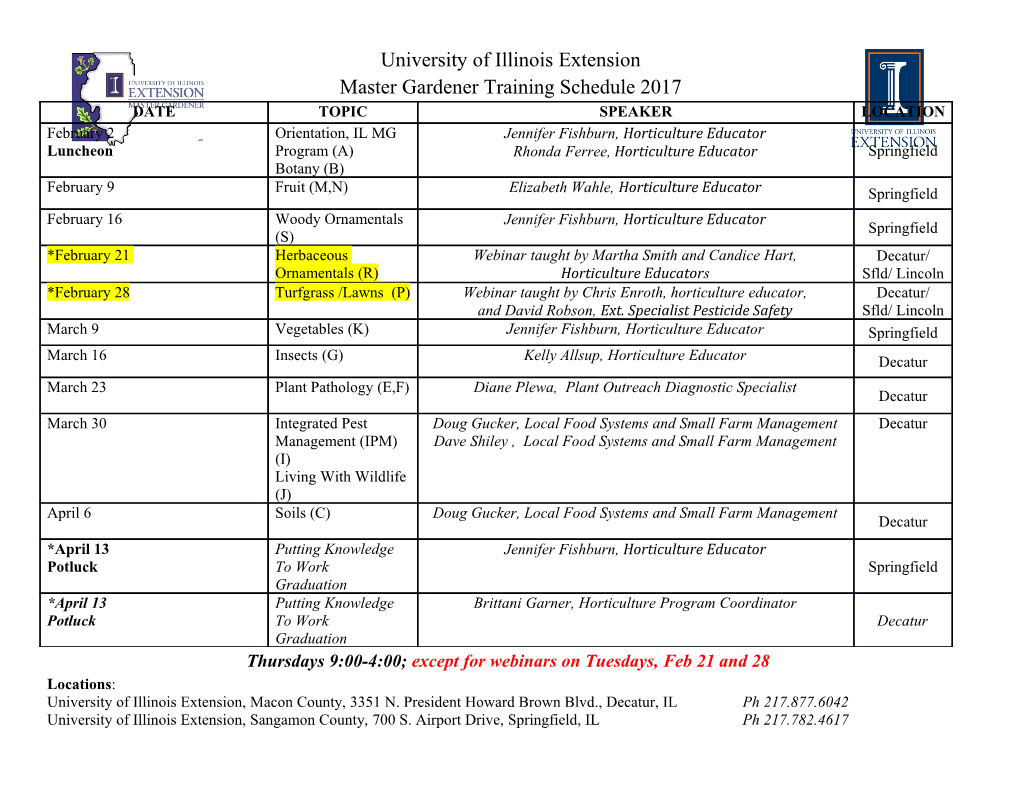
Look around you—on store shelves, in your home—and you’re certain to see material that’s been printed by flexography. Though often taken for granted, packaging is everywhere, and so, too, is flexography; it prints candy wrappers, shopping bags, corrugated boxes, milk cartons, gift wrap, wallpaper, and many other goods and packages. Printing on packaging is essential to businesses around the world. In fact, graphics on packages provide some of the most important advertising for the products themselves. Flexography’s soft compressible plates, fast-drying inks, and its simple, efficient inking system make it possible for manufacturers to reproduce high-quality graphics on a wide variety of surfaces. Over the last decade, the use of the flexographic printing process has been growing approximately eight percent a year, a rate unparalleled by any other printing technology. Although some of this growth can be attributed to a greater need for packaging, flexography is increasingly used in markets traditionally served by gravure and offset lithography. Since advances in technology have significantly improved flexography’s ability to print accurate type, color, and halftone images, manufacturers and print buyers are recognizing flexography as a high-quality, economical alternative to gravure and lithographic printing. This booklet describes the flexographic printing process from start to finish, including design, color, and prepress considerations. Understanding the requirements of flexography helps ensure that designs will look their best, and will aid in the communication between print buyers, in-house prepress departments, service bureaus, and printers. 2 Flexographic Markets 4 Traditional Printing Processes Contents 6 Flexographic Technology 8 Flexographic Plates 9 Plate Elongation & Distortion 10 Substrates 11 Color Capabilities 12 Trapping 13 Type 14 Color Management 15 Dot Gain 16 Halftones & Screening 18 Step-and-Repeat & Die-Cutting 19 Prepress Output 20 Proofing 21 Prepress Checklist & The Press Check 22 Glossary & Index The terms printed in red throughout this guide can also be found in the glossary. 1 The use of flexography is grow- Market Categories ing in popularity in today’s The use of the flexographic process has continued to grow in all packaging markets, printing markets, where short including those that have traditionally used gravure and lithographic methods. run, low-cost, and high-quality Corrugated are crucial to success. A look at By far the largest market for flexography, the development of flexography reveals corrugated is printed on sheet-fed presses. a printing technology and culture that Fast drying water-based inks, the soft, conforming plate, and light impression has been willing and capable of change pressure make flexography well suited for in response to the needs of the packag- printing corrugated boxes in large quantities. ing industry. An evolutionary process of improvements in materials and Flexographic Markets Flexographic equipment, rather than a single discov- Flexible Packaging ery, has led to flexography as it is Most flexible packaging uses non-absorbent known today. polymer film, including bread bags, snack food bags, candy wrappers, pouches, and textile wrap. The first use of soft compressible plates can be traced back to the late 1880s, when letterpress printers needed to find a way to print kraft paper grocery bags and corrugated boxes. The materials Gift Wrap and Wallpaper were rough in texture, and did not A continuous repeat allows the printing of respond well to the ink transfer pressure products such as wallpaper and gift wrap. of hard letterpress plates. To solve the Design rolls, which do not have a plate seam, are used to print a continuous back- problem, printers began creating plates ground color. from rubber, rather than from wood or lead. This quickly became the dominant method for printing corrugated, and Folding Cartons also grew steadily in the bag printing Although folding cartons, including cereal, industry. In 1914, the Interstate Com- detergent, and cosmetic boxes, are printed merce Commission approved the corru- by both the lithographic and gravure pro- cesses, flexography has recently increased gated box as a shipping container, a its market share due to improved quality. decision that began a new growth period for flexography. Clear Packaging In the early-to-mid 1920’s, flexographic Rigid Paper Boxes printers responded quickly to the intro- Rigid paper boxes, or pre-formed boxes duction of cellophane as a clear packag- are used for bakery products, shoes, and neckties. ing material. White inks were developed, drying systems were improved for cello- phane’s non-absorbent surface, and press tension systems were refined to handle Envelopes its caliper and weight. Approximately Flexography is used to print many kinds ten years later, polyethylene was intro- of envelopes, including those for direct duced, and went on to become the most mail, sweepstakes, general mailing, and overnight delivery. The security printing commonly used material for clear, flexi- on the inside of many envelopes is often ble packaging. applied by flexography. 2 Origins of the Name Originally, flexography was known as aniline printing, a name taken from Paper Grocery Bags the aniline dyes used as colorants for The paper bag is the original flexographic product. In the late 1800’s flexography the ink. Aniline dyes, however, were evolved from the need to apply graphics considered toxic and eventually banned to plain brown grocery sacks. The evolution continues today. for use on food packaging. New inks were developed as replacements, but the name remained until 1951, when Franklin Moss, a leader in package Plastic Carrier Bags printing, started a campaign to change Flexography can add advertising and it. He asked aniline printers and suppliers graphics to plastic bags that are carried for suggestions, receiving over two by customers in stores. hundred. Of those, three finalists were selected: permatone process, rotopake process, and flexography. After a vote, the process came to be known as flexog- raphy in 1952. Milk Cartons Approximately 90% of all milk cartons In the United States, the Clean Air Act are printed using flexography. of 1980 began a development in flexog- raphy toward environmentally friendly printing using low-solvent and no-solvent inks. Today, flexography is often chosen because of the ability to print with clean water based or solventless ultraviolet inks. Newspapers In the United States alone there are Today the process continues to adapt. between 35 and 40 newspapers using the flexographic printing process for the As the technology is refined, quality entire paper. Many newspapers use flex- continues to increase, making flexogra- ography to print the Sunday comics. phy the leader in packaging graphics applications. Tags and Labels The fast drying fluid inks used by flexogra- phers allow inline die cutting immediately after printing. The quality of many flexo- graphic labels is equal to or better than that offered by lithography or gravure. Pre-printed Linerboard Pre-printing linerboard allows high-quality graphics to be placed on corrugated containers. 3 The three most widely used Offset Lithography printing processes in use today are offset lithography, gravure, and flexography. Printing presses for each method differ primarily in design of the image carrier or printing plate, the ink, and the ink delivery system to the printing plate. Offset Lithography Widely used in the publication indus- try, offset lithography presses print magazines, catalogs, and daily newspa- pers, as well as annual reports, advertising, and art reproduction. Offset lithography Traditional Printing Processes Printing Traditional can also print paper-based packaging, such as cartons, labels, and bags. Gravure Offset lithography is a planographic process, meaning that the printing plate holds both the image and non-image areas on one flat surface or plane. On most offset presses, image areas on the plate are chemically treated to attract the lithographic paste ink, while a fountain solution or ink repellent chemical treatment protects non-image areas from inking. From the plate, the image is first transferred to a blanket (hence the term offset), and then to the paper or other material, known as the substrate. To dry, most lithographic inks require a certain period of time or an application of heat. Flexography Gravure The gravure method, sometimes known as roto-gravure, is used on a wide vari- ety of substrates, including vinyl floor- ing, woodgrain desktops, and paneling. It is the second most often used process in Europe and the Far East, and the third in the United States. Gravure is used to print high-volume products such as packaging, magazines and the advertising inserts found in newspapers. In addition, offset versions of gravure presses are used to print labels or logos 4 Traditional Printing Processes on medicine capsules and the “M” on M&M® candy. Offset Gravure Flexography Lithography Gravure is an intaglio process, in which the image area is recessed below the level of the non-image areas. The image Typical Magazines, Magazines & Newspapers, Uses newspapers, catalogs, Sunday phone directories, is etched or engraved in a cell format advertising pieces, supplements, candy corrugated onto a copper plate or copper-plated annual reports, cereal wrappers, cereal containers, bread boxes, bags, tags & boxes, snack food bags, cereal boxes, cylinder. By varying the size and depth labels bags, vinyl flooring milk cartons, gift of each cell,
Details
-
File Typepdf
-
Upload Time-
-
Content LanguagesEnglish
-
Upload UserAnonymous/Not logged-in
-
File Pages28 Page
-
File Size-