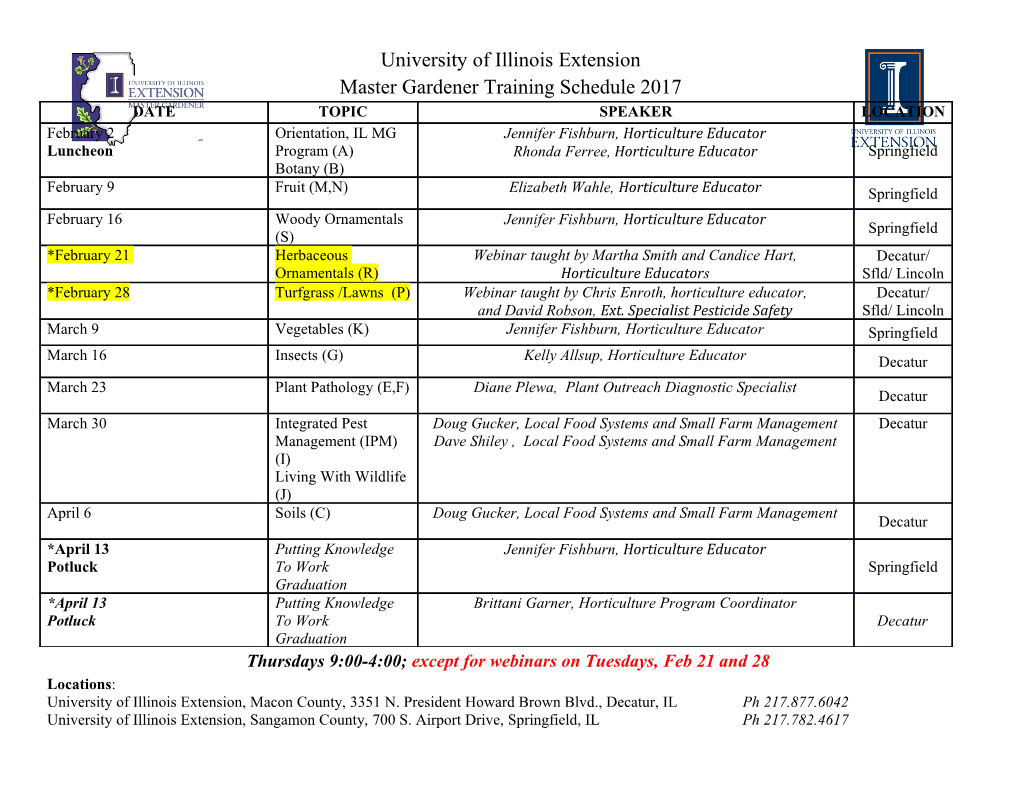
Reconditioning of Aluminium Engines Contents Page Chapter 1: General 3 1.1 Reasons for using aluminium cylinder blocks 3 1.2 Known brands of aluminium alloys for cylinder blocks 3 1.3 Vehicles/engines with aluminium cylinder blocks 3 1.4 Design details 3 1.5 Composite materials for cylinder liners. Aluminium/ cast iron 4 1.6 Use of Cr-coated piston rings 4 1.7 KS cylinder liners for Alusil engines 4 Chapter 2: Reconditioning an Alusil®cylinder block 5 2.1 Preparatory machining of the cylinder block 5 2.2 Installation of the Alusil 6 cylinder liner 2.2.1 Installation with dry ice 6 2.2.2 Installation with liquid nitrogen 6 2.2.3 Preheating of the cylinder block 6 2.2.4 Fitting the cylinder liner 7 2.3 Planing of the cylinder block 7 2.4 Prehoning, finish honing, polishing 8 2.5 Silicon lapping 8 2.6 Tables 9 Chapter 3: Reconditioning a Lokasil cylinder block based on the example of the Porsche Boxster engine 14 Chapter 4: Reconditioning the threads for the cylinder head bolts 16 Chapter 1: General 1.1 Reasons for using alumin- 1.3 Vehicles/engines with alu- 1.4 Design details ium engine blocks minium cylinder blocks Alusil: It has always been a challenge • Alusil base material is expensi- for engine designers to make, GALNIKAL / NIKASIL ve and difficult to machine due besides cylinder heads and pis- to the high silicon content tons, the entire cylinder block BMW • Boring the cylinder block is from aluminium without addition- 2.0 Litre 6 cylinders possible al cylinder liners or surface rein- 2.5 Litre 6 cylinders M52 • Oversized pistons are availa- forcements. Besides a favour- ble 2.8 Litre 6 cylinders M52 able running behaviour due to • Pistons in Alusil blocks are weight reduction, it is especially 3.0 Litre V8 coated with iron and tin the heat balance which can be 4.0 Litre V8 controlled much more easily be- Motorbike 100 K Galnikal: cause the thermal conductivity of • Galnikal base material is chea- aluminium is about 4 times high- JAGUAR per than Alusil and easier to er. The engine warms up more machine due to its substantial- V 8 quickly and uniformly. So the ly lower silicon content weight savings are not limited to • The cylinder bore is nickel the cylinder block weight but a coated reduction of the cooling water ALUSIL / SILUMAL • Boring the cylinder block is not volume is also possible because possible because of the nickel of the better thermal conductivity MERCEDES-BENZ coat ! and heat radiation of the cylinder 3.8 Litre before 8.81 • Oversized pistons are not block. 3.8 Litre after 8.81 available 4.2 Litre 5.0 / 5.6 Litre Chromium cylinders: 6.0 Litre • As Galnikal 1.2 Known brands of aluminium • but: the cylinder bore is chro- alloys for cylinder blocks PORSCHE 928 mium coated 928 S KOLBENSCHMIDT MAHLE 944 Lokasil / KS patent: • Lokasil base material costs BMW Alusil Silumal less than Alusil and is easier to 750 i process. 3.5 Litre V8 Galnikal Nikasil • Preforms, which are special 4.4 Litre V8 prefabricated liners from Loka- Chrome cylinder Cromal AUDI sil with a high silicon content of V8 4.2 Litre 20 - 27 %, are cast into the cy- Lokasil (KS patent) V6 2.8 Litre linder bore • Oversized pistons are availa- ble LOKASIL • Boring of the cylinder block is possible PORSCHE Boxster 1.5 Composite materials for cylinder liners. Alu- minium/cast iron KOLBENSCHMIDT MAHLE Alfin cylinder Biral cylinder Alfin cast into cylinder Outer cylinder wall surface rough 1.6 Use of Cr-coated piston rings KOLBENSCHMIDT MAHLE Cr piston rings Alfin cylinder Biral cylinder possible Alusil Silumal possible Galnikal Nikasil not possible Chrome cylinder Cromal not possible 1.7 KS cylinder liners for Alusil engines Manufacturer/engine KS Art.No. Flange dia- Flange Outside dia- Inside dia- Length meter (mm) height(mm) meter (mm) meter (mm) (mm) MB 3.8 Litre before 8.81 89 321 190 97.50 4.70 95.50 91.00 134.70 MB 3.8 Litre after 8.81 89 189 190 93.50 4.70 91.50 87.00 134.70 MB 4.2 Litre 89 321 190 97.50 4.70 95.50 91.00 134.70 MB 5.0/5.6 Litre 89 190 190 102.00 4.70 100.00 95.50 155.70 MB M120 12 Cyl. 89 418 190 94.50 4.70 92.50 88.00 131.55 PORSCHE 928S 1984-1986 Diameter 97mm 89 190 190 102.00 4.70 100.00 95.50 155.70 PORSCHE 928 from1985 Diameter 100 mm 89 327 190 107.00 4.70 105.00 99.50 145.00 reduce to block height PORSCHE 944 89 327 190 107.00 4.70 105.00 99,50 145,00 BMW M70 12 Cylinder 89 400 190 89.00 4.70 87.00 83.00 126.50 ALUSIL raw casting 89 397 190 — — 110.00 90.00 160.00 on request 4 Chapter 2: Reconditioning an Alusil®cylinder block 2.1 Preparatory machining of 1st stage: Pre-boring with a mate- they may be subject to dimen- the cylinder block (Fig. 1) rial removal of sional changes in unstressed Tighten the bearing cap applying 7/10 mm max. condition, such as oval deforma- the torque specified by the engine 2nd stage: Finish boring with a tion, but when installed, after the manufacturer. Next, clamp the cyl- material removal of shrinking process, they will again inder block onto the boring ma- 5/10 mm max. revert to the cylindrical shape of chine, align it roughly and than Then the flange support is turned the base bore. Subsequently, the fasten it. Swivel the cylinder block to a diameter “B” to a depth of “C” top edge of the cylinder bore is to and set it to the final machining (values see Table 1, page 9). be provided with a chamfer of 0.5 position by fine alignment. In order to avoid the risk of liner + 0.1 mm x 45°. The semi-finished Alusil cylinder flange cracking, care should be liners offered by KS are manufac- taken to ensure that the support tured to a high degree of accuracy. surface of the liner flange is ex- The outside diameter tolerance is actly perpendicular to the cylinder 0.03 mm max. bore. In order to achieve an exact bore, The diameters for the respective the following work sequences are engine types can also be found recommended for preparing the listed in Table 1. As dry cylinder bore to accommodate Alusil liners: liners have extremely thin walls, Figure 1 5 2.2 Installation of the Alusil 2.2.2 Installation with liquid 2.2.3 Preheating of the cylin- cylinder liner nitrogen (Fig. 3) der block (Fig. 4) 2.2.1 Installation with dry ice The cylinder liner is placed in A heating oven with appropriate (Fig. 2) liquid nitrogen and reaches a dimensions is ideal for heating A relatively simple method is to temperature of -180° C. Liquid up the cylinder block. The cylin- nitrogen may be obtained from der block remains in the preheat- use CO2 (carbon dioxide) filled into riser-type pressure bottles. the local gas dealer. ed oven for about 20 - 30 min- Physical principle: when the gas utes. flows out, dry ice is forming due If the installation is done with dry to the sudden strong expansion. ice, it is essential to preheat the The dry ice may be collected in cylinder block to a temperature an insulated container. This insu- of 160° C. It is not absolutely lated container should meet the necessary to preheat the cylinder necessary demands on insulation block if the installation work is and strength. The cylinder liner done with liquefied nitrogen. may be cooled down to about - However, if there is a possibility, 80°C with the dry ice. we would recommend about 100 - 120°C. A temperature difference be- tween cylinder block and liner of about 200°C is necessary to en- sure safe installation. Figure 3 Figure 2 Figure 4 6 2.2.4 Fitting the cylinder liner (Fig. 5) Installing the cylinder liner is ab- solutely unproblematic. By cool- ing the cylinder liner, its diameter will decrease by about 0.1 mm whereas by preheating of the cylin- der block, the base bore will be- come enlarged by about 0.25 mm, so that when fitting the liner, there will be a clearance of about 0.35 mm. However, the Alusil cylinder liner should be installed relatively quickly because this is a cylinder liner of extremely thin walls and aluminium is a very good heat conductor. 2.3 Planing of the cylinder block (Fig. 6) After aligning, the cylinder block is planed. The material removal should be 0.1 mm in order to en- sure a perfectly plane surface. Figure 5 Figure 6 7 2.4 Prehoning, finish honing, With this machining step, the polishing (Fig. 7) silicon crystals in the cylinder Honing should be done using a block are exposed, which leads Sunnen honing machine. For the to a more durable and wear-resi- first 3 honing phases (prehon- stant cylinder surface. ing, finish honing, polishing), different honing stones are to be applied. The type of tool used (honing stones, honing oil) and the machine adjustments are im- portant for efficient machining and may differ from engine type to engine type. The respective values can be read from the va- rious tables provided. Figure 7 2.5 Silicon lapping (Figs.
Details
-
File Typepdf
-
Upload Time-
-
Content LanguagesEnglish
-
Upload UserAnonymous/Not logged-in
-
File Pages20 Page
-
File Size-