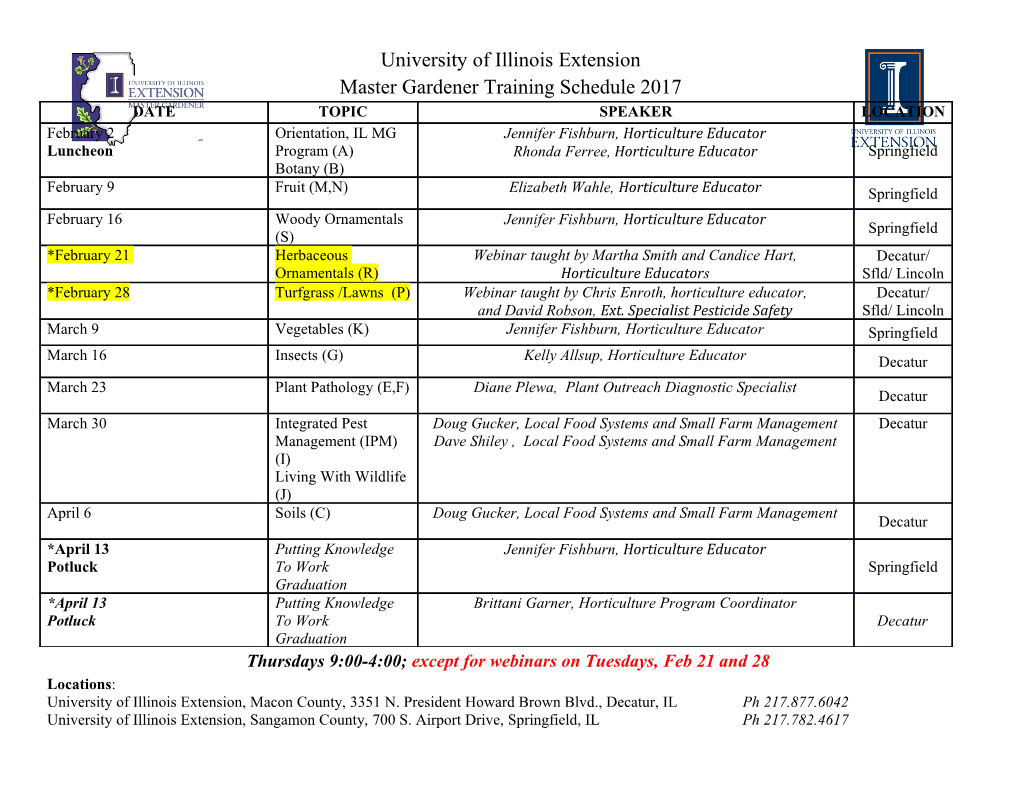
United States Patent (19) 11) 4,416,737 Austin et al. (45) Nov. 22, 1983 54 PROCESS OF ELECTROPLATING A 2,844,530 7/1958 Wesley et al. ................ 204/43 TX NICKEL-ZINC ALOY ON STEEL STRIP 4,249,999 2/1981 Tsuda et al. .......................... 204/28 4,251,329 2/1981 Asano et al. ... ... 204/27 (75) Inventors: Lowell W. Austin, Weirton, W. Va.; 4,268,364 5/1981 Hall .................... ... 204/43 Z. James O. Stoddart, Clinton, Pa. 4,282,073 8/1981 Hirt et al. ........... ... 204/28 (73) Assignee: National Steel Corporation, 4,313,802 2/1982 Shibuya et al. ....................... 204/28 Pittsburgh, Pa. OTHER PUBLICATIONS (21 Appl. No.: 347,704 J. K. Dennis et al., "Nickel and Chromium Plating', pp. 22) Filed: Feb. 11, 1982 140-142, (1972). (51) Int. C. .......................... C25D 3/56; C25D 7/00 Primary Examiner-G. L. Kaplan (52) U.S. C. ........................................ 204/28; 204/27; Attorney, Agent, or Firm-O'Neil and Bean 204/43 T; 204/DIG. 13 ABSTRACT 58) Field of Search ..................... 204/43 T, 43 Z, 27, 57 204/28, DIG. 13 An electroplating process is disclosed for coating metal strip or sheet with a nickel-zinc alloy comprising at least 56) References Cited 80% nickel. Steel sheet coated with the alloy exhibits U.S. PATENT DOCUMENTS excellent weldability. 2,419,231 4/1947 Schantz ........................ 204/43, ZX 2,840,517 6/1958 Faust et al. ....................... 204/43. T 9 Claims, 1 Drawing Figure 50 A 225ppm Zn O 40Oppm O600ppm A 800ppm 0800ppm 3 O PERCENT Zn N DEPOST vs. goTATION RATE (CURRENT DENSITY = 75A/f ) U.S. Patent Nov. 22, 1983 4,416,737 50 A 225ppm Zn / O 400ppm O 6OOppm A S388. O80Oppm RPM PERCENT Zn. IN DEPOST vs. SOTATION RATE (CURRENT DENSITY = 75A/ft?-) 4,416,737 1. 2 At higher magnifications some of the grains appear to PROCESS OF ELECTROPLATING A exhibit internal structure; however, even at the highest NICKELZINC ALLOY ON STEEL STRIP available manification, little detail could be picked out. The structure appears to be a mixture of dislocation FIELD OF THE INVENTION tangles and twinning. The estimated grain size of an The invention is directed to high nickel content al alloy containing 5.45% zinc produced on a pilot line run loys produced by electrodeposition and to an improved was somewhat finer, ranging from about 190 to about electrodeposition process for the production of said 210 A mean grain diameter. alloys. The nickel alloys contain nickel and less than 20 Electron diffraction patterns indicated no consistent weight percent zinc. The alloys are provided as coat O overall preferred orientation of the deposit, although ings on metal substrates such as sheet steel. small regions exhibited local preferred orientation that varied from region to region. At times, the coating took BACKGROUND OF THE INVENTION on a striated appearance, sometimes with well defined Plated sheet steel is well known and widely used for boundaries, but more often with no obvious boundaries. various applications particularly where corrosion resis 15 Another feature revealed by the electron miscro tance is an important consideration or where severe scope study was the appearance of angular etch pits working as in a deep drawing or drawing and ironing resulting, apparently, from the coating replicating etch operation is required. For such uses in the past, tin has pits in the underlying steel. Usually these pits occurred been the most common coating metal and tinplate has in clusters having the same orientation but whose orien been widely used particularly in the production of cans 20 tation varied from one cluster to another. The rectangu for food, beverages, and the like. The use of chromium lar flat bottom shape of the pits suggests that the pits plated steel is also widely used in the production of have walls and bottom and reflect the orientation of the cans, and galvanized steel and nickel-plated steel have underlying steel. also been used for various purposes. It has also been Another reflection of substrate structure is the appar proposed to include minor amounts of zinc in a nickel 25 ent replication of fine-grained patches noted in a photo plating bath to produce a brighter finish for nickel micrograph made at 16,000 X in which one white grain plated articles and it is known to include small amounts which measured 4 cm across was actually 2.5 microns of nickel in a zinc plating bath. across (0.0001), corresponding to ASTM grain size 14. SUMMARY OF THE INVENTION 30 In the photomicrograph the etch pits were roughly The invention is directed to the production of high hexagonal, again implying walls and that the steel grains nickel content alloys by electrodeposition. Generally, have a plane parallel to the surface. the alloys contain at least 80% nickel and up to 20% Often associated with the "fine grain” patches were zinc, but preferably the alloys contain at least about long, dark regions which sometimes contained internal 90% nickel and up to about 10% zinc. The alloys of the 35 structure. Such a dark structural component, compared invention are produced by electroplating onto a steel to the rest of the field, is much thicker than the rest of substrate from a nickel salt-boric acid electrolyte con the structure. Sharp boundaries indicated a sudden taining at least about 40 ppm zinc at temperatures rang change in thickness. The dark material may be either a ing from about 120 to 160 F. wall standing up from the coating or a ditch or crack in The steel products of the invention are steel plate or 40 the steel. Examination of a number of such dark regions sheet of the type suitable for the production of contain indicates that they are walls or dykes standing up from ers or cans, for example, and coated with the nickel–zinc the surface. alloy. The coated steel sheet exhibits excellent corro On the whole, the coatings were remarkably free of sion resistance and workability. Moreover, steel sheets pores or perforations. Occasionally a string of pinholes coated with the alloy exhibit excellent weldability, that 45 would be seen, or clusters of pinholes would be de is, steel coated with the alloy of the invention exhibits tected. Whether these "pinholes” are a sideproduct of excellent bonding to itself. In fabrication of seamed alloy production or a result of electrolytic stripping and containers, the alloy coated on steel provides an excel specimen processing is unknown. In a few cases a small lent seam when formed by wire-mesh welding pro pinhole, roughly the same size and shape of the pinhole, cesses without requiring edge stripping or brushing. 50 can be seen next to the pinhole, implying that pinhole was present in the coating but was dislodged during DESCRIPTION OF THE DRAWING specimen preparation. FIG. 1 is a graph in which the zinc content of the The process of the invention for making the alloys alloys is plotted against the rotation rate of a rotating includes producing them electrolytically from an elec disk electrode in an electroplating solution used in the 55 troplating solution on a steel substrate. The electroplat process of the invention. ing solution is acidic with a pH of about 3 to about 5 and contains a source of soluble nickel and at least about 40 DETALED DESCRIPTION OF THE DRAWING ppm of zinc in, for example, a soluble salt form. Typi Alloys of the invention contain generally at least 80% cally, the source of nickel will be nickel sulfate and nickel and up to 20% zinc. The grain structure of the 60 nickel chloride, as nickel sulfate is a relatively inexpen alloys was studied by electron miscroscopy. None of sive source of nickel ions; the chloride ion provided in the diffraction patterns showed any evidence of free the form of nickel chloride allows proper anode corro zinc. Specimens of the alloy exhibited remarkable uni sion. The plating solution thus will contain: formity. Generally, the microstructure consisted of fine Nickel sulfate (NiSO4.7 H2O): 60 to 90 g/1 grains with little texture. Grain diameters were gener 65 Nickel chloride (NiCl2.6 H2O): 60 to 90 g/1 ally less than 33A having some internal structure with Nickel equivalent as metal (total nickel content): 25 only highly localized preferred orientation and overall to 45 g/1 random orientation. Very little porosity was detected. Boric acid (H3BO3): 30 to 50 g/1 4,416,737 3 4. pH: 3 to 5 excellent seam, when formed by wiremash welding Zinc (provided as ZnSO4.1 H2O): 40 ppm to 1800 techniques. ppm ... The following examples present specific embodi Generally, the zinc is present in amounts less than 1800 ments of the invention by way of illustration. ppm, as at that concentration, the deposit is dark uni formly at effectively low agitation rates, while at rela EXAMPLE 1. tively higher agitation rates, the deposit is dark with A number of coils of 80 lb. base weight continuous streaks. Preferably, the zinc concentration is less than cast steel strip were continuously annealed to a T-4 about 1000 ppm. Most preferably, the zinc concentra temper. The strip was then plated in accordance with tion ranges from about 50 ppm to about 400 ppm. 10 the invention in a five day run on a modified horizontal The electroplating solution is maintained at a temper halogen tin plating line in which nickel anodes replaced ature of about 120 to about 160 F., cathode and anode the tin anodes and a nickel plating solution replaced the current densities can range from about 50 to about 150 halogen tin plating solution.
Details
-
File Typepdf
-
Upload Time-
-
Content LanguagesEnglish
-
Upload UserAnonymous/Not logged-in
-
File Pages8 Page
-
File Size-