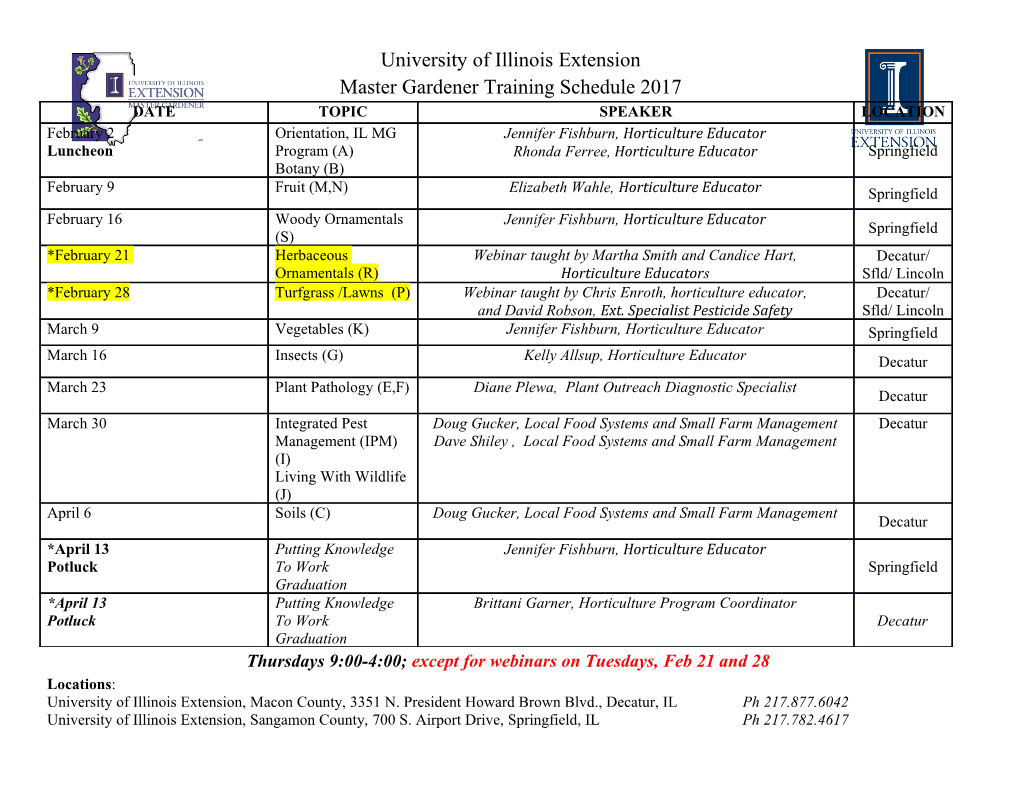
ME477 Fall 2004 Introduction SHEET • Cutting and forming thin sheets of metal usually performed as cold working METALWORKING • Sheet metal = 0.4 (1/64) to 6 mm (1/4in) thick 1. Cutting Operation • Plate stock > 6 mm thick 2. Bending Operation • Advantage - High strength, good dimensional 3. Drawing accuracy, good surface finish, economical mass 4. Other Sheet-metal Forming production (low cost). 5. Dies and Presses • Cutting, bending, drawing γ 6. Sheet-metal Operation ε1 Localized necking 7. Bending of Tube Stock θ=55° Because ν=0.5 in plasticity, ε =-2ε =-2ε ε3,ε2 ε1 ε ε2 1 2 3 2θ 1 2 Sheet Metalworking Terminology Sheet-metal Characteristics • Elongation – the capability of the sheet metal to stretch without necking and failure. • “Punch-and-die” • Yield-point elongation – Lüeder’s bands on Low-carbon steels and Al-Mg alloys. – Tooling to perform cutting, bending, and Lüder’s bands can be eliminated by cold-rolling the drawing thickness by 0.5-1.5%. Yupper • “Stamping press” Ylower – Machine tool that performs most sheet metal • Anisotropy operations – Crystallographic and mechanical fibering anisotropy • Grain Size effect on mechanical properties • “Stampings” • Residual Stress, Springback and Wrinkling – Sheet metal products • Testing method – Cupping test – Forming Limit Diagram 3 4 1. Cutting Operation Cutting Operation • Cutting operation – Plastic deformation Punch – Penetration (1/3 thickness) t –Fracture • Shearing using a machine called power Die shear or square shear. c • Blanking – shearing a closed outline Rollover part (desired part called blank) Burnish • Punching – sheared part is slag (or scrap) and remaining stock is a desired part Fracture zone Burr 5 6 part Kwon 1 ME477 Fall 2004 Analysis Die, blank and punch size • Clearance - 4-8% but sometime 1% of thickness For a round blank, – Too small – fracture does not occur requiring more force. Blank punch diameter=Db-2c Blank die diameter = D – Too large – Get pinched and cause an excessive burr b For a round hole, • Clearance: c=a*t D Hole punch diameter=D – Metal group a h h c c Hole die diameter = D +2c – 1100S and 5052S aluminum alloys, all tempers 0.045 h Db Angular clearance of 0.25o to 1.5o – 2024ST and 6061ST aluminum alloys; brass, soft cold rolled steel, soft stainless steel 0.060 Cutting forces: F=S*t*L=0.7*TS*t*L – Cold rolled steel, half hard; stainless steel, where S= Shear strength half hard and full hard 0.075 t=thickness L=length of cutting edge Angular clearance TS =Ultimate tensile strength 7 8 Other Cutting Operations 2. Bending Operations part • Cutoff and Parting part • V-bending part scrap • Slotting, Perforating and Notching • Trimming, Shaving and Fine Blanking • Edge Bending Trimming Shaving Fine Blanking 9 10 Analysis of Bending I Analysis of Bending II • Bend Allowance - length of a neutral axis • Compensate for spring back A BA = 2π ()R + K t 360 ba – Overbending A = Bend Angle – Bottoming – squeezing the part at the end of R = Bend Radius the stroke 2 A’ Kbf ()TS wt A t = Stock Thickness F = • Bending force: D K ba = A Factor to Estimate Stretch w –Kbf=1.33 for V-bending Kba=0.33 if R<2t and Kba=0.5 if R≥2t A' − A' –Kbf=0.33 for Edge-bending • Springback SB = b ' D Ab – w= width of part A' = includedangleof thesheet metalpart – t=stock thickness ' D Ab = included angleof the bending tool – D=die opening dimension 11 12 Kwon 2 ME477 Fall 2004 Other Bending Operation 3. Drawing • Flanging • Basic drawing operation – a cup-shape • Hemming part • Seaming F Fh F • Curling h Dp • Channel, • U-bending Air bending, c c D Offset bending, p Corrugating and Db Tube forming 13 14 Detail Steps of Drawing Analysis of Drawing v F v F Fv Fv v v • Measure of Drawing D – Drawing ratio:DR = b feasible if DR<2 Dp F F Db − Dp v v v – Reduction:r = feasible if r<0.5 Db 1. Initial Contact 2. Bending – Crude measures of the severity of a deep F drawing operation Fv v v Fv Fv ⎛ D ⎞ v ⎜ b ⎟ • Drawing Forces: F = πDpt()TS − 0.7 3. Straightening ⎜ D ⎟ Max at 1/3 length ⎝ p ⎠ 2 2 • Holding Force: Fh = 0.015Yπ [Db − ()Dp + 2.2t + 2Rd ] 4. Friction & 5. Final Shape Compression 15 16 Other Drawing Operation Forming-Limit Diagram • A grid pattern of circles, typically 2.5 to 5mm in diameter, • Redrawing produced by electrochemical or photoprinting. • Drawing without a Blankholder • After drawing, the circles are observed for failure. • The major strain is on the major direction and magnitude • Not cylindrical cups of strain • Defects (Fig. 20.24) – Wrinkling in the flange 120 Failure – Wrinkling in the wall Major Axis Major Axis Low Carbon Steel80 – Tearing High Strength Steel Simple – Earing – anistropy in sheet metal Minor Axis Minor Axis 60 Tension Major strain Al alloy – Surface scratch Pure Equal shear Safe biaxial 0 0 80 17 -60 Minor strain 18 Kwon 3 ME477 Fall 2004 4. Other Sheet-Metal Operations 5. Dies and Presses • Stamping Die • With Metal Tooling – Punch – Ironing –Die Punch Holder – Coining and Embossing –Stripper Punch Stripper – Lancing •Types –Simple Strip stock – Compound Guide pin die • Using hydrostatic pressure – Progressive – Guerin Process – Rubber pad •Press Die holder – Hydroforming - Hydraulic fluid – Hydraulic Press base Blank – Mechanical 19 20 6. Other Types Sheet Metal Stretch forming and Roll bending & Operations Forming • Stretch Forming • Roll Bending and Forming • Spinning– make cone, hemisphere, tubes – Conventional – Shear – Tube • High-Energy-Rate Forming – Explosive Forming + – Electrohydraulic forming + + – Electromagnetic forming 21 22 Spinning & Explosive forming 7. Bending of Tube Stock • Bending without collapse and fold • To avoid flattening Mandrel Clamp Mandrel Clamp – R(bend radius) > 1.5D(tube diameter) with a mandrel – R>3D without mandrel. Roller tool Shear Spinning Conventional Spinning F •Types – Stretch bending Explosive – Draw bending (rotating form) – Compression bending (form block) – Roll bending (similar to sheet metal) Explosive forming Tube Spinning 23 24 Kwon 4.
Details
-
File Typepdf
-
Upload Time-
-
Content LanguagesEnglish
-
Upload UserAnonymous/Not logged-in
-
File Pages4 Page
-
File Size-